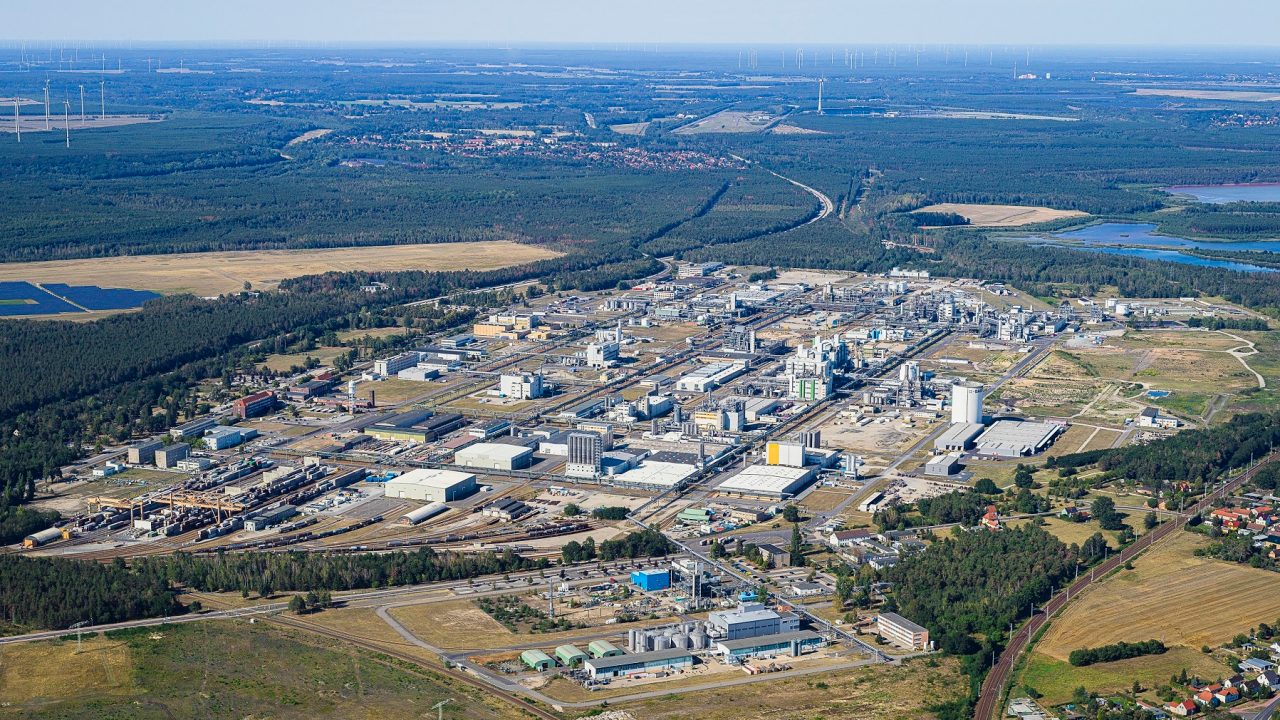
Guben and Gubin are two towns on opposite sides of the River Neiße. One town is in Germany, the other in Poland. Until now, the border town has been known mainly for its ‘Polish Market’ where Germans can fill up on fuel and buy groceries cheaply. In addition, Guben is the birthplace of Wilhelm Pieck, who was the first and only president of the GDR between 1949 and 1960. The office was renamed after that.
A new chapter in its history may be added within a few years. Guben will be getting the largest lithium factory in Europe. The originally Canadian company Rock Tech Lithium reckons it will be able to process enough lithium for half a million electric cars every year from 2024 onwards. The goal is to process 24,000 tonnes of the raw material each year into lithium hydroxide, a main ingredient for almost all batteries in electric cars (used as electrolyte). The refinery at the Guben-Süd industrial area entails an investment of around US$500 million.
At the signing of the contract, Jörg Steinbach, Brandenburg’s Minister of Economic Affairs and Energy called it great news. It indicates that his state is developing into a center for electromobility with at its heart the Tesla factory, approximately 60 kilometers away on the outskirts of Berlin. If all goes well (the factory is built, but there is no environmental permit as yet), 500,000 cars will soon roll off the assembly line and they will be needing a lot of batteries.
Tesla as a driver of economic activity
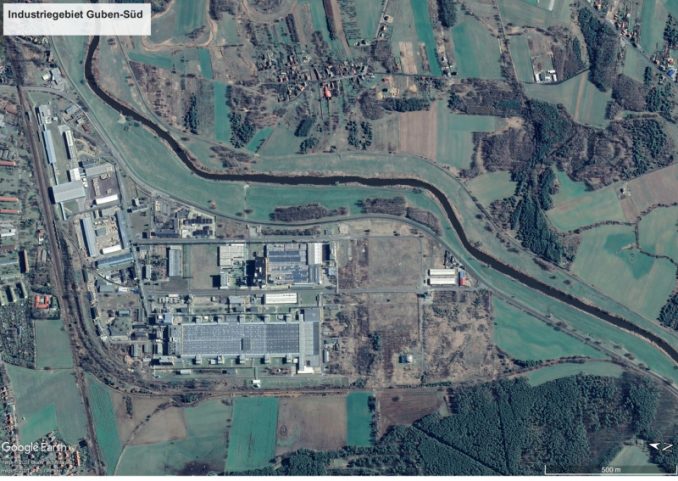
But it is not just in Brandenburg where the arrival of Tesla is being felt. The same holds true for the neighboring state of Saxony-Anhalt.
In Bitterfeld-Wolfen – at the time of the GDR one of the largest (and dirtiest) chemical cities in the world – a factory like the one in Guben is going to be built, only this time by the Dutch-American company AMG Advanced Metallurgical Group . The intention is to process about 20,000 tonnes of lithium there.
AMG lithium factory
“With this lithium production, an important part of the supply chain for electric cars will be brought to Saxony-Anhalt and we will be one step closer to our goal of enabling innovations to flourish in this region for the entire production chain,” was the enthusiastic response from Thomas Einsfelder, a senior official responsible for bringing in investors into Saxony-Anhalt.
According to Michele Fischer of AMG, the choice for Bitterfeld was not so difficult. “It’s right in the middle of the fastest growing center for batteries and electric cars, and it’s within easy reach of our customers,” she says calling from the US.
Who the customers and suppliers are, she doesn’t want to divulge just yet. “The negotiations are ongoing.” That Tesla is one of the potential customers goes without saying. But there are many more battery factories that are settling in the area:
- In Bitterfeld, for example, Farasis is building a battery factory that should be ready by 2022. The long-term goal is 16 gigawatt hours (GWh) of battery capacity per year.
- Near Berlin – in Ludwigsfelde (Brandenburg) – a Microvast plant (8-12 GWh) has been operational since the beginning of this year. They make batteries for large and small buses.
- Chinese CATL is building a 14 GWh plant in Erfurt (150 kilometers southeast of Bitterfeld), with the option of doubling it in size over time.
- To the northeast in Salzgitter, a large factory run by Volkswagen and Northvolt (24 GWh in the future) is set to be built. The batteries there are mainly for VW’s own use.
- BMW is doing the same but in Leipzig instead (40 kilometers from Bitterfeld).
Rock Tech wants to expand to 5 factories
For Rock Tech Lithium, the factory on the Polish border is just the beginning. According to chair of the board Dirk Harbecke, it is only in Germany that there is a “gigantic demand” for battery parts for electric cars made by the Volkswagen Group, BMW and Daimler. The Vancouver-based company therefore wants to build five factories in Europe. One will be added each year.
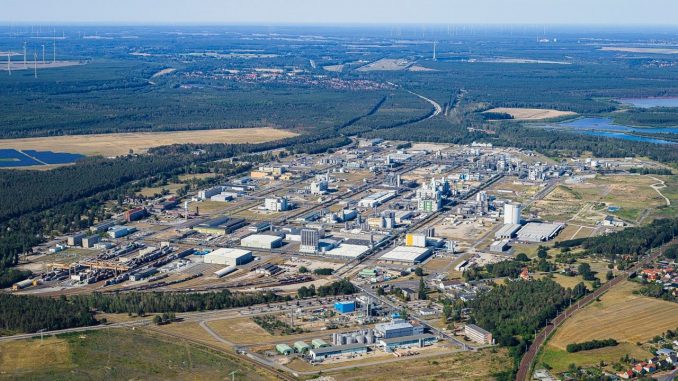
For the time being, the Canadians are still extracting the lithium from Canadian soil. However, this is set to change soon. By 2030, about 50% of the raw material is expected to be extracted from old batteries. This is also needed in order to be able to meet demand. The European Commission expects that 30x as much lithium will be needed in 2030 than today and even 60x as much in 2050. At present, almost all lithium still comes from Asia.
Analysts are anticipating that about 1.5 million tonnes of waste from discarded batteries will be eligible for recycling by 2030.
Cathodes and anodes
Obviously, much more is needed to make a battery besides lithium. This is another area where the East German states of Brandenburg, Saxony and Saxony-Anhalt want to play a role. And they are managing to do that quite well. A good example is the construction of a BASF factory for cathodes in Schwarzheide near Cottbus. BASF has big plans for battery technology. With cathode material alone, they think they can generate sales of 7 billion euros by 2030.
Raw material shortages are also a problem for BASF. This is why it wants to build a recycling plant in Schwarzheide for old batteries from which not only lithium but also cobalt and nickel can be recovered, all raw materials that are becoming increasingly scarce.