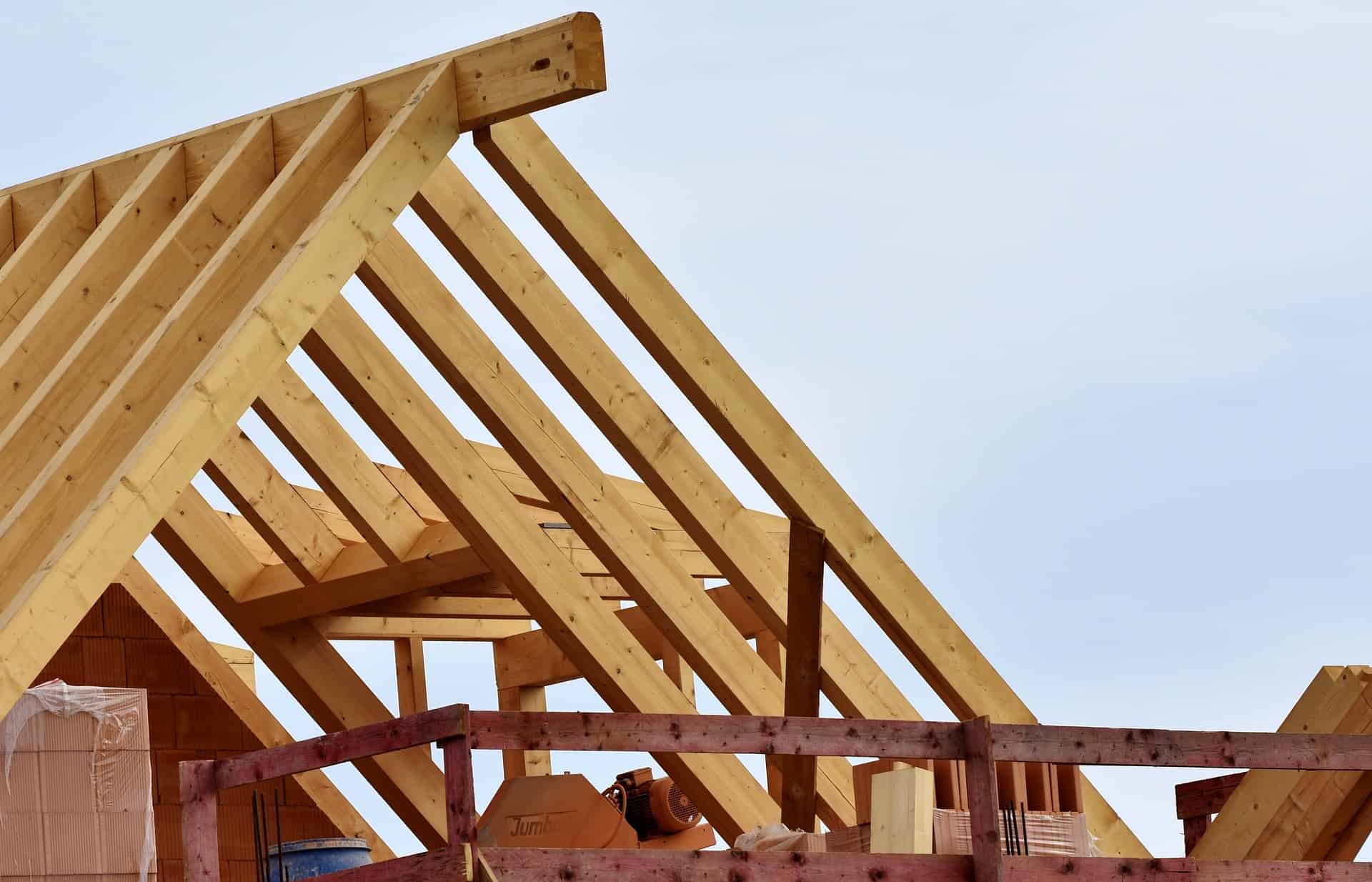
There is a good chance that the next generation of housing will be built from flax, wood fibers and elephant grass. “The production of concrete, steel and bricks still emits too much CO2. We need to build more with biobased materials,” is the rallying call from Monique de Vos, co-owner of sustainability company Faay. That all seems very cool and innovative, but there are some snags. The techniques and materials are already here, although actual practice shows that their use is taking time to catch on.
What are biobased building materials?
Biobased building materials are made from animal material or from fungi, plants and bacteria. They must be ecologically grown, used and then able to be reused. A material is biobased if it is made from a raw material from living nature that can grow back within a hundred years after being harvested. Another essential condition is that the material is later reusable as a raw material in new building materials.
Biobased building materials can overcome problems surrounding resource scarcity, supply security and CO2 capture. “That’s not even mentioning the healthier indoor environment, lower nitrogen and CO2 emissions and the establishment of additional production chains at the hyperlocal level,” according to a recent study.
It is therefore not for nothing that the PBL Netherlands Environmental Assessment Agency sees it as one of the most important pillars on the path to a circular construction economy. But for the time being, however, the results are disappointing, as the proportion of biobased materials in the construction sector is still negligible. “Wood accounts for 2 percent and other biobased materials collectively have only a proportion of 0.1 percent,” Arcadis stated in the study.
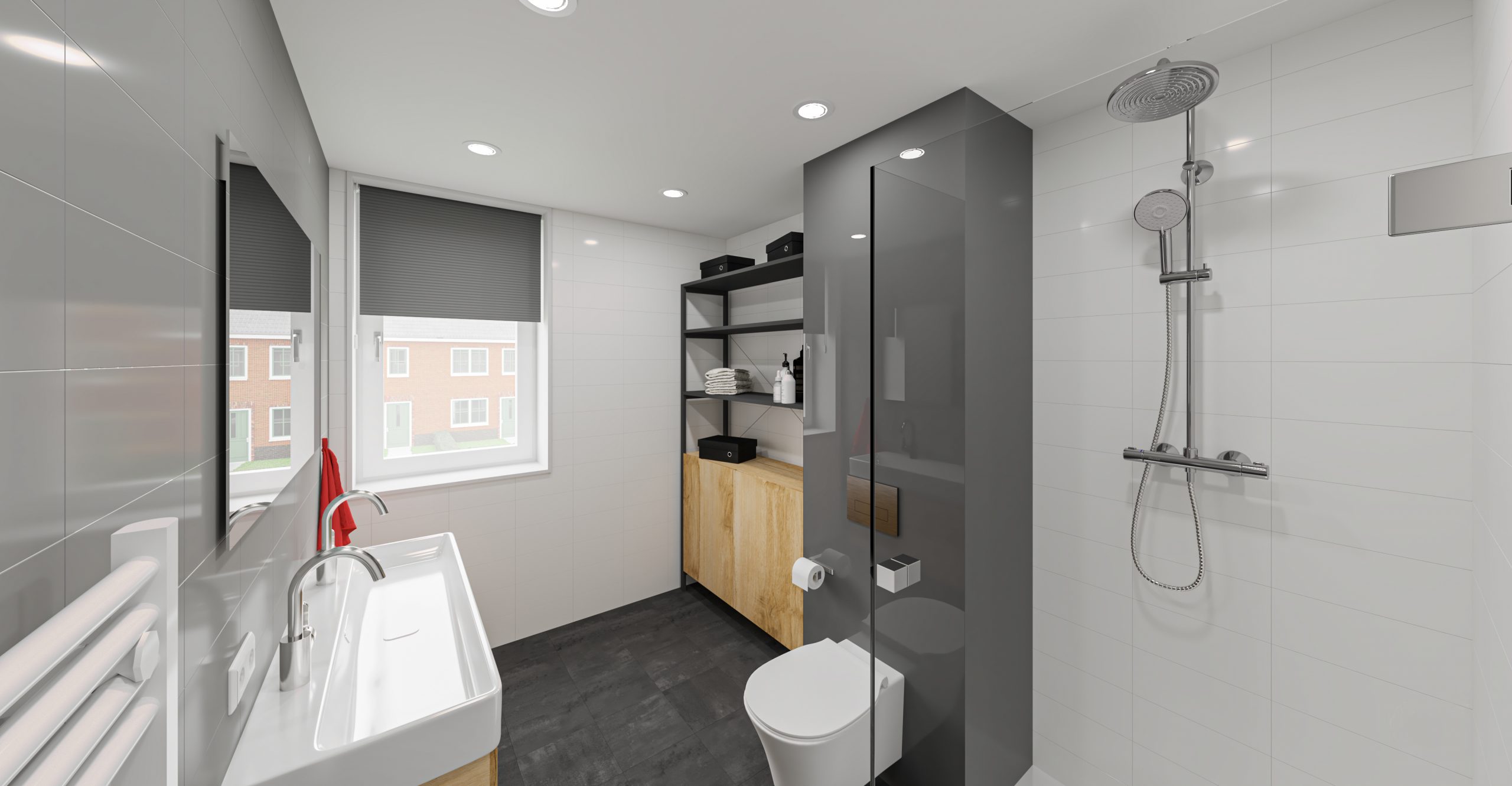
Growth opportunities galore
Nevertheless, experts see ample opportunities for rapid growth of biobased building materials. “It’s a market that will have to develop itself, but I definitely see opportunities,” said Pim Schaaper, product manager at pipeline manufacturer Pipelife. “The volumes available are limited, so you get a ‘chicken or the egg’ situation. The prices are high, which causes demand to stagnate. This, in turn, leads to less production, which means the prices aren’t going to drop.”
According to Schaaper, the main problem is that we have to get used to the whole idea. “Right now, lack of familiarity with the material is the biggest obstacle. As a result, people often think that biobased materials dissolve in the ground or in another environment. This is not true. Biobased means that the raw material of your product is obtained from a renewable source. Biodegradable materials dissolve in the natural environment without leaving microplastics or other harmful traces,” Schaaper explains. The beauty of this is that biobased materials work just as well as the fossil-based alternatives. They are just created in a more sustainable way.
Solution to the housing shortage
As such, the suitability of materials for the construction industry also seems to work as a solution to the current crisis in the housing market. “The PVC pipes that are in your wall, where the power cables also run through, well, you could also make them biobased, just to give a basic example.” This is a way that people can still make their homes just that bit more sustainable. Pretty handy now that it has been announced by the Dutch government that we have to pay for the CO2 that our homes emit, among other things.
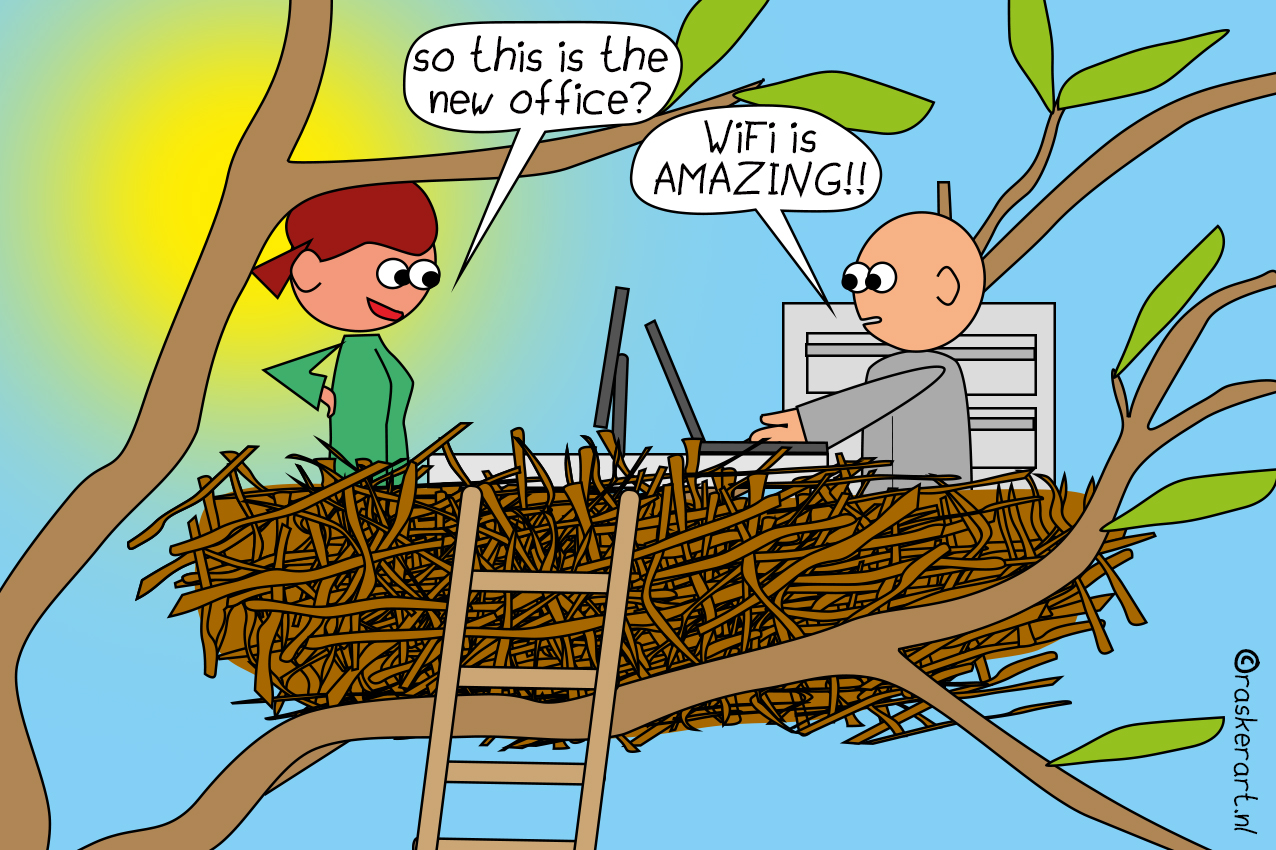
The housing construction task is still substantial, with one million more homes needing to be built before 2030. “By building these homes out of wood, it is estimated that these houses will be able to save a quarter of our annual emissions. Climate Cleanup and ASN Bank therefore see the housing construction task in the Netherlands as an interesting opportunity in the transition to a climate-positive society,” which was the conclusion drawn by the companies in a recent study.
Even more broadly applicable
However, the housing construction sector is not the only industry where there are numerous opportunities for biobased construction. A current example is the ‘organic highway‘. A case study by CBE, a company focused on sustainable innovation, shows that biobased alternatives are now available in fourteen components of a highway design. “The most obvious alternatives are wooden guardrails, biobased asphalt, noise barriers and road signs, and wooden bridges and viaducts. Over time, this could lead to as much as a 94 percent reduction in CO2 emissions.”
But the Dutch water sector is also making great strides towards a biobased future. Earlier this month, the first biobased pipeline was laid underground in Brabant. This water pipeline was made with deep-frying fat, but wood pulp or residues from sugar cane also work well as a basic raw material. Schaaper: “The net CO2 savings can be as high as ninety percent.”