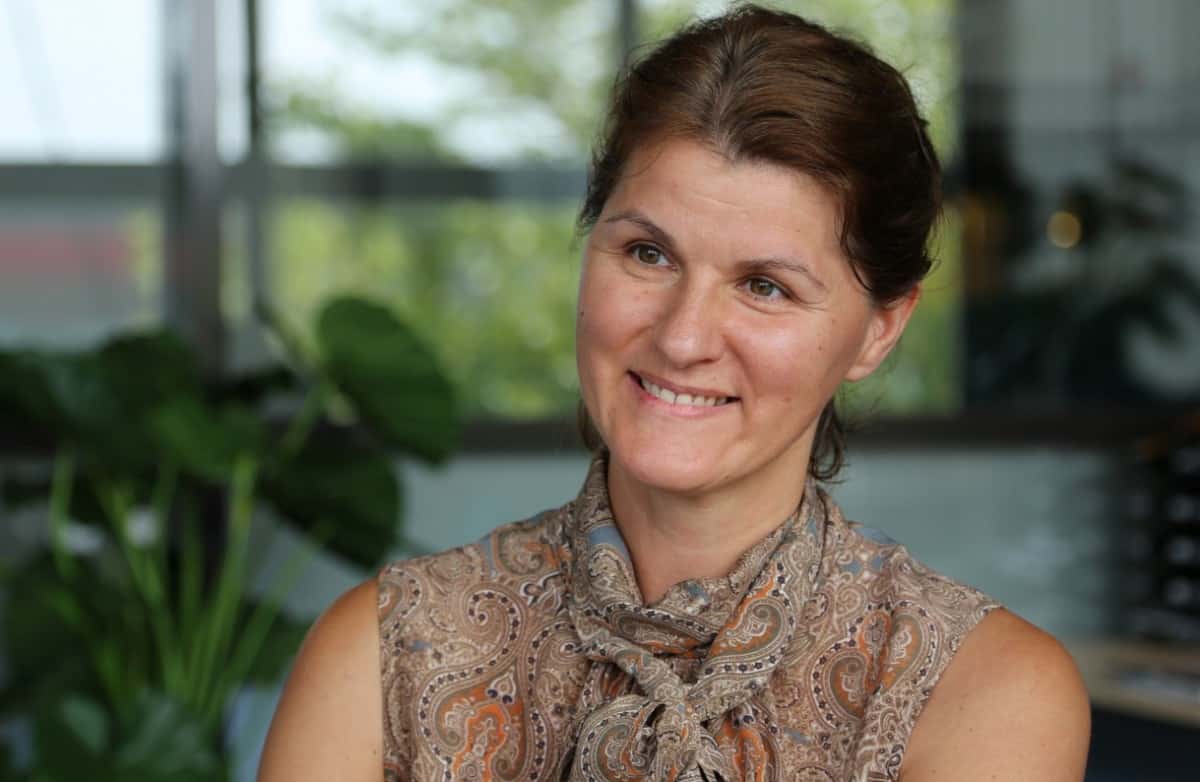
A very clever industry incubator is taking shape on the campus of the University of Twente. It’s the latest move by Fraunhofer, Europe’s largest application-oriented research organization. With 72 institutes and research units across Germany and a research budget of €2.3 billion, this network is already making a significant impact on many European societal needs. That includes health, security, communications, energy and the environment.
Read more about the cooperation between Fraunhofer and Eindhoven here
Dr Biba Visnjicki is Director of Business Development at the Fraunhofer Project Center in Enschede. She explained to Jonathan Marks the impact their plans will have on the European Photonics Industry.
“People sometimes forget that profits are made by manufacturing products, not in the research and development.”
“Fraunhofer chose to partner with the University of Twente not only because it’s at the heart of one of the world’s leading clusters in optics and nanotechnology. But also because of its international reputation for production and manufacturing competencies.”
Photonics: measuring what cannot currently be measured
“Light-based technologies are proving to be the key to building smaller, cheaper, faster devices to solve many grand societal challenges. Photonics is already having a knock-on effect in various sectors, including healthcare (precision tools in surgery, faster DNA sequencing), next-generation 5G Photonics networks, Ultra-Secure Quantum computing, self-driving and driver-assist vehicles (LIDAR), infrastructure monitoring in aircraft, food safety tests for pathogens as well as environmental monitoring both on earth and from space. These are all areas that interest us in Fraunhofer.”
Why European Photonics Needs to Scale
“European regions like Overijssel, Gelderland and North Brabant (especially the Brainport Eindhoven Region) want to maintain Europe’s lead in both the development and manufacture of Photonic Integrated Chips. Scaling up to volume manufacture of chips and complete product systems is essential for a prosperous and environmentally sustainable industry sector. Scalable production technology has been key to other high-tech sectors like automotive LIDAR-Systems, Datacom-Applications, Consumer Electronics and many more.”
Several Fraunhofer institutes in Germany (e.g. Heinrich Hertz Institute in Berlin, or the Institute for Production Technology in Aachen) are active members within the European Photonics Alliance, an initiative started by PhotonDelta. Because of the complex, expensive nature of these nanotechnologies, Europe needs an inter-regional collaborative approach if it wants to successfully scale up its leading photonics companies. They are responding to a need to stabilize and scale Photonic Integrated Circuit production platforms to provide qualified, tested and functional samples with guaranteed delivery dates. Large international corporate clients are demanding a path to cost reduction through modular scale-up production of PICs, packaging and testing.
Understanding the path to growth
“Over the last two years, we have been listening to the needs of leading companies in the Dutch photonics industry. Most innovative companies can build a few dozen working samples of their devices. Scaling up to make 100,000 to a million pieces a year to meet growing customer demand is always more difficult.”
It is important to remember that the microelectronics industry and photonics are at very different stages of development. The semiconductor sector is dominated by huge multi-national players who operate and act globally. But, according to European Photonics Industry Consortium (EPIC), around 60 per cent of European photonics companies have less than 100 employees. Yet they are driving breakthrough innovation in many other high-tech sectors, punching above their weight in very advanced high-quality solutions. So how will these companies grow and prosper?
“In today’s photonics industry, only 20% of the costs are in the design and manufacture of photonic integrated circuits. But these systems-on-a-chip need to be accurately connected to the outside world in order to function. That’s why packaging and assembly processes currently account for 80% of the costs in photonics system development and production. That must change. Part of the reason is that the assembly processes are still done manually under a microscope with all kinds of tools. The result is very dependent on the skills of a human operator and there is always a natural limit to how fast they can work.”
So why do many European companies still do most of their assembly processes manually? “They claim that’s because they work in niche markets, with low volume requirements. Others explain that the investment for automation is too high and the return on investment too long. Yet, Fraunhofer’s wide experience in semiconductor and laser manufacturing tells us that you don’t need very high volume before that value “tipping point” in favour of automation is reached. As the market matures and much shorter time to market becomes essential, photonics companies are therefore considering production automation much earlier. That’s where the expertise at the Fraunhofer Project Center in Twente comes in.”
“Most innovative companies can build a few dozen working samples of their devices. Scaling up to make 100,000 to a million pieces a year to meet growing customer demand is always more difficult.”
Interconnection of manufacturing processes such as Real-time Testing
Automation not only improves the yield and quality of any photonics product. It becomes simpler to integrate real-time testing or interconnect manufacturing processes which have been separate until now.
“Testing is key in both high and low volume manufacture. Think of a high-volume production company, where the failure of 10 devices is insignificant compared to the other 10 million that do work. On the other hand, there are companies whose business model is to produce 100 high-spec lasers a year. The cost of failure of just one of these laser systems is the equivalent to the annual salary of 3 employees.”
“We can learn a lot from the mature semiconductor industry. When you buy electronic devices in the store, most of the components inside are not individually tested and calibrated. The manufacturers have developed processes that can produce reliable chip yields that are so high, they can easily cover the cost of any failures that are ‘dead on arrival’.”
The Fraunhofer Partnership Offer
The new Photonic Incubator is based in Twente with the goal of providing European companies with flexible assembly solutions for their optical systems. It means accompanying customers along the entire realization phase of a novel photonic product launch. That starts with a modular design for manufacturing and assembly at the prototyping.
But current automation solutions from the semiconductor industry are normally geared to rapidly producing 100,000 pieces or several million units. It is either high volume production or nothing. At the Fraunhofer Project Centre in Twente, a different approach is taken, developing machines with a modular production concept. The platform can be used for making one or two prototypes. Once they have been validated, then the same machine can be used to incrementally scale up production from 100 to 1000, to 100,000 and, if needed, a million components a year. The institute is building on knowledge developed for other sectors (like automotive) by the colleagues at the Institute for Production Technology in Aachen.
Uniquely Scalable Approach
“We have taken this tried and tested technology and developed a new tool head specifically suited to the multiple fibre-handling needs of the photonics industry. If you don’t connect the fibres to the chip with sub-micron accuracy and maintain the fibre polarisation, then valuable photons are lost entering or leaving the chip. With a step-resolution of less than 20 nanometers and a machine setup tailored to the specific needs of photonic systems, we can achieve final assembly accuracies in the deep submicron range – even after bonding.”
PHIX is First
“We’re in the final stages of installing the first complete machine for our first customer – the PHIX Photonics Assembly facility at the High-Tech Factory in Enschede. They offer assembly services for all three major PIC technology platforms (InP, Si and SiN) and are specialized in hybrid integration of chip-to-chip and fibre-to-chip modules. We have developed a highly intuitive user interface to ensure a smooth transition to high-volume automation. The process routines can be developed, tested and made robust by the customer’s engineering staff without the need for specialist automation knowledge.
We’re also proud of our association with the Fraunhofer spinoff AIXEMTec who license our knowledge in flexible automation and contract manufacturing. They manufacture the machine tools as well as offering assembly services for early-stage companies that are still prototyping. All in all, it’s a complete offer that fits the need for Industry 4.0.”
Sharing Industry 4.0 Production Knowledge with the University
“Last, but not least, we’re very much aware that engineers of tomorrow need to understand the changes going in high-tech industrial production, including photonics. Our industry incubator in Enschede, therefore, has close practical links with the students at the University of Twente. A good example is the Master Course on Product Life Cycle Management, which forms part of the curriculum on Industrial Design Engineering. It teaches students to understand industrial processes and ways in which data and industry experience can be used to speed up product development cycles.”