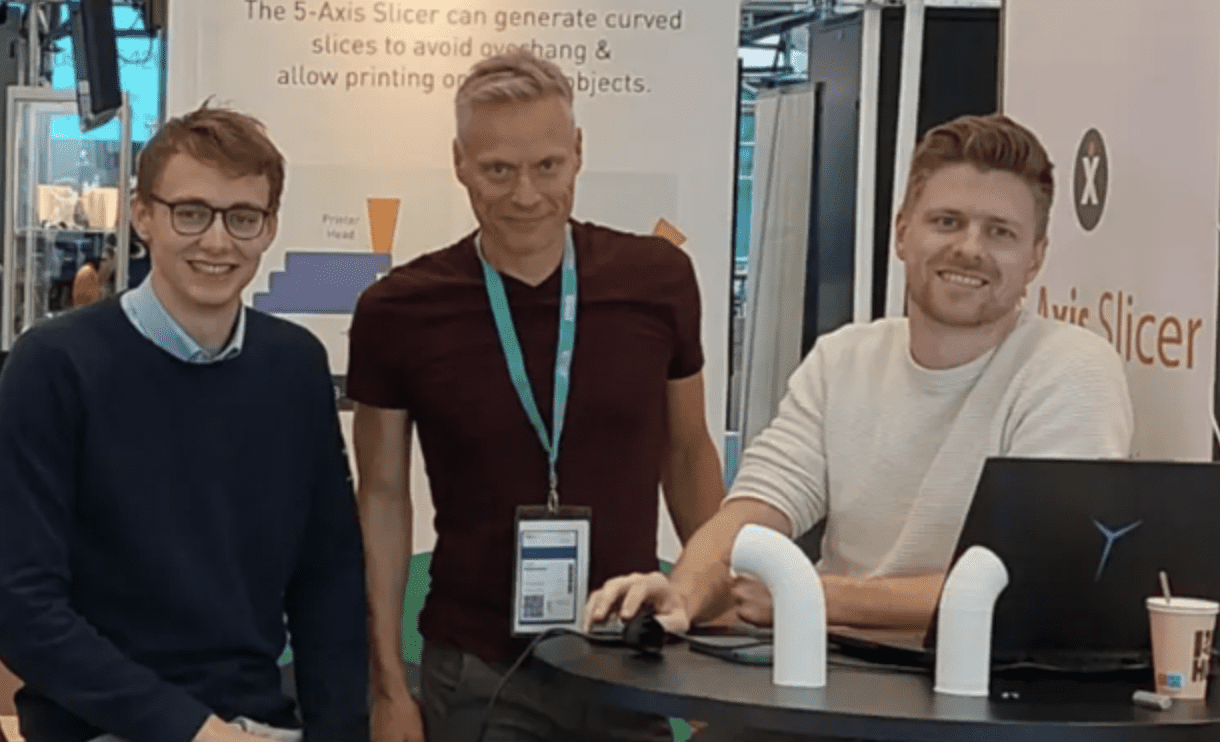
DoTX Control Solutions’ 5-Axis slicer software for multi-axis printers is pushing the boundaries of what 3D printing can do. EIT Manufacturing will help them access both the markets and the financial means to move the company forward, says tDoTX Control Solution in a press release.
The issue with three-axis printers is that this model has to be printed in flat, horizontal layers. Most of the existing slicers accommodate those printers. As a result, you are facing trouble. For instance, if the overhang angle exceeds its limit, supports will have to be printed that you must remove later. This is a major problem in metal printing, for example.
“Our 5-Axis Slicer software can actually generate toolpaths for 3D printers that have five or more axes, allowing to print virtually any model without overhang. This unlocks exciting possibilities,” says Jan Schuurmans, Director at DotX Control Solutions.
Complex shapes
The 5-Axis Slicer software enables the printing of complex shapes without any support structures. And printing on top of other objects is now an option. “You can basically print anything with our 5-Axis Slicer” affirms Jan Schuurmans. “What this means for industrial customers is yet to be seen, but so far, we have seen most interest from metal 3D printing.
One of the applications is metal dye repair. The damaged dye is scanned first, and converted into what we call a base model. Then, the operator draws the print model in CAD. Both models, base and print model, are imported in our 5-Axis Slicer, which then calculates the toolpath for the welding torch.”
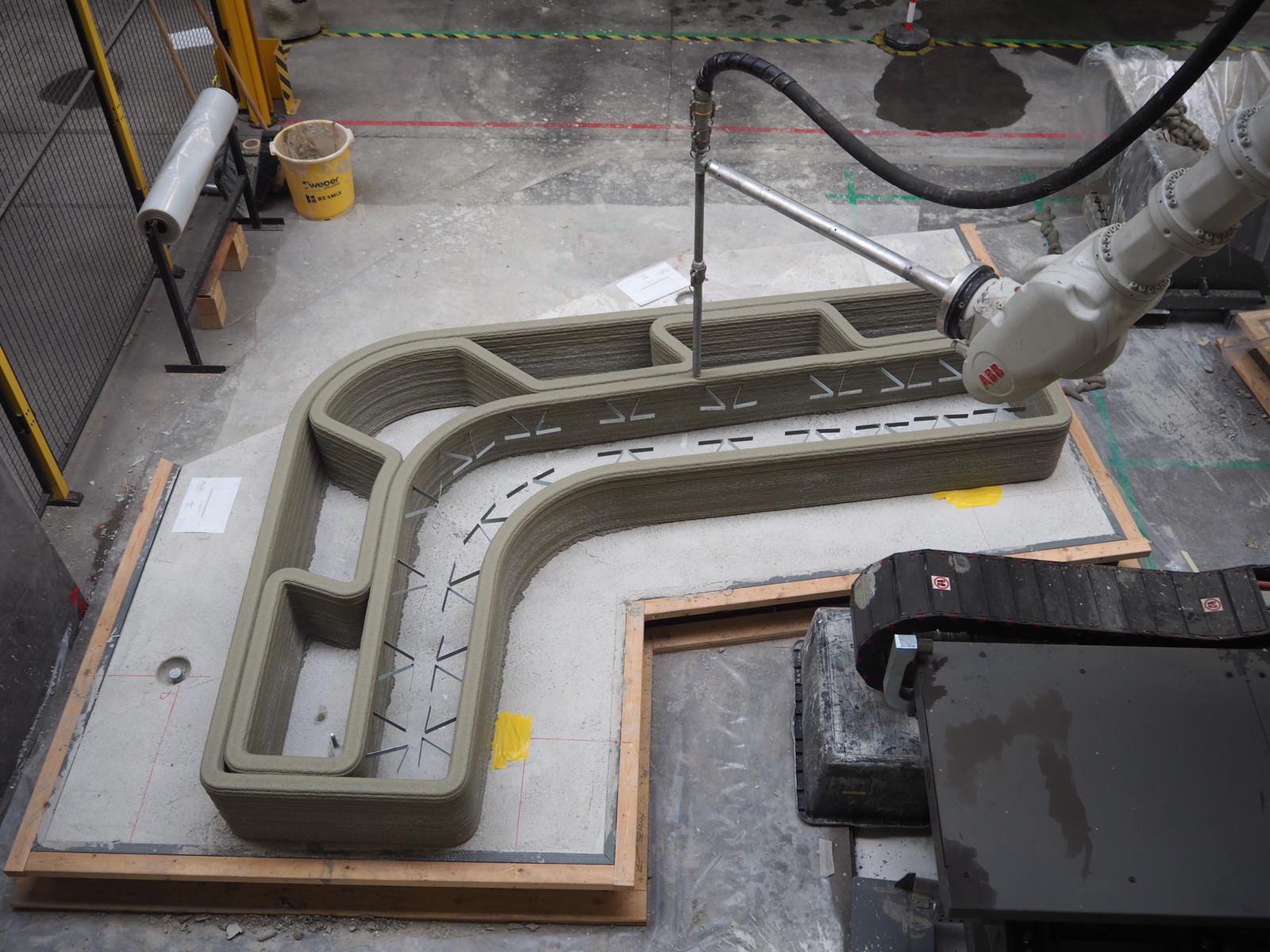
Wind turbine controller
The DotX Control Solutions team, Jan Schuurmans, Jelle Kalsbeek, and Pieter van Klaveren, all have a background in control systems from TU Delft. “For our customers, we analyze where problems or challenges lie. We usually model the process or product first and can find out how to set up the control system algorithms,” says Jan Schuurmans. “We then convert our algorithms into the software.” The wind turbine controller is another of their developments. The control software contains algorithms that reduce manufacturing costs and maximize electricity production. It is applied to wind turbines all over the world.