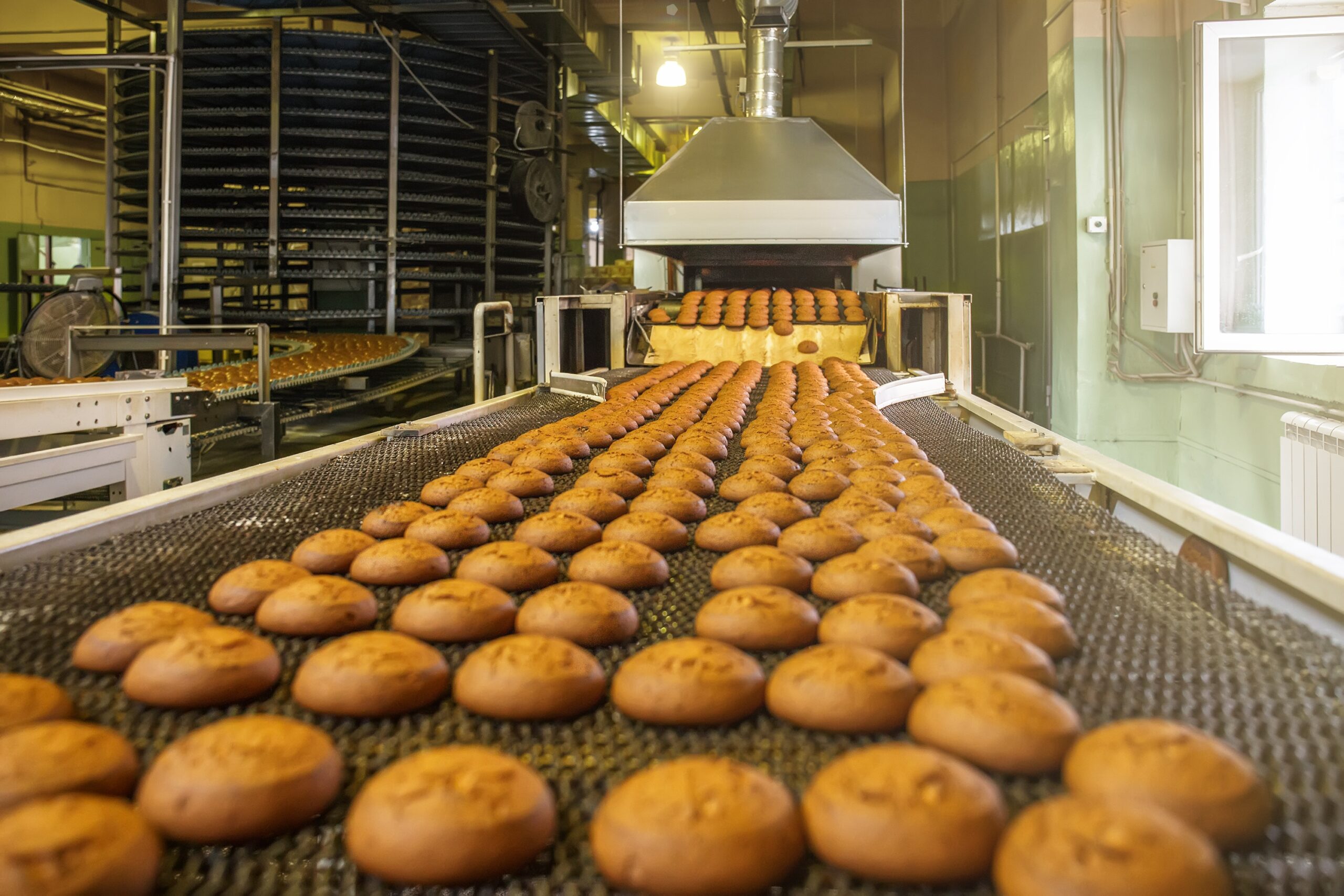
About Indicode
- Founders: Nicholas Theuma, André Aquilina, and Eryl Vella
- Founded in: 2021
- Employees: -
- Money raised: 25.000 euro
- Ultimate goal: Ultimate goal: To facilitate the process of automating visual inspections for production engineers.
Companies want to produce quality products. Shipping defective goods leave dents in consumer trust and hurt the company’s bottom line. Indicode founder Nicholas Theuma has developed an AI system that detects defects in products in a swift way. In today’s installment of start-up of the day he tells more about this system
What is Indicode capable of?
“We received an investment of around 25,000 euros. We three founders put that towards building a working version of our product over the past year. Indicode is a web platform you can access from any device – laptop, tablet, or mobile phone. We can offer clients a cloud-based solution or a locally deployed solution. So let’s say our client manufactures plastic dolls. Maybe they produce thousands of pieces a day. But then they use manual inspections to check those pieces for defects. Furthermore, they don’t check 100 percent of their product line. They would inspect a subset, for example, 10 percent. Indicode does the same job faster and smarter.
Most of our clients are already capturing images of their products on the production line. Users simply need to upload 200 images of a good product through our platform. Our model will train on it for two minutes to learn what good products look like, and then it’s ready to start spotting visual defects. It’s very fast and we’re happy with the speeds achieved. It’s about 99.5 percent accurate.
Users also get access to an analytics dashboard that collects data of the spotted defects. It can be shared with anyone in the company and different profiles can be given different permissions to access different things. Users can adjust the sensitivity of the model. For example, a plastic doll might not need to be entirely perfect, whereas a small component for a circuit board needs to have stricter parameters. It’s very customizable.”
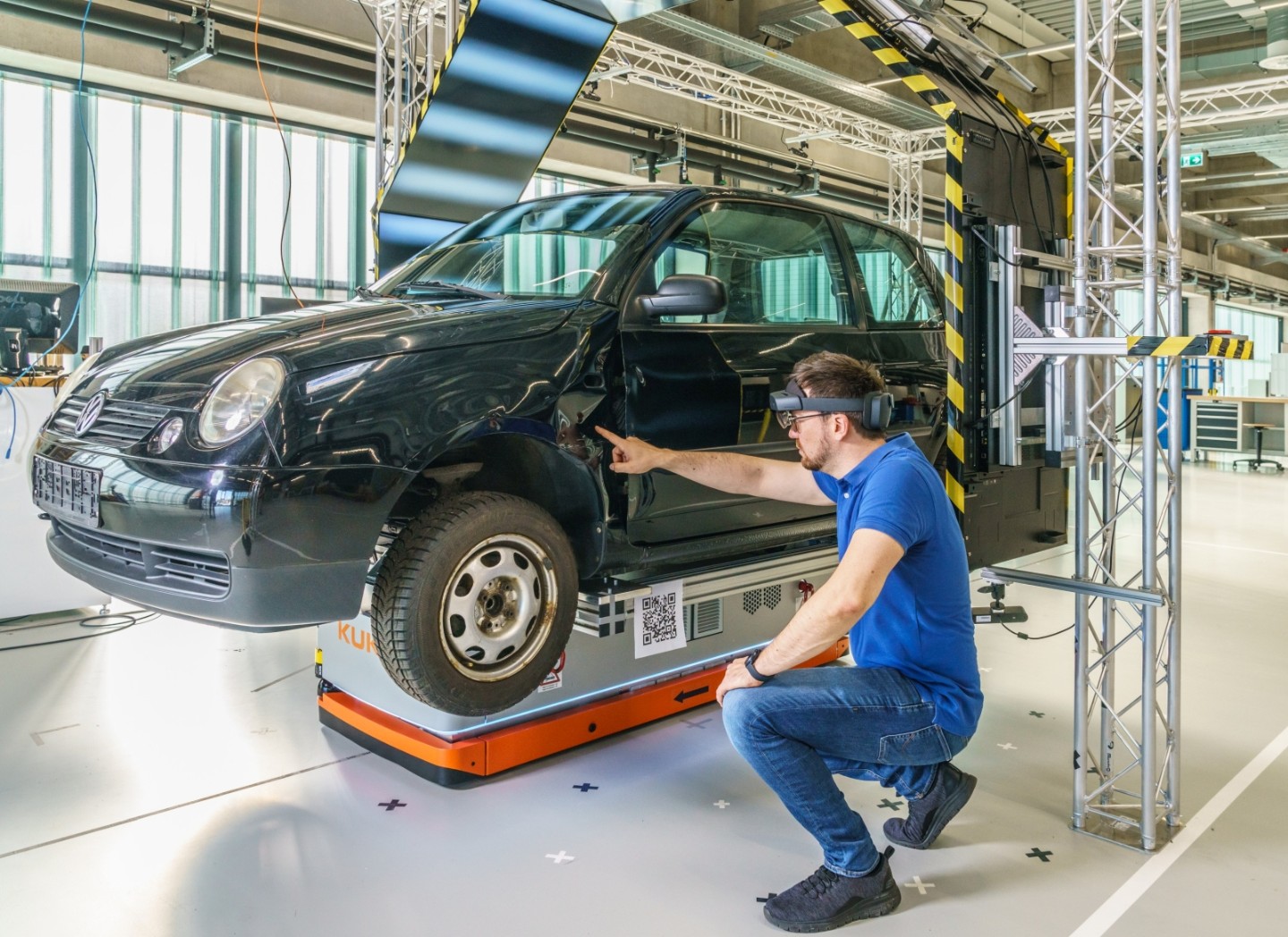
Are you the only one doing this?
“Locally yes, while abroad there are others who are automating visual inspections. But most other systems are based on image classification using AI. This type of AI sees a cat and labels it as a cat for example. In manufacturing, the AI would label an image as a broken bottle and another image as a contaminated bottle and so on. It works based on these labels and it’s a much more intensive process. The training is also intensive because the training data set needs to be labeled manually by an expert. It’s time- and cost-intensive.
In our case, we work using anomaly detection. We’re only interested in identifying what is defective and everything else is marked as standard. We teach our AI model what a standard bottle version should look like, and anything that varies from that version is marked as an anomaly. So now we reduced things to only two labels – good or bad. This is much simpler and much faster. While other companies are using similar systems, it’s all very new as these are things based on research carried out just two years ago.”
Is it cheaper for people to keep their current systems or to switch to Indicode?
“With our system being automated you can run it 24/7. Now suddenly, instead of only checking 10 percent of your product, you can check 100 percent of your product. During manual inspection a person gets tired, makes some mistakes, and needs training. There’s also a difference in the speed of the actual detection. Our system tells you if a product is defective or not in as little as 100 milliseconds. The fastest human inspectors will take around 2 to 5 seconds to complete the same task. We’re not asking clients to fork out a lot of money for the system, and our competitive pricing works on a subscription basis.”
Are there any extra equipment costs for your clients?
“No. The cool thing about this is that we started using an old webcam. Although now we’re using an industry-standard Basler camera. But our system works with any camera. Even if the images are taken in a high resolution, our system down samples them to keep processing speeds fast. So we end up using images of around 250 by 250 pixels. That’s very low resolution. The images also don’t have to be standard ones, they can also be X-Rays or seismic images.”
Why is Indicode not only cloud-based?
“A year ago, we were going only to offer a cloud-based solution. One would just log into our website and have all their data there. We found that many manufacturing clients aren’t very happy with that solution because of their data security. They wouldn’t want to risk sharing their intellectual property publicly. They wanted locally hosted solutions. So we gave them the option of deploying a server within their factories which can’t be accessed from the outside.”
What’s the biggest challenge you’ve had to overcome as a team?
“Understanding our customer. I think it’s the biggest challenge because it’s constantly a challenge for us and still is a challenge. But we’ve also managed to turn it into one of our biggest advantages. In the manufacturing industry, especially locally, you can’t do research about everything. Everything is kept very close to the chest of the people working in the field. You have to meet stakeholders and understand them. We know that our customers need this solution. And there’s a gap in the market. At the moment, we’re offering consultations free of charge to customers to test our system with products that are relevant to them. So we invite interested parties to contact us to supply us with data, in the form of images of their products, to test on.”