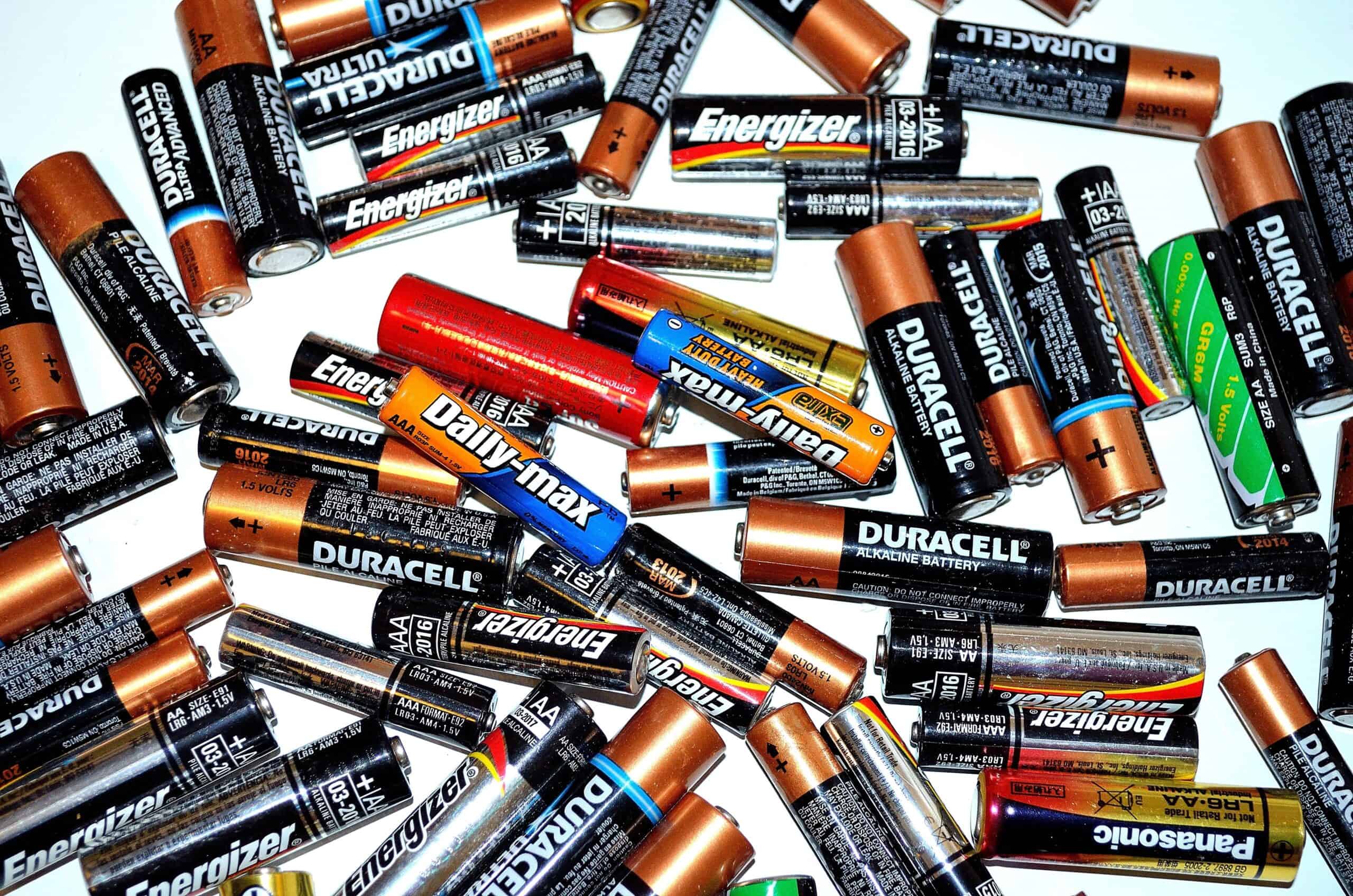
The French government has presented two lithium battery recycling projects funded under France 2030. This is reported by the Dutch embassy in Paris on its website NL in France.
The start-up MeCaWaRe is to install a pilot line at the Verkor research site (one of the future gigafactories) in Grenoble, while Canada’s Li-Cycle has announced it will establish a recycling unit in Harnes in the Hauts-de-France region. Their technology recycles all types of lithium-ion batteries, with a recovery rate of up to 95%.
Following the announcement of five gigafactories in northern France, the recycling aspect is receiving plenty of attention in France. The management of mountains of spent batteries – or “urban mining” – will be an environmental but also an economic challenge in the future, as they constitute a stockpile of critical metals (especially in terms of lithium, nickel, and cobalt) that may prove crucial to supply Europe with metals that cannot be found in France.
Funding from the ‘France 2030’ program.
That is why in February 2023, the deputy minister of industry, Roland Lescure, announced funding two battery material recycling projects under the France 2030 program, which provides 2.9 billion euros to secure access to raw materials. Two pilot lines will receive 30 million euros in support under the project ‘Recycling, recyclability and reprocessing of materials’. One is a proposal by Veolia and Solvay on a site owned by the former near Metz (Moselle), and the other is by MeCaWaRe (Isère) at the Verkor company in Grenoble,
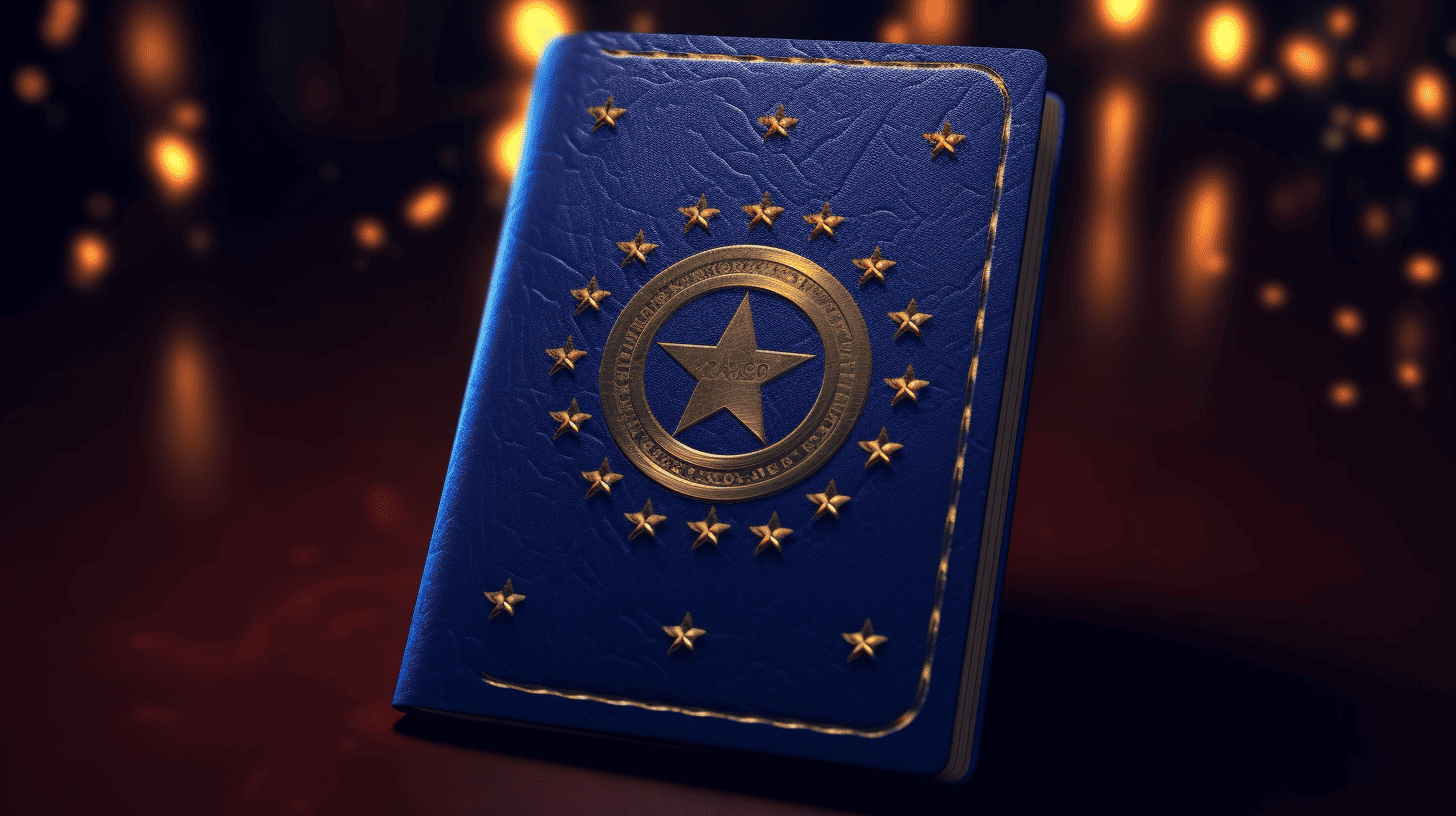
Industrial park in 2028
As part of the consortium between waste recovery specialist Veolia and chemical company Solvay (which Renault joined in 2021), the France 2030 program honors the project for a hydrometallurgical recycling demonstration project near Metz (Moselle). This advanced technology will allow lithium to be recovered from used batteries and meet the high recycling rates set by future battery regulation. The plant will have to process 4,000 to 7,000 tons of used battery powder (the black mass produced by Veolia) per year.
Veolia said that the goal is to leverage Solvay’s chemical expertise to achieve sufficient purity to reuse recycled metals in new batteries. An industrial processing unit capable of processing 30,000 tons of batteries per year will be built by 2028.
Scrap CO2MET
MeCaWaRe has partnered with Grenoble-based start-up Verkor to install a gigafactory for batteries in Dunkirk and has Renault, Schneider Electric, Capgemini, and Arkema among its partners. This young spin-off from the Institute of Molecular and Supramolecular Chemistry and Biochemistry (ICBMS), founded in 2020, will install an initial recycling pilot (50 to 100 tons per year) in Grenoble, in Verkor’s new R&D center. If all goes well, an industrial-scale project (6,000 to 8,000 tons) is planned next, but at Verkor’s gigafactory in Dunkirk.
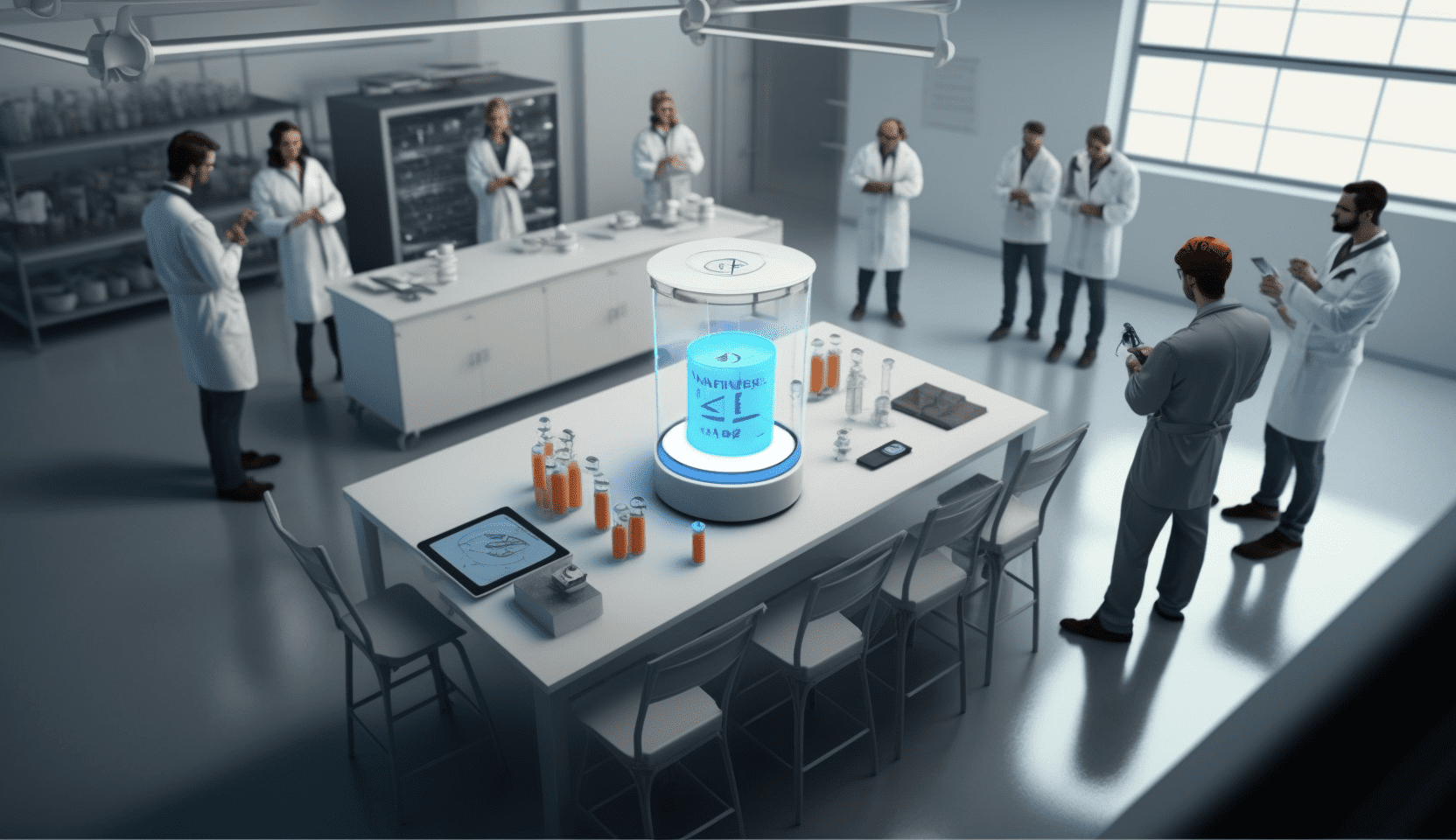
This is the first major customer for MeCaWaRe, which is developing a revolutionary battery recycling technology that uses captured CO2 in plants instead of acids. The start-up, which focuses solely on manufacturing waste often abundant in battery factories, plans to install several small recycling units directly in or near mega factories.
Metal & Carbon Waste Recycling
MeCaWaRe is a deep-tech startup from Lyon’s Saint-Etienne research ecosystem. MeCaWaRe stands for Metal & Carbon Waste Recycling and is housed at PULSALYS, Lyon Saint-Etienne’s deep-tech incubator and accelerator. It has a process unique in the world: it recycles technological products, particularly batteries, to recover critical metals and rare earths (lithium, cobalt, nickel, manganese, lanthanum, etc.) in an eco-efficient, i.e., ecological as well as economic, way. The technology comes from the Institute of Molecular and Supramolecular Chemistry and Biochemistry (ICBMS) in collaboration with the Laboratory of Catalysis, Polymers, Processes, Materials (CP2M) and the Institute of Molecular Sciences of Marseille (ISM2), with support from SATT Sud-Est.
MeCaWaRe’s pioneering process is based on innovative chemistry where strategic metals are recovered with high efficiency and purity (from 98 to 99.9%), while industrial CO2 emissions are at the core of the process, and no liquid wastewater is generated. The process operates at atmospheric pressure and ambient temperature and consumes very little energy: this important economic achievement should allow to halve the operating costs and position this innovation in industrial sectors to meet the energy and environmental challenges.
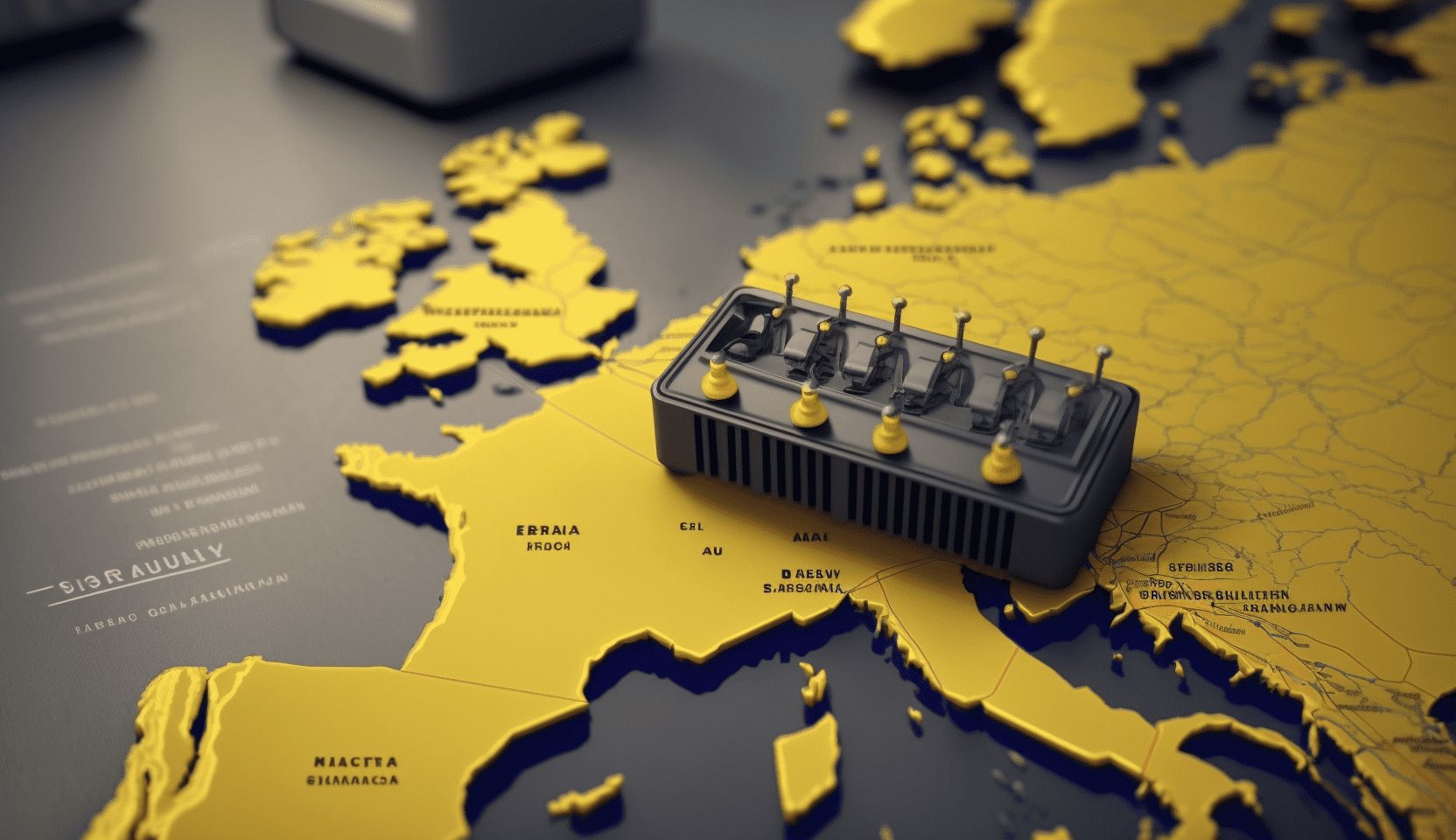
In November 2022, the government presented five projects to accelerate the production of critical metals in France, including the Eramet project for recycling batteries (Relieve). Because of its to start in Trappes in 2023, the latter project has recently received European funding of €70 million.
Li-Cycle
Another new project is the lithium-ion battery recycling plant of the Canadian company Li-Cycle in Harnes (Pas-de-Calais) which should be operational in 2024. In late March 2023, Li-Cycle announced its plans to locate in France. The Canadian company will establish itself in Harnes (Pas-de-Calais) with a lithium-ion battery recycling plant.
At startup, the site should have a processing capacity of 10,000 tons of material per year with about 30 people employed. Eventually, the processing capacity should reach 25,000 tons. Li-Cycle’s patented technology will be used for this purpose. With this solution, all lithium-ion batteries can be recycled, with a recovery rate of up to 95%.
The recovered materials, particularly lithium, cobalt, and nickel, can be reintegrated into the supply chain, helping to reduce the extraction of these rare components. With Li-Cycle’s “third generation technology,” batteries are entirely recycled, without manual disassembly.
Li-Cycle will run 100% on renewable energy and produce no industrial wastewater.
This will allow Li-Cycle to better position itself in the French battery market, especially in the Hauts-de-France region, where four gigafactories are already planted.