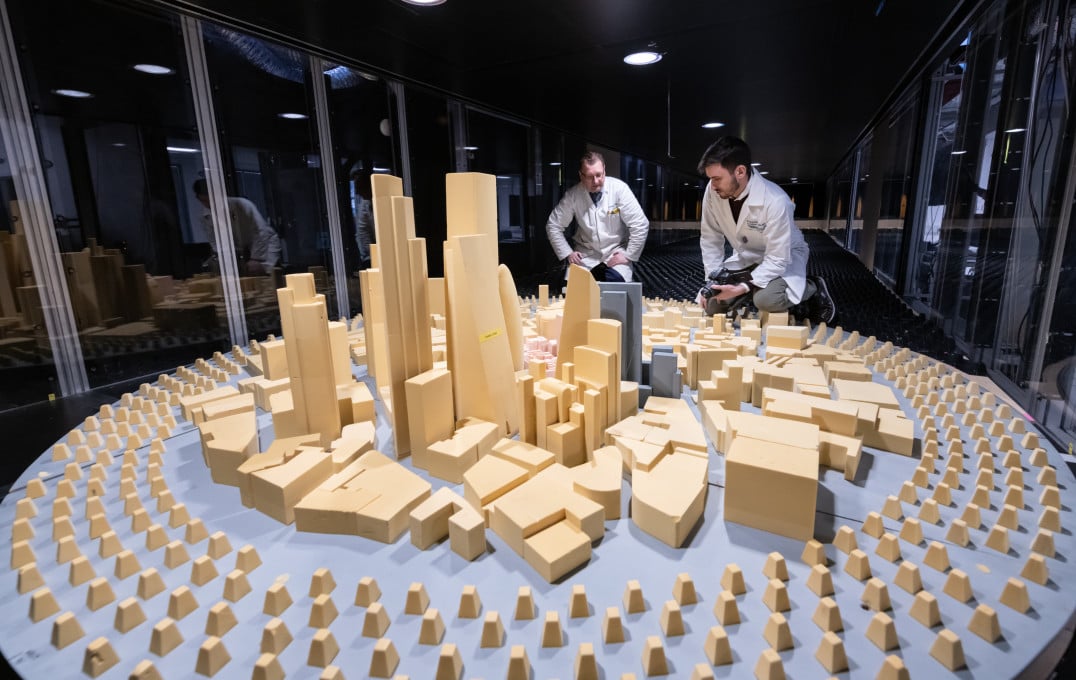
Real wind tunnels are expensive. And the scale models of the objects that are tested for their wind resistance are also expensive. In Formula 1, therefore, the computer has long since replaced not only the good old drawing board for designing the race cars, but the teams themselves are also relying more and more on CDF (computational fluid dynamics) simulations instead of elaborate tests in physical wind tunnels. This development could now soon find its way into the design of cars, ships, and even aircraft.
Apart from being far less expensive than physical wind tunnels, digital representation of flow conditions has another major advantage: digital simulations are more detailed and provide data more quickly than physical wind tunnel experiments. A team of scientists from the U.K., U.S., Japan, Canada and Germany has now shown how digital wind tunnels could be used to make aircraft more efficient and fuel-efficient.
For starters, designing turbine blades for jet engines
Currently, engine turbines are being designed using a combination of Reynolds Averaged Navier Stokes (RANS) simulations and wind tunnel testing. The RANS simulations attempt to capture the behavior of turbulent flow using approximate models. But the accuracy of these simulations leaves much to be desired, especially for unsteady flows. Besides, real wind tunnel tests are not only costly but also time consuming and often provide limited data.
Therefore, direct numerical simulations are becoming more prevalent as they are more accurate and directly capture all aspects of turbulent flow physics. This makes accurate predictions possible even without wind tunnel tests. In their study, the researchers focused on optimizing the design of turbine blades for jet engines to achieve greater weight savings. This could reduce aircraft fuel consumption and at the same time cut emissions harmful to the climate.
Many possible areas of application
“Our simulations are exciting for several reasons,” says the lead author of the paper published in Computers & Fluids, Professor Peter Vincent of Imperial’s Department of Aeronautics. “First, they give us more accurate and detailed data, so we can learn a lot about the underlying flow physics and potentially use them to train new turbulence models using machine learning approaches.”
Second, with advances in computer hardware, it may soon be possible to collect data faster and at a lower cost than physical wind tunnel tests. “Even though digital wind tunnel testing won’t replace physical wind tunnels for several years, our study suggests that it is a real possibility now,” Vincent said.
While the current study was specifically about testing jet engine turbine blades, the results could be useful in many other areas including the design of submarines, cars, skyscrapers and wind turbines. Engineers here are still testing in wind tunnels. “Applications beyond turbomachinery include marine, automotive and green energy where we hope the technology will play an important role in the coming years,” Professor Vincent says. These digital wind tunnels could both reduce costs and lead to improved designs.
Also of interest:
How researchers plan to integrate the structural battery into aircraft components
“Green Operation for Future Aviation” – Climate-neutral production of hydrogen aircraft
Small airplane height adjustment, great effect on global warming