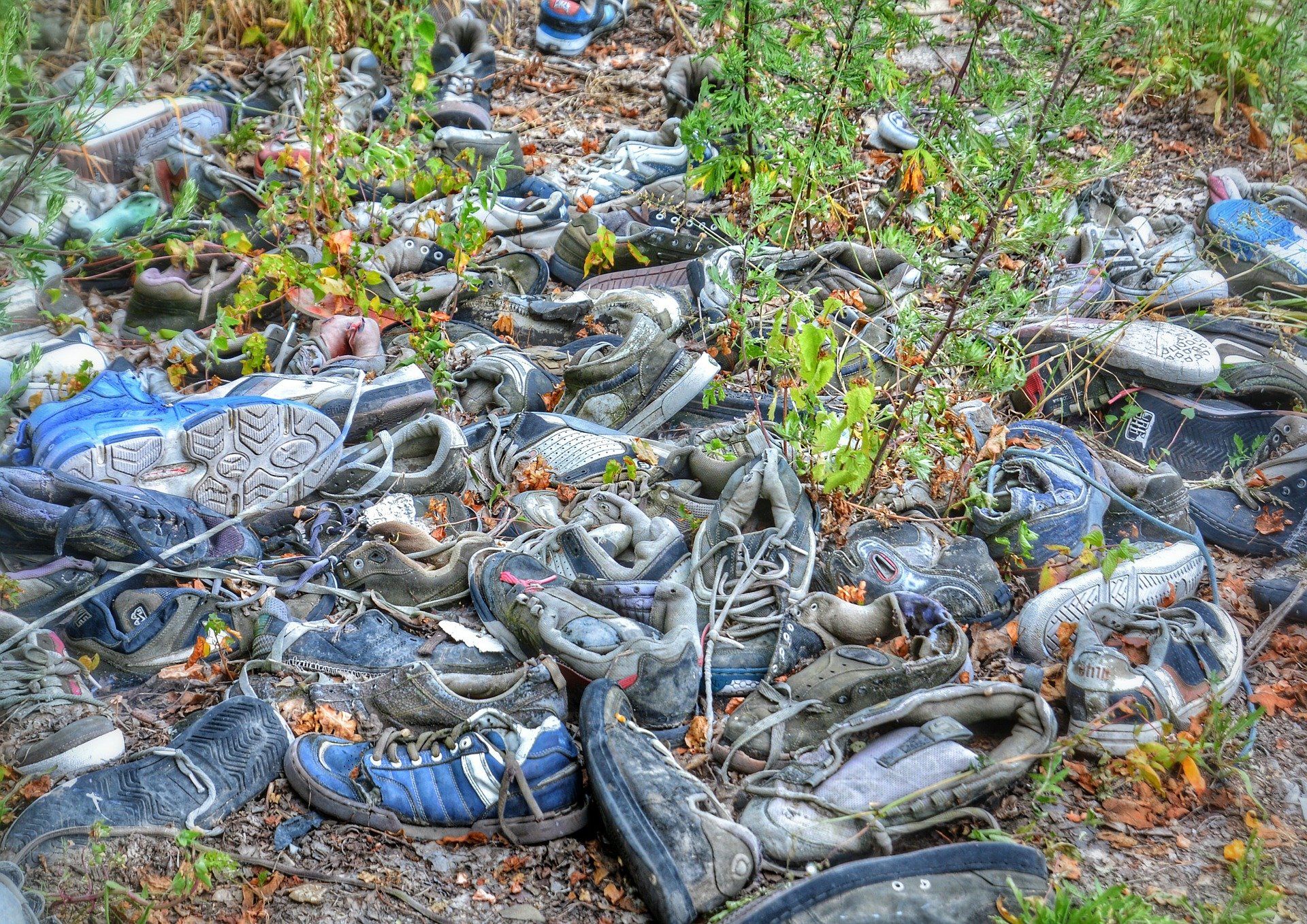
“In the early days, we took shoes apart by hand and put the materials in the microwave or in a pan on the stove,” says Danny Pormes of Fastfeetgrinded when he first started trying to recycle footwear five years ago. Nowadays, there is a machine that processes 2500 shoes per hour.
The industry produces around 70 million shoes every day. And for every pair sold, another pair is discarded. Since footwear is often made of many different materials, recycling is difficult. That is why old shoes are often shipped to Africa, Asia or Eastern Europe, where they end up in landfills or incinerators. Pormes and his partners thought that this was a wasted opportunity.
Shoe recycling machine
Former marine Pormes has a running shop and supplies sports shoes to the Dutch Ministry of Defence. Five years ago, the Ministry asked whether it was feasible to recycle shoes. Pormes and fellow marine David Uijtewaal got stuck into the problem and never let it go. And they succeeded. Fastfeetgrinded built the world’s first ever footwear recycling machine, also known as the SRM: the Shoe Recyle Machine. “The SRM can process 2,500 shoes per hour,” an enthused Pormes tells us over the phone. ” The shoe goes in on one side of the machine and on the other side, we separate it into three different materials: foam, rubber and textile. These come out in the form of granules or yarn.”
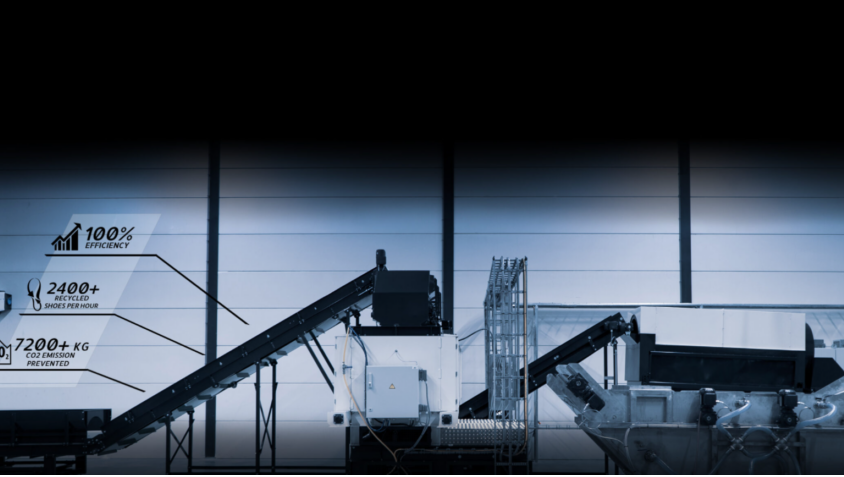
Asics, Decathlon and Bever
How exactly does the apparatus work? “That’s the secret of the blacksmith,” Pormes laughs. “The system is patented and we want to develop it further ourselves.” The machine has now attracted the attention of a wide range of well-known sports brands such as Asics, Decathlon and Bever. As a society, we need to reduce our use of raw materials by half by 2030. As a result, Pormes expects the demand for recycled materials to continue to rise.
Growth at home and abroad
Not only is demand for the recyclate produced by SRM increasing. ” We are now receiving worn-out shoes from all over the Netherlands at our office in Susteren,” says Pormes. “It is too much to process and we are short of space. So this week we decided to relocate. We will expand fivefold at the new location in Wieringerwerf.” Plans for a second factory in the Netherlands are now in place. Germany is also on the agenda for Fastfeetgrinded.
It will be some time before consumers can actually buy the first circular shoe. “But it is definitely possible,” Pormes assures us. “There is a pair here on my desk. We don’t want to build a brand, we are using the pair to show the industry that it is feasible.” Because the shoe is made from a blend of coloured materials, the end result is predominantly brown for now. “If we were to add paint to it, the shoe would obviously no longer be 100 % circular. Fortunately, brown will probably come back into fashion on its own accord.”
Also interesting: Lionel Messi’s new sneakers come from the recyling bin
This article is courtesy of ChangeInc, who Innovation Origins has an editorial partnership with.