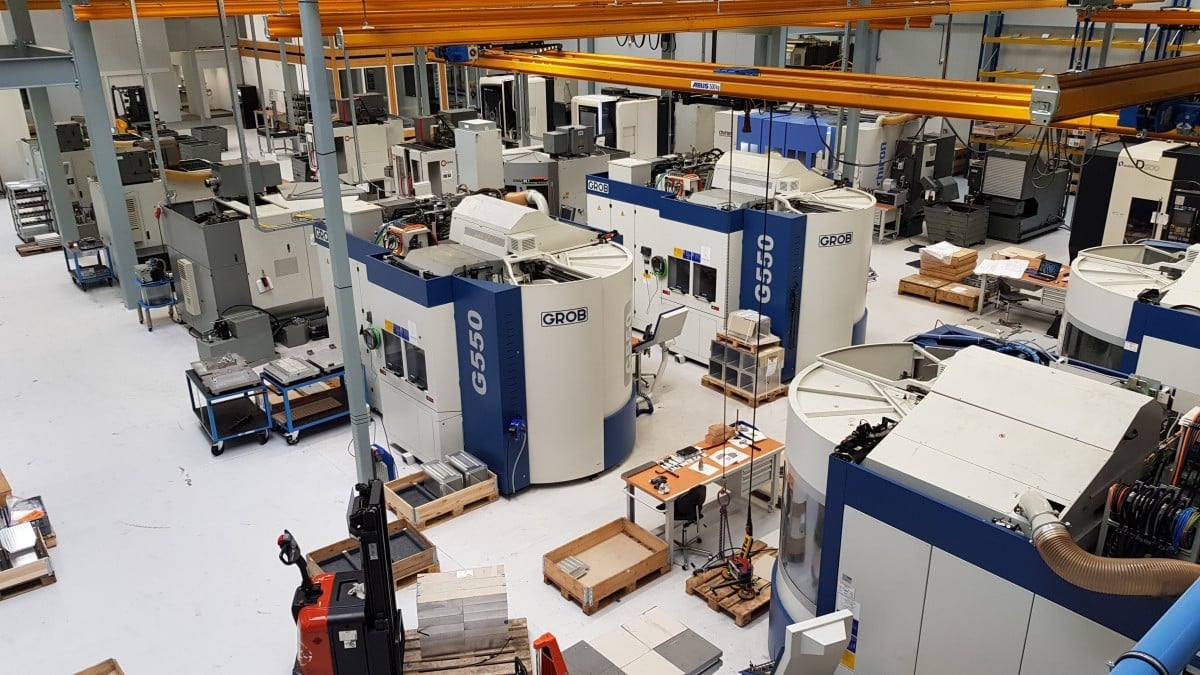
Several industries were hit hard last year when the coronavirus broke out. Especially industries that depend on parts from other companies for manufacturing. For example, the automotive industry, where major manufacturers assemble cars with parts sourced from global suppliers. If one of the manufacturers in the supply chain is unable to deliver, this causes a chain reaction. Thatโs what happened during the first corona wave. Due to factory closures and lockdown measures during the first corona wave last year the European automotive industry missed out on making 1.5 million cars.
In the high-tech manufacturing industry, producers are also highly dependent on their suppliers. If there is a hitch somewhere, the entire production process can grind to a halt. To prevent this and to make these manufacturing supply chains more resilient, they must become more transparent.
Matthijs Punter is working on this within the European project Market 4.0 on behalf of the Netherlands Organisation for Applied Scientific Research (TNO). In this project TNO is also collaborating with KMWE, a supplier to the high-tech engineering industry, and Brainport Industries, among others. The Limburg-based company Batchforce is participating in the creation of the software. Punter outlines what this transparency actually entails. And answers the question of how manufacturing companies can benefit from this. โA manufacturer keeps an overview of what is going on within the walls of a factory. They know exactly when a certain part needs to go to the next production station. If things go wrong somewhere, for example, due to a breakdown, they notice that and can quickly adjust their planning accordingly.โ
The secret? Sharing information
Whereas there is an overview within factory walls, that is not always the case in the supply chain. For instance, parts sometimes arrive at a factory too late without any prior notice. Or manufacturers occasionally have to chase up orders over the phone. โThis throws the entire production process out of synch, especially in the manufacturing industry where parts are extremely specific. You canโt just get something from somewhere else. But whenever a major manufacturer like ASML knows in advance that one of their suppliers canโt deliver a part or deliver it on time, they are able to prepare for that.โ
The secret, according to Punter, lies in sharing information. At present, manufacturing companies use a variety of different software systems to keep track of schedules, orders and other practical matters related to the production process. This creates a problem. All these different software platforms make it difficult to share data. Systems donโt โtalkโ to each other. Just like you canโt send messages from Facebook to Twitter.
The Smart Connected Supplier Network
This is what the Smart Connected Supplier Network (SCSN) has been designed to solve. A standard for data sharing that ensures that companies are able to exchange information with each other, no matter what. Without it mattering which service provider or software system they use. This is comparable to how you can call someone with a different network provider or another type of phone. The former field lab at the Brainport Industries Campus has now evolved into a foundation. The aim is to gain a foothold not only in the Netherlands, but also in Europe. Work is being done within Market 4.0 to expand this standard further. Market 4.0 is a collaboration between 18 European partners in which three similar cases are being fleshed out. Besides the Dutch section for the high-tech manufacturing industry, work is underway in France to gain the same insight into the supply chain for plastic composites. And in Spain, the focus is on the purchase of metal-processing machinery.
Sharing information in an uncomplicated way
Punter: โThe manufacturing industry is broader than just the Netherlands, we want to set a standard for the whole of Europe. And at the same time we want to expand it with new functionalities. This not only enables manufacturing companies to send information more easily through the chain, but also gives them more control over their own data. This will enable them to develop additional functionalities. Such as digital twins, simulations or to set up collaborations with other companies more quickly.โ
But before these extra functionalities are developed, Punter says it is important that the chain is first closed. โSome small suppliers at the bottom of the chain are not using any software or IT system to keep track of schedules and orders. This creates a kind of blind spot in the chain because information is missing in these spots. Manufacturing companies above these small parties have no insight into the status of their orders. Rubix, which is also involved in the project, is running up against this in Germany with roughly 1,400 parties in total.โ
โWe have now developed an app in The Netherlands that allows these companies to provide easily accessible information about their production. By also connecting these small parties, we are closing the chain and making it more transparent. More than 2.3 million euros has already been allocated over the past two years so as to connect manufacturing companies and service providers with the Market 4.0 project. We expect to see the preliminary results of these projects very soon.โ
This article was written with the help of Mike de Roode (TNO).