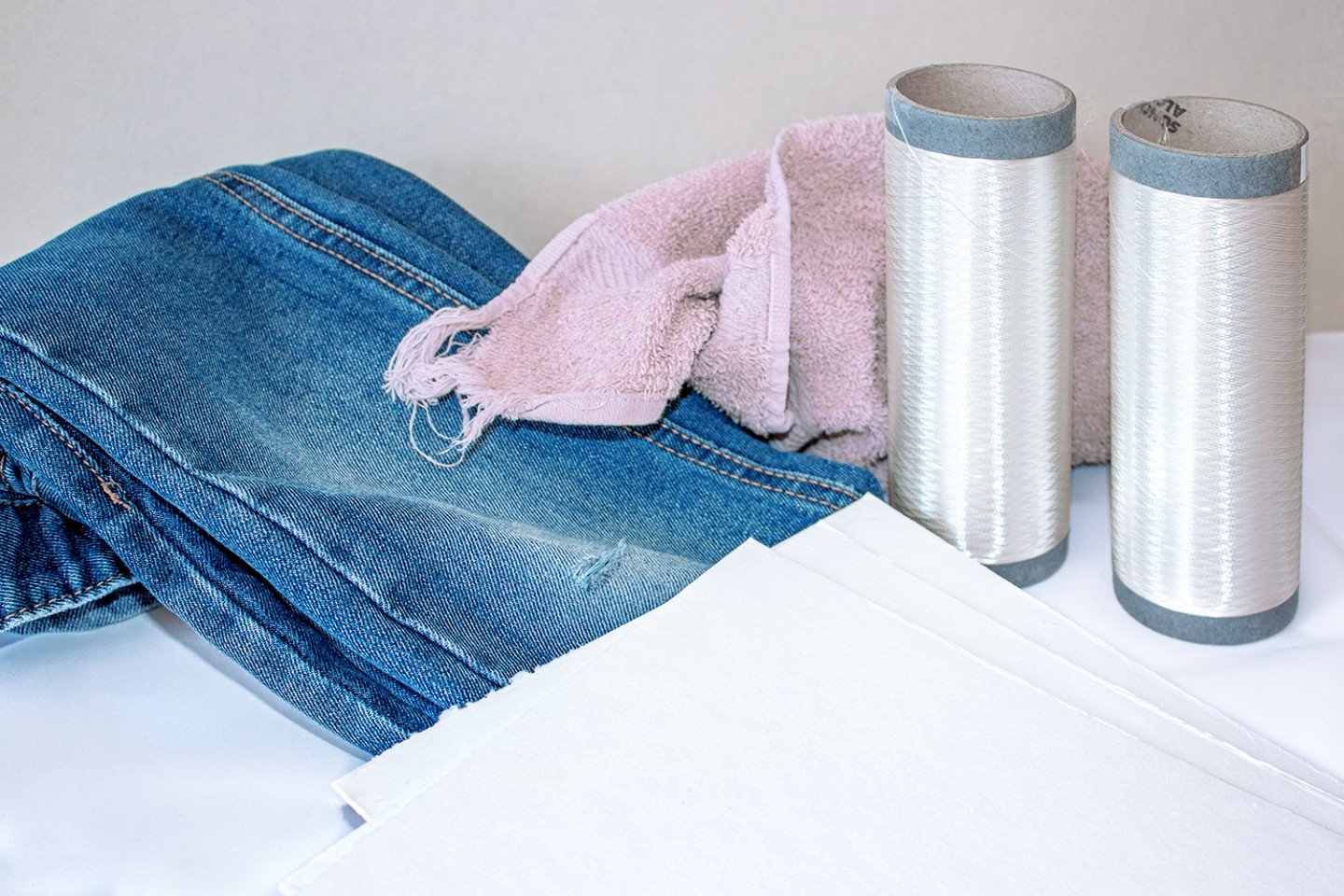
For the first time, a new processing procedure makes it possible to convert old cotton clothing into viscose filament yarn (VFY). โUsually, cotton clothing is burned or ends up in a landfill,โ says Andrรฉ Lehmann, scientist at the Fraunhofer Institute for Applied Polymer Research IAP in Potsdam, Germany. The recycling of cotton clothing has not been technically possible until now.
Lehmann went in search of a method to process recycled cotton into viscose fibers on behalf of the Swedish company re:newcell, which specializes in sustainable clothing. The new fiber is even suitable for mass production.
Clothing turned into inferior products
A lot of cotton clothes end up in the rubbish bin. Which is not environmentally friendly at all. Enormous amounts of raw materials, chemicals, and water are needed for the production of these clothes as it is Although old clothes are often recycled in Europe, they are mainly used to make inferior products, such as household cleaning cloths. To date, there are not many new, upcycled garments out there.
โTextiles are rarely made of pure cotton. For example, jeans always contain some kind of chemical fibers such as polyester or elastane,โ Lehmann explains. That means that trousers, shirts, and the like are rarely made of 100% cotton. Instead, they are normally made of blended fabric. And up until now, it has not been possible to separate these interwoven fibers.
Pulp is usually used in the textile industry as a raw material for the production of synthetic regenerated cellulose fibers such as viscose, modal or Lyocell. Since this pulp cannot be melted, it has to be dissolved and transformed into cellulose-containing fibrous layers. The pulp is commonly obtained from wood.
Filament thread of 100 % cellulose
โRe:newcell, however, gave us pulp plates made from recycled cotton and we were asked to check whether they could be further processed into viscose fibers.โ Lehmann goes on to describe the process. โBy setting the proper parameters, such as effective filtration steps, we were able to extract the extraneous fibers contained in the pulp. The result is a filament yarn. This is a continuous fiber several kilometers long, 100 % cellulose. In terms of quality, it can certainly compete with wood-based regenerated cellulose fibers. New fibers could be produced from the cotton pulp by using a spinning process. These would make it suitable for mass production.
โWe were able to meet re:newcellโs high standards when it came to the purity of the new fiber,โ says Lehmann. The result was convincing and exhibited the same properties when compared to commercially available viscose fibers.
Complex viscose process
That was no easy task at all, as the viscose process is complex. First, the pulp has to be activated with lye and then chemically derivatized. A highly pure alkaline viscose solution is produced this way, which is then spun in an acid bath. In the next process, the thread is rinsed before being wound up in its dry state. At this stage, it is now made up of pure cellulose. Which makes it particularly environmentally friendly. This is because cellulose rots and does not contribute to the mountains of microplastics that pollute the oceans. This is a major advantage over petroleum-based polyester fibers, which still dominate the world market with a share of around 60 %.
Sustainable clothing and alternative source of pulp
n the future, clothing such as old jeans or an old T-shirt can consequently be recycled several times and in that way contribute to more sustainability within the fashion industry. In addition, it will also be possible to expand the raw material base for pulp production in the textile industry. Lehmann: โUp to now, wood cellulose has been the raw material for viscose fibers. By optimizing the separation processes and intensifying the filtration of the extraneous fibers during the spinning process, we are able to substantially reduce the amount of waste.
Read also: eco is the new cool and eventually the new normal