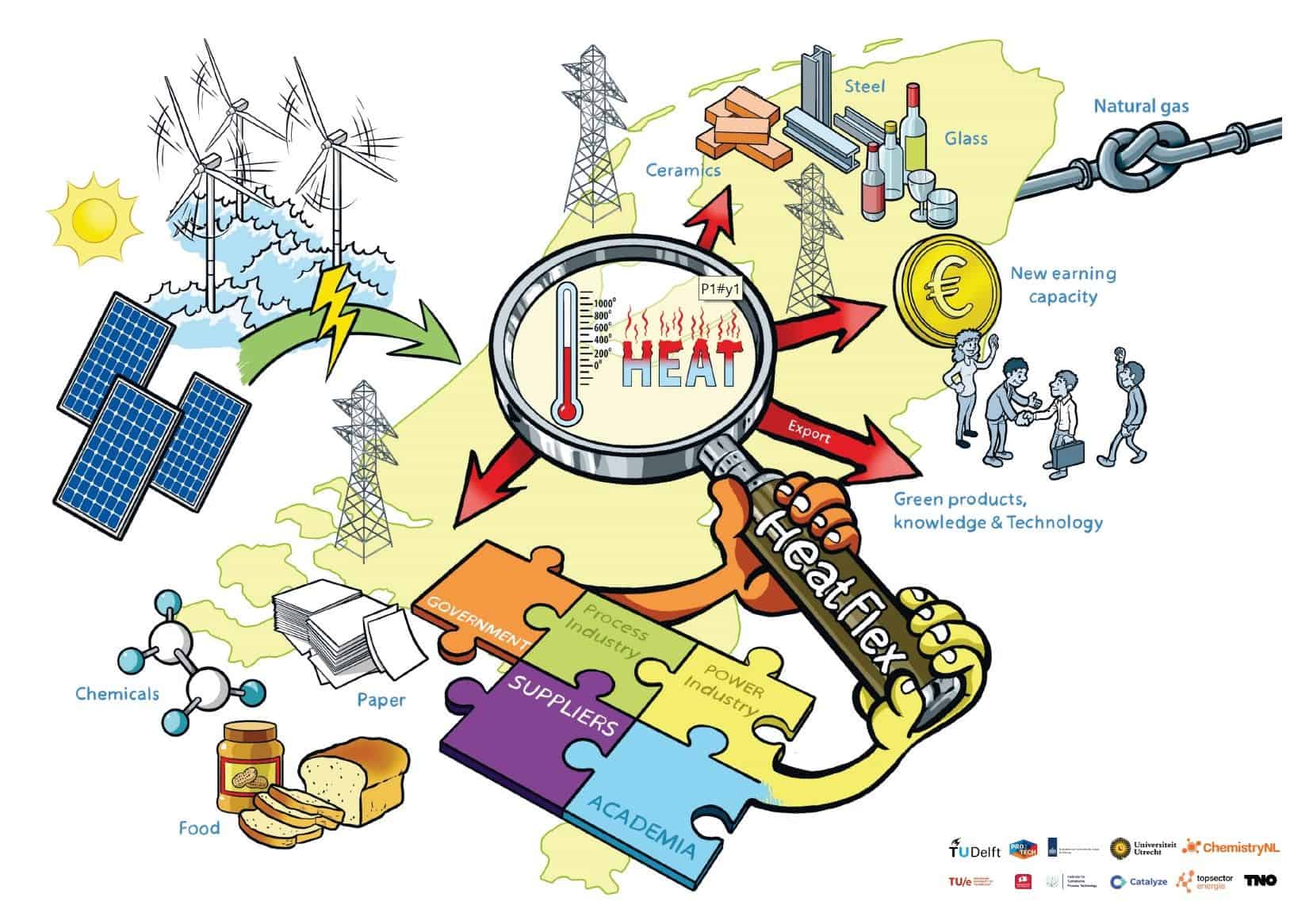
Behind most things we use and consume daily is a specific industrial process. From making ceramic tiles to baking cookies on an industrial scale, there are dedicated production lines. And while these two examples seem at odds, one thing brings these two and many more production processes together: heat. Temperatures vary. Steel manufacturing requires up to 1800ยฐC heat, while producing paper needs a 200ยฐC heat input. As things stand, heat generation is behind 21% of the worldโs CO2 emissions.
Why this is important:
A considerable part of the emissions reduction efforts are bound to the greening of industrial processes. Most of the emissions of this sector come from heat generation.
In an effort to deliver a sustainable heat supply, a diverse team of Dutch academics established HeatFlex. The initiative is supported by four Dutch universities, the institute for applied scientific research TNO, and top sector institutions such as ChemistryNL. The goal is to empower the Dutch industry sector, fostering the uptake of renewables by leveraging, studying, and testing new technologies.
To do so, HeatFlex established several work packages to delve into the different aspects of the matter. โThe prompting question is how do we help the process industry transition to a greener one in a structural and timely way? From there, as a group of scientists, we had the first contact with the industry, which was positive. However, we also realized how a development route was missing, although all the stakeholders felt the urgency of undertaking the transition,โ underlines John Nijenhuis. He is a chemical engineer by training and a technology manager at the Delft University of Technology (TU Delft).
Industrial heat pumps
Heat pump technology advantages are well-known for reducing householdsโ environmental footprint. In 2023, over 150,000 of them were sold in the Netherlands. Adapting this technology to the industrial setting is also one of the ideas for decarbonizing the process industry.
According to the researchers, switching to electricity is essential in this transition, and industrial heat pumps are one of the go-to solutions. They can generate heat and use an existing heat source, bringing it up to a higher temperature. In industrial settings, waste heat generated from processes is one of the ways to source heat. Leveraging a heat source allows a heat pump to produce much more heat with a certain amount of electricity rather than fully electrifying a whole plant.
Although promising, lots of development needs to happen since industrial heat pumps are not yet capable of providing the high temperatures needed by the most energy-intensive industrial processes. โThere is a lot of development that still needs to be done to improve their efficiency and integration. But also, the different technologies used for heat pumps need to be further explored to understand how to increase temperature output,โ explains Rene Pecnik, an energy technology at the TU Delft.
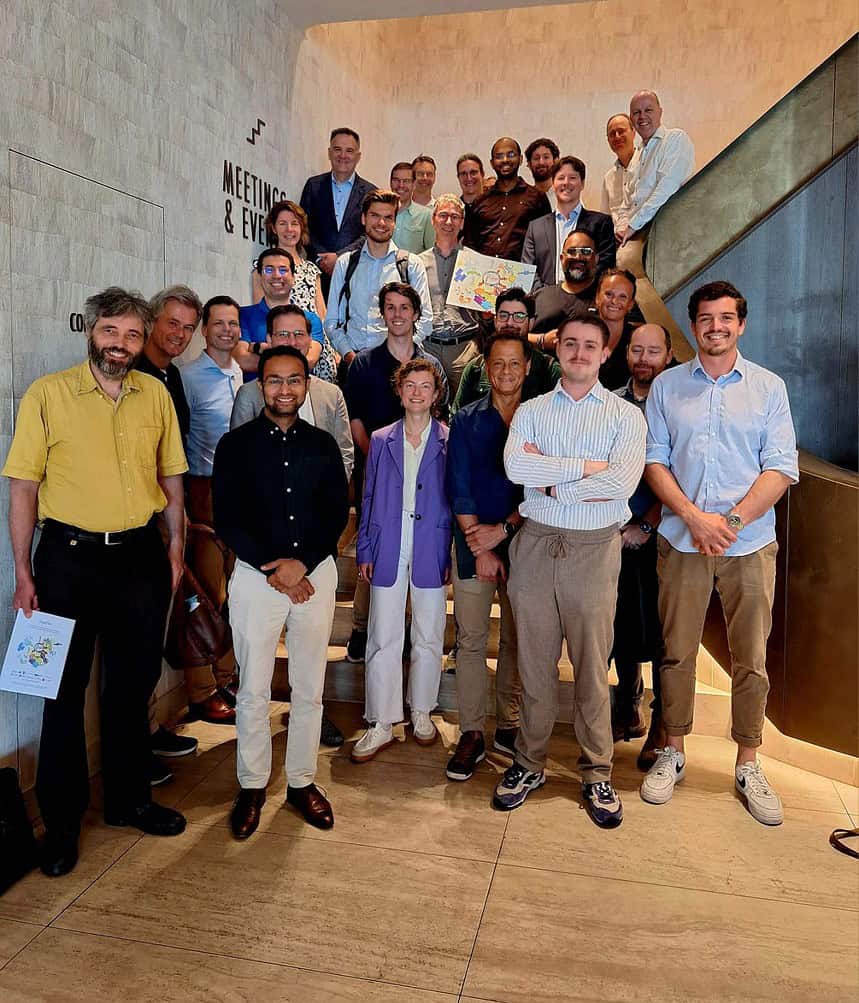
Thermal batteries
To further enhance flexibility, the HeatFlex consortium is also studying the use of thermal heat batteries. This way, companies can optimize their heat consumption. Particularly, the research group plans to integrate molten salt heat storage technology into some demonstration plants.
These salts, which have long been used in the solar concentrated industry, allow storing renewable power for later use. Furthermore, they are a good match with heat pumps. During the day, or in moments when renewable energy production is high, heat pumps can heat the salts, and then store this heat in tanks for later use.
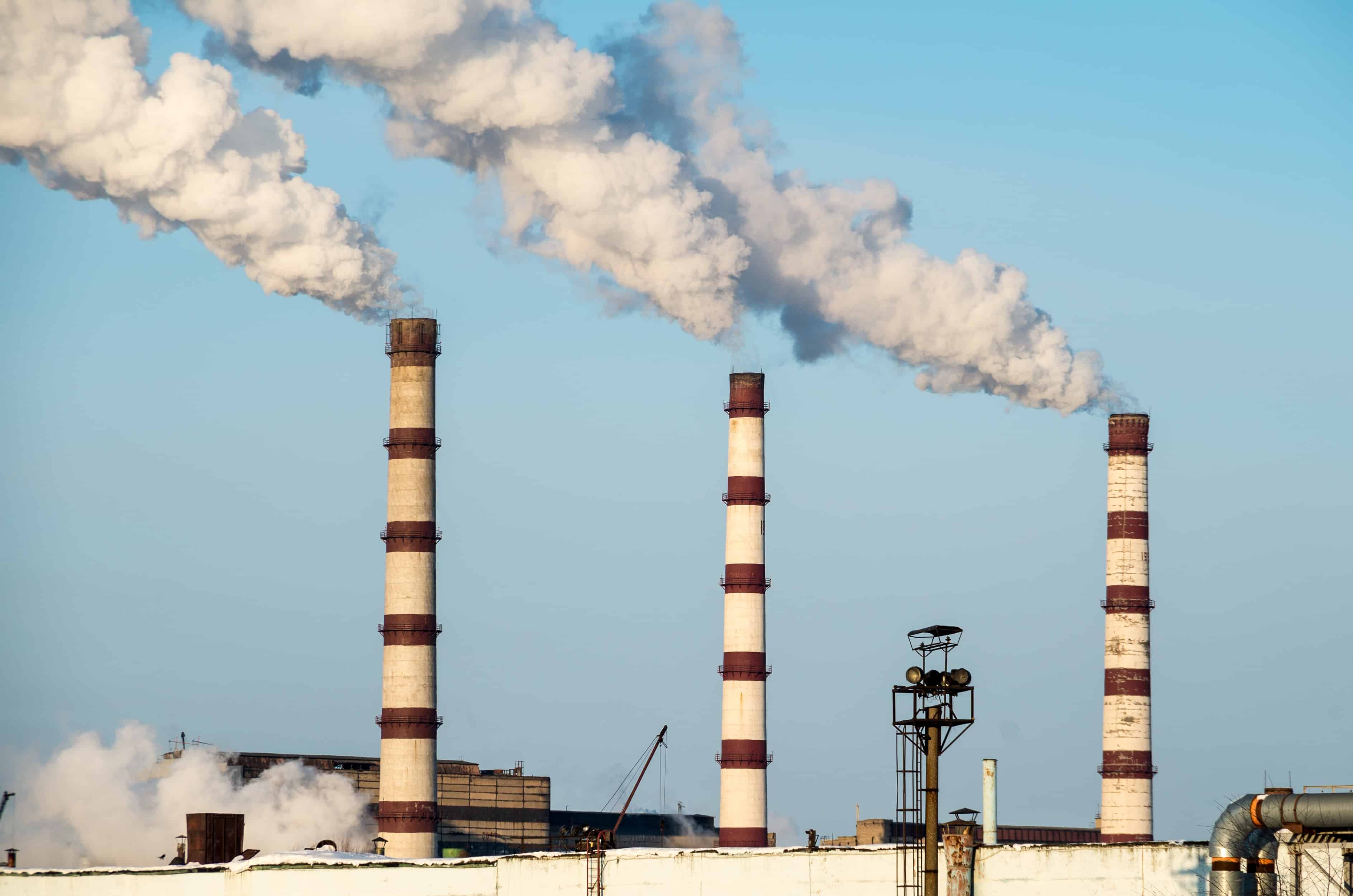
Systematic rethinking
Switching to different technologies entails comprehensively rethinking the industryโs systems and processes that supply heat. โConnecting all the latest developments with the existing industry is the hardest task. Typically, because with fossil fuels, there was no need for it as with renewable sources,โ underlines Matteo Gazzani. He is an associate professor at the University of Utrecht and Eindhoven University of Technology (TU/e) and focuses on rethinking and readapting the industry.
โWhile you can have a long-term contract for gas, connecting to the electricity grid means that your demand should align with the fluctuating supply and maximize your benefits. Thatโs where industrial heat opens up a potential reservoir of flexibility since thermal energy storage is more cost-efficient than batteries,โ explains Robert de Boer, a TNO scientist working on industrial heating systems. Studying the integration of such systems and what technologies work best with different temperature windows is also a task of HeatFlex.
Demonstrations
A cornerstone of HeatFlex is the deployment of demonstrations. These pilots are essential to follow up on the university lab research, putting new tech with real-world working conditions to the test. This way, the validity of technology is not only investigated, but its integration with the existing procedures and system is also verified.
At the moment, discussions for three pilots are ongoing. One of them is to provide a new heat pump design to a company producing food packaging. In another pilot, they plan to develop a direct connection to electric heating. The third company currently uses wood snips to make bioenergy, yet they are looking for a way to store thermal energy and convert it back to electricity.
With climate targets looming, HeatFlex sees its work as instrumental. โAt this point, itโs like a car going full speed against the wall. If we keep relying on fossil fuels but still have to comply with regulations that want to quit them, jumping this wall will become too difficult. With HeatFlex, we are building a ramp to jump this wall,โ Gazzani sums up.