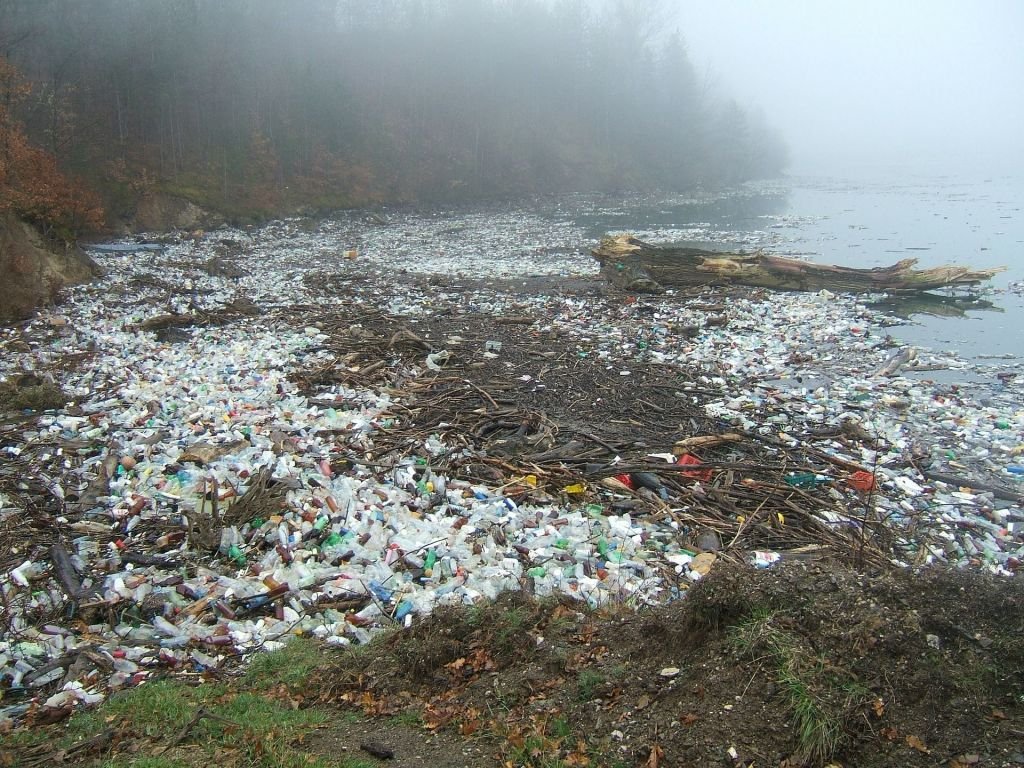
From TU/e technology to working with a multinational
In a series of articles, we try to find out what the value of the TU/e Campus is, outside education and research. In the previous two articles, we described what the university does and how it cooperates with the business community. Today we look at the activities that the university itself produces and focus on the TU/e spin-off Ioniqa. CEO and co-founder Tonnis Hooghoudt talks about how Ioniqa wants to make the world a cleaner place.
Read all the articles in the series here
Ioniqa launched TU/e technology in 2009. In the beginning, the company focused on the automotive market, but after two years of research it found out that plastic was ‘the way to go’. After years of research and testing, Ioniqa has now engaged a launching customer, Unilever. Together with the world’s largest PET producer Indorama, the three companies are going to try to turn PET plastic into a circular raw material. “We actually started working with Indorama at an early stage to ensure that our products were in line with the market. Otherwise, you’ll be working on fun things, but it’s of no use to anyone.”
Two years ago, Ioniqa started testing on a larger scale at a demonstration plant in Rotterdam. “Together with Unilever, we tested whether it was possible to make bottles from recycled PET plastic again. This turned out to be the case. We have shown that our new raw material for PET plastic products can compete in terms of quality and price compared to PET products made from oil. We have already produced thousands of bottles. For us, this cooperation is a way of showing the market that we are being taken seriously.”
The future of Ioniqa
The plans for the future are clear. Next year, Ioniqa wants to have built a factory where large-scale production will take place. This plant will process 10 kilotonnes of plastic per year. By way of comparison, in plastic producers’ factories, some 100 to 200 kilotons per year can be processed. “In fact, our process is a blueprint that we are offering to the market so that it can take the next step.”
In doing so, Hooghoudt indicates that the company mainly wants to send out a signal that 100% recycled plastic is possible. Ioniqa itself will not become a plastic producer but will sell licences for the technology. “We do this in order to keep up the speed, to ensure that this technology really goes to the market and to make the planet a lot cleaner. We do not want to be the bottleneck in this ourselves. At the end of the day, our core business is chemistry. We are chemists, we understand this process well and we know something about upscaling, but we are not as good as global players setting up factories across four continents. Ioniqa is a relatively small club of twenty men. We are not a billion-plus player with the financial clout that comes with it.”
Plastic as a circular material
The fact that PET bottles will soon be fully recyclable is, of course, a good thing, but it is far from solving the plastic problem. Therefore, after PET, Ioniqa will focus on all other types of plastics. “This technology actually means that plastic can be made sustainable, that it can be used and reused. There is no loss of raw material or quality. This is because the plastic is broken down to a molecular level. We already know the raw material, but it was always made from oil and now you can produce it from plastic. So we say as a small player: ‘The oil tap for plastic can be turned off’. PET products are the basis of our current process. In doing so, we looked at food packaging, then at the textile market. From sports houses to soft blankets and fleece sweaters, we can recycle everything that contains polyester.”
According to Hooghoudt, enough technology has been developed to really recycle plastic and it is now up to the major brands and other stakeholders to get started with it. “Everyone complains about plastic, but then it disappears into the ground or is burned, while you can easily recycle it. The big brands are also increasingly realising that things have to be done differently than they are now. Mechanical recycling does not exceed 25% recycling, while companies can simply re-use what they produce. With the same quality and preferably even cheaper. Companies like Unilever must now make sure that the circle is closed, because as a consumer you will, of course, not pay more for a bottle that has been recycled.”
The relationship with the TU/e
With technology developed at the TU/e, Ioniqa started working in 2009, but nine years later there is little left of the bond with the university. The technology Ioniqa uses has been developed to such an extent that the patents are on the name of the company and the patent it started with in 2009 will no longer be used.
Ioniqa has had positive experiences with the TU/e: “We have had a lot to gain from the TU/e Innovation Lab, both in terms of the business side and financing. They helped us with incubator loans and Bright Move funding so that we could develop before we went to market. TU/e business support has also been crucial to the growth of Ioniqa.”
But the relationship with the university is also a distant one: “Our technology has evolved further and we have established new patents. There is interaction with the TU/e, but what sometimes frustrates me is that it can be difficult to cooperate with the university if you don’t employ anyone from a university. The distance between a small company, especially if you’re not yet on the market, and the university I often find too big in the Netherlands.”
For example, when it comes to accommodation and the use of university laboratories. “As a start-up, before you are on the market, you spend a great deal of time raising finance. It is strange that you are working on this and have to pay the normal commercial rates for your accommodation and measurements on a lab. We simply paid as much as a multinational. It will have to do with regulation, but I think that we in the Netherlands are looking at this in too much black and white. I know that they are doing better to the south of us. There, the transfer of university and business is not as tightly regulated as we do in the Netherlands – and there is still a lot of profit to be made for the Netherlands BV.”