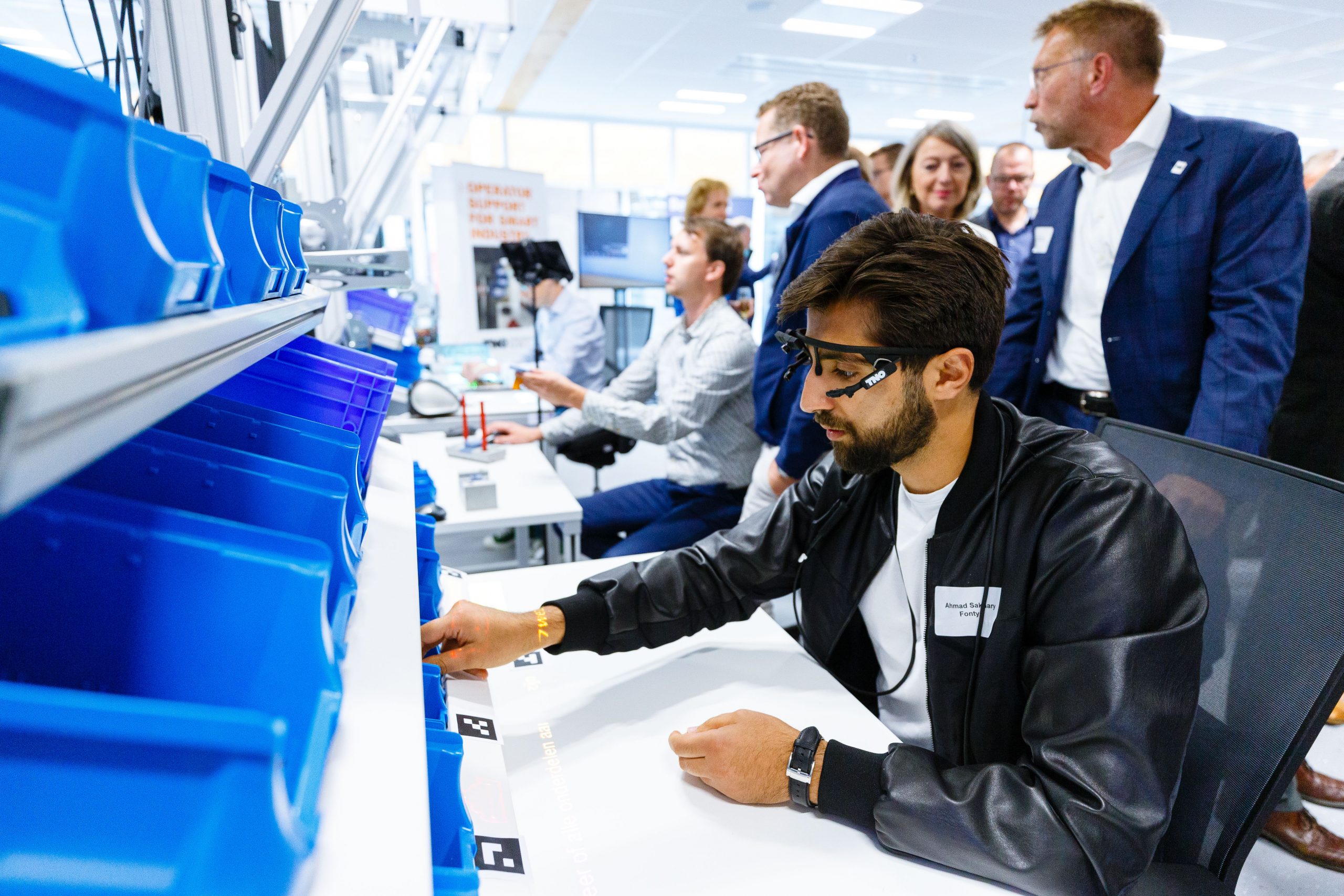
You can look through a glass wall directly down onto a large factory hall. This is where self-driving vehicles – known as palletizers – drive their test rounds. One cart drives around as an order picker equipped with a robot arm. While another brings parts from A to B. Smart technology works together with other existing systems. This allows users to set up the operation of it quickly and flexibly, without the need for complex programming. “Why should you have to keep reinventing the wheel,” Michel Weeda asks himself, shrugging his shoulders. Weeda is the program manager of the ‘Factory of the Future‘ innovation program at the Brainport Industries Campus (BIC) in Eindhoven, the Netherlands.
“A one-trick robot is handy, but in the manufacturing industry, we make complex products in smaller series with lots of variations. That’s why you want to be able to use a robot in different ways without spending a lot of time reprogramming it,” he explains while the trolleys underneath him are making another round. The same applies to other processes in the manufacturing industry. Such as factory logistics as well as automation and robotization of machine tools like lathes and milling benches and 3D printing.
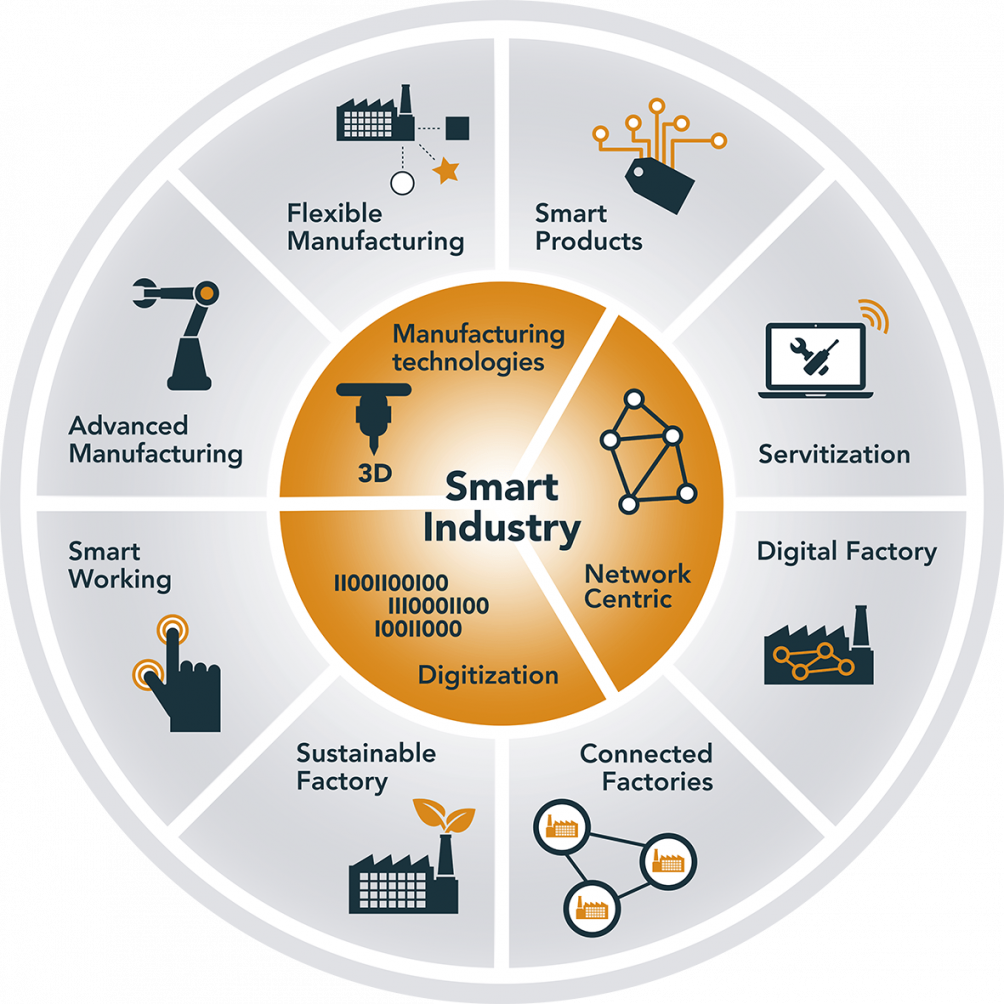
In the innovation program, companies, schools, knowledge institutes and government work together at eight field labs on themes concerning the digitalization and automation of the manufacturing industry. “The ultimate goal is a ‘digital’ factory where manufacturers can track and adjust all their production processes in real-time if they want,” says Weeda. From incoming tenders and design drafts to products or systems that leave the factory floor and are delivered to the customer via the supply chain. All of this is data-driven and connected to each other. This is the only way the Netherlands can stay ahead of the competition.
Software and hardware go hand in hand
For Weeda, the software is crucial in this respect. “This is how you operate smart factories. It enables manufacturers to see exactly when maintenance is needed and where processes can be made more efficient. The strength of the Brainport region is that we have strong software as well as hardware players. These parties all come together in the High Tech Software Cluster, which is also a field lab. But even companies that don’t know what can be achieved with data, for example, can come here too.”
Read more about the High Tech Software Cluster here
The innovation program has been underway for almost two years and various technologies and new work methods are finding their way into practical applications. “The Smart Connected Supplier Network is a good example of this. This network improves data exchange in the supply chain. This concerns product specifications and order data that often change because the end customer changes something. These changes are frequently carried out by hand. This takes time and raises the risk of errors. Now it’s automated and way smarter,” Weeda explains.
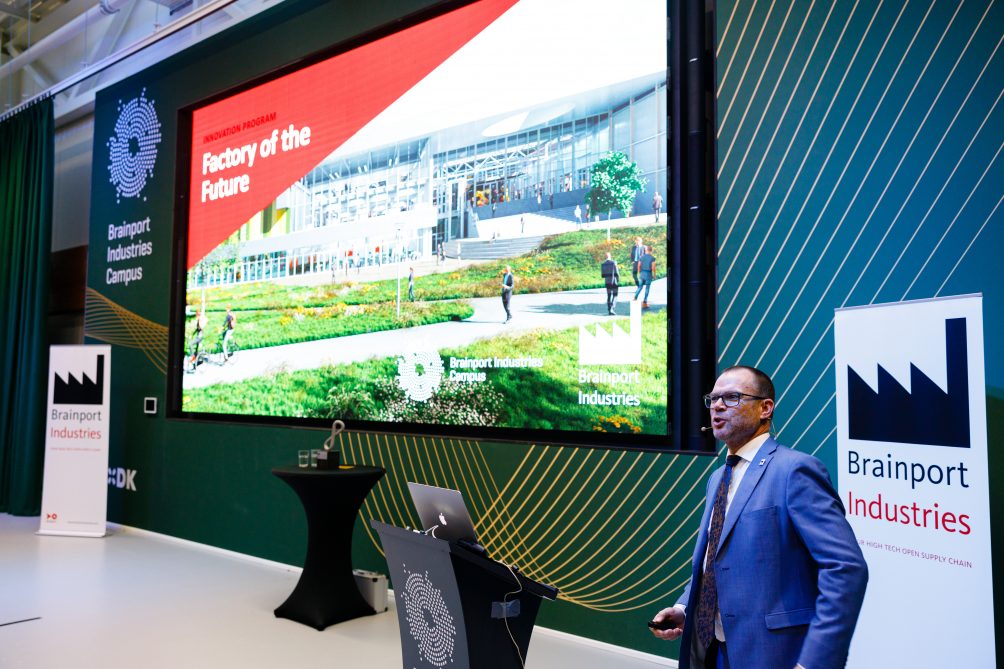
Photo: Bram Saeys;
It works on the same principle as the telephone network, whereby customers from different providers can easily call each other. This means that companies do not have to invest in different software packages. “It has the potential of setting a new standard. More and more companies are joining up. Their numbers are growing rapidly. Moreover, there is also a lot of interest from, and collaboration with, Germany,” says Weeda enthusiastically.
Not just about developing technology
The development of technology is not the only purpose of the field labs. They also aim to promote the sharing of knowledge, talent development, and showcase the potential of technology and digitalization. “People from these companies work together with people from all levels within education. This not only brings in smarter talent, but employees also benefit from the knowledge they gain through the projects. In the form of workshops, for example. This interaction ensures that you keep on learning and can stay ahead of the curve in terms of developments,” says Weeda.
There are now 115 companies, educational and knowledge institutes participating in the innovation program. So far, about 50 business cases have been developed. “Various 3D print innovations in both metal and multi-material printing fields. Around 800 people have been trained and educated this way. We also regularly give international delegations a tour to show what’s happening here and organize events around ongoing projects to spread our message further,” Weeda sums up.
Nevertheless, the program manager has noticed that it is difficult for new companies to make the right connections. Yet he doesn’t dare to hazard a guess as to why this is exactly. “Everywhere I speak, I stress that the innovation program and facilities are not just for companies at BIC. The Smart Industry Hub South is an important network in this regard (development companies, industry associations, and their affiliates are represented here, ed.). They help members on their way and offer support in the world of innovations and field labs.”
‘Want to do something with data? Yes, but what?
Weeda also helps companies to find the right kind of knowledge in the field labs. “A lot happens and each field lab has its own story. There is no gold standard. But at the same time, there is plenty of cohesion. Robotization, for example, is not possible without good software. Not everyone is aware of that by far. I know which field labs are best suited for answering certain questions.” he says, clarifying his role there.
“A lot of companies know that they want to do ‘something’ with digitalization and the data that they have, but often don’t know everything that can be done. They can find inspiration at the field labs. And we have developed a business scan for companies that can’t see the wood for the trees with all the various smart industry solutions. This enables them to get advice on what the best first few steps might be.”
Digitale tour en roadmap
Siemens set up a digital tour of the innovation program in order to also give interested parties an online look behind the scenes. In this tour, they can see what kinds of facilities a field lab has and what the participating parties are working on. Weeda: “Almost everything that can be found at the BIC can be found online here. What machines are there? Can you use them? Are there any workshops and training courses available?”
Despite the fact that the program will run for another two years, we are already thinking about a successor. “Actually, we’ve only just got started. Developments are moving along, so we are already working on new things. For this, we are not only focusing on Brabant or the Netherlands. We are in talks with Germany and Belgium as part of the Smart Factory EU project. We are also working with our partners on a European Digital Innovation Hub. Over the coming years, we want to make sure that the facilities at the BIC will remain available and easily accessible for experiments and research.”
Weeda and other project participants will explain during the Technology Update XL: ‘the 4th Industrial Revolution’ how exactly this follow-up program will look like and how companies can join. The roadmap ‘Factory of the Future’ for the period 2020-2024 will also be presented. You can register and find more details here.