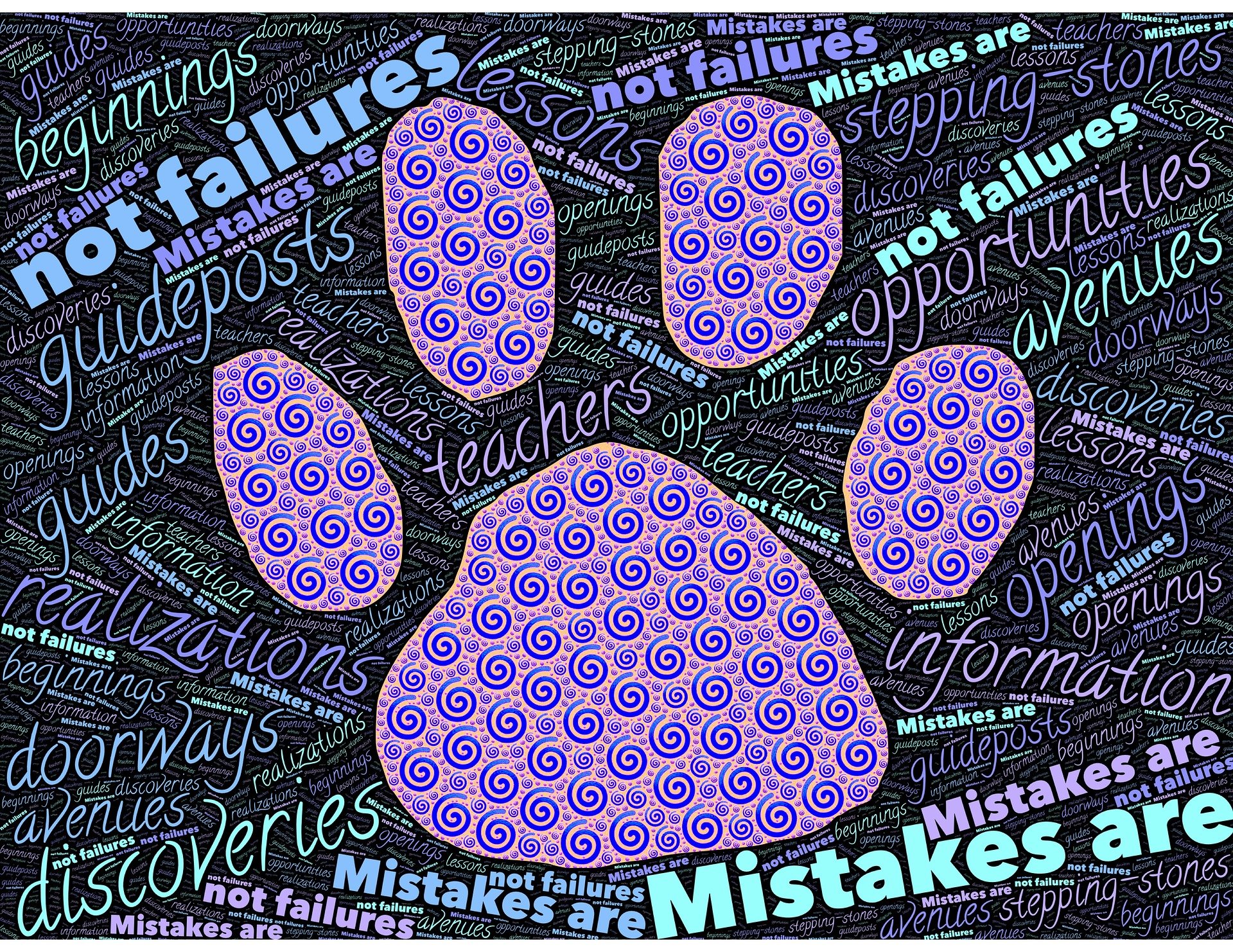
More and more HR officers, directors and managers are dealing with the topic of “error culture” and “failure” in their companies. On the one hand, the so-called VUCA world has become a tangible reality for many companies, and not just since Corona. Sales, procurement and labor markets are increasingly characterized by high volatility, uncertainty, complexity and ambiguity. The cycles of change in the markets have become shorter and shorter in recent decades. This reduces the ability to plan and increases the susceptibility to errors. On the other hand, young professionals and graduates have very clear expectations of the culture and purpose of a company. And this also includes dealing with mistakes and failed projects.
Mistakes or failures are experiences we are reluctant to deal with. In many schools, we still learn that we should do everything correctly and make as few mistakes as possible. We are expected to be perfect in reproducing and applying what we have learned. Mistakes are considered to be something bad and lead to disparagement and disadvantages. This continues on later in professional life. We strive for perfection, for smooth processes and predictable results. Those who cannot achieve this disrupt the system.
Creative and innovative solutions
However, this is at odds with the demands of reality. Rapidly changing conditions mean that we have to adapt to these changes more and more quickly and find creative and innovative solutions. But creativity and innovation are at odds with freedom from error and perfection. Flawlessness requires that we have clear benchmarks against which we can measure compliance with a standard or target state. But these relate to the past and we cannot be sure that norms and expectations that were correct in the past will still be correct in the future.
The term “error culture” implies that we can cultivate a way of dealing with errors. Often, supporters of such a culture are accused of downplaying mistakes and overlooking the business consequences of errors and failure. Errors are associated with costs in the form of money, time and other resources and thus represent waste and must be negative per se. And what sense would it make to “cultivate” waste? Proponents argue that mistakes are ultimately learning experiences and should as such be viewed more as investments than as waste.
The avoidance of dealing with terms such as error or failure means that there are very different assumptions and demarcations about these terms. Is a failure now a waste or an investment? And how might we tell the difference? What distinguishes negative from positive mistakes, blameworthy from praiseworthy mistakes?
Two simple criteria
Harvard professor Amy Edmondson suggests two simple criteria for evaluating mistakes: Predictability and avoidability. Foreseeable errors are those for which it is known that a particular behavior or action will result in error X. Preventable errors are those where the parties involved have an influence on whether or not the error occurs. Blameworthy or “negative” errors are those that are predictable and preventable. These include deliberate deviation from process descriptions, inattention, and lack of skills that lead to errors. If errors are not predictable or avoidable, Edmondson refers to commendable or “positive” errors that happen, for example, during experiments or uncertain conditions.
When we talk about “error culture,” we should be clear about what we mean by an error. Not all errors are the same. A culture that allows and tolerates avoidable and predictable errors, allowing arbitrariness and the waste of resources, will not last long. On the other hand, a culture that is intolerant and sanctions unavoidable and unpredictable errors will suppress any creativity or willingness to innovate.
It is the differentiated handling of errors and their causes that makes an “error culture” a success factor. Successful companies manage to cultivate this differentiation. They allow and even provoke errors where exploration and creativity are required and sanction them where clear processes and specifications make errors predictable and avoidable.
About this column
In a weekly column, written alternately by Eveline van Zeeland, Colinda de Beer, Eugène Franken, Carina Weijma, Katleen Gabriels and Bert Overlack, Innovation Origins tries to figure out what the future will look like. These columnists, occasionally joined by guest bloggers, are all working in their own way on solutions to the problems of our time. So that tomorrow is good. Here are all the previous articles.