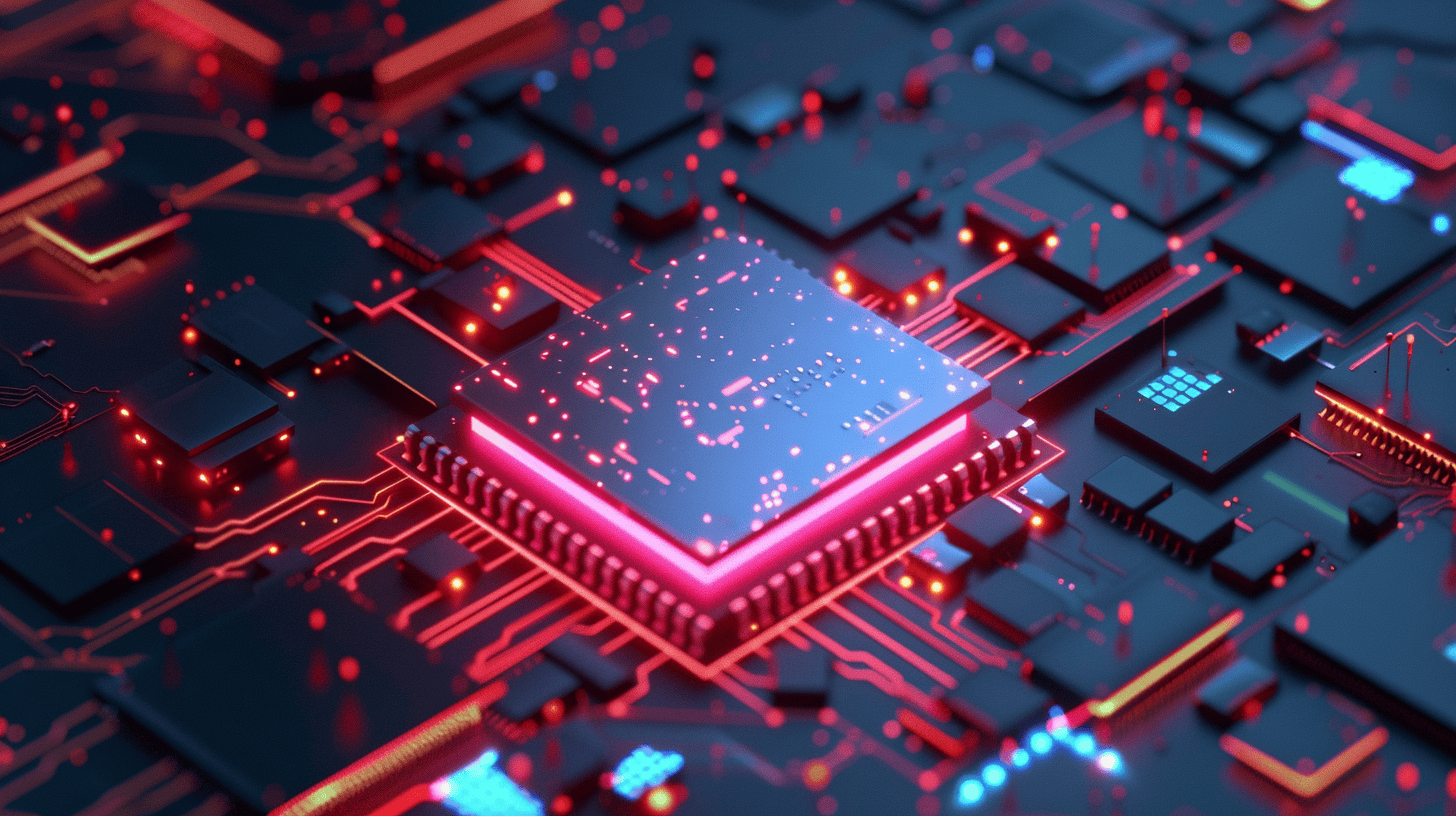
A new study by Lam Research can mark a turning point in the chip industry. Their Pulsed Laser Deposition (PLD) thin film deposition technique enables the production of complex multi-compound materials on wafers, surpassing conventional methods. With enhanced uniformity, particle filtering, and lower costs per wafer, PLD addresses critical demands in micro-electromechanical systems (MEMS) based on 5G and Wi-Fi advancements. The technologyโs ability to increase scandium concentration in aluminum scandium nitride films from 30% to at least 40% promises improved performance in various applications, from automotive to healthcare. As the demand for MEMS manufacturing equipment grows, PLD is poised to accelerate product roadmaps and unlock new possibilities in semiconductor production.
Lam Researchโs Pulsus PLD system is revolutionizing how thin films are deposited in semiconductor manufacturing. By leveraging a high-energy laser to vaporize target materials, creating a plasma that condenses on wafers, this technique enables the deposition of complex, multi-compound materials with exceptional uniformity and quality. This development marks a departure from traditional methods like reactive sputtering, which often struggle with film uniformity and particle contamination.
Technical aspects of PLD
Pulsed Laser Deposition operates by focusing a high-energy laser on a target material within a vacuum chamber. The laserโs energy creates a plasma plume from the target, which deposits onto the substrate. This process involves several stages: laser absorption and ablation, plasma dynamics, material deposition, and thin film nucleation and growth. The precision of PLD ensures that the stoichiometry of the target material is retained, and parameters like laser energy density and pulse repetition rate can be finely controlled.
The versatility of PLD is further demonstrated by its applications. It is used to fabricate rare earth barium copper oxide films, hydrogen-free DLC layers, and scandium-doped aluminum nitride thin films. Moreover, it can create crystalline thin films on wafers up to 300 mm, which are crucial for micro-nano electronics. Despite some challenges like particulate deposition due to sub-surface boiling, these can be mitigated using techniques such as shadow masks or rotating targets.
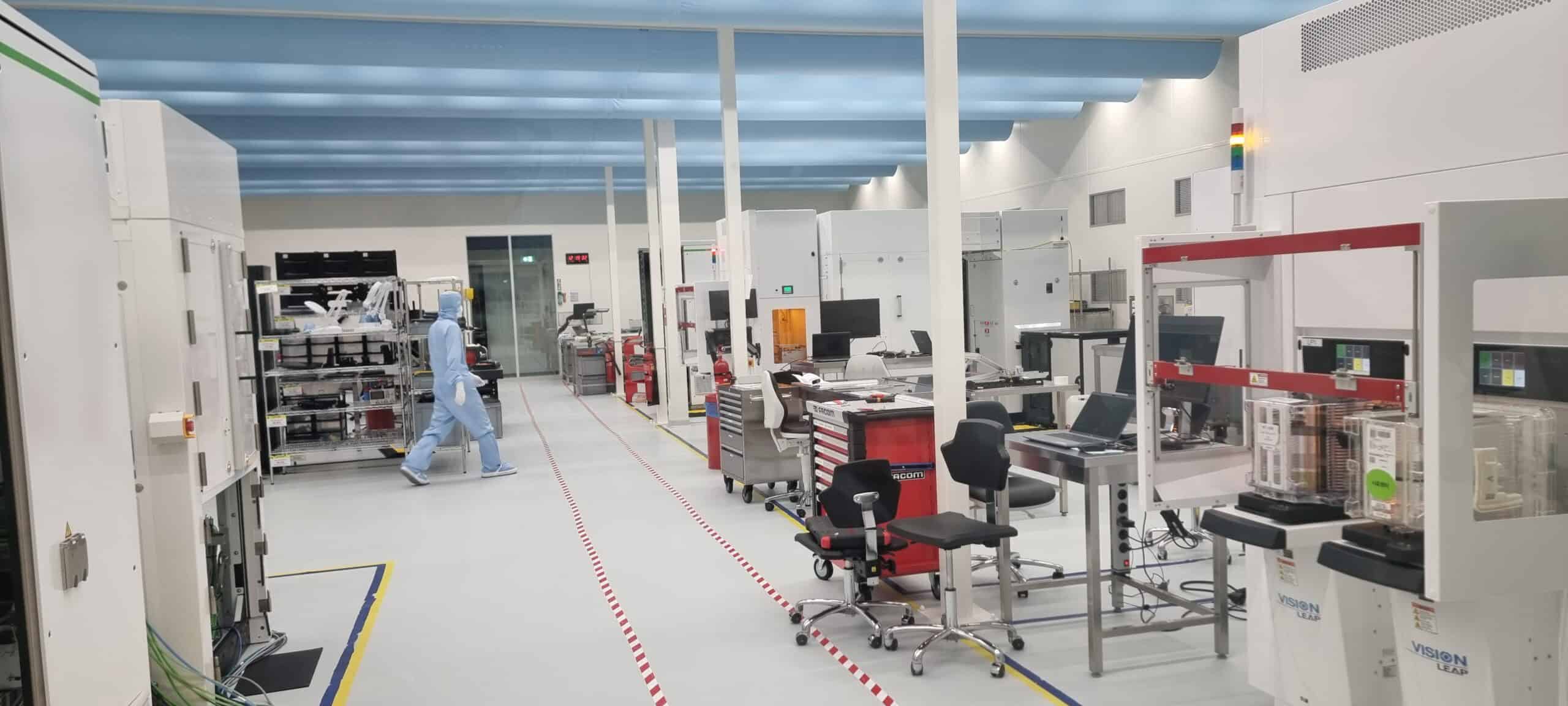
Addressing industry challenges
One of the most significant advantages of Pulsus PLD is its ability to overcome long-standing technical challenges. Issues such as film uniformity and particle filtering have historically hindered the broader adoption of pulsed laser deposition. However, Lam Researchโs innovation has resulted in enhanced manufacturing yields and reduced costs per wafer. This makes the technology particularly appealing for the production of next-generation MEMS-based microphones and RF filters, which are essential for advancing 5G and Wi-Fi technologies.
In particular, the technique allows for higher concentrations of scandium in aluminum scandium nitride films, boosting the performance of RF filters. By increasing the scandium concentration from 30% to at least 40%, the technology significantly enhances the signal-to-noise ratio in piezoMEMS-based microphones. This improvement is crucial for enabling low-power or no-power โalways listeningโ states in mobile devices, which is a key feature for modern consumer electronics.
Expanding applications and market impact
The demand for MEMS manufacturing equipment reached over $940 million in 2023, reflecting the growing need for advanced semiconductor technologies. PLDโs ability to deposit a wide range of complex materials that are difficult to apply using other methods opens new avenues for innovation. Industries such as automotive, healthcare, retail, and industrial automation stand to benefit significantly from these advancements, driven by the increasing integration of artificial intelligence and the Internet of Things (IoT).
In conclusion, Lam Researchโs Pulsus PLD system represents a transformative advancement in semiconductor manufacturing. By providing a more efficient, cost-effective method for thin film deposition, PLD is positioned to meet the growing demands of the industry. As technology continues to evolve, the role of PLD in enhancing device performance and enabling new capabilities will only become more critical.