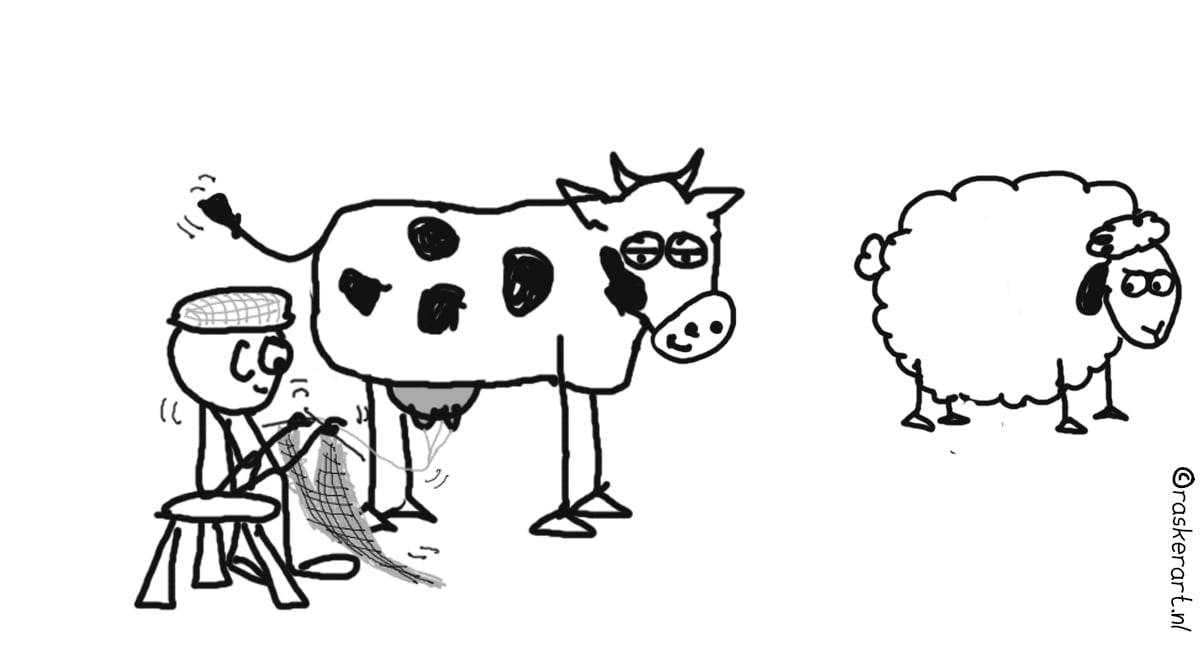
A shirt made from sour milk flakes doesn’t sound particularly appealing. Yet this is exactly what microbiologist and fashion designer Anke Domaske does. She developed a sustainable method to extract casein from milk flakes. In last week’s best read article, Domaske explains that the method is a bit like cooking. A special recipe using the flakes combines other ingredients such as beeswax, wheat bran and water to form a kind of dough. This is then run through a large pasta machine which has small holes, except textile fibers come out of the machine instead of pasta.
The technique of making textile fibers from milk protein is not new. According to Jantiene van Elk, librarian at the Textile Museum in Tilburg, this has been in use since the 1930s. “Normally I would refer you to a book,” Van Elk laughs over the phone. Then she explains: “It’s a semi-synthetic fiber and it’s used as a substitute for wool. Milk wool is much softer than normal wool. The milk protein is made into a long fiber via all sorts of steps and chemical pulps.”
What’s novel about Domaske’s ‘recipe’ is that no chemicals are used in the process. Also, the raw material that forms the basis for the textile is usually thrown away. Research carried out by the University of Berlin discovered that Germans collectively throw away about two million tons of milk a year. And the Dutch are also capable of dumping plenty as well. According to figures from Milieu Centraal (a Dutch environmental association), per person, the Dutch flushed about 10 liters of milk and dairy beverages down the drain in 2019. A real shame, as Domaske would have known what to do with all of that.
Cellulose pulp
But most fabrics are made of cellulose pulp according to Van Elk. “You have natural cellulose from plants – of which cotton is the most well known – and trees. The industry uses all kinds of wood chips for this. But you can also extract cellulose from bamboo. Then there’s synthetic cellulose from petroleum processing – all kinds of variants of this have been invented ever since the 1950s. But whether you use natural cellulose or synthetic pulp, the pulp only transforms into a textile fiber after all kinds of steps have been taken and and chemical pulps have been made.”
Can’t that be done more sustainably? Sure, what would you say about Jalila Essaidi? Who not only designed a very strong fiber that is based on spider silk, but also makes clothes out of cow manure. Or check out designer Billie van Katwijk with her bags made from cow stomachs. Both of these raw materials are generally seen as waste and are rarely if ever given a second lease of life.
The same goes for any surplus algae that is fished out of lakes or washed ashore on the beach. But designer Tjeerd Veenhoven has proven that you can make textile fibers from them too. He was awarded the Global Impact prize in 2015 – an incentive prize for circular innovation in the clothing industry. “Mother Nature has given us a very beautiful fiber with cotton,” says Veenhoven. “But the way we are using it right now, we need so incredibly much of it. That’s just not tenable anymore.”
Alternative to arable farmland
It all started in a large tub where Veenhoven allowed the algae to ferment. He dried them out and then treated them in a similar way to regular cellulose, i.e. with chemicals. “Yeah, I know. I wanted to find an alternative to cotton cultivation. Ever larger areas of land all over the world are being reserved for cotton crops. In order to maintain the harvest of these crops, plantation farmers use a lot of water as well as fertilizers and pesticides. You can find photos on the internet of lakes in China that have completely dried up over the past twenty years as a result of cotton farming. Cellulose does not necessarily have to come from the cotton plant. It can be found all over the world. Even in algae, so arable farmland could be used for something else.”
Algae fabrics
Nevertheless, despite the alternative Veenhoven has to offer, his ”algae fabrics” are not (yet) in production. It’s too expensive to extract cellulose from the algae. “At the moment the narrative is stronger than the business case. But I’m certainly not pessimistic. I’m not the only one working on this. More and more start-ups – who are much further ahead than I am – are coming up with more sustainable alternatives. They are also increasingly being taken over by the major brands, that really has an impact. Because the major brands are active throughout the entire chain.”
Nor has he given up yet. Because in order to be able to get rid of the chemicals that Veenhoven uses in the process, he is researching whether the cellulose can also be extracted from the algae in a natural way. “Enzymes have been found on Earth for millions of years. They dismantle systems in a natural way. Digestion works in the same way. It takes a while to figure it all out, because every system has its own enzymes.”
Natural breakdown of systems
The use of enzymes as opposed to chemicals has a number of other advantages. For example, you can use biological systems that are capable of breaking stuff down over and over again. Veenhoven: “All you have to do is keep the enzymes alive. But that’s not so difficult in principle. They do their job very well at room temperature. Unlike chemical processes that often require heat. So our method will be far more energy efficient.”
Veenhoven does think that it will be another five to ten years before the entire clothing industry has switched to more sustainable alternatives other than the cotton plant. “Many processes are now just below the point of implementation. It’s all about finding the right business case. There is also a growing demand from the industry and consumers are becoming increasingly aware of clothing. But change takes time.