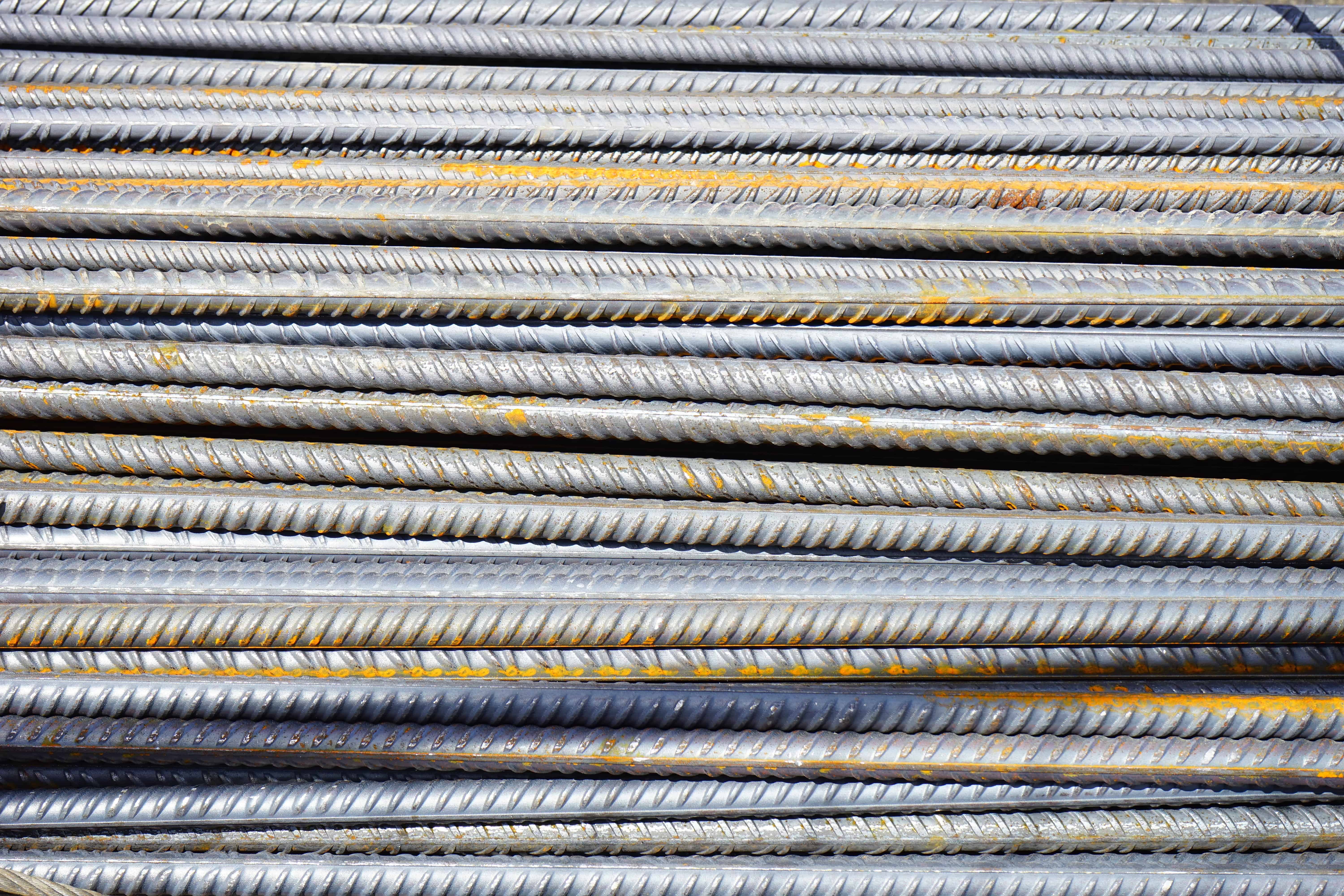
When it comes to sustainability and green steel, everybody talks about hydrogen. But current means of storing and transporting hydrogen request high pressures and low temperatures, which are both energetically and economically costly. Max Planck Institute researchers have discovered a groundbreaking method to produce green steel using ammonia, overcoming the limitations of hydrogen storage and transportation., says the institute in a press release.
Currently, steel production contributes to 7 percent of global CO2 emissions, prompting the search for sustainable alternatives. The new study reveals that ammonia can act as both a hydrogen carrier and a direct iron reductant, reducing overall costs by 18 percent while providing the same metallization degree as hydrogen-based reduction. Additionally, ammonia offers low liquefaction costs and has established logistics for worldwide trade.
The researchers’ next steps include synthesizing green ammonia, fine-tuning the iron reduction process, and testing different process parameters for broader industrial applications. The project is supported by the European Research Council Advanced Grant and the Walter Benjamin Programme grant.
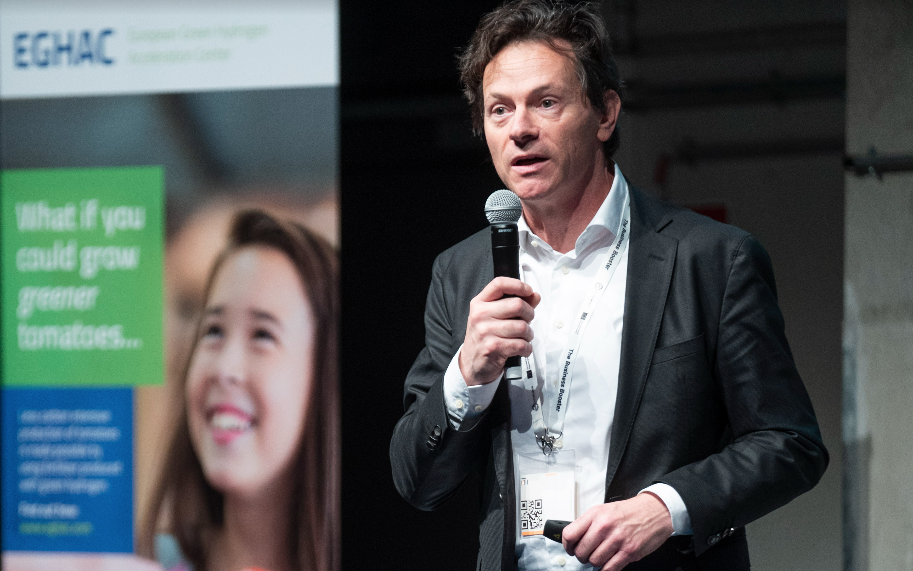
Challenges and Solutions for Ammonia
While ammonia offers a promising alternative to hydrogen for green steel production, it comes with its own set of challenges. One potential drawback is the environmental impact of ammonia production, which typically relies on natural gas as a feedstock, resulting in significant CO2 emissions. Furthermore, ammonia is a toxic and hazardous substance, raising concerns about its safe handling and storage during the steel production process.
However, researchers are working on solutions to address these concerns. For instance, green ammonia production methods are being developed, such as using renewable energy sources to power the Haber-Bosch process. This would greatly reduce the carbon footprint of ammonia production. Proper safety measures and strict regulations should be implemented to ensure the secure handling and storage of ammonia, minimizing the risk of accidents and environmental hazards.
Real-World Examples and Case Studies
As the concept of ammonia-based green steel production gains traction, industries worldwide are beginning to explore its potential. One such example is the Hybrit project, a collaboration between Swedish steel manufacturer SSAB, mining company LKAB, and energy company Vattenfall. While this project primarily focuses on hydrogen-based steel production, it also considers the integration of ammonia as a potential hydrogen carrier and storage medium.
Another example is the Green Ammonia Consortium in Japan, which aims to develop and promote ammonia as a clean energy source. The consortium includes major Japanese companies such as Mitsubishi Heavy Industries, JGC Holdings, and Mitsui Chemicals, who are actively researching and investing in green ammonia production and its applications, including in the steel industry. These real-world examples showcase the growing interest in ammonia as a viable solution for sustainable steel production and its potential to transform the industry on a global scale.