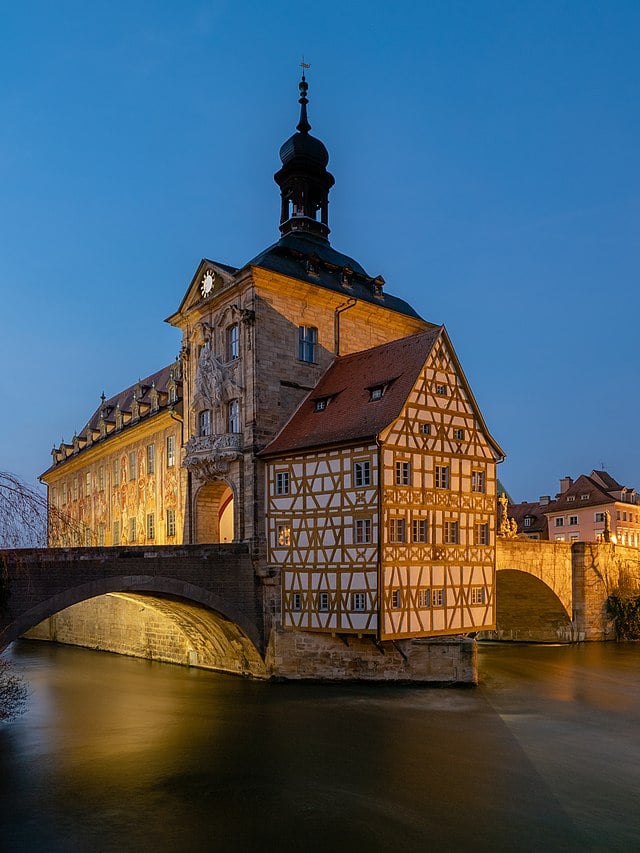
The city of Bamberg in northern Bavaria is known as Little Venice because of its many canals. Spared by WWII bombs, historic houses with latticed frameworks grace wide canals crossed by historic bridges, which all need regular maintenance. This is about to become a lot easier and less expensive with new technology using big data and a digital twin. Its name: the intelligent bridge.
German law requires two walk-through inspections of each of its 100,000 bridges per year. On top of this comes a more thorough bridge inspection called Bridge TรV 1076, mandated every six years. Finally, standard maintenance procedures are required at regular intervals, regardless of the bridgeโs actual condition. These inspections all cost significant time and money. With the intelligent bridge, they could not only be done virtually but provide a constant flow of maintenance data in real-time. This would allow issues to be detected and rectified earlier. It could potentially even prolong the life of the bridge.
To create a digital twin of an object, a component is sent through the production facility. Along the way, it generates data at each production stage that are then combined to create a digital twin of the actual object. This virtual copy then serves as the basis for configuring further production and processes.
A digital twin of the Heinrich Bridge will serve as the basis for detecting cracks, deformation, carbonation, corrosion and other required maintenance on the bridge. Previously, the data provided on the bridge originated from various sources: planners, construction engineers and inspectors. This information was all provided in different formats and some was still being provided on paper.
These varying formats have prevented the creation of a digital twin up until now because the centralization of the data was not possible. That is now changing with the new smart bridge. All data will be standardized and automated. As soon as the digital twin of the bridge goes online, computers at the University of the Federal Armed Forces (Universitรคt Bundeswehr) will be able to calculate how traffic is affecting the condition of the Heinrich Bridge based on these data. Additional planning and mathematical models such as Building Information Modeling are also underway. Initial results of the prototype of the intelligent Heinrich Bridge of Bamberg are already expected in the second quarter of 2021.
This is just the beginning. In addition to being applied to other bridges, this model of using data collected via smart technology could support the development of new building materials. Ideally, digital twins would be created for future structures already during the building phase. This would enable the builder and engineer to detect and correct errors early, reducing cost and construction time.
Several companies and institutions worked together on this project. The Fraunhofer Institute for Experimental Software Engineering IESE produced the required software for this project, BaSys 4.0. There is also an open-source version called Eclipse BaSyx. The company NetApp created the data infrastructure and containers using Kubernetes and a central virtual memory. The company Objective Partner AG assisted with digitalization. The Fraunhofer Institute for Integrated Circuits (IIS) outfitted the Heinrich Bridge with sensors for the transmission of data.
Experts involved in the project include Dr. Thomas Braml and Johannes Wimmer, Bundeswehr University Munich; Dr. Stefan Maack, Stefan Kรผttenbaum, Federal Institute for Materials Research and Testing; Dr. Thomas Kuhn, Fraunhofer IESE; Maximilian Reingruber, Alexander Gordt, and Andreas Bader, Objective Partner AG; Dr. Peter Spies, Fraunhofer IIS; and Jรผrgen Hamm, NetApp.
Short interview with Jรผrgen Hamm, Solutions Architect at NetApp
Explanatory video on digital twins