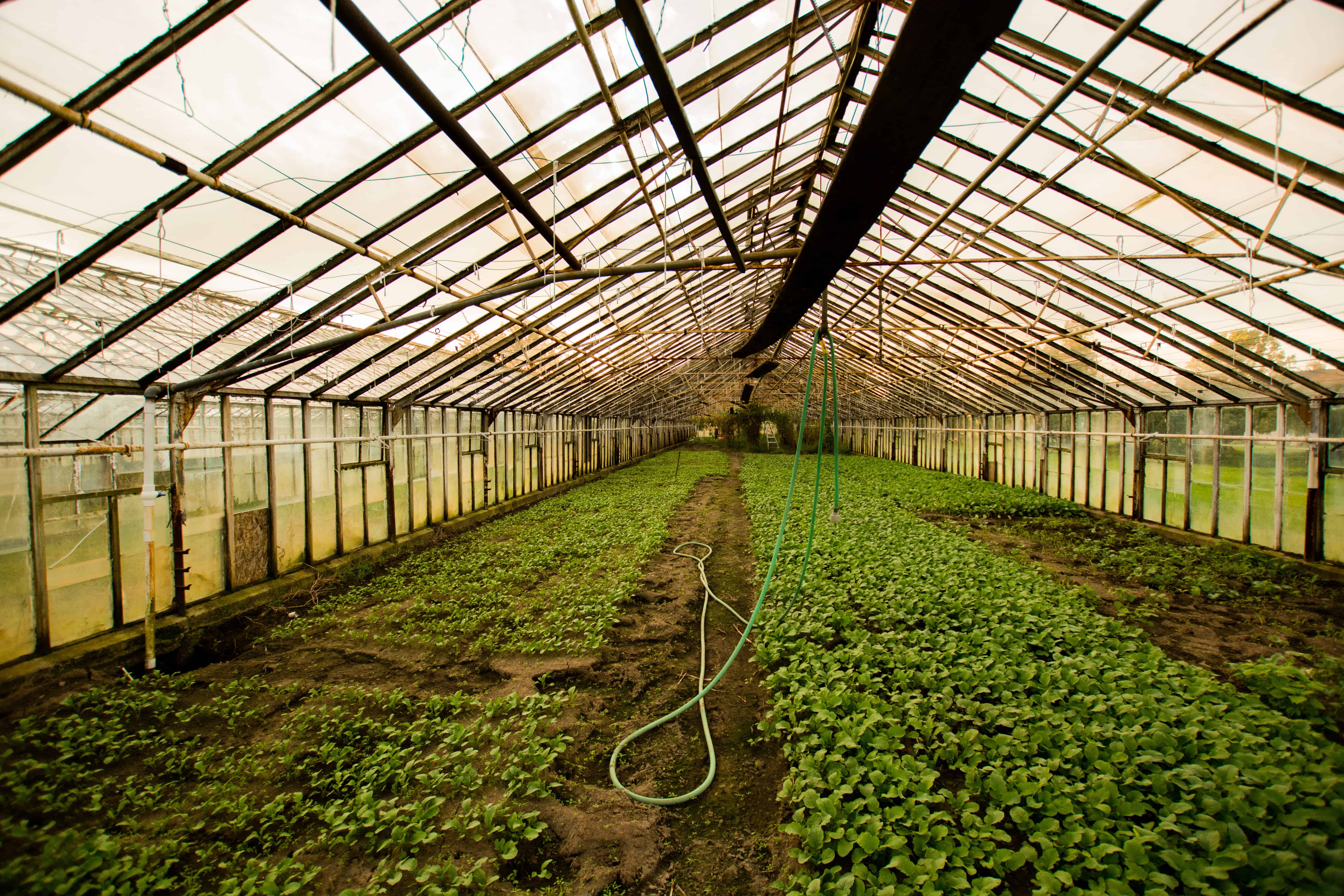
The world is slowly heading towards a sustainable future. Yet the worrying concentrations of carbon dioxide in the atmosphere remain an inescapable fact. Dutch company Skytree recently received a multi-million dollar investment to market their pioneering technology for the decentralised capture of CO2. This means good news for greenhouse horticulture, among others.
- Thanks to a new grant, Skytree can bring a CO2 capture system to the market.
- This will mainly come in handy in greenhouse horticulture.
How does Skytree’s technology work?
Skytree’s technology, Direct Air Capture (DAC), involves the use of filters that ‘harvest’ carbon dioxide molecules from the outside air. Inside these filters is a specially designed material, solid state sorbent (Porous plastic beads with added benzylamines), to which the CO2 molecules adhere. By heating this material, the molecules are released again when they are needed. Skytree technology originated at the European Space Agency in Noordwijk. Since 2014, Skytree has further developed the DAC technology.
Never before has the concentration of CO2 in the air been as high as it is today: 415.79 parts per million. That is considerably more than desirable for a healthy climate. Ice core studies show that before industrialisation in the 19th century, global CO2 concentrations averaged between 180 ppm (during ice ages) and 280 ppm. The excessive presence of carbon dioxide in the atmosphere is one of the main causes of global warming.
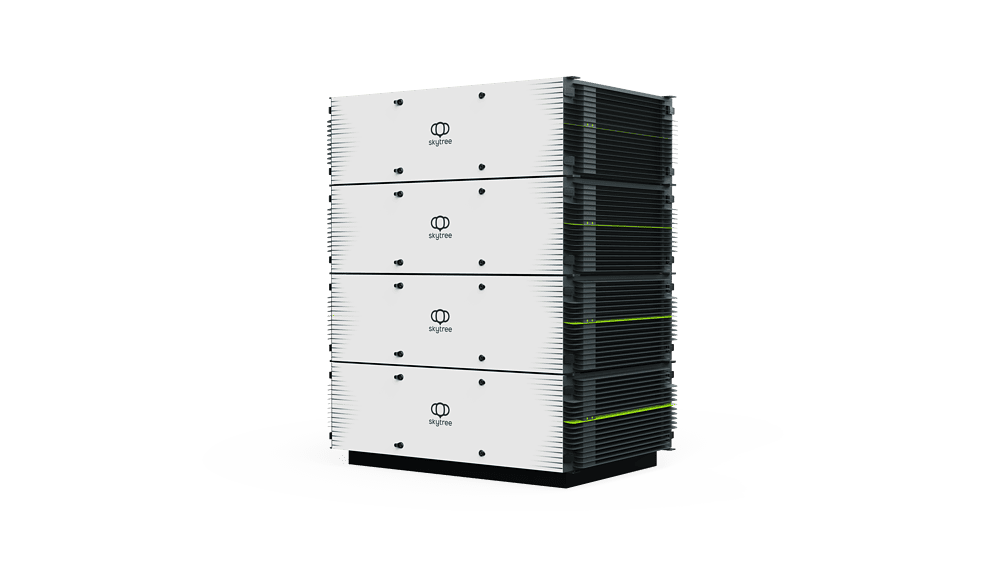
The recent €5.5 million investment in Skytree, from various investment funds and private investors, thus comes at a crucial time. With it, the company can take follow-up steps to filter CO2 from outdoor air and market it. “A molecule that was always known to be harmful now has the potential to be turned into valuable applications in various industries and sectors,” says managing director Rob van Straten.
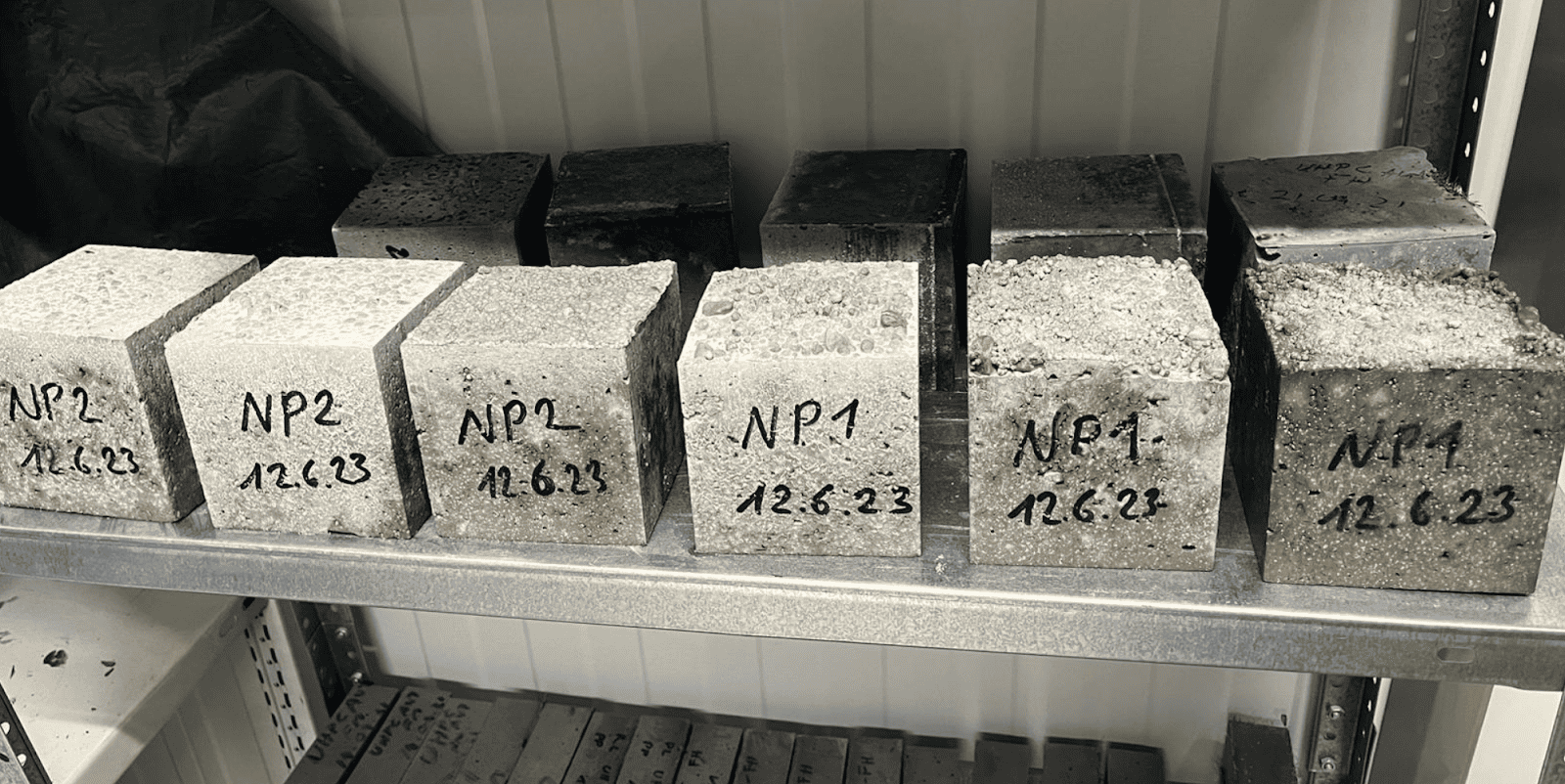
Greenhouse horticulture
The largest investor is Horticoop: a collective of 380 Dutch greenhouse growers. Almost a third of Dutch horticulturists are now shareholders in the company. CO2 comes in handy in greenhouse horticulture, among other things. Van Straten: “It significantly increases crop production. The production of tomatoes, flowers or cucumbers, for example, sometimes increases by up to 30 per cent.” This is because plants use the gas for photosynthesis, resulting in greater growth and yield.
CO2 and greenhouse horticulture
In the Netherlands today, CO2 is often captured in large industrial plants, such as oil refineries and fertiliser producers, and then used by greenhouse growers, for example, to stimulate plant growth. But certain elements of this process, such as the capture process, purification steps and transport, add extra CO2 emissions to the total. This creates more emissions. So Skytree addresses this problem, with its machines that operate cleanly and are also placed right next to the greenhouses.
Numerous applications
Besides greenhouse horticulture, CO2 comes in handy in many more sectors, Van Straten explains. For instance, it is used in the production of champagne and beer, but also for welding techniques and medical applications. “In addition, we foresee significant growth in the future in the use of CO2 for the production of green hydrogen,” Van Straten says.
Scaling up
In short: The world is open to Skytree. It wants to become a global supplier of the innovative CO2 capture equipment. However, this will not happen automatically. “Scaling up requires several steps. Besides perfecting the technology and getting it ready for production, the installed devices also need maintenance. That means we need to expand our organisation to ensure good quality, logistics and customer service.” So there will be plenty of work to do in the coming years.
Skytree recently introduced the Cumulus, a system that removes 12 kilos of CO2 from the air. “We are currently in production and sales and expect to serve the first customers early next year,” says Van Straten. This system is intended for vertical farms and all kinds of pilot projects. Next year, the company will bring the Stratus to market, the size of a 10-foot container with a capacity of 200 kilos per day. This system can be clustered for even higher capacity and is particularly suitable for greenhouse farming. “We are planning the first pilots for this larger system next year, and production is expected to take place in the second half of 2024.”