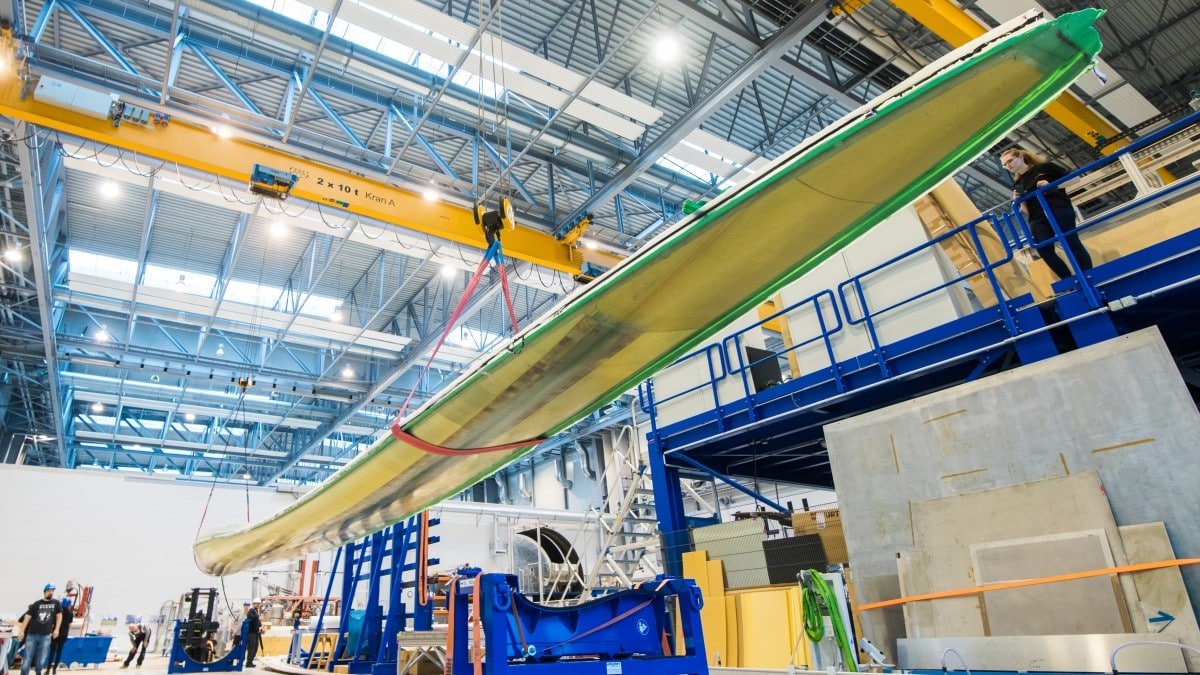
Wind energy is regarded as one of the energy sources of the future. Wind power plants generate electricity by driving a generator with a large propeller. Due to their climate-friendly eco-balance, ever larger, more powerful wind turbines are being built all over the world.

Photo: DLR
However, the rotor blades have to withstand heavy forces, especially in difficult wind conditions. In addition to the centrifugal forces triggered by the rotational movement itself, there are also forces caused by bending and shear forces. German researchers have now designed rotor blades with a bending torsion clutch on the blade hub. As part of the “SmartBlades-2” programme, scientists from the Fraunhofer Institute for Energy Systems (IWES) and the German Aerospace Center (DLR) in Boulder/Colorado (USA) are testing three rotor blades with such a coupling. The test site in Boulder belongs to the US National Renewable Energy Laboratory (NRL) of the Department of Energy. The site was selected because of its environmental conditions. In winter, they offer a wide range from low to gusty and very high wind speeds.

Photo: DLR

Photo: DLR
“This measurement campaign is the first test for our developments. We are very excited to see how our rotor blades will perform in this free-field test,” says SmartBlades2 project manager Zhuzhell Montano Rejas from the DLR Institute of Composite Structures and Adaptronics.
How smart blades work
Usually a wind turbine is controlled by adjusting the position of the rotor blades in relation to the air flow, i.e. the blade angle. Some models simply adjust the blade tips. This allows the operators to control the performance of the turbine and, for example, avoid overloading when wind speeds are too high. When a propeller is required to produce power, the blades are positioned at right angles to the airflow. The blades are switched off by the so-called sail position. In this case, the operators turn the propeller blade into the wind, so to speak, so that one edge points directly into the air flow. The propeller then stops turning.
The bending torsion coupling is located directly at the propeller attachment. It offers additional flexibility. This coupling allows the rotor blades to adapt automatically to changing wind conditions. They twist at higher wind speeds and thus offer the air flow less surface area to make contact with. This reduces the load on the wind turbine while increasing the service life of the rotor blades.
Rotor blade tests run until autumn 2019

Photo: DLR
The three “Smart Blades” were designed by scientists from the Fraunhofer Institute for Wind Energy Systems (IWES). They were built at the DLR Centre for Lightweight Construction Technology in Stade. During construction, numerous sensors were installed to collect measurement data. “In order to record the deformations, accelerations and stresses of the blades, we are using several measuring systems that allow measurements to be taken over the entire length of the blade. The flow around the rotor blades at the surface is measured using an aerodynamic measurement system,” reports Dr Christian Kress, head of the measurement campaign at Fraunhofer IWES. The Fraunhofer Institute is in charge of the measurement campaign. The test generator provided by NREL was also equipped with sensors.
In addition, a laser sensor scans the wind field in front of and behind the wind turbine. This enables the scientists to observe how the rotor influences the air flow. The measurement campaign will last until autumn 2019. Those responsible hope to gain insights both for the further development of rotor blades with bending torsion couplings and for their market launch.