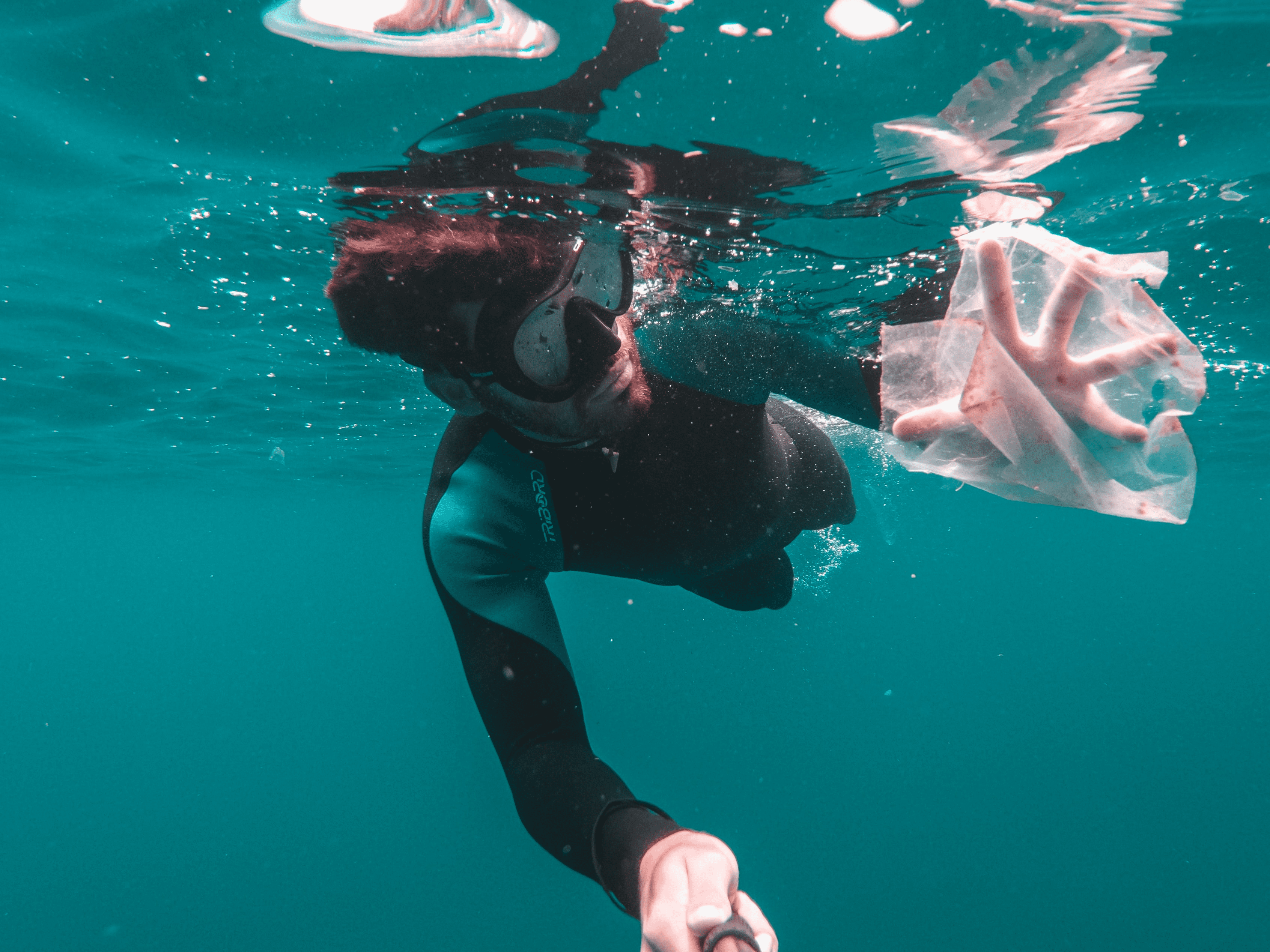
Light yet strong, easy to mold and shape, and wear-resistant. Plastic has them all. These features made it so convenient to use to the point of becoming the go-to material for hundreds of applications. The other side of the coin of such convenience is the resulting throw-away culture. Many plastic objects we use every day only last a few minutes – to wrap some food or carry groceries home. Conversely, bags, bottles, and films remain in the environment for hundreds of years, affecting oceans, wildlife, and our food too.
OECD estimated 367 million metric tons of plastic waste in 2020. This figure is expected to triple by 2060.
Plastic can stick around for centuries. For instance, a plastic bottle can take up to 600 years to decompose.
According to OECD, less than a tenth of worldwide plastic is recycled. In the EU, 41 percent of packaging plastic was recycled in 2019.
In addition to bans on single-use plastics, EU countries are introducing a plastic tax. These duties change state by state – albeit part of the European Green Deal strategy – tax businesses consuming non-recycled plastic.
If, on the one hand, norms can help – such as bans on single-use plastic – on the other efficient recycling methods represent a necessity. Several types of plastic cannot even be recycled. They get burned and the resulting heat can eventually be collected and used as energy. However, most plastics end up in landfills – staying there for centuries. European researchers are working on solutions to tackle this problem, and here are a few examples.
Greasy plastic
TUSTI is striving to improve plastic recycling, focusing on some of the most challenging fractions of this waste: the greasy ones. The firm, based in Eindhoven, the Netherlands, developed an innovative method to treat this waste without heating the material at high temperatures or using hazardous chemicals.
Plastic is shredded into tiny pieces, which are washed with a patented pending cleaner. Then, fractions are dried and packed into bags to reach the closest recycling facilities.
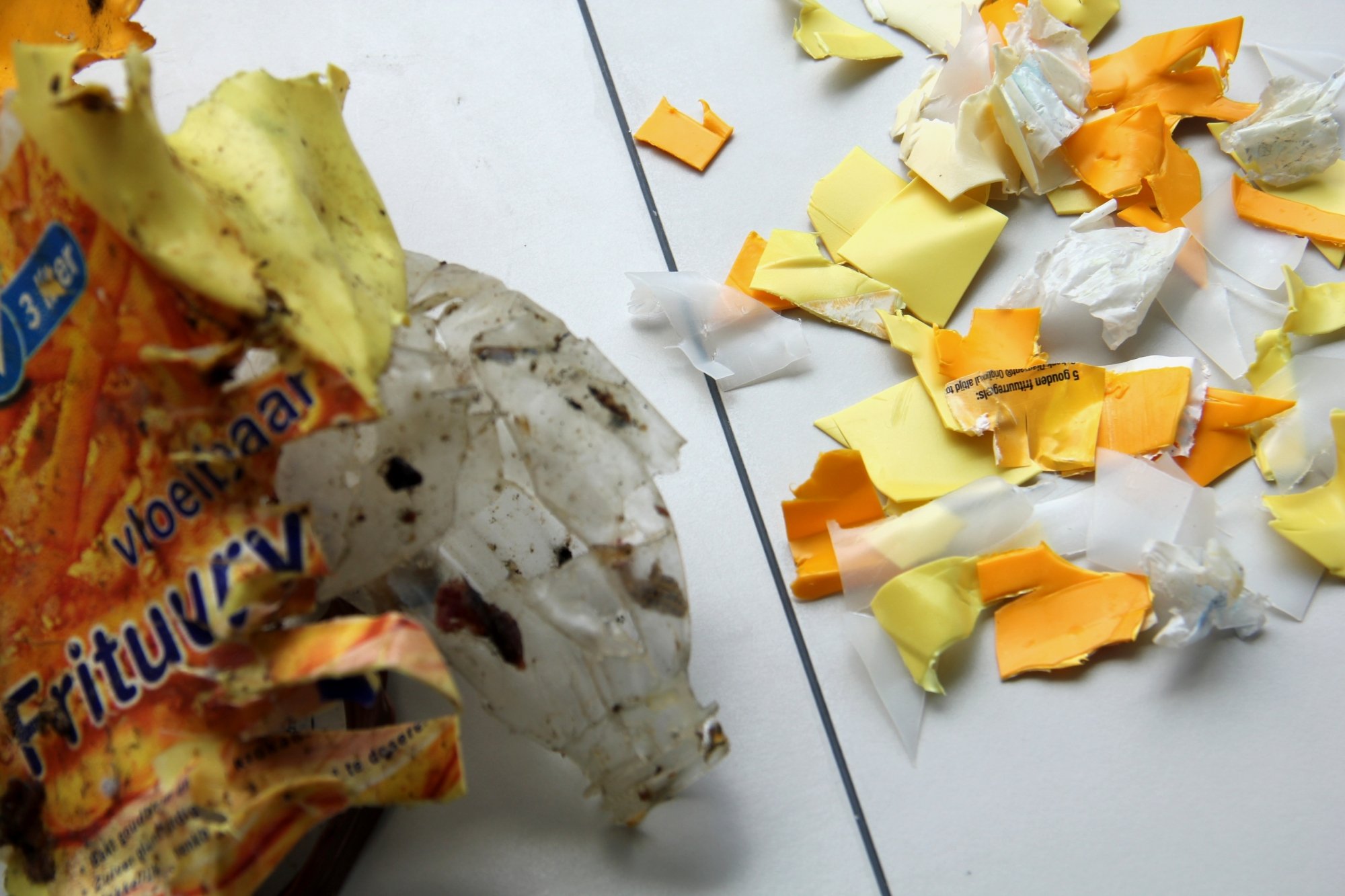
Infrared and AI for plastic recycling
Sorting plastic films is one of the main constraints to their recycling. They can either be single-layered – such as toy wrapping – or multi-layered – such as food packaging. To distinguish between the two varieties of plastic, scientists at the University of Leoben, Austria, are using near-infrared light. The research aims to see the difference in radiation between the two kinds of material. Researchers use a neural network to spot the differences between single and multi-layered plastics.
If the process works out fine, films will return to the product cycle, potentially being able to be reused several times. Manufacturing consumption would decrease while saving tons of CO2 emitted to produce new plastics.
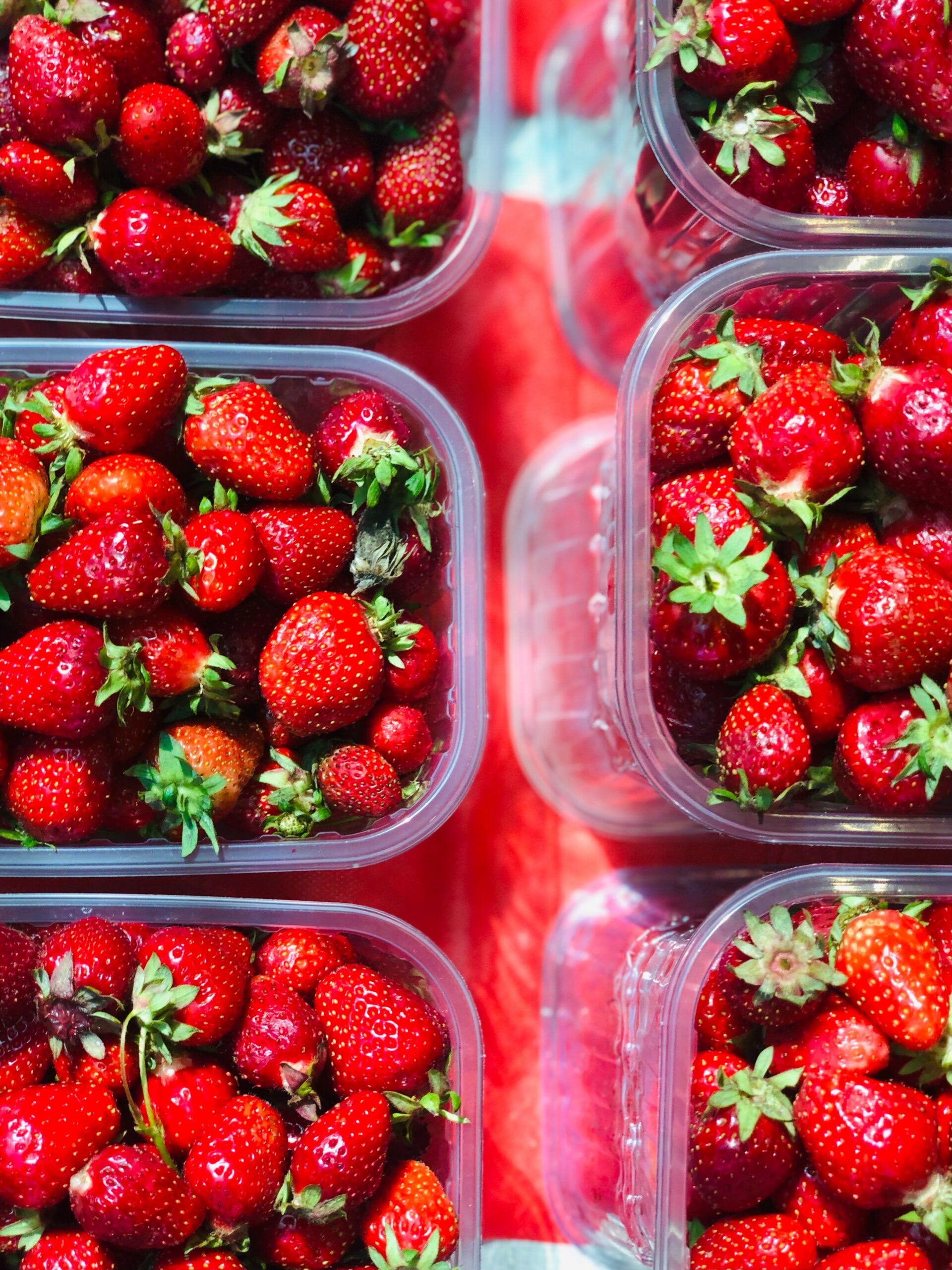
Plastic-eating enzyme
Plastic objects can take up to 500 years to degrade. Is there anything we could do to boost this process? Enzymes can undoubtedly be a good option. By nature, they are proteins that accelerate chemical reactions – such as human metabolism.
Scientists at the University of Portsmouth, England, engineered PETase, an enzyme that breaks down PET plastics used for single-use drinking bottles. The protein can degrade discarded plastics, reducing the time needed for recycling. Last year, they announced that they characterized another enzyme that helps break terephthalate – one of the PET building blocks – resulting after PETase action.
Polyurethane recycling
Polyurethane – PU – is one of the most used commodity plastics. Windows, fridges, and shoes contain it – it can be shaped in countless forms. A team of scientists at Aarhus University, Denmark, found a way to recycle this material, getting as an output of the process the essential compounds composing it.
By heating the material with alcohol – a special one called tert-Amyl – and potash – a class of minerals containing potassium – PU breaks down. Researchers proved the method with several kinds of PU, patenting it.
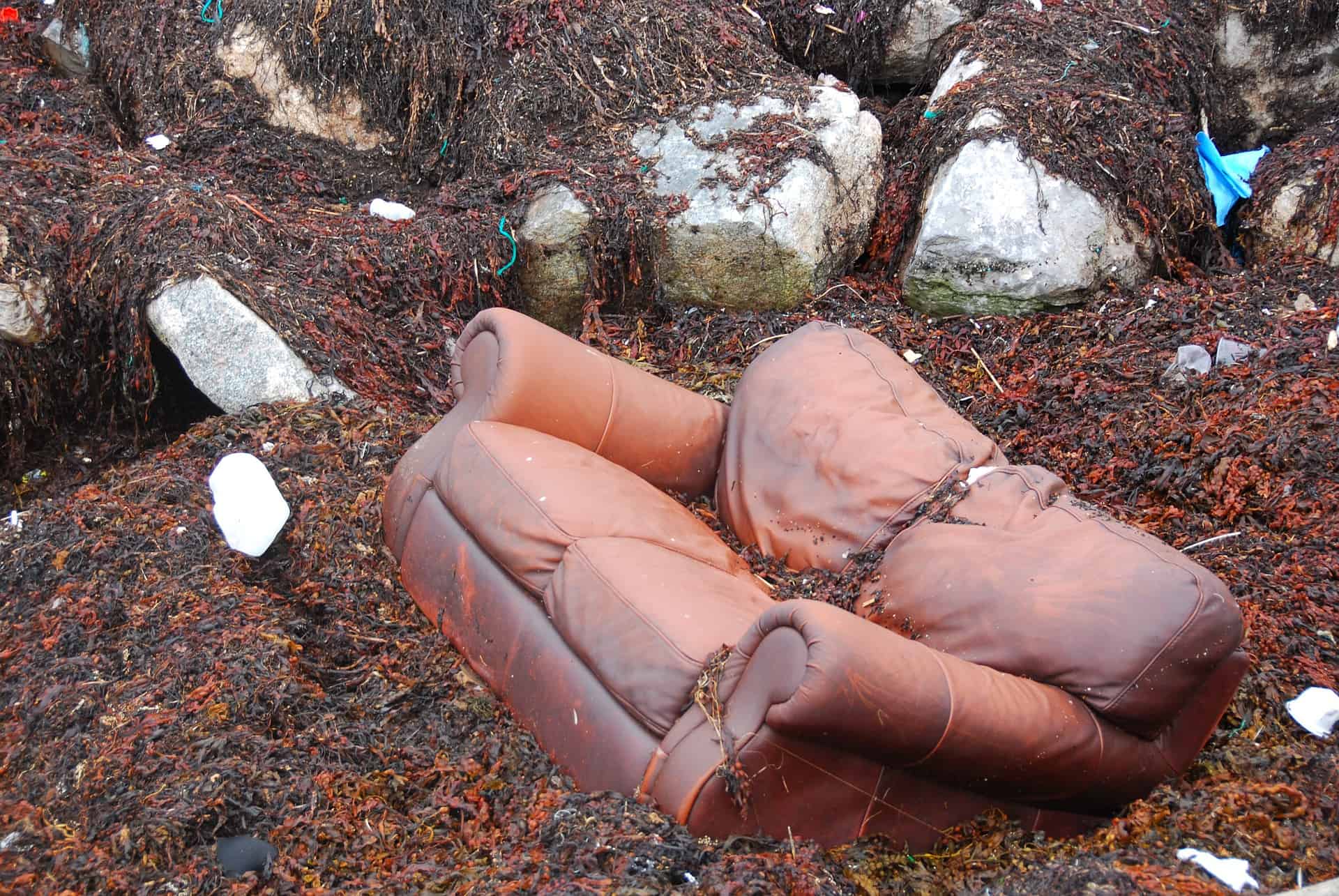
Thermo-chemical recycling
At the Chalmers University of Technology, Sweden, scientists are experimenting with new technology: thermo-chemical recycling. This method allows turning waste into new plastics. In fact, they developed three processes for recycling plastic: pyrolysis, gasification, and combustion plus synthesis. Each of them targets different kinds of plastic – clean or mixed – allowing the production of high-grade plastics.
The method distinguishes itself from mechanical recycling, which works well for clean and small materials. Furthermore, thermo-recycling enables the production of high-grade materials by requiring less energy for plastic output than when producing them from fossil fuels.
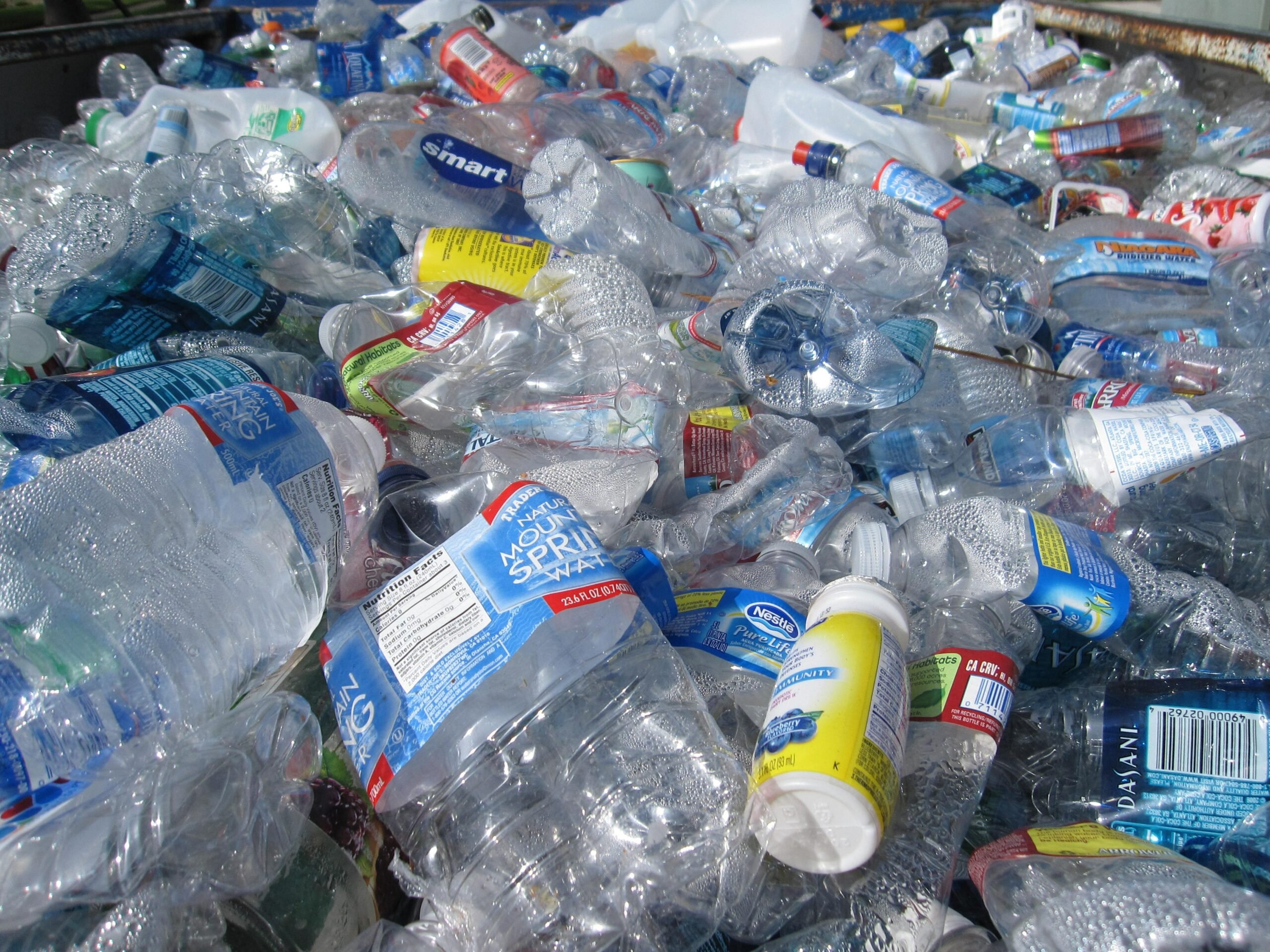
What’s going to help?
Enzymes, chemistry, and AI, we have plenty of allies in recycling plastics, and we will need all of them to recycle as much as possible.