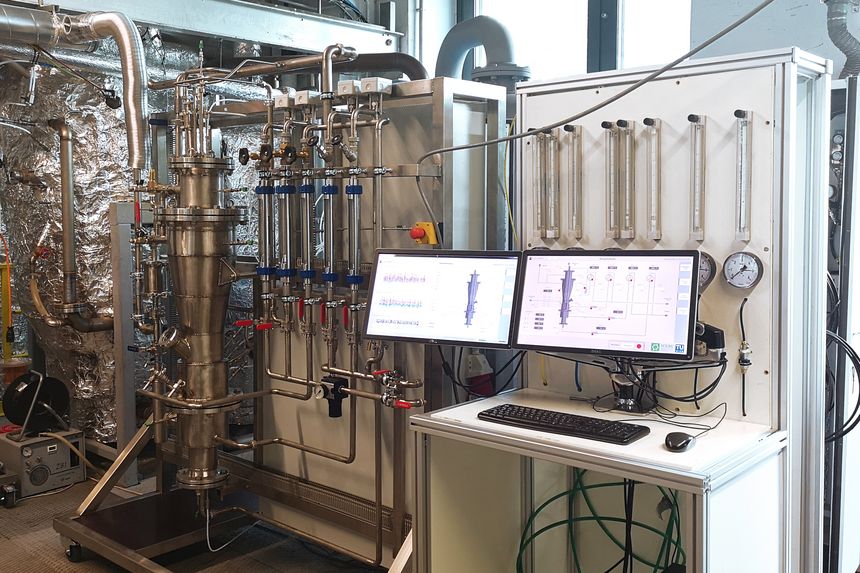
Biogenic waste comprises plant-based waste from industry and waste of the kind that accumulates in municipalities. Examples are sewage sludge, lignin and bark. If solid waste such as bark is simply left to decompose out in the open, then its energy potential is wasted. Burning this solid waste to generate electricity and heat is an initial step. But it is by no means an ideal solution. This is because energy can be used in that combustion process, but not stored.
Another approach is to produce a combustible gas product ( gas fuel) from biogenic waste materials. Water vapor, air, oxygen or carbon dioxide are used as gasification agents. However, existing technologies, such as the fixed bed air gasification process commonly used in wood gasification power plants, have one major drawback: The resulting gas product has a high nitrogen content. This does not matter for electricity and heat production. However, if you want to convert the gas product into green gas (synthetic natural gas), you have to first remove the nitrogen from it with the aid of an elaborate process.
Also interesting: New emission-free method for producing hydrogen and carbon from natural gas
Another problem with fixed-bed gasification processes is that they require a homogeneous fuel mixture. However, this is not the case with plant waste from industry and waste from municipalities. The chemical composition as well as ash and water content tend to vary in these.
Dual bed fluidized bed process
At the Institute of Chemical, Environmental and Bioscience Engineering (part of the Vienna University of Technology, TU Vienna, Austria), research has been going on for several decades on a CO2-neutral technology for the conversion of biogenic waste materials into an alternative energy source. This research resulted in the dual fluidized bed process. Which is already being used on an industrial level to produce gas from wood chips and forest waste. These types of power plants are in operation in Austria, Germany and Sweden, as well as in Asia.
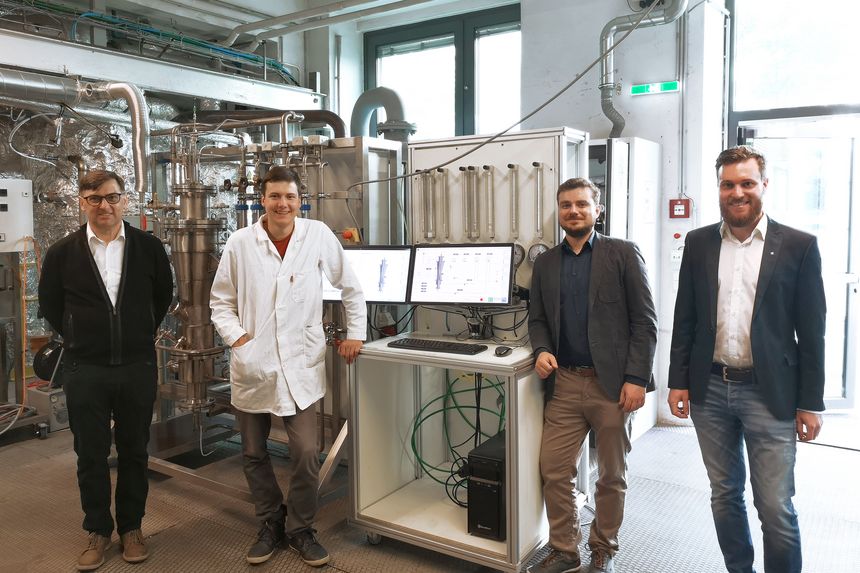
Nitrogen problem is addressed
In the ongoing ReGas4Industry project, the institute is carrying out joint research with the SMS Group, a global partner for the metal industry. The team developed an experimental plant that is suitable for a broader range of biogenic waste materials (fuels). A variety of process chains not only allow the production of synthetic gas, ultra-pure hydrogen and liquid fuels with diesel-like properties can also be produced. However, the production of hydrogen is not under consideration in the project.
The experimental plant also addresses the problem of nitrogen. The resulting gas product contains hardly any nitrogen, which would otherwise make the synthesis process more difficult.
The experimental plant will be used to examine the fuel properties of various types of biogenic waste. The focus is on sewage sludge, digestate from a biogas plant, rejects from the pulp and paper industry, and bark and lignin.
Gasification of biogenic waste
The process runs through two reactors: One for gas generation and one for combustion. The basis for the separate syntheses is the gas that is produced. It is created in the gas generation reactor, where biogenic waste is exposed to high temperatures and water vapor. Parts of the biogenic waste that are not converted into gas are fed into the combustion reactor. Once there, they are burned to provide energy required for gas generation. Heat is transferred via hot sand that circulates between the reactors.
In a further step, the gas that is produced is fed into a connected gas purification section and synthesis unit, where it is first purified and then processed into synthetic gas (methanation). In this step, the carbon monoxide or carbon dioxide contained in the gas is converted with hydrogen into synthetic natural gas.
Methane and hythane
The alternative energy sources that result from this process are methane and hythane. Hythanes are a blend of hydrogen and methane.
During synthesis, the researchers study basic reactions and mechanisms of the various biogenic waste materials. They are modeling the experiments with the help of process simulations in order to collect data on the technology, economic efficiency and environmental friendliness. The. intention is to highlight the potential for industrial applications.
Carbon dioxide versus steam
Gasification is usually carried out with steam since a higher proportion of hydrogen is required for various synthesis reactions. In the test facility at the Vienna University of Technology, CO2 or a mixture of CO2 and steam can be used as an alternative to steam.
If biogenic waste is gasified with carbon dioxide, gas produced contains a higher concentration of carbon monoxide. This enables CO2 to be recycled. This is because the CO2 is converted back into CO2, which can then be used in syntheses or as a combustible fuel.
Furthermore, this gas produced could also be used for a power-to-gas concept. “When we gasify using carbon dioxide, we end up with a higher carbon monoxide content in the gas produced. In order to be able to methanize this gas then, additional hydrogen has to be added by means of electrolysis, for example. The hydrogen concentraion in the gas produced is not enough,” explains project member Alexander Bartik from the Institute of Process Engineering, Environmental Engineering and Technical Biosciences at the Vienna University of Technology.
Testing biogenic waste materials
The tests have been running since April 2019 and the researchers have already tested several types of biogenic waste in gas production. In the process, even plastic waste from sorted household waste was able to be converted into gas. “That is not biogenic waste, and it’s not CO2-neutral, but at least the carbon could be converted into an energy carrier one more time before it is released into the atmosphere,” Bartik notes.
However, bark and sewage sludge were the most promising sources. About 10.5 petajoules of synthetic natural gas could be produced from available resources of bark in Austria, and 1.3 petajoules from available sewage sludge resources. This corresponds to about 3.7 percent of the annual natural gas consumption in Austria and would result in a substantial reduction in CO2 equivalents: Replacing just 1 percent of natural gas with synthetic natural gas would save 121,600 metric tons of CO2 equivalents per year.
The potential is endless
Yet “the potential is endless,” according to Florian Benedikt of the Institute for Process Engineering, Environmental Engineering and Technical Biosciences at the Vienna University of Technology. That’s because they are tied to the local availability of biogenic waste materials. “It would not make sense to import biogenic waste materials from other countries or even continents. Then you really need to build decentralized solutions,” Benedikt points out.
Also interesting: RENEWABLE ENERGY: ELECTRICITY BECOMES GAS
From a technical perspective, bark would also be preferable on the grounds that it has the best combustible properties of the various biogenic waste materials currently being used and also produces high-quality gas. In comparison, the quality of product gas from sewage sludge is poorer and requires more purification. However, sewage sludge would be preferable from an economic point of view, the researchers say. This is because sewage sludge is paid for when it is disposed of. Consequently, it would have a negative cost price.
Biogenic waste in industry
The synthetic natural gas (SNG) produced in the experimental plant is suitable for supplying the gas grid. And it can also replace fossil-based natural gas in general. In industrial applications, however, it could also be replaced by the less expensive combustible gas hythane, the production of which is also being studied in the ReGas4Industry project. Eligible industrial sectors are those in which high-temperature processes are used. Examples are the rotary kilns in the pulp and paper industry. As well as and in the cement industry, where it is used for burning lime. Synthetic natural gas could also be used for blast furnaces such as those used in the steel industry.
In the current project, the focus is on the pulp and paper industry and other energy-intensive industries. Their biogenic waste materials and common substitute fuels, such as bark, are being studied. Owing to the large reserves of wood, the paper and pulp industry in Austria is particularly dynamic. Half of Austria’s national territory is covered by forest and the abundant wood resources incentivize a buoyant industry. The industry generated sales of 4.2 billion euros in 2019 (source: Austropapier).
About the ReGas4Industry project
The project is funded by the Austrian Climate and Energy Fund and is part of the Energy Research e!MISSION program. Project partners are the SMS group Process Technologies GmbH, a global partner for the metal industry, along with Energy & Chemical Engineering GmbH, an engineering company for process technology based in Vienna.