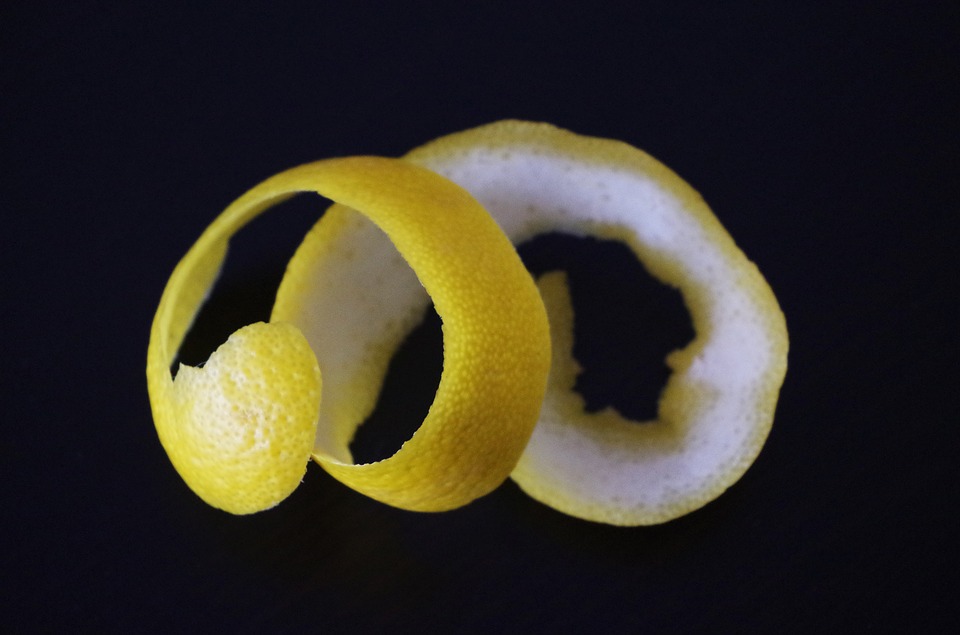
Extracts of lemon and almond peels can be used for sustainably produced car parts and building components. This BARBARA project jointly funded by the European Union and industry ensures that food waste can be put to good use, replacing petroleum-based plastics with more environmentally friendly bioplastics.
The BARBARA project is supported by the European consortium called Bio-Based Industries. The intention is to make new bioplastics from extracts of plant residues for use in so-called fused filament fabrication or FFF, reports the EU. FFF is a versatile and widespread 3D printing technology.
The motivation for the project is mainly that there is a lot of superfluous food.
“EU countries produce around 110 million tons of animal and plant waste annually, while 33% to 50% of all food produced worldwide is never eaten,” explains BARBARA coordinator Berta Gonzalvo Bas.
While most commercial bioplastics in use today, such as plastic bags or other single-use materials, have poor mechanical and thermal properties, BARBARA researchers are focusing on much more robust and high-performance applications.
Strong and heat-resistant
By chemically processing starch and similar biological compounds from corn by-products and developing bio-additives based on lemon peels, almond husks, pomegranate and inorganic enhancers, hybrid nano-biocomposite materials are produced. These new biopolymers are not only strong and exhibit a high thermal resistance, they can even be produced in different colors with additional functions such as antibacterial or odor-giving properties.
These new compounds are currently being tested for different applications. These include 3D printed car door handles and dashboard components developed in collaboration with Centro Ricerche Fiat. Moulds for load-bearing truss connections that meet the strict thermal and mechanical requirements of the construction industry are also being developed in collaboration with ACCIONA Infrastructure.
It is hoped that, thanks to Barbara partners’ technology, these new biopolymers and similar products will be able to compete with petroleum-based plastic materials that are currently being produced and disposed of on a large scale.
One-fifth less CO2
“End products made with these biopolymers should result in a 40% reduction in costs and a 20% reduction in CO2 emissions. The sustainability of the entire production process will thus be significantly improved,” says Gonzalvo Bas. Partners include production companies, agricultural cooperatives and leading research institutes. They want to look at the processes and production techniques of the project for commercial operation so that potentially innovative new industries can be developed.
“The use of biobased and biodegradable materials in combination with additives extracted from vegetable residues and by-products is considered one of the most important pillars of the circular economy. We are transforming agrifood waste into a valuable raw material,” concludes Gonzalvo Bas.