
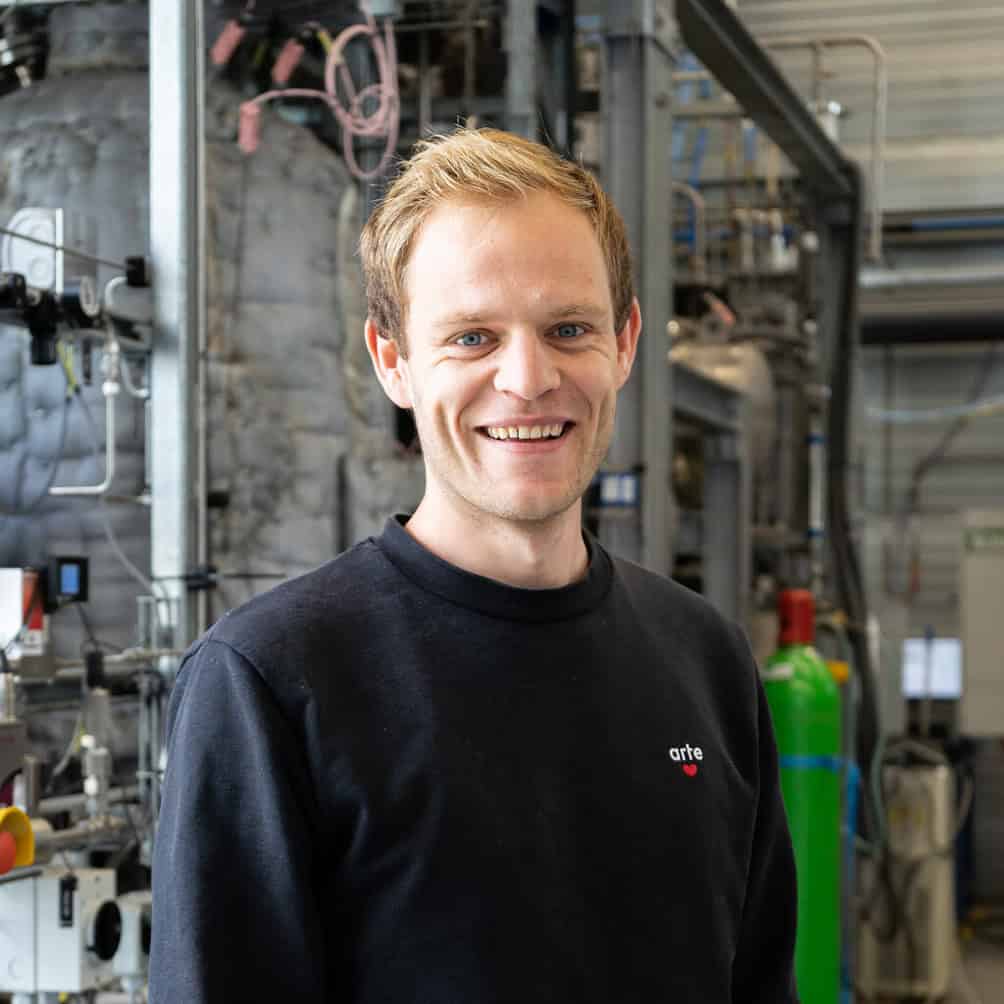
Chemicals: we can’t live without them. We use them to make medicines, packaging, and batteries, among other things. But until now, the raw materials for chemicals have come from fossil sources, such as oil. BioBTX, a Groningen-based developer of renewable chemicals, is going to change that. The company recently raised more than €80 million to launch its first commercial-scale plant. We spoke with Tijmen de Vries, responsible for strategy at BioBTX, about how the company is currently doing.
Congratulations on €80 million! That must be a big milestone.
“Absolutely right. We’ve been working hard on it for three years and are happy that we can now take the next step: building our first commercial plant. Back in 2017, we built our first pilot plant. In doing so, we convinced both ourselves and others that it is worth scaling up our technology further. We are now going to make that happen.”
Where do you get the raw materials to make renewable chemicals from?
“Partly from plastic waste, partly from biomass. Plastic waste is already partially mechanically recycled. However, there remains a residual stream that is currently incinerated. This is the plastic stream we use as input. This includes foils, trays, and other packaging that you throw in the trash, which is too contaminated to recycle mechanically.”
How exactly does your process work?
“We do this through chemical recycling. I just mentioned mechanical recycling. In that, for every kilo of waste you put in, a kilo of recycled material comes out. Mechanical recycling works for food packaging films, for example, but after a few reuses, the quality deteriorates even though the quantity remains the same. With chemical recycling, you get about half a kilo of BTX (benzene, toluene, xylene, ed.) out of a kilo of waste. However, the quality of the material actually goes up; you put waste in and get high-quality applications in return, such as medicine and food packaging. Both methods are necessary for a circular economy.”
What are the chemicals you produce used for?
“You can make batteries and medicines from them, for example. To give you another example, one of our new investors is Covestro, a large German producer of polymers. Among other things, they produce PUR applications: insulation material for refrigerators and cars, among other things.
20,000 tons of waste
The Groningen company plans to scale up its technology at the PETRA Circular Chemicals Plant in Delfzijl. The plant will convert 20,000 tons of mixed plastic waste annually. Once production is proven, the company plans to roll out the technology worldwide to customers in the chemical industry.
What are you guys busy with at the moment?
“We are now in the final stages of designing the plant: detail engineering, as it’s called. We have the building mostly on paper and are now working on details such as electrical outlets and piping. Once that is done, we will make the final investment decision at the end of the year. The goal is to have the building plans ready before the end of the year. After that we need two years to build the plant, we want to be operational in early 2027.”
Do you think the world will embrace your idea in the near future?
“Yes, I’m pretty sure of that. We are increasingly talking to companies that are actively looking for ways to become more sustainable. Partly this stems from moral awareness, partly from increasingly strict regulations, such as, for example, a minimum amount of recycled material in certain products, such as plastics. Moreover, circular BTX offers not only sustainability benefits but also strategic opportunities. Our technology provides greater independence from other countries. Just as we increasingly fill our energy needs ourselves with solar panels and wind turbines, we also want to become less dependent in terms of raw materials on countries such as Russia and China, from which we currently get our oil.
I expect us to make a huge impact in the future. The BTX market is immense and companies that have always used BTX, such as battery manufacturers, don’t have to change anything in their production methods. They just get their chemicals from a sustainable plant. It’s as simple as that.”
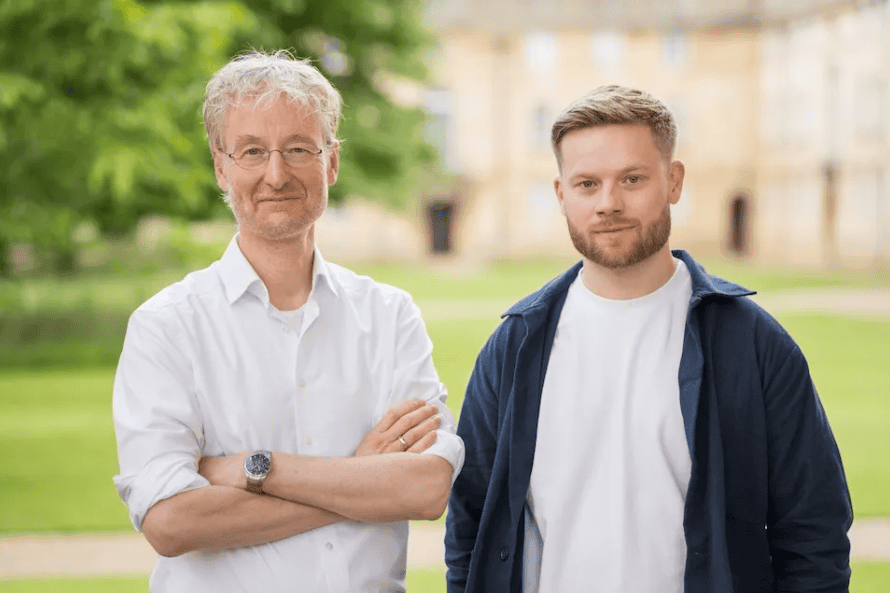