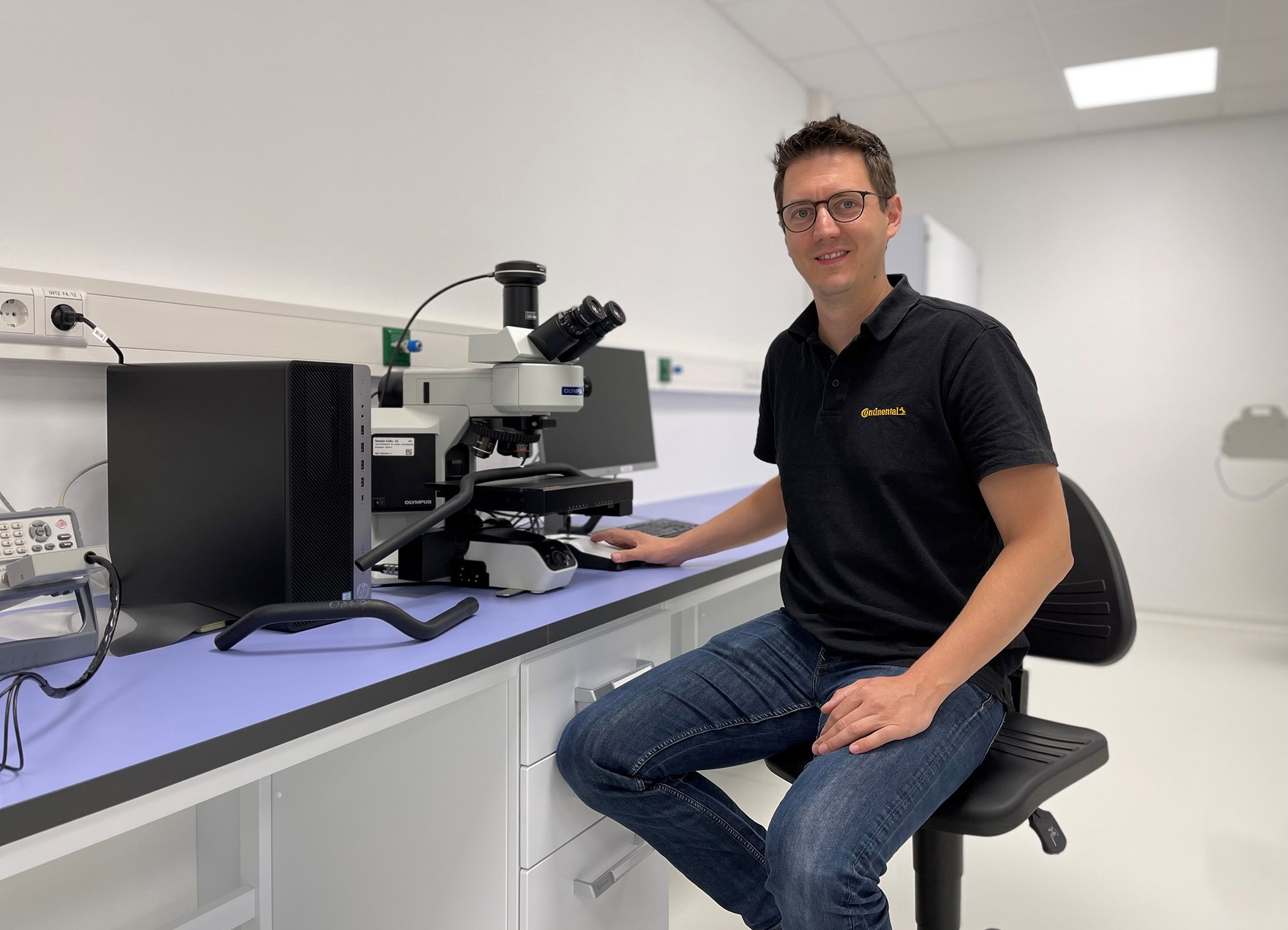
Rubber parts play a crucial role in the automotive industry, as today’ cars rely on rubber-made parts such as tyres and belt drives. However, there are no effective ways to know the status of the elastomer components. Therefore, a team at the tyre manufacturer and technology company Continental is working alongside other partners to integrate printed electronics into rubber.
The sensIC project is carrying out tests that combine sensor technology with printed electronics in hose lines. The German Federal Ministry of Education and Research is funding the 3-years-long program. At the end of this term, the different partners will have to present what is known as a demonstrator. The researchers are working on a hose for fluids as the demonstrator for their project.
The researchers are working at Continental’s Center for Functional Printing Technologies in Freiburg. SensIC involves a network of companies and universities in the southwest of Germany, each of them bringing various ideas and expertise to the research. Continental is in charge of the functional printing of the rubber, the integration of the sensor system, and the coordination of the entire project.
“Nowadays, rubber products have a mechanical function but not an electronic one. We would like to know about the status of parts, the history of the applications, and the expected lifespan”, explains Tim Wolfer, mechanical engineer, and Continental’s project manager in Freiburg.
Considering the possibility to tailor printed electronics for all kinds of uses, the German company has high hopes for the project. Hoses, air springs, and tyres are just a few examples of the potential applications this technology could have in the future.
Interacting with components
Despite the thousands of data points available in modern cars, there is no data available on the performance of rubber components.
“Making sure that the components can monitor themselves via sensors is the goal. The product itself should be able to sense what is happening. It should be able to tell us if the temperature is too high or if the load is too heavy”, Wolfer adds.
According to the mechanical engineer, such technology could be useful for preventive maintenance too. “We would like to able to ‘ask’ the product how long it is going to last and when we need to replace it.” Components could also be read in workshops to further verify their status. Maintenance would be smarter, as only the worn-out parts of a single item would need to be replaced.
This way, end users can gain more insight into the status of rubber components. Depending on their actual usage, users could be notified more precisely about the lifespan of rubber car parts, which would improve the current wear-assessing methods.
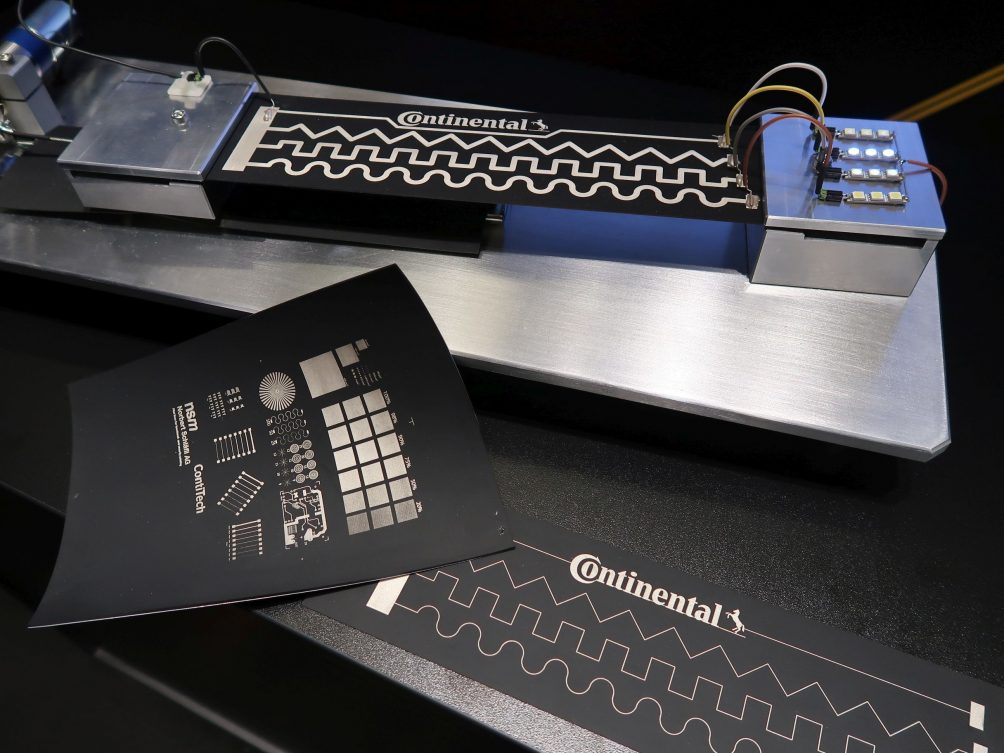
Sensors will form part of the rubber components, enabling them to track tyres, drive belts, and hoses’ complete lifecycle. Having data on how car parts perform is also useful for designing more efficient parts. “We will be able to have data from the car part and to write information into a given component”, Wolfer goes on to explain. Continuous interaction with car parts will therefore improve efficiency. Sensors then communicate to the user about the status of the car parts through the car’s feedback system.
Also interesting: Virtual sensors help to design more efficient cars
Keeping a closer eye on car parts leads to more sustainable practices too. “I recently replaced my car’s tyres. I did it because I had been using them for several years. But when I looked at them, they still looked great, so I thought it is not all about how old they were. It would be great if the tyre could tell us how long it is going to last”, says Wolfer.
Although tyres look good, age does matter even though they may not have been used at all. What the technology developed by Continental and its partners will do is send a warning about the condition of the compound, signalling its bad state or if it is under duress.
Designing better components
Combining printed electronics and rubber represents the real challenge of the sensIC project. Making sure that the stretchability of the electrically conductive material is the same as how they rubber behaves is essential for the success of the project.
Given that the sensIC programme at its very initial stages, it is still too early to predict the results. The component will be tested with different levels of temperatures and pressures, as well as with different frequency variations. In addition, the chemical compatibility needs to be considered too.
According to Wolfer, there is more that can be achieved. “Having high reliability over a long period of time is the main challenge. It is what we are aiming for with the other partners that are helping us in the evaluation and development of the material.”
Looking ahead
The potential of combining printed electronics and rubber also lies in the chance to use highly productive printing processes which are at the same time cost-effective. However, such an application will only be possible in the future. Since it is just the beginning of the project, Wolfer and his team are facing new challenges every day. This is due to the complexity of these small systems and their thin nature.
“In the field of printing, it is always about large-scale productions. At this point, we are unable to do that yet, as we are currently working on basic issues for integrating rubber and printed electronics. But large-scale production is what we’d like to achieve as costs would be low”, Wolfer notes.
The combination of rubber and sensors will take time to put into practice. Nonetheless, sooner or later we will be able to know exactly when to change our tyres.
In the first photo: Tim Wolfer.
In the second photo: Rubber substrates on which silver electrical conductors have been printed.