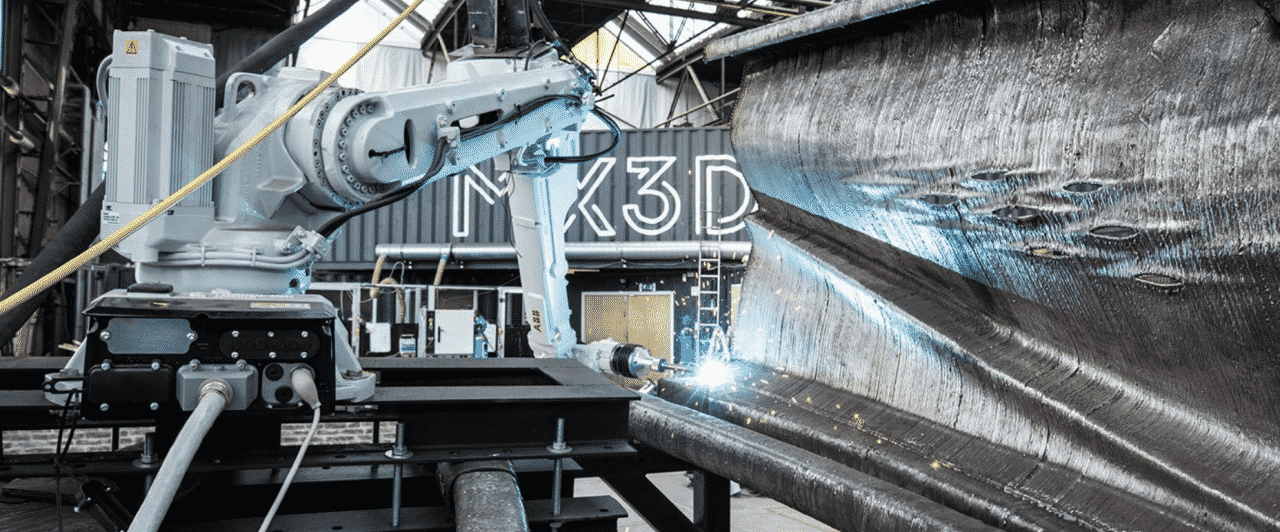
MX3D uses a modified welding robot to print large metal objects, such as a pedestrian bridge which is to span one of the canals in Amsterdam as soon as the final tests have been completed. Founder Gijs van der Velden explains how and why the idea came about.
How exactly does the MX3D method work?
“Our goal was to create a 3D printer that would be able to print large metal objects at a low cost, for idealistic reasons. We started with a standard robot and welding machine. And we wrote software for that so that we could turn the welding robot into a 3D printer. As a result, we were able to print large objects in metal. Instead of welding two plates together, our robot welds welding to welding. This ultimately results in a model that the designer has made on their computer which they want to have printed out. This is entirely made up of welding cables, each half a millimeter thick. It is kind of like rethinking something that already exists and that you will use in a novel way. When you build up the material welding wire by welding wire, as our welding robot does, it does involve a lot of research. Because no one has ever done it like this before. In some places, the metal surfaces are really nice and smooth. But there were imperfections on some of them. We had to find out all these things in order to make it a reliable printer. Research into materials will never stop. But the basis is there. The fact that we can make a decent end product has now been proven. Our first product, a metal pedestrian bridge that spans a canal in Amsterdam, still needs to be tested a number of times for its load-bearing capacity. It has already been proven during the Dutch Design Week in 2018 that it can carry up to 10,000 kilos. Ultimately, it should be able to carry up to 17,000 kilos. This is the standard load-bearing capacity of such a bridge, including an extra margin on account of the new technology.”
What was the driving force behind developing this new system?
“We were frustrated that 3D printers were not being made available for the production of large metal objects. As everyone was focusing on small objects and micro precision. Then we ourselves started looking for a method. We bought an industrial robot and connected it to a welding machine. As inventors, designers and artists, we were especially curious about the possibilities that this might offer us. For us, it was about the fact that what designers had designed on their computers could actually be done with a large metal printer. Without such a printer, the process was sometimes very expensive or it took a very long time. We use our software to make the manufacturing process digital. In the upper right corner of your screen, you can immediately see that my design will take 3 hours to print. You are also able to see when you can do it and how much it will cost. Designers and inventors are offered a freedom when it comes to metal design that they previously did not have. We started from the design angle out of curiosity. But with the tools that we have created, we’re slowly moving into the industrial arena. Since it has been proven that our system is suitable for making artwork and even a bridge, there is a demand for the production of industrial components. And so we are evolving towards a machine that is suitable for the metal industry.”
What has been the greatest challenge for MX3D so far?
“When we started working on our bridge project, we set out a clear vision for the future. We wanted robots to be able to build a whole bridge without any human intervention. The robots must be able to work independently on a bridge [see the video below for a demonstration of this, ed.]. However, in practice this turned out not to be feasible for the very first bridge. But that is definitely the direction MX3D wants to go in. Although we proved then that we could print on the bridge using robots, we split the production into parts that were later welded together for the sake of efficiency. This had to be done because the engineering skills and software weren’t yet able to make the complex design of that first bridge in just one go. We had to radically adapt the bridge design to the capabilities. We didn’t immediately throw everything overboard, but tried to make the bridge so that you could see that it was made in a way that is not yet known to the world. It had to be the banner for large scale metal printing.”
Which moment gave the greatest satisfaction?
“That was when our bridge was installed at the Dutch Design Week of 2018. That it was actually finished and people could walk on it made me very proud. The visitors thought our bridge was the most beautiful project of the fair. That is why we received the 2018 public’s prize. Another time was when we received the award for the best doctor and technology project of 2018. The European Commission offers it to very promising starters. We then went to the Ars Electronica festival [a center for electronic art, ed.] in Austria with the whole team to receive the €20,000 prize.”
What can we expect from MX3D in the future?
“We are busy with a new kind of bridge project that will be unveiled in September. We hope in this way to maintain the high profile that our first bridge gave us. In the future we hope to see the possibilities that MX3D has created on computer screens in schools and in companies that are using our software. We wanted to give designers a tool for redefining the shape of metal. Soon we will see more and more of this design language around the world because people will be using our tool.
MX3D is one of the twenty start-ups that the pan-European network RobotUnion nominated in July for a prize of up to 223,000 euros. The next round of this European start-up competition is in October.