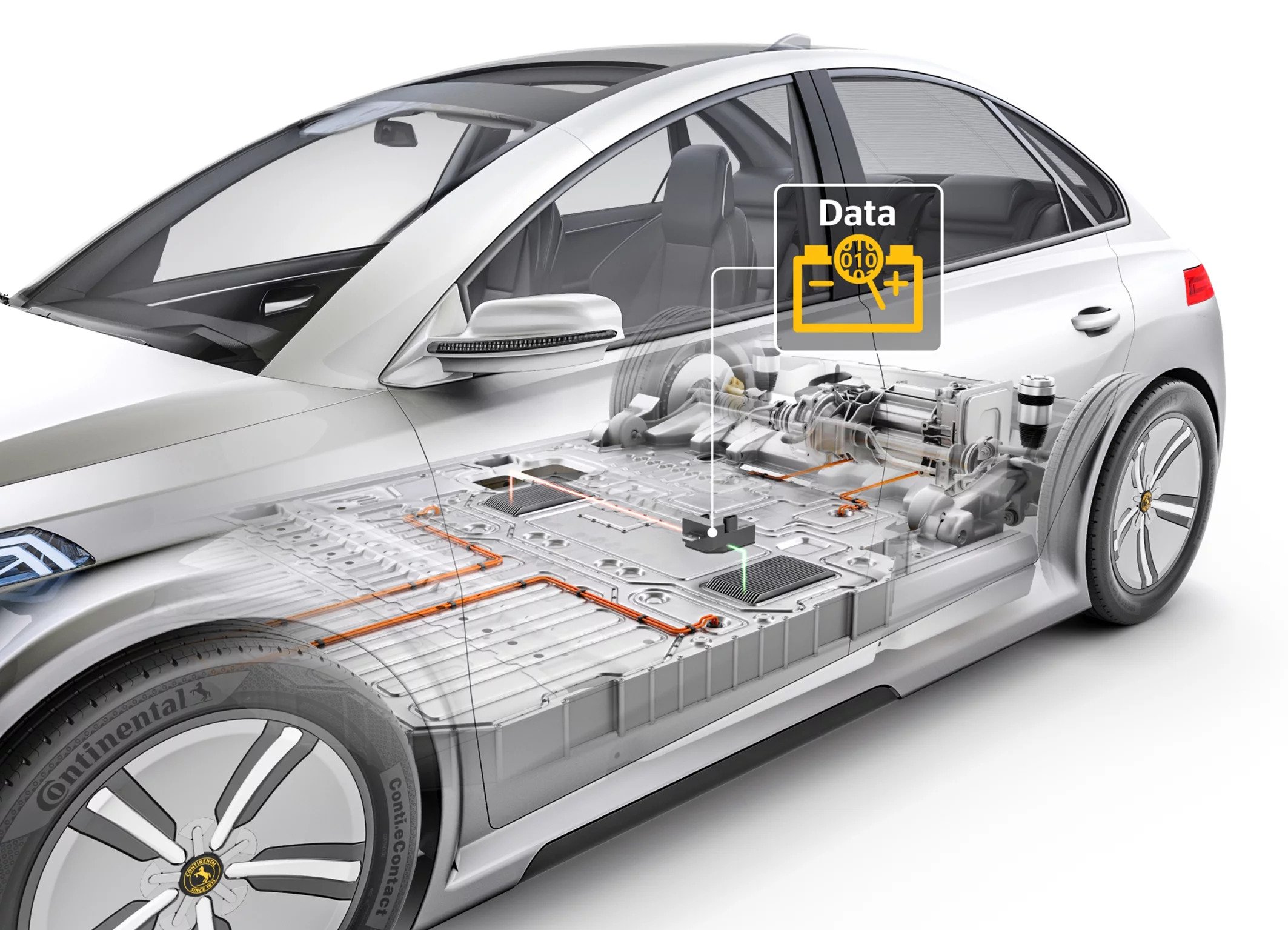
Batteries are the single most costly part of electric vehicles (EVs). Their range is the main pressing concern for those who are considering buying an EV. Consequently, being able to monitor their status as well as protect them can improve safety. To make sure that the driving range doesnโt lessen over time, new technologies can now check the batteryโs status. Such developments can have an impact not only on batteriesโ lifespan but also on the design of the next generation of batteries.
Continental is launching two sensors for EV batteries โ the Current Sensing Module (CSM), and the Battery Impact Detection (BID). Both of them provide critical info to the battery management system, which helps protect and optimize how the energy module functions.
The German company keeps in close contact with automobile manufacturers. The need for new sensors to monitor battery life culminated in two new modules that address that need. Drawing on its experience with the design of sensors โ such as those for airbag or lead-acid batteries โ creating new types was a seamless process.
โWe have different sections designing passive safety and occupant safety, just to name a few, so it was easy to adapt these concepts to other applications,โ explains Jรผrgen Maier, who is part of the group that worked on the BID. How do these two new sensors help to control EV batteries?
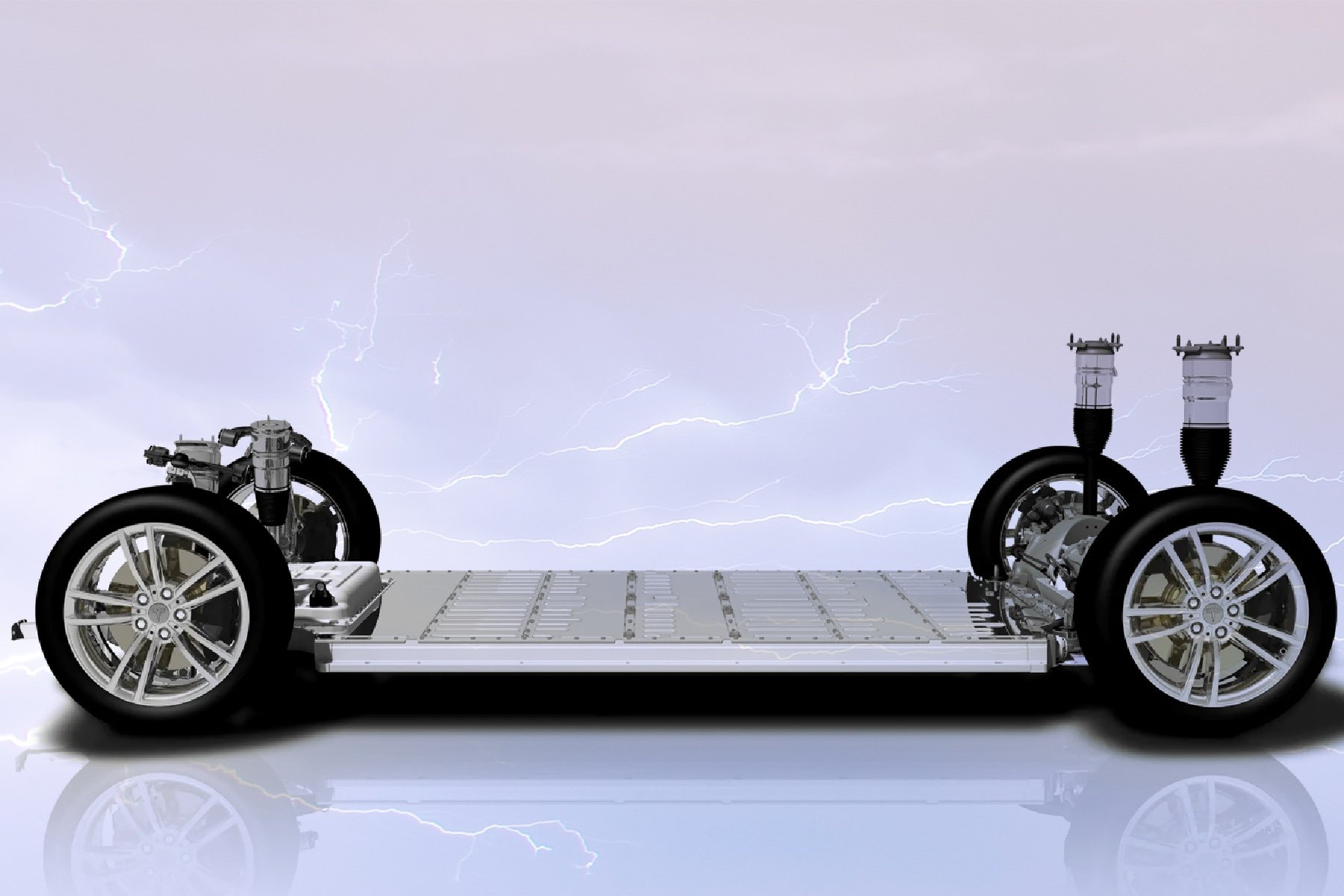
Improved accuracy of the battery status
To guarantee a certain amount of driving range, batteries store a certain amount of energy. When using them โ particularly during fast charging โ they tend to heat up. This kind of over-stressing may affect both the battery life and passenger safety, which is why a system to control the temperature within a certain gradient is needed.
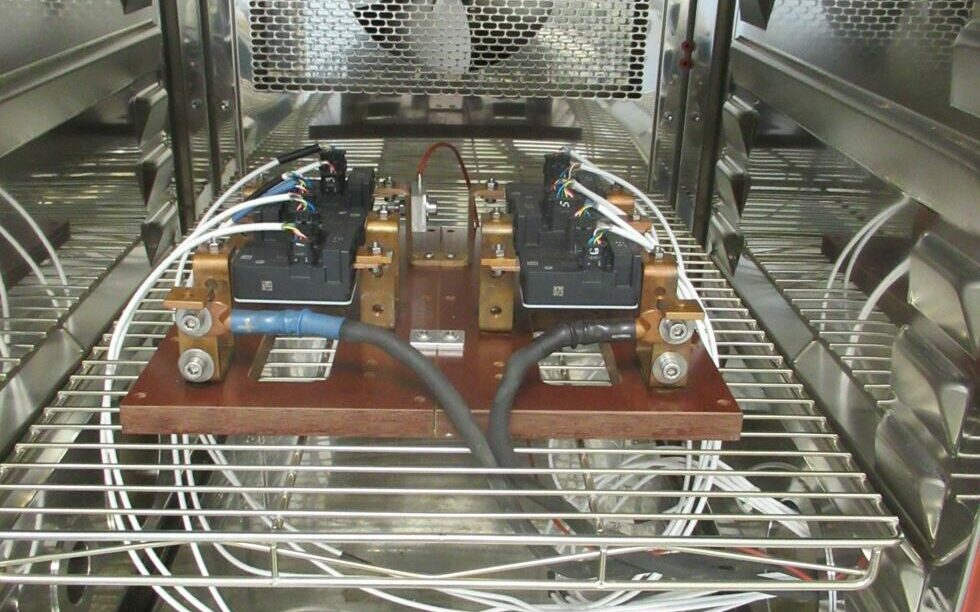
The CSM module is able to measure the temperature as well as the actual current, that is then sent to the battery management system, which reliably monitors the driving range. All measurements help optimize charging efficiency while also detecting potential malfunctions โ which could potentially cause a fire.
โIf the battery fails, you need to switch it off immediately. The sensors we designed can measure current peaks up to 2000 amperes,โ explains Horst Gering, program manager in the passive safety and sensorics department of Continental. โBesides that, the fact that we measure the battery current via two channels โ the shunt and the hall elements โ ensures that there is redundancy and therefore a greater level of safety.โ
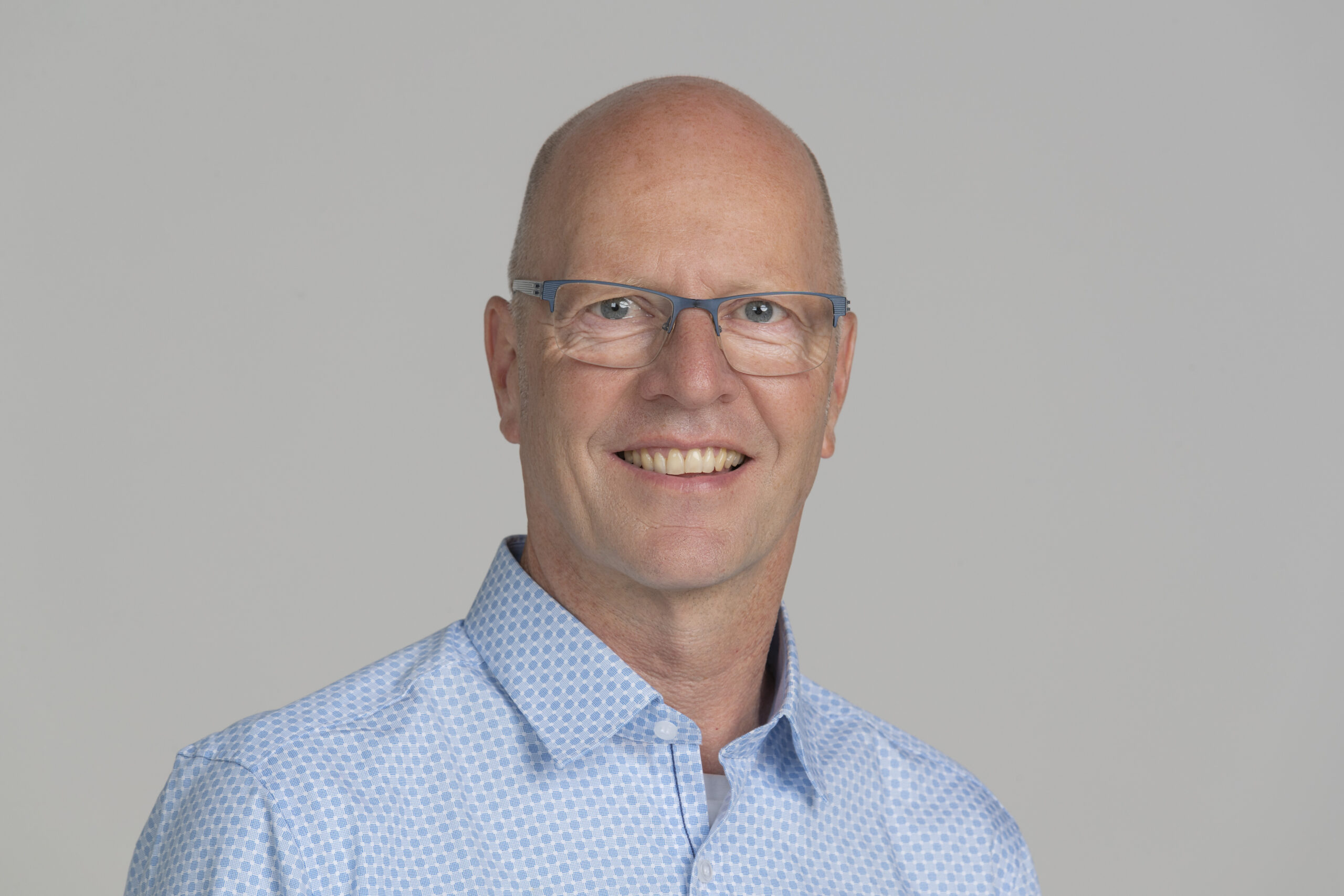
Gering Horst
Program and Innovation Manager Sensors and Subsystems at Continental
He has worked for Continental in various management positions in R&D, business development, and product management across the automotive product sector.
Sensing battery damage
This is due to two reasons: its weight contributes to a low center of gravity and the cells are protected by the structure of the vehicle. However, this solution does not keep the battery pack away from shocks below the undercarriage. To tackle this issue, automotive companies shield the battery pack with a metal cover.
Continental is offering them a new concept. Having conducted trials with a plastic cover and a nine-meter-long tube โ with two pressure sensors โ they were able to provide insights into undercarriage shocks. โThe BID is able to detect the level of impact and its position, thanks to its two pressure sensors. The information is then sent to the battery management system, tguch might potentially turn off the car,โ Maier adds.
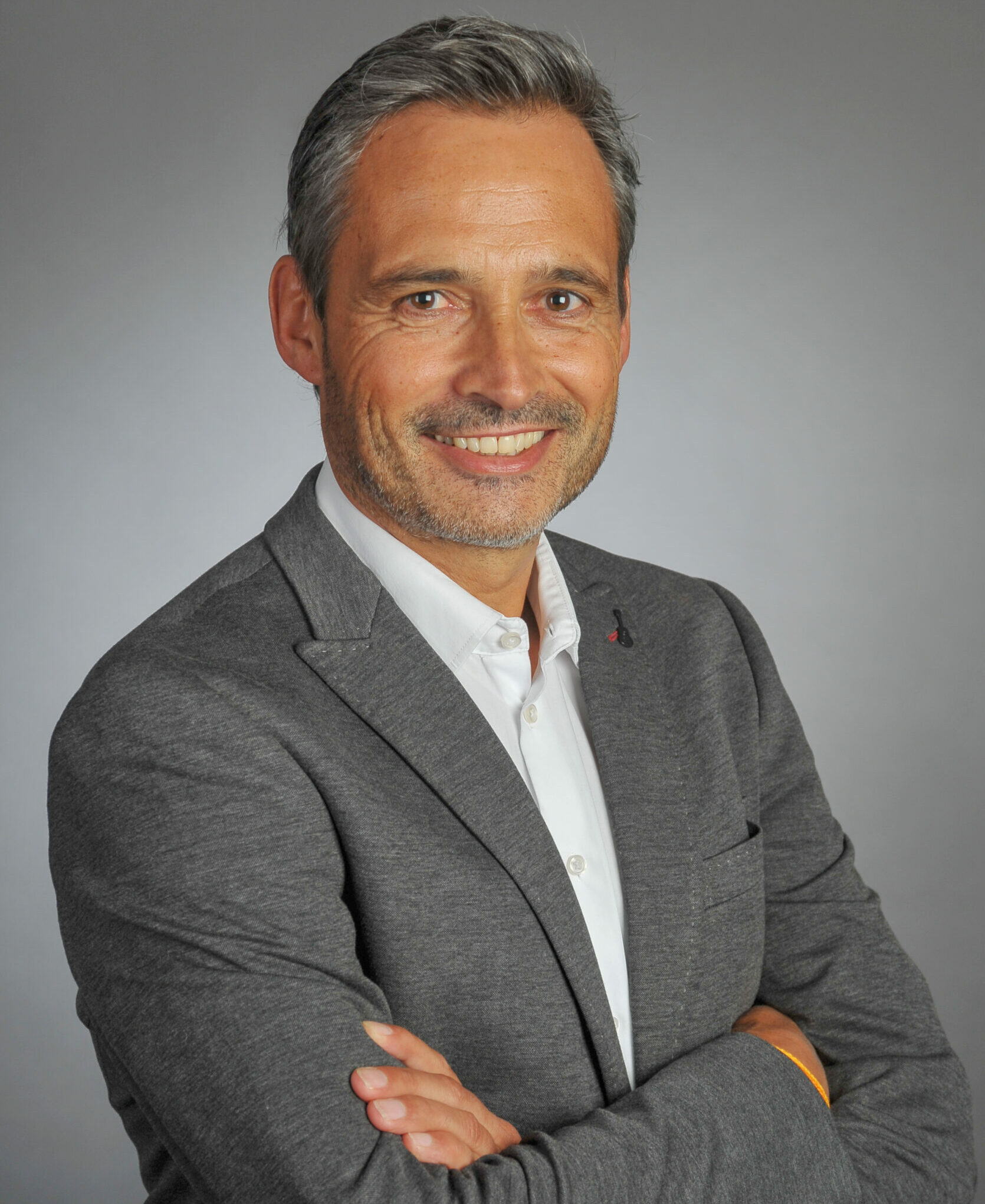
Jรผrgen Maier
Head of Sensors for Occupant Safetyโs product line
He is an electronics engineer with extensive automotive experience in different positions across R&D, quality, and management for sensors and powertrain applications.
According to the engineer, this is nothing new. โPassenger impact detection systems in the bumpers of cars use the same sensors,โ he adds. In other words, it all started as a trial to see if such technology could work with batteries too. Once they saw the promising results, engineers conducted trials with a plastic cover, which reduces the vehicleโs weight โ hence improving efficiency โ without sacrificing the robustness that metal can offer.

Electrification comes with new technical requests
The CSM and the BID are just some examples of new technologies that cars will use in the upcoming years. Given the EU ban on fossil-fueled cars by 2035, electrification needs to be ramped up. Accordingly, car and battery manufacturers are looking for new solutions allowing them to gain as much data accuracy as possible.
โThatโs what they ask for because that kind of precision can help with making better estimations of the battery charge status. In the beginning, fast charging is needed, but as soon as a battery is eighty percent full, you need to lower the current,โ emphasizes Gering. If you donโt reduce it then, the battery becomes over-stressed, consequently decreasing its lifespan and increasing safety risks.
According to Gering, there is more to it than that. โBesides guaranteeing the predicted mileage and the durability of a product, these sorts of sensor developments could also have implications in the design of more compact fuel battery cells.โ
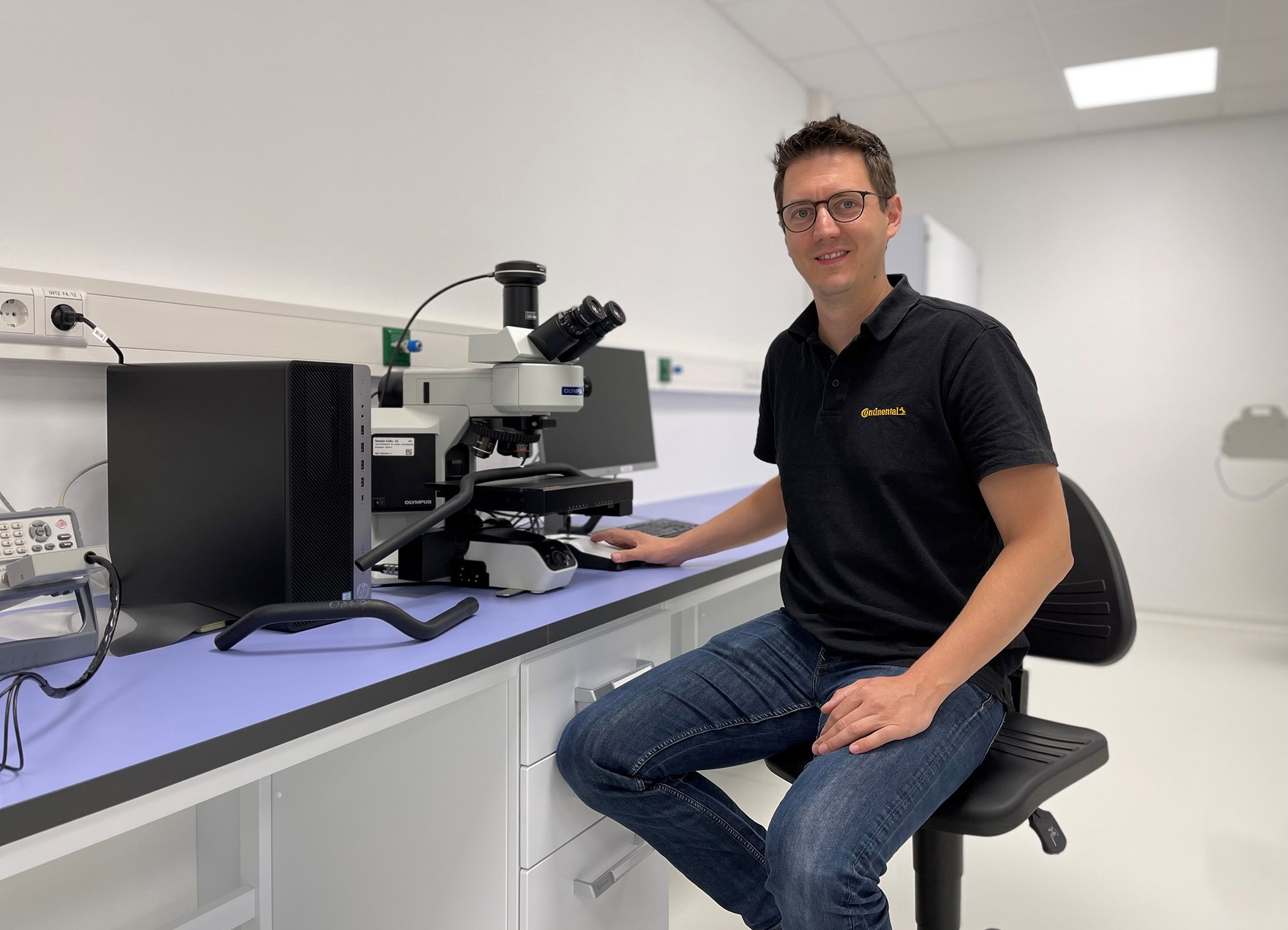
From Maierโs perspective, a second version of the BID would definitely improve safety levels. โFor better impact detection, accelerating sensor improvements could help explain a collision diagnosis in more detail. In addition, research into materials to cut down on weight โ both in terms of the protective plate and the frame โ will be continued.โ
Production of the CSM will begin towards the end of the year. The BID wonโt be on the market for another few years. Better batteries are sure to follow as well, thanks to the insights that sensors can provide.