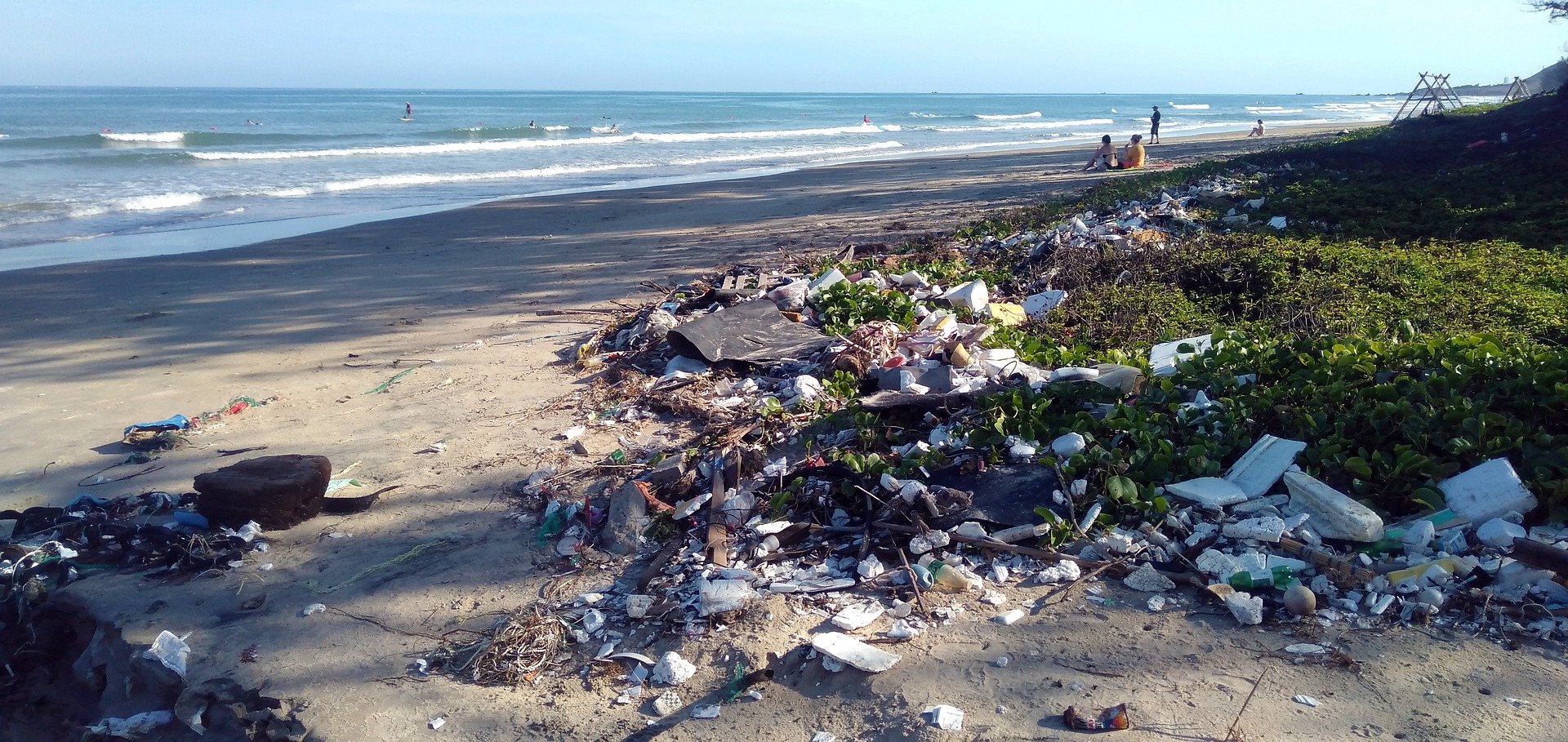
An empty bag of chips in a ditch, thousands of trampled cups at a festival or a stray sandwich bag flying through the air -no doubt you have seen them all before. Those stray disposable packaging materials on the street seem harmless, but they really aren’t. Disposable plastic is a major threat to our environment. At a neighborhood get-together in 2005, four neighbors decided that things had to change. They developed a biodegradable coating for fruits and vegetables. With their company Liquidseal, they are not the only ones who are earnestly seeking alternatives to disposable plastic packaging. There are a variety of alternatives and scientists also have the subject high on their agenda.
This is desperately needed, because disposable packaging for our food and drink makes up the largest portion – 82 percent – of the rubbish floating around in the oceans. Just in Europe, between 307 and 925 million pieces of litter end up in the ocean every year. If this trend continues, around 1.3 billion tonnes of plastic will eventually be drifting in the oceans by 2040. Fortunately, there are scientists and entrepreneurs who have made it their mission to put a stop to that.
“Aside from the fact that plastic is a threat to the environment, we also throw away a third of the food we produce globally,” says Victor Monster, Managing Director at Liquidseal. The company is developing a biodegradable coating technology for fruits, vegetables and flowers as an alternative to plastic packaging. “This enables us to reduce waste by thirty to forty percent and to extend the shelf life of the products.”
Slow-release systeem
Liquidseal is a spray or liquid which fruits and vegetables are dipped into. A thin film layer that is about three to four microns thick then forms. Inside that layer is a channel structure that affects not only how the product handles the evaporation process, but also the oxygen and CO2 exchange. “Compare it to the vent of a BBQ. When it’s fully open, the coals burn up quickly. If you leave the vent slightly open, the coals burn up much more slowly. That’s also what our technology does; we extend the shelf life of the product by using a slow-release system,” Monster goes on to explain.
A complicated task, because each kind of fruit and vegetable has a different oxygen requirement. Consequently, Liquidseal has to adjust the formula of the liquid and the channel structure for each product.
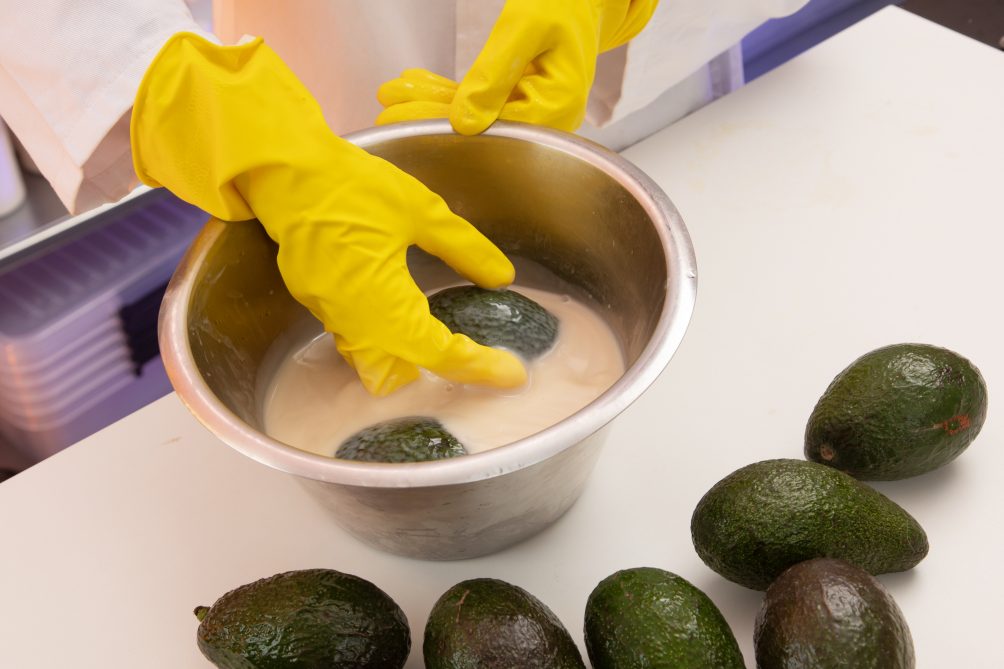
Legislation and regulations
At the moment, the company is focusing solely on the European market, specifically on packaging for avocados, mangoes, citrus, melons and papayas. “Packaging for bananas and pineapples is also in the pipeline, but our hands are tied by European legislation and regulations. There is a list of the components that you are allowed to use for packaging. If you use other ingredients, you are officially breaking the law.” For example, Liquidseal is only permitted on hard-skinned fruits and vegetables for the time being, and apples, pears, tomatoes and cucumbers are completely off-limits so far.
Yet Monster is confident that this is set to change in the future. “People do want less plastic packaging, environmentally friendly packaging, fewer chemicals on products and less food waste. Liquidseal meets all of these conditions.”
From field to fork
Another challenge for Liquidseal is that the coating must be applied to the product as soon as possible after harvesting for it to work optimally. “Therefore, we need to be able to gain a foothold among growers in Ecuador, Mexico and Colombia.” At present, Liquidseal is still doing a lot of testing to demonstrate to importers and retailers the advantages of the environmentally friendly packaging. “A number of importers have already committed themselves and we are in the process of introducing it to the market.” Monster expects it will be another five years before there are any fruit and vegetables on the shelves with Liquidseal’s coating layer.
Environmentally friendly alternative to aluminum layers
Scientists are also looking for alternatives to environment-damaging disposable packaging. For instance, the research group of Wiebe de Vos, Professor of Membrane Technology at the University of Twente (UT), and the group led by Jasper van der Gucht, Professor of Physical Chemistry and Soft Matter at Wageningen University (WU), are jointly developing an environmentally friendly alternative for the evaporated aluminum layer on the inside of packaging. The layer blocks oxygen so your chips are kept crisp and your coffee stays aromatic, “but all those layers also make a lot of food packaging very difficult to recycle,” Van der Gucht adds.
So, there are actually two problems with present-day packaging: the layer of aluminum is difficult to dissolve and difficult to separate from the other layers. In addition, plastic is tricky to recycle anyway because the polymer molecules are stuck together with permanent chemical bonds. “We are trying to do something about both aspects. Our polymer layer replaces aluminum and the layer comprises bonds that you can expand. That makes recycling that much easier,” says Van der Gucht.
Negatively and positively charged polymers
That special polymer layer is the outcome of an experiment with positively and negatively charged polymers. Together, they form a dense and protective layer against oxygen. But it is also possible to switch off the bond. “That way, you no longer need that aluminum layer,” he adds.
What is important here is that the positive and negative polymers bind to each other and release at the right time. Van der Gucht cites a pot of paint as an example. “If you add negatively and positively charged polymers that bind together prematurely, then you end up with lumps in the paint pot. If they bind too late, you will not get a dense, solid paint coating. That is why we apply a pH trick: at the beginning, the pH level is high and so the charges do not bind together. During the drying process, the base evaporates and the pH gradually decreases, so that the polymers do bond. We do the same with packaging.”
Sustainable polymer packaging
The research is being carried out in cooperation with UT, BASF and AkzoNobel. In the meantime, the UT and WU researchers have shown that good quality films can be made this way, that the oxygen barrier meets the requirements, and that it is more easily recyclable.
“The problem that we are still running into is that this layer is not yet strong enough. You can solve this by using an extra layer, but ultimately we want to move towards packaging that is made up of a single layer.” In addition, the research is currently still focused on simple polymers made from raw fossil materials. In the future, Van der Gucht wants to move toward packaging made from sustainable raw materials. “The best thing would be if you could use organic waste to make polymer packaging.”
According to Van der Gucht, the discovery is a significant step towards a sustainable packaging industry. “The quality of this polymer-based coating is at least equivalent to that of aluminum-coated packaging, but the environmental gains are great because polymer packaging is potentially much more recyclable.”
One way or another, armed with polymer packaging and eco-friendly coatings, in the future, the plastic soup will become smaller.