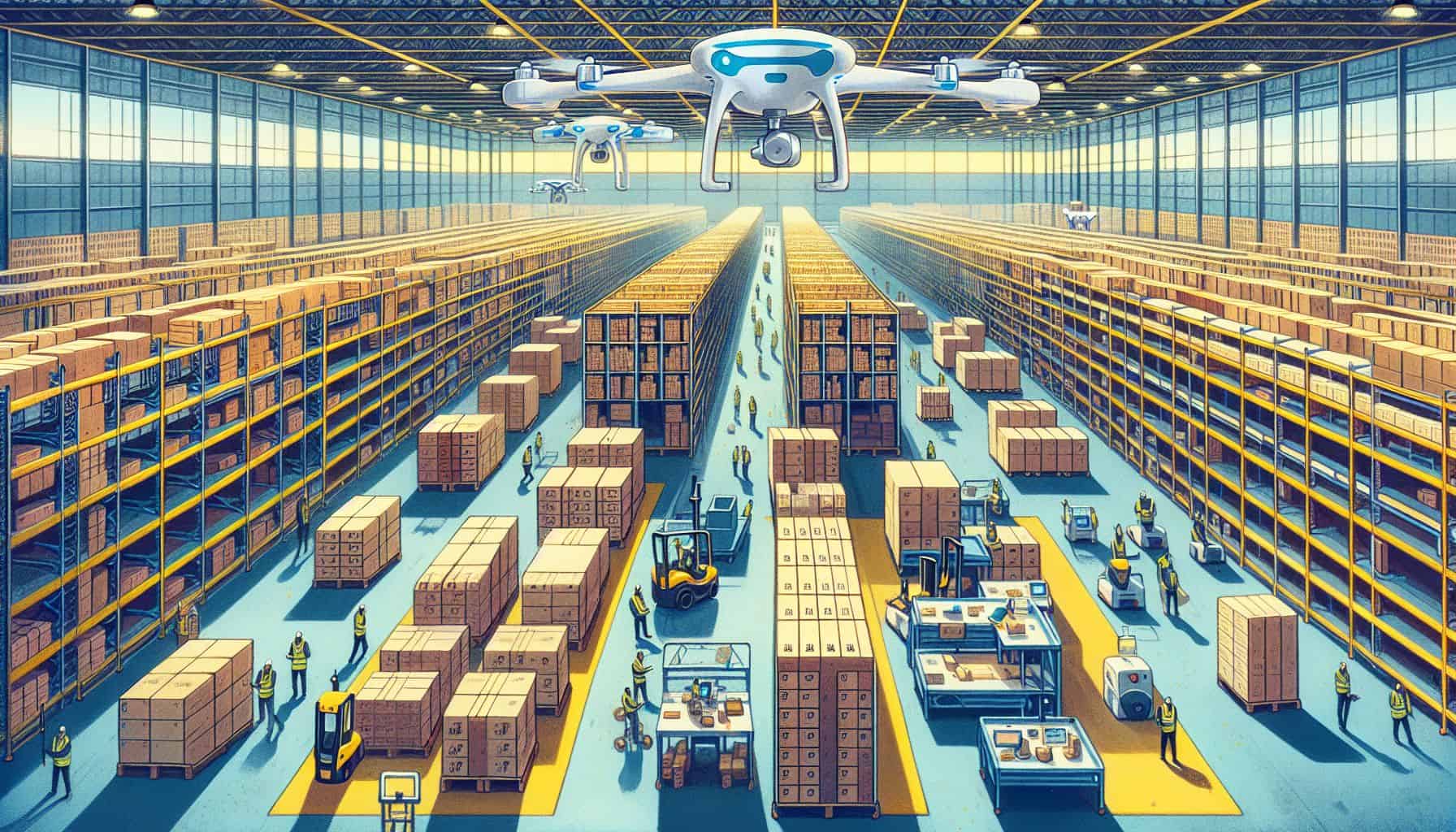
IKEA introduces AI-enhanced drones for 24/7 autonomous inventory management in distribution centers. This upgrade promises increased efficiency, improved stock accuracy, and better employee working conditions. The technology is set to expand globally.
The integration of AI into IKEAโs inventory drones represents a shift in how the company manages its warehouse operations. Traditionally, inventory checks have been labor-intensive, requiring employees to manually count and verify stock levels. The introduction of AI-powered drones now allows for seamless, continuous inventory monitoring, providing real-time data that enable immediate action. This not only improves accuracy but also significantly speeds up the process, ensuring that stock levels are always up-to-date.
How the tech works
These AI-enhanced drones are designed to operate autonomously around the clock. Equipped with AI algorithms, they can identify and photograph product storage locations, navigate through the warehouse using a custom indoor positioning system, and avoid obstacles with detection capabilities. This allows the drones to perform inventory checks without disrupting the workflow of the distribution center. The dronesโ ability to reach higher storage levels and their programmed flight paths ensure comprehensive coverage of the warehouse.
Global implementation
IKEAโs journey with AI-powered drones began in 2021 through a partnership with Verity, a company specializing in autonomous drone solutions. The first AI-enhanced drone was tested in Switzerland, and following its success, over 250 drones have been deployed across 73 locations in nine countries. The most recent successful test took place at the Distribution Centre Winterslag in Belgium, and plans are in place to expand this system to additional locations in Europe and North America over the next year.
Employee and customer benefits
Implementing AI-powered drones brings multiple benefits to employees and customers, IKEA says. For employees, the drones take over the physically demanding task of manual inventory checks, reducing ergonomic strain and improving job satisfaction. According to IKEA, this shift allows employees to focus on more engaging and less physically strenuous tasks, ultimately enhancing their working conditions. For customers, the improved accuracy and efficiency in inventory management mean better stock availability and a more reliable shopping experience.
More innovations
Future upgrades may include advanced functionalities such as distinguishing between different types of cargo and optimizing loading processes. This continuous improvement strategy aims to further streamline warehouse operations and elevate the customer experience. As IKEAโs Global Category Area Manager Logistics Services, Claes Lindgren, stated, โThe drones are a good example where we can achieve a win-win in both of these areas; by simplifying our processes in the logistics units, and hence, ensuring better inventory integrity leading to a better customer experience.โ