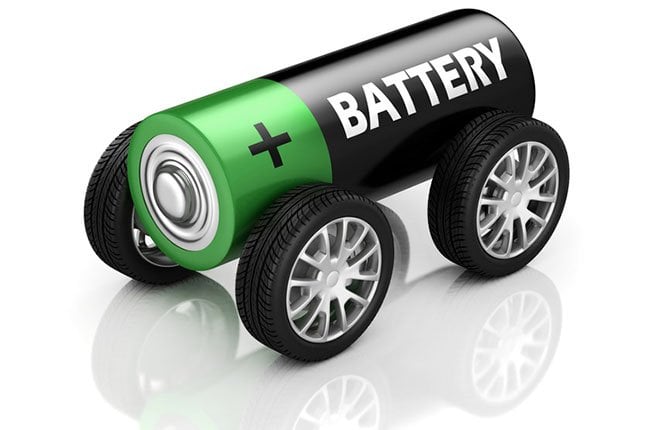
The European Commission wants to build a strong battery industry that can compete with Asia, but has it entered the game too late?
By 2020, China will produce more than 70% of the lithium-ion batteries that cars run on. Europe is fighting back, hoping to build up to 20 gigafactories by 2026.
By Ben McCluskey, the Technologist
Since first appearing on the consumer market in 1991, lithium-ion batteries have become ubiquitous in phones, laptops and even e-cigarettes. With the rise of electric cars โ global sales exceeded 1 million for the first time in 2017 โ the demand for li-ion is soaring. Predicts Fabrice Stassin of Umicore, a materials technology multinational: โBy 2025, the transport market segment may represent 80% of future li-ion demandโ.
Europeโs position in the automotive market is being seriously challenged by this transition to e-Mobility. Batteries count for up to 40% of the value of the car but production is dominated by Asia. Chinaโs global market share is projected to rise to more than 70% by 2020.
Europe, on the other hand, does not even have a battery manufacturing industry. โSecure supply chains can be challenging if raw materials and cell production are based in other parts of the world,โ says Tejs Vegge of the Technical University of Denmarkโs Department of Energy Conversion and Storage (DTU Energy).
More on the research on lithium batteries here
In response, the European Commission hopes to forge a strong and sustainable battery industry within an initiative called the European Battery Alliance. The Alliance aims to provide a framework that includes secure access to raw materials, support for technological innovation and consistent rules on battery production. The ECโs Horizon 2020 research fund has set aside โฌ200 million for battery projects. In addition, โฌ800 million is available to finance building demonstration facilities. Poorer areas can also apply to the $22 billion Regional Development Fund. And the European Fund for Strategic Investment is available to co-fund the billions of euros needed to build equivalents of Teslaโs large-scale battery-cell production facility in Nevada, which its founder, Elon Musk, has dubbed a โgigafactoryโ.
Lithium deposit, Portugal. Containing upwards of 2% of global deposits, the resources in Portugal could ensure a significant supply of lithium for Europe.
The rise of the gigafactories
The EUโs vision is to create between 10 and 20 gigafactories. Car manufacturer Daimler is planning for two in its home country, Germany, which is also the front-runner for Teslaโs first European gigafactory. If the EU hits that target, Europe would account for some 15% of global cell manufacturing capacity by 2026.
Progress is already underway in some countries. Opened in 2018, LG Chemโs Polish factory is ramping up production targets sevenfold. Swedenโs Northvolt plans to spend โฌ4.13bn on a Nordic plant and Germanyโs TerraE has announced two plants in Germany.
Umicore is forming a technological alliance with BMW and Northvolt. Stassin explains: โThe alliance will cover active materials development, utilisation of raw materials coming from recycling, battery-cell manufacturing scale-up, cell and pack design and, finally, collection, dismantling and recycling with a focus on increasing the sustainability of the battery-value chain.โ
Lithium-ion batteries consist of two layers: one made of lithium cobalt oxide, the other graphite. Energy is released when lithium ions move from the graphite layer to the lithium cobalt oxide layer. Charging a battery simply shifts those ions back the other way.
Also read: Auke Hoekstra: The incredible potential of batteries
But efforts to scale end-to-end battery production wonโt be straightforward. Asia has worked hard to control much of the semi-rare (cobalt and lithium) raw materials it needs from Africa and Australia.
A growing mineral crisis
The next step is to find alternatives to importing components and raw materials. In May 2018 a huge lithium deposit was unearthed in Portugal. At least 14 million tonnes of the precious element are believed to reside around the Mina do Barroso in the Vila Real district and the government is negotiating with mining companies as they queue up to exploit this massive resource.
โContaining upwards of 2% of global deposits, the resources in Portugal could definitely ensure a significant supply of lithium for Europe,โ notes Vegge. But this is not good enough for the long term, he says. โIf you need the quantum leap of a sustainable battery that is fully scalable to the terawatt challenge, we cannot rely on the materials weโre using today.โ
Is Europe too late?
Is Europe is trying to maximise its market share of a li-ion industry that is destined to decline in the face of newer technologies? The answer is the EUโs Battery 2030+ Vision, which aims to give Europe a competitive edge by disrupting discovery, development, and manufacturing processes for battery materials and technologies.
Veggeโs work on the Battery Interface Genome โ Material Acceleration Platform (BIG-MAP) is a key component of this longer-term vision. It harnesses the power of machine learning to find the optimal materials โ from aluminium-sulphur to lithium-oxygen and beyond โ and material designs to meet future battery applications. โBIG-MAP basically combines the understanding of the fundamental chemistry and physics behind the batteries with our ability to accelerate production,โ he explains. โArtificial intelligence controls which experiments to do, how to synthesise the materials while also doing on-the-fly characterisation of the data that emerges.โ
The success of such a strategy will be crucial to helping Europe accelerate the discovery of greener battery technologies. The researchers are using the same technology that one uses to run a text search on a Google app in order to search for the best way to synthesise certain types of material. โWe can go through the last 100 years of published scientific articles and screen for the best options for making these types of materials,โ says Vegge. Speed is the key. Asia may be miles ahead in the market, but the slow pace of battery innovation โ the technology has barely changed in 27 years โ could help the Europeans.
[learn_more caption=โA silicon solutionโ]
Franรงois Ozanam explains how research on silicon-alloy anodes could help improve the batteries of the future
A silicon atom can attach to four lithium ions, so a silicon anode can store 10 times as much lithium as the graphite ones currently in use. โThis means the electrodes offer very high-performance but theyโre very unstable,โ says Franรงois Ozanam of รcole Polytechnique.
When lithium ions attach to the anode as a battery is charged, it swells slightly, shrinking again as itโs used. A graphite anode swells and shrinks by about 7%. Silicon particles can swell up to 400%, meaning that, even in controlled lab conditions, most silicon anodes tear themselves apart after a few charging cycles.
โOur main work is on the nanostructures of these silicon-based materials,โ Ozanam explains. โSo, we arenโt really looking at the material itself but rather how to shape it in order to make it more resistant to lithium cyclingโ.[/learn_more]
This article was first published on โThe Technologistโ and was republished with permission