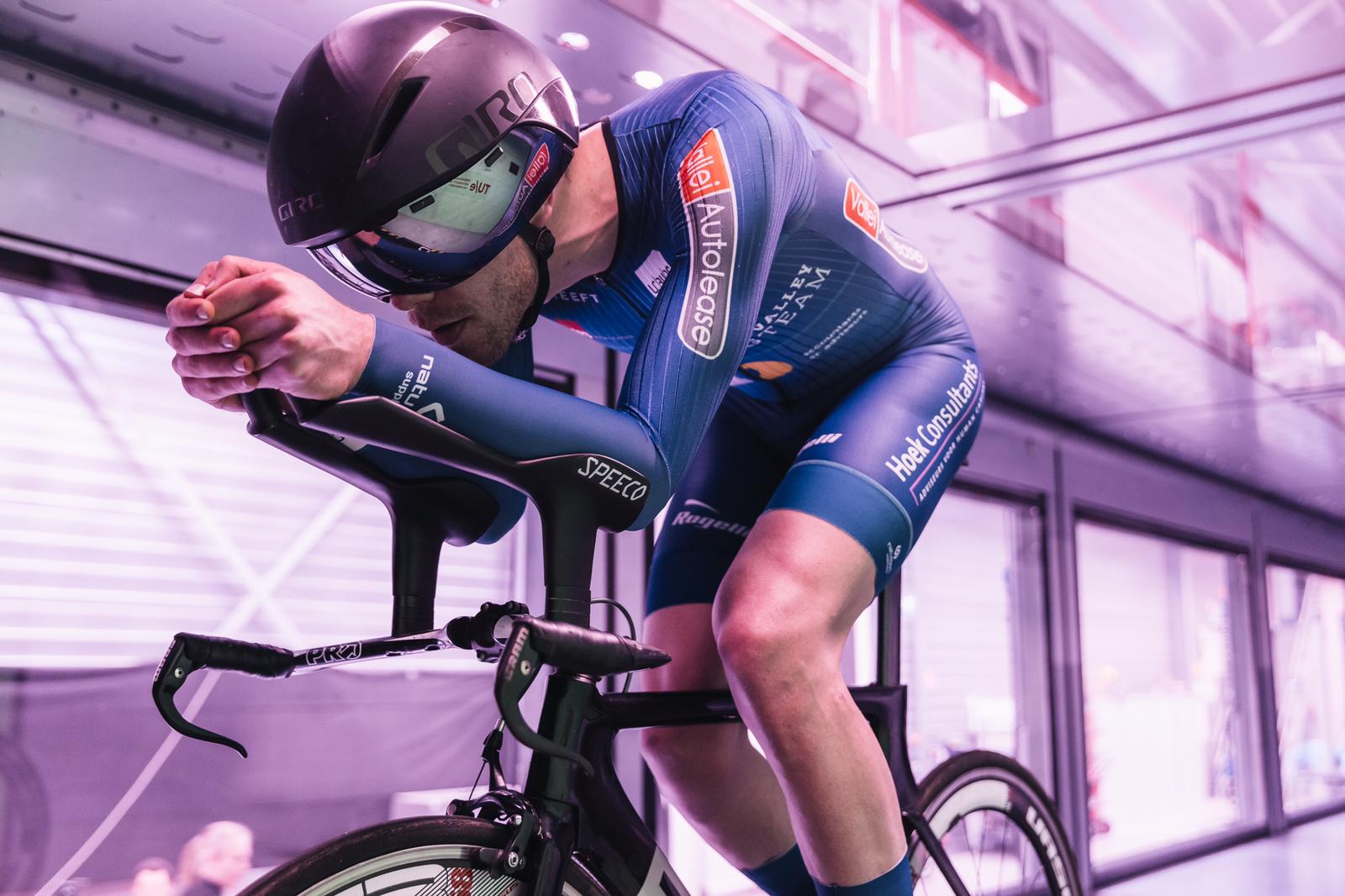
Studying and performing sports at a high level, many people see this as a difficult combination. Especially if you also want to add your innovative solutions in an entrepreneurial setting. For Noah van Horen and Jules de Cock, it turns out differently. The two time trial riders combine cycling with their studies and their drive for innovation at the Eindhoven University of Technology (TU/e). With the knowledge gained with their study and the added practical experience, they designed a new armrest for their bikes. One that is more aerodynamic, comfortable and affordable than current models. How is that possible? By automating handwork, they say.
Dutch champion Marien Bogerd and Dutch student champion Pieter ten Kortenaar will soon ride their time trials with an armrest made by Speeco, the students’ start-up company. The first customers have already arrived. At first, it started as a homemade solution to a problem they encountered while cycling. “I made the first prototype of the armrest during my graduation project for the Bachelor of Mechanical Engineering”, says de Cock. “I rode it at the national championships time trial for students. People immediately came to us and wanted to know more.” From then on, the project of the two fanatical athletes is slowly growing into a start-up.
Aerodynamic
During a time trial, in which the fastest cyclist wins, aerodynamics is very important. The more wind the athletes catch, the slower they go. That’s why they sit completely bent over on the bike, with their arms in a horizontal pose, on an armrest. There are currently two types of armrests, one adjustable and one handmade. “Such an adjustable bracket is for sale in the bicycle shop. But because of its adjustability, such an armrest never fits perfectly and is not stable”, Van Horen explains. “A custom-made bracket fits the cyclist’s arm exactly. But it also has a huge price tag on it”. These armrests are currently only available for the best time trialists in the world.
With Speeco, Van Horen and De Cock try to combine the price tag of the adjustable support with the comfort of the handmade support. “If the support fits perfectly around the arm, the wind moves more easily along it. That provides more aerodynamics. It’s also more comfortable. Because the support is made exactly for the cyclist’s arm, he or she is also immediately in the right aerodynamic position,” says De Cock. “Then the cyclist doesn’t have to look for the right position during the ride. Which also saves time.”
The students tested the armrest in the university’s wind tunnel. “It turned out to be 2.5 percent more efficient than the old handlebars”, Van Horen continues. “That doesn’t seem like much, but in this sport, it’s a lot. You can’t gain that much in a year by just better training.”
3D printer
To achieve this, Van Horen and De Cock measure a client’s posture very precisely. They then produce the armrest out of carbon, using 3D printed molds. “It’s partly made by a machine, but it also takes quite a lot of hours of manual work”, Van Horen explains. “Our goal for next year is to make the design process completely parametric. That means that we fill in a few values in a machine and that it then automatically generates the product.”
In this way, the students try to make a product with the characteristics of a handmade product part of an optimized production process. “That’s how the price can remain low. We think our armrest will cost about €1600, while the fully handmade versions cost more than €3000”. This makes the product accessible to a larger group of cyclists, the students think.
Small market
The students don’t want to say exactly how the production process works. The market in which they find themselves is very small, which is why it is often unprofitable to apply for patents. De Cock: “Working with carbon is a complicated process, which requires certain knowledge. Not everyone can reproduce it just like that.” Moreover, it was a puzzle to ensure that the armrest was approved by the cycling association. “There are strict rules that the bikes must comply with.”
Comfort
In the future, the students also want to look at an armrest for a triathlon bike. Van Horen: “There is a bigger market for this in the Netherlands. The development of custom saddles and shoes is also an option according to them. “We can’t gain that much in terms of aerodynamics, but it does provide extra comfort,” says De Cock. So there are plenty of ideas to make cyclists even more comfortable – and faster.
Van Horen: “It’s nice to combine the lessons we’ve learned as an automotive engineer and mechanical engineer and put them into practice. At TU/e innovation Space students receive guidance in entrepreneurship. “We are now trying to set up a business together with a business administration student. In doing so, we run into very different things than in school. The goal is to really help athletes further with our products.”