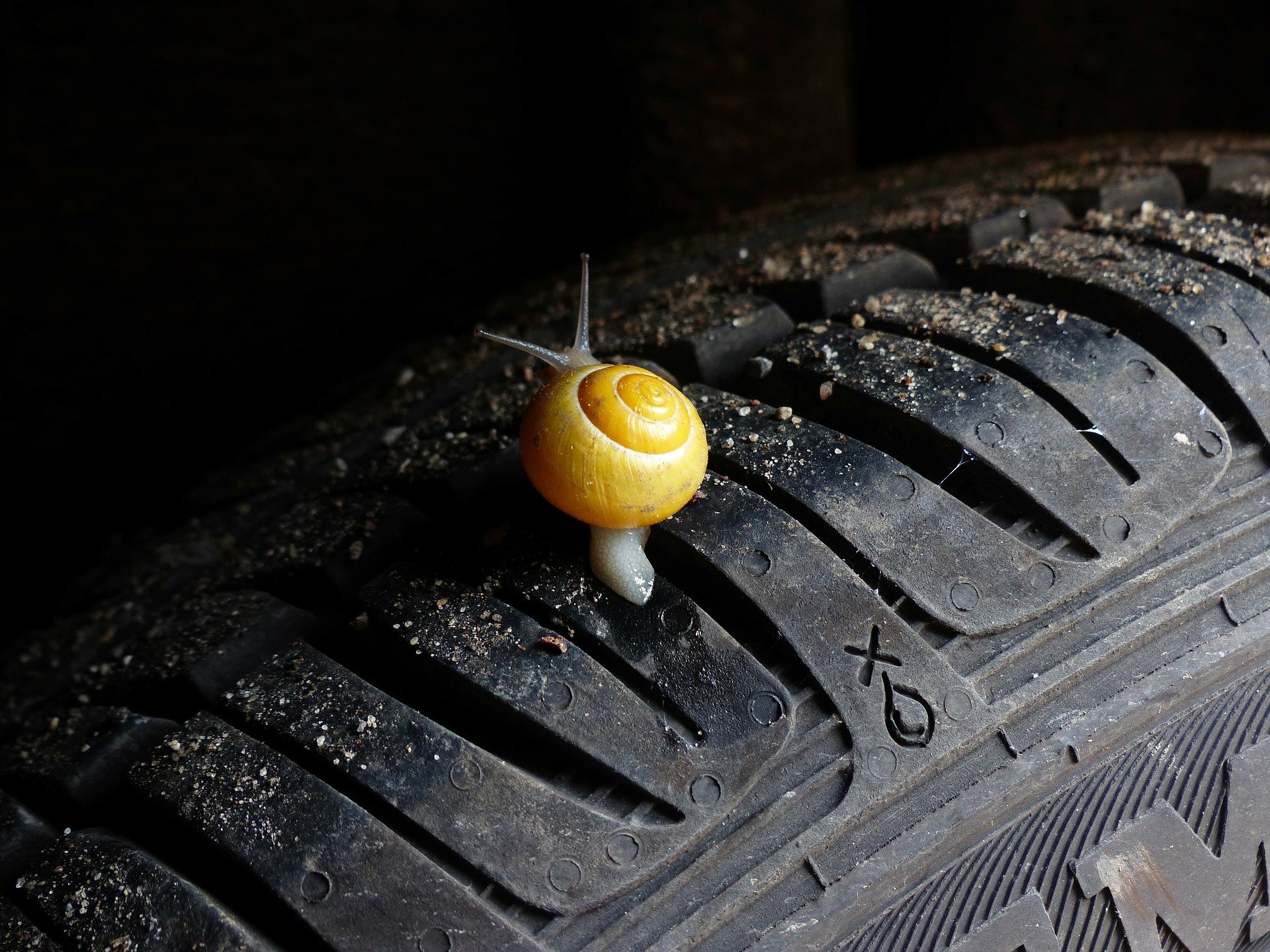
Butadiene doesn’t ring a bell with most people, yet there’s a good chance we’ve all come into contact with this organic compound. It is found in the soles of the shoes we wear, in the tires of our cars and in all kinds of different plastics that we use. The gas is created as a byproduct during the cracking of naphtha in the production of ethylene, among other things. It is also a commonly used building block for plastics.
Except that cracking naphtha is not exactly a sustainable process. Heating the ovens to around 900 degrees costs a lot of energy and lots of emissions are released into the air during this heating process. Which is why scientists and start-ups are looking for cleaner alternatives for making the various building blocks for plastics.
ETB Catalytic Technologies, originally from Russia, is one such start-up. On the Brightlands Chemelot Campus in the Dutch city of Geleen, the team is working hard to bring their cleaner production method for butadiene to the market. How does it work? CEO Noah Vladimir Hirsch Trembovolsky explains. “We have created a catalyst that converts bioethanol into butadiene. This is currently done on a semi-industrial scale, but we intend to scale this up. Not just to show that it does work, but we want people like you and me to be able to use biobased end products. We want to reinvent the value chain,” he clarifies.
Old technology in a new guise
The technology which converts ethanol to butadiene is not new and was first discovered in the early part of the last century by Russian chemist Sergei Lebedev. Leading up to World War II, the technology was used primarily by the Soviet Union as an alternative to natural rubber that frequently came from English-owned plantations. By making synthetic rubber from butadiene, the Soviet Union was no longer reliant on England. Trembovolsky remarked with a slight chuckle, “This is political history and it obviously goes much deeper. But that’s another story.”
As the chemical industry boomed and naphtha crackers became the norm, Lebedev’s technology disappeared from view in the 1960s. “Naphtha crackers mainly produce ethylene, but also other chemical raw materials for the medical industry, for example. Butadiene is one of the residual products that is released in this process. So the price plummeted dramatically; it was no longer profitable to make butadiene from ethanol.”
But according to Trembovolsky, this has started to change recently. More and more, shale gas is being cracked instead of naphtha. This method yields significantly less butadiene. “As a result, the price of butadiene is far from stable. And sometimes there are even shortages, which drives prices up even further. An alternative is needed. Our technology is one such alternative, with the great advantage that it is a lot cleaner. Especially when it comes to using bioethanol made from grain, for instance.”
Fewer emissions and lower energy consumption
When asked how much cleaner, Trembovolsky is unable to name an exact figure at this point. “This is a difficult comparison to make. In a naphtha cracker, butadiene is a byproduct; the energy does not go directly into the production process. But if you compare it to other processes, where butadiene is a main product, our emissions are about three times lower.”
It all started in 2010 at the University of Moscow (Lomonosov Moscow State University), where Trembovolsky’s team revamped the “forgotten” technology into a modern form. “Look at the climate and all the challenges that come with it. The chemical industry also has to become more sustainable. We want to use biobased raw materials for this and are convinced that this can be done. At first we started with lab experiments; we had to find an alternative for some of the materials in the original catalyst. These were no longer available on an industrial scale. In addition, the original technique was not efficient enough; we wanted to improve that,” Trembovolsky recalls.
To Brightlands Chemelot
They managed to do just that in collaboration with the ‘best scientists, engineers and chemists at the university’. Trembovolsky and his team succeeded in making a more advanced catalyst. He prefers not to give specific numbers. According to the CEO, the new technology produces a lot more butadiene, while requiring a lot less energy.
After successful trials in Moscow, a lengthy market study followed and then ETB patented their technology in several countries. “We want to be close to our customers, so we looked at several countries where green butadiene could become big,” he says. At the time, Trump was still in office and he was going full fossil. So America dropped out quickly. Europe had been talking about becoming more sustainable for some time. The Green Deal that is currently being developed also fits in with our philosophy. That’s why we decided to go to Europe. We came into contact with a scout from Brightlands Chemelot at Slush in Finland.”
Scaling up production of green butadiene
Trembovolsky candidly admits that he had never heard of Geleen before. But after listening to a detailed explanation, he became enthusiastic and decided to take the plunge with his team. “It’s really interesting to be together with so many different chemical start-ups, you learn a lot from that. Also, you have several major players here and the contact with universities is excellent. It’s a good place to start from in Europe.”
In the meantime, ETB has outgrown the lab, which is why he believes the Brightlands Chemelot Campus is the ideal place to keep on growing. To this end, the company is constantly looking for partners to make the value chain more sustainable and to scale up the production of green butadiene. For a pilot plant in Europe, ETB has already signed an agreement with Trinseo, an international chemical giant that is particularly big in the production of synthetic rubber. Trinseo will use the bio butadiene from this plant to make synthetic rubber for tire production. “We plan to test on an industrial scale in this plant whether the bio butadiene can be used higher up in the production chain for more sustainable rubber and green tires. This collaboration represents the first step towards a cleaner and more sustainable value chain, as butadiene is used in many more products.”