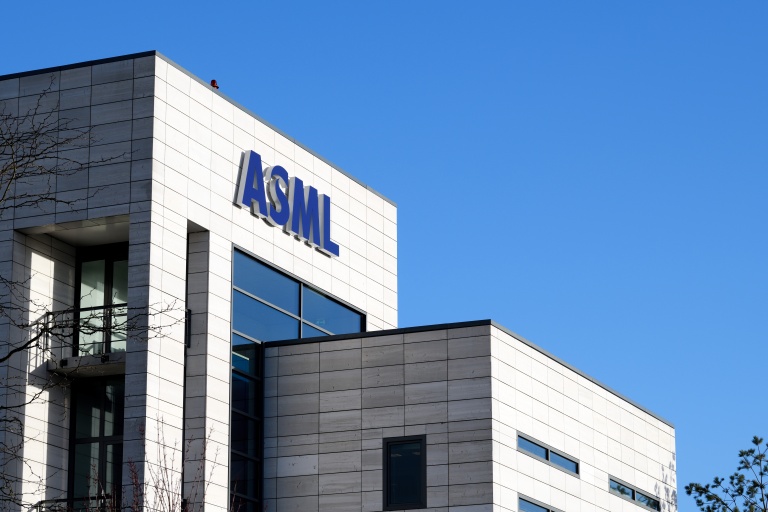
The Brainport region is an important growth engine of the Dutch economy. It is therefore very important, both for the region itself and for the country, to further strengthen this position. The fact that this not only increases the earning capacity but also makes it possible to tackle numerous societal challenges, makes that goal all the more relevant. In a series of 12 articles, Innovation Origins looks at the most striking issues within this endeavor. In this, we are guided by the research report ‘Brainport at the top‘ that Rabobank published in collaboration with Strategy Unit. Today, the second article in this series, in which we focus on the Original Equipment Manufacturers (OEMs).
The starting position of the high-tech manufacturing industry is relatively strong, according to those involved in the system itself. “The innovativeness and cooperation are of a very high level; in Eindhoven and the surrounding area, something can be done that is unique worldwide”. At the same time, the research report points to the vulnerability of the system. Although the robustness of the Brainport ecosystem is graded with a nice 7.4, the spread between high and low is considerable and there is a large group that gives a lower score.
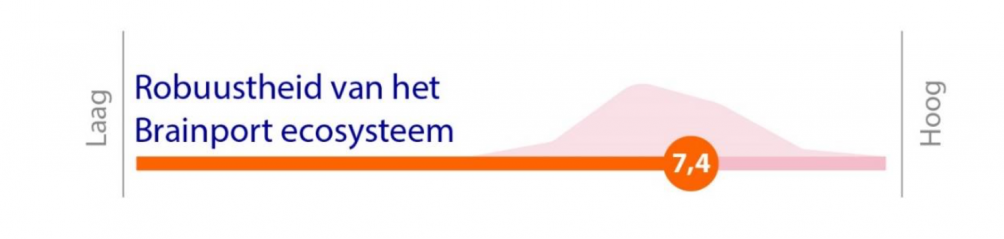
Perhaps this is also due to the differences between the sectors, says Jos van Rooij, Senior Relationship Manager for the Industry Sector at Rabobank Corporate Clients. “The high-tech manufacturing companies are generally doing well and the outlook there is positive. High-tech, Healthtech and the semiconductor industry are rightly optimistic. Their order books are still pretty full. But if you look specifically at the automotive sector, for example, that gives a different picture. In general, I think that robustness has increased in recent years. This is because Brainport companies are active in more end-markets, in combination with product diversification and a focus on digital domains.”
Robust and adaptive
Ger Post, lecturer Business Entrepreneurship at Fontys and owner of Stepsto-innovation, also warns against becoming too robust. “Above all, let’s remain adaptive. I see the need for robustness more in the system, including the governance than for the companies themselves.”
And looking at that system, according to Post, there is, mainly, much reason for optimism. “The entire system was created in the 1990s in response to the problems at Philips and DAF. The collaboration between government, industry, and knowledge institutes that was conceived at the time also helped us through the crises that followed. If there is a problem, we know where to find each other, as you can see now. If we can hold on to that, this region will remain strong in the years to come.”
The supply chain
Despite the excellent starting position, there is a challenge to develop this further and to work on improving resilience. This applies in particular to the supply chain. “A better balance is needed between serving existing value chains and finding and tapping into new value chains and end markets”, the researchers concur. An important part of the investments and innovations at the OEMs takes place at the suppliers. This is expected of them and it is also an important strength of the ecosystem. However, being shockproof, combined with the need to continue to invest, requires a lot from the companies in the chain, especially financially.
Much will therefore depend on the relationship between the OEMs and the suppliers that work directly with them. The dependencies are not always healthy. “We don’t have to worry so much about the top layer, the so-called ‘tier 1’ companies, but in the layers below you regularly see companies that depend on a large OEM like ASML for more than half of their turnover, says Post. “A better spreading would definitely help, but that’s not so easy. If ASML knocks on your door again because there are more orders, you don’t say no so quickly.”
If ASML sneezes…
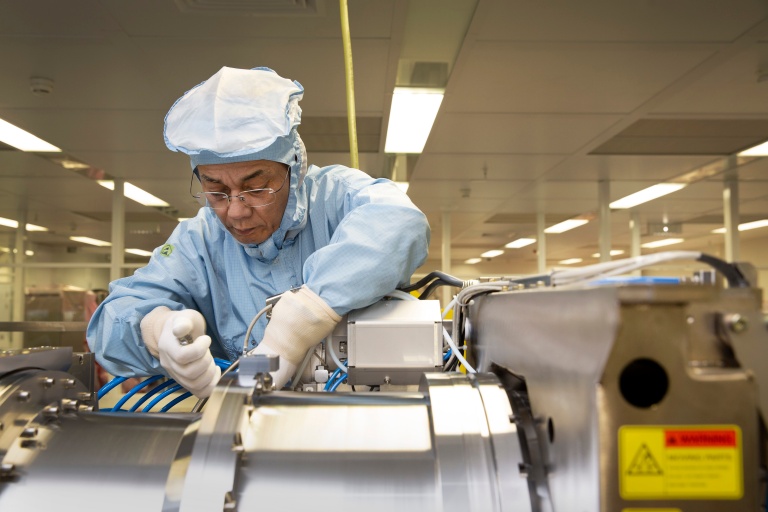
ASML is certainly not the only OEM in the region. Philips, DAF, VDL, and Thermo Fischer Scientific can also be included, albeit in different relationships with their suppliers. This also applies to a relatively new player such as Additive Industries, which has acquired a position on the world market in a short period of time but has a much less dominant position towards suppliers. The dependence of SMEs on ASML is unparalleled, says Jos van Rooij. “If ASML decides to move up a gear, the entire chain moves along with ASML. That’s logical and not a problem as long as it’s viewed from a situation of abundance. But you sometimes hear the fear that if ASML sneezes, the entire ecosystem will catch a cold. Of course, we have to prevent that and that’s precisely why it would be good if there were more ASMLs.”
For many of the ‘tier 1’ suppliers there is something else that’s special, adds Ger Post. “They may not be OEM, but they are OMM, ‘Original Modules Manufacturer’. They supply complete modules as an end product to, for example, ASML. Think of companies such as NTS, AAE, VDL ETG and KMWE: all of them companies that are ultimately responsible for products that may eventually become part of another machine, but which do have their own Research and Development and service provision to customers.”
Boundaries
An interesting question pops up around the extent to which the Brainport ecosystem is bounded by the borders of South-East Brabant. After all, why should a supplier not also seek help from an OEM outside Brainport? And vice versa, why shouldn’t ASML also call on suppliers from elsewhere? “In theory, that’s right,” says Van Rooij. “Since recently, we know that that more and more can be done remotely. And indeed, you see that there are companies from outside Brabant that can really call themselves part of the system. But these are exceptions, and it’s fair to say that proximity also has major advantages. You notice that especially when there are issues: those responsible within the interplay of entrepreneurs, knowledge institutions, and governments always know where to find each other on time. That phone call caused by an emergency situation is a lot more effective if you’ve met each other in person just before.”
In addition, the chain can also cross borders together. “Which also happens literally,” Van Rooij observes. “Companies such as Frencken, Prodrive, KMWE, Sioux Technologies, and NTS have production locations in countries such as China, Malaysia, the US, or Germany, precisely because the OEMs from Brainport are also located there. This has major advantages: it strengthens the link in the chain, but it also makes it easier to find new talent on location, for example. This enables the suppliers to grow along with the OEMs and reduces their dependence.”
Read the other articles published so far in this 12-part series.