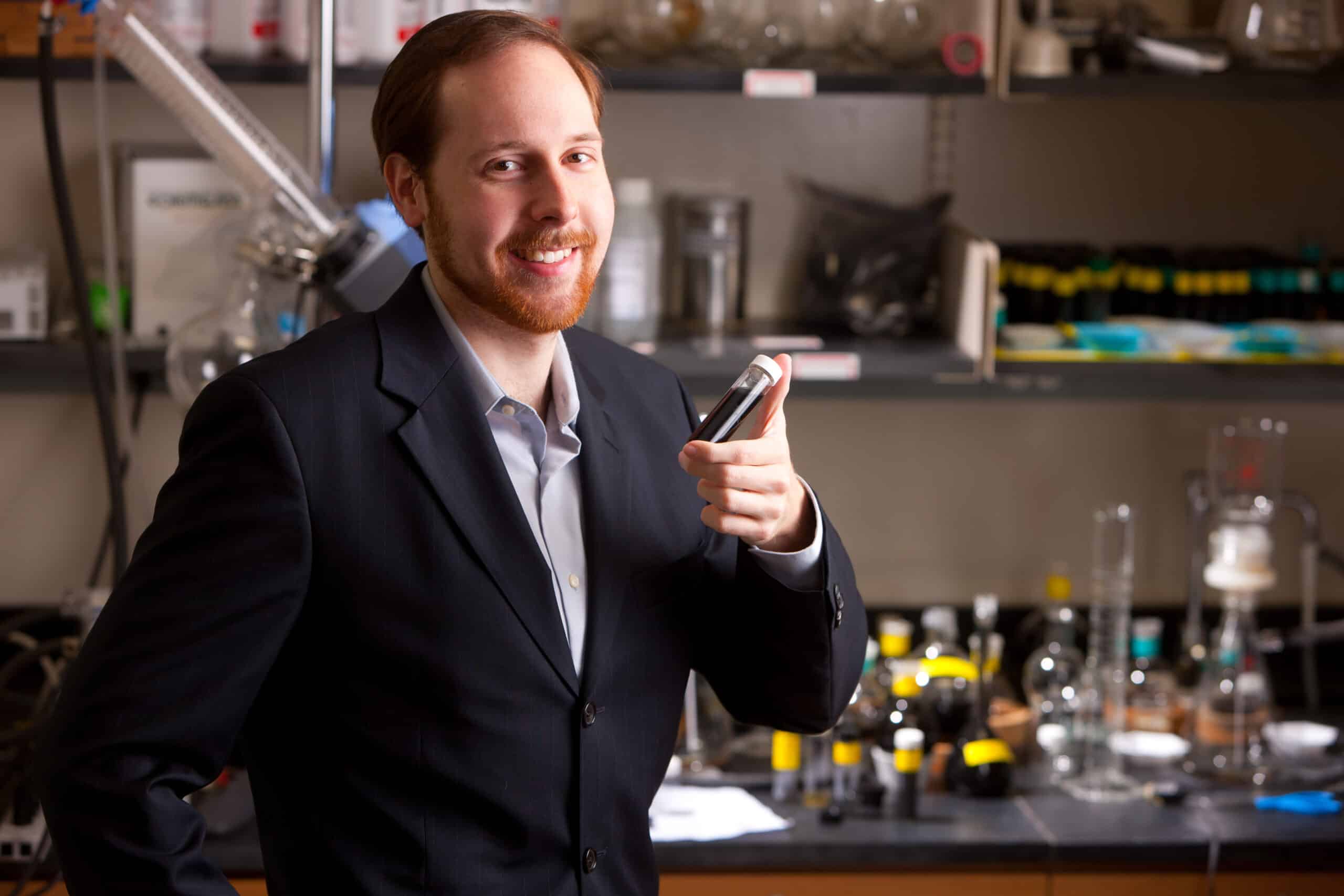
The advantages of silicon for batteries have already long been known. But because of its limited life cycle, safety concerns, and high costs, it has always failed to turn those advantages into actual results. GDI says it has now overcome all these obstacles. With an investment of 13 million euros, the American company will start pilot production this year in Eindhoven, the Netherlands.
“GDI’s patented 100% silicon anode technology increases energy density and reduces charging time and can thus become an important driver of the further development of electric vehicles and e-mobility,” says CEO Robert Anstey. The big difference is in the use of silicon instead of graphite. “Besides completely replacing graphite in lithium-ion batteries, we also manage to achieve a good price/performance ratio. That will make the difference for electric car manufacturers and end users.”
Fifteen-minute charging
Silicon is considered a promising active material in anodes because of its ability to store large volumes of lithium ions, resulting in a battery with significantly higher energy density than batteries made with conventional graphite-based anodes. Whereas many battery manufacturers use a small amount of silicon (less than 10%) in their graphite anodes to improve their energy density, GDI’s approach – with 100% silicon – yields much better performance and increased safety by preventing lithium dendrite formation.
What does that mean for an end user? “Suppose you drive a Kia e-Soul with a 64 kWh battery and 425km of range, with GDI’s silicon anode, you would increase the battery to 85 kWh and at least 550 kilometers of range. Charging 350 km will take 15 minutes – barely enough time to get a cup of coffee and stretch. And that’s not to mention during the winter when that car has about 100 kilometers less range because of the cold; that issue will also be improved because silicon performs well at low temperatures.”
Lithium
The presence of silicon in virtually every place in the world is another major advantage over graphite. Anstey: “Our silicon anode technology frees us from dependence on any single country, such as China, which control over 90% of the battery grade graphite production. On the other hand, silicon is the 2nd most abundant element in the Earth’s crust.”
Unfortunately, Anstey and his colleagues don’t provide an alternative to lithium for EVs. “With some regularity, we all hear the stories about producers who claim to be able to build a high-energy battery without lithium, but just a quick look at the periodic table of elements shows that lithium is the smallest and lightest ion. You end up hearing about potassium (K) or sodium (Na), but they are 3-6 times heavier/bigger than Li-ions. With volumetric energy density at a fraction of Li-ion, especially vs. silicon, Na and K ion batteries will only achieve very short distances, or they will be used primarily in stationary storage. So for the complete replacement of gas cars with Evs, we really have to rely on lithium.”
Eindhoven
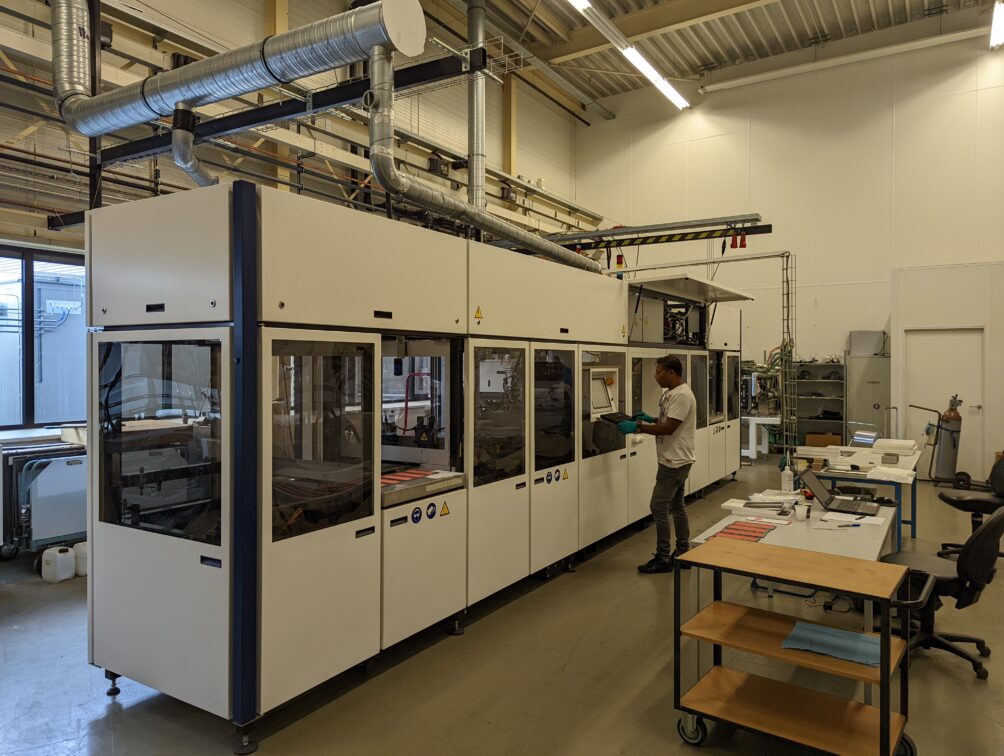
GDI has set up a European pilot production facility in Eindhoven. Near the local airport, it has been working with several European manufacturers for some years already, and that cooperation is now being intensified. By the end of this year, GDI anode production capacity will reach over 300 kWh. By comparison, a smartphone has about 12Wh. This will make GDI one of the world leaders in the production capacity of 100% silicon anodes. With the €13M funding, combined with planned strategic partnerships, GDI expects to scale up production to more than 100MWh by the middle of 2024. ”Design for manufacturing is core to our technology’s strength.”
But if silicon can be found everywhere on earth, why does GDI choose to start initial production in Western Europe? “That has everything to do with the region’s history,” says Anstey. “This area was always strong in innovation and glass production and later in plasma technology. We want to build on that legacy.” In addition, says the GDI founder, the presence of qualified personnel is also an advantage this region offers. Currently, the battery developer still involves a handful of staff, but future plans will undoubtedly change that.
EIT InnoEnergy
For co-investor EIT InnoEnergy, GDI fits nicely within the developments around the European Battery Alliance. Within it, a group of some 750 companies is working together to boost Europe’s battery ambitions. “GDI’s ability to seamlessly integrate their solution into existing lithium battery architecture and production lines offers significant cost advantages and enables products to be brought to market faster,” says Roel van Diepen, Investment Director at EIT InnoEnergy. “But just as importantly, adopting a silicon anode reduces dependence on traditional materials such as graphite, making the European battery value chain more resilient while increasing European production volumes.”
Josh Grehan, Principle at Helios Climate Ventures, expects this funding to help GDI gain a position at the forefront of the market. “Advanced silicon anodes can accelerate the adoption of electric vehicles. In addition, these silicon anodes improve the performance of electronic products worldwide with faster charge times, higher energy density, and improved safety.”