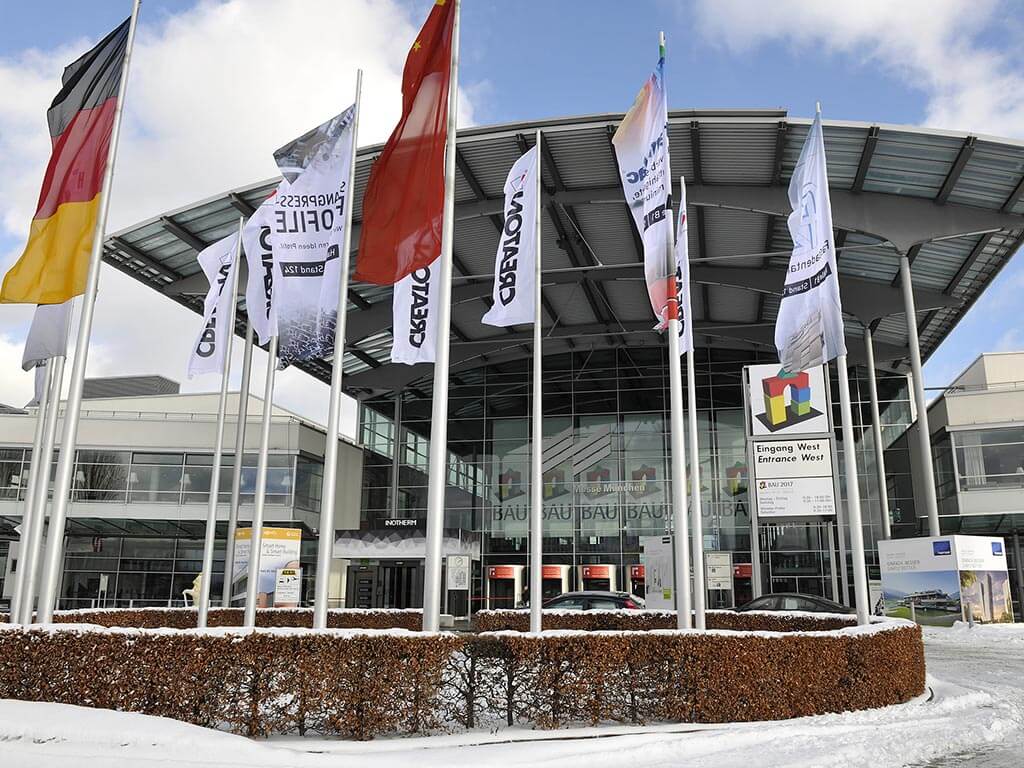
The Fraunhofer-Institut will show two innovative research developments for the construction industry at the BAU trade fair in Munich. The prototypes of the EDF drying system (EDF = energy-efficient, diffusion-open, flexible) and the textile concrete presented there for the first time allow to get control over damp walls and ramshackle components.
2.3 billion euro damage
With their drying system, the researchers at the Fraunhofer Institute react to bursting pipes, leaking fittings and leaking heating boilers. According to information from the German Insurance Association GDV, every 30 seconds in Germany a damage to tap water is reported. Thus costs of 2,3 billion euro develop.
Walls and floors must be dried professionally after water damages, in order to avoid mold formation. Heating and airing are not sufficient however normally. Therefore infrared heating plates and foil tents, combined with Adsorption dryers dry damp walls. With this method, however, ceilings are difficult to reach. In addition, this system is very energy-hungry.
Direct drying
With the EDF drying system, the 100×50 centimetre system consisting of fireproof, diffusion-open insulating material and a heater, the damp component is dried directly. This means that it can be mounted directly onto the damp component.
Tests on soaking wet vertically perforated brick walls have shown an energy saving of 80 percent compared to IR heating plates with the same drying time. A sensor in the drying system of the Fraunhofer researchers regulates the temperature of the heating. The diffusion-open insulation at the back of the EDF module allows moisture to pass through unhindered and minimizes heat losses.
A patent application has already been filed for the drying module. It can be easily installed, even on curved surfaces or round walls. Particularly pleasant: The drying of the wall is noiseless. Since the EDF module does not weigh much, researchers say it is also easy to transport.
The next step is to carry out tests under real conditions. The market launch of the EDF module is planned for summer 2019.
With sustainable textile concrete against building damage
According to researchers at the Fraunhofer Institute, cracks in concrete and rusting steel will be a thing of the past in the future. The secret: textile concrete. The corrosion-free building material has a long service life and offers the same static properties as reinforced concrete. In contrast to the reinforced building material, it is characterized by a material thickness of only a few centimetres. Thus filigree constructions are possible. In addition, textile concrete adapts to almost any geometry.
In high-performance textile concrete, carbon, glass fibre or plastic fabrics replace steel. The Fraunhofer researchers now want to replace these fibres with a textile made from renewable raw materials and thus contribute to environmental and climate protection. They rely on native plants such as flax, which can be further processed by spinning and weaving.

Concrete with fabric
Depending on the requirements placed on the component, the researchers supplement the flax with polymer fibre strands to create a mixed fabric that allows the stiffness of the material to be individually adjusted. The material mix is woven on a double gripper weaving machine with Jacquard attachment. According to Fraunhofer, it is unique in Europe. Thanks to the machine, it is possible to combine conventional and sustainable materials in an economically efficient and technically complex way.
Protected from weathering
The researchers use high-performance concrete to protect the fabric from weathering. Before this, they modify the woven textile with natural resins. Since the flat textile is inserted into the components in layers, curved shapes or rounded wall elements can also be easily converted. Liquid concrete then fills the component. The concrete was developed by the Centre for Light and Environmentally Compatible Constructions (Zeluba) in Fraunhofer WKI.
Since the material mix consists of very fine aggregates, water, concrete additives and concrete admixtures, as well as textile reinforcement made of flax, it is even better than reinforced concrete for bridge construction. According to researchers, the material structure is so dense that harmful substances cannot penetrate the structure. This results in a significantly longer service life of several decades.
Slim constructions
The textile concrete also makes light, slender bridge constructions possible that can be crossed by motor vehicles. For example, a reinforced concrete bridge with a span of 15 meters would normally be about 35 to 40 centimeters thick – with the flax version only twelve to 16 centimeters. However, a building supervisory approval for the building material is still pending.
At the BAU trade fair from 14 to 19 January in Munich, the Fraunhofer Institute will be showing a prototype of the EDF drying system as well as textile concrete at its joint stand in Hall C2, 528.
Photo: Munich Trade Fair Centre