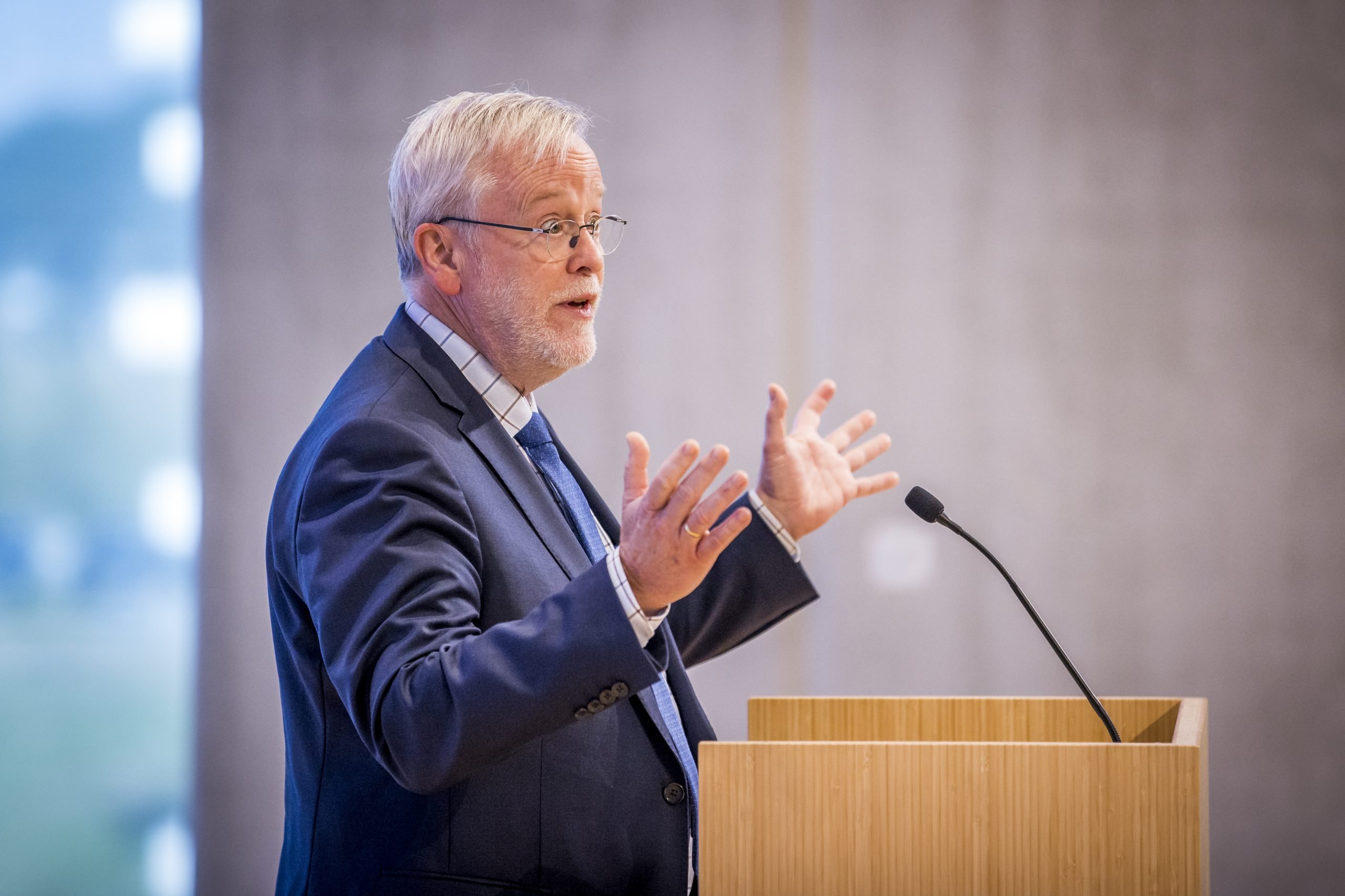
Who knows nowadays that DSM is an abbreviation of De Staats Mijnen (The State Mines)? There could hardly be a greater contrast with the present. The mines, which guaranteed prosperity through the coal mining and once formed the basis for the modern-day DSM chemical group (along with huge CO2 emissions) have long since closed their doors.
Today the Brightlands Chemelot Campus is located on the old DSM site in Geleen, the Netherlands. There, DSM, along with its former subsidiaries that were sold to the SABIC chemical group, is researching how to make raw materials circular. Like plastic, for example.
The aim is to drastically reduce CO2 emissions in order to meet the Paris climate targets. In addition, the groups and other companies on the site must quit using fossil fuels such as petroleum naphtha products and natural gas.
The idea is that the Brightlands Chemelot Campus will become the most important hub in the field of circular chemistry known to Europe. That is according to Bert Kip, director of the campus.
Geleen celebrates its 80th anniversary of innovation of raw materials
Kip introduced journalists to the activities and objectives of the campus on the occasion of the 80th anniversary of the innovation of raw materials in Geleen. In Kip’s opinion, the Brightlands Chemelot Campus holds a pivotal position in the world where the development of circular raw materials is concerned. The reason for this is that the volumes of raw materials produced by companies like SABIC are so enormous, that they influence the entire chain of plastic products around the world.
“We have years of expertise here on chemical processes. How to scale them up and how to eventually market them,” Kip said. “There are a lot of large parties involved with other components on the site that have made their business out of this. Our combination is unprecedented. If you ever manage to set up a circular hub somewhere, it would bound to be right here in Geleen. I feel confident in claiming that standpoint. We are the first hub in Europe to create a circular reality here. We produce millions of kilotons of material right here. All of which lands on the market. If we were to reuse all the plastic waste from the Netherlands in the SABIC cracker located on-site, then that would only be a slight percentage of the cracker’s total output.”
“If you are able to make raw materials more sustainable at the initial stages of production, you are then making the entire chain of processes that subsequently follow more sustainable. Plastic granules are made from these raw materials. They are used to make plastic bags, car bumpers, or medical implants, to name a few examples. Anything and everything! If you make the raw material of a product sustainable, the entire chain will then become sustainable.”
Naphtha and natural gas have got to go
As Kip points out, large-scale factories run on naphtha and natural gas. Both of these are fossil fuels. They determine the CO2 footprint of raw materials up to, and including, the end of the lifespan of products. This is the point when they are then burnt as waste. The goal is to minimize the waste stream and ensure that naphtha can be replaced as a fuel. This is done by producing oil from waste. You put it in the cracker. Once you do that, you make the processing of raw materials a truly circular process. This has not quite gotten off the ground as yet. Because you always end up losing a little. So, then you need to fire up a bit of biomass. The aim is to make the entire chain circular.”
One of the ways to achieve this is for all municipalities in the Dutch province of Limburg to offer their waste collectively. This is what Ruud Burlet (FvD) believes, the representative in charge of this issue. “We need to tackle this project on a grand scale and see how we, as a society, can best align with the industry that processes this plastic waste.”
Experimenting with circular technology
In order to become fully circular, Limburg and the Chemelot Campus are innovating in three ways. Kip explains further: “First, we look at companies around the world that already have this circular technology in place. Then we look at whether we can bring them over here. An example is Plastic Energy. Secondly, there are companies that are experimenting with new circular technology. We also intend to bring them on board here at the campus. Thirdly, we have research institutes where we bring together great minds from the universities, TNO (the Netherlands Organisation for Applied Scientific Research, ed.), and the business community. They are also building on new technologies together.”
These new technologies from Limburg should eventually enable naphtha and natural gas to be replaced with renewable sources of fuel. These include waste, biomass, green electricity, and CO2-free-produced hydrogen.