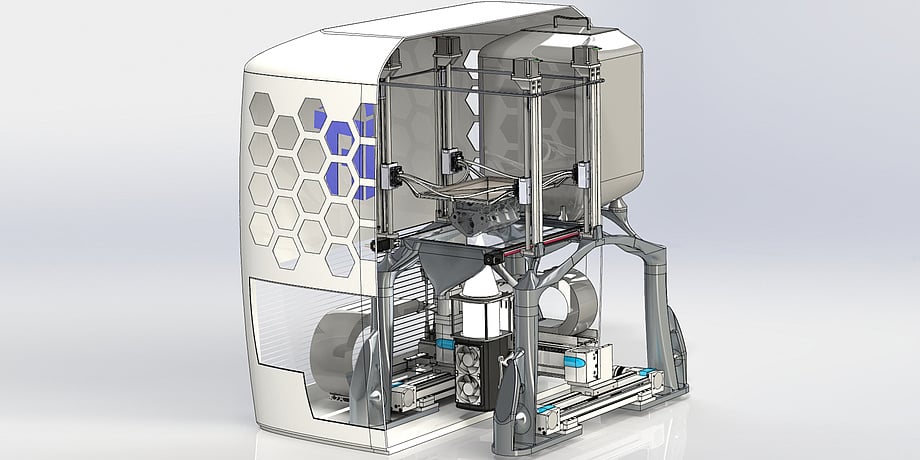
The Technical University of Graz (TU Graz, Austria) has designed a new type of 3D metal printer that utilizes LED light instead of a laser. The main advantage is that parts can be manufactured much faster. This means that the equipment can be used, for instance, during medical surgeries where metal parts are needed. The LED printer is more efficient when it comes to processing metal powder and requires less maintenance as well.
TU Graz announced that this week. The researchers call their patented invention “Selective LED-based Melting” (SLEDM). According to the project leader Franz Haas, the production process is comparable to other 3D printers. E.g., screws or bolts are built up layer by layer with molten metal. Thanks to SLEDM, however, it’s now possible to make larger parts (in particular) more quickly. In addition, the printer is designed in such a way that it is easier to eliminate irregularities or residual material, amongst other things.
Flexible lens
The higher rate of speed is primarily due to the light diode from the Austrian company Preworks used in the SLEDM system. They made a variable lens whereby the diameter of the LED focus can easily be adjusted between 0.05 and 20 millimeters during the smelting process.

This technology is combined with a new type of machine. And in contrast to other metal smelters, this adds the metal layers from the top to the bottom. The part is thus exposed to light, the required amount of powder is kept to a minimum and the requisite post-processing can be carried out during the printing process.
The first application for the machine is a project being carried out by the Medical University of Graz. This is where the very first medical 3D printing laboratory was opened back in October 2019. The printing process will be used there to fabricate metal implants. Ideally screws made of magnesium alloys for use in bone fractures.
Magnesium screws for bone fractures
These implants dissolve in the body after the fracture has fused together. A second operation, which is often very stressful for people, is subsequently no longer necessary. The production of these types of implants would be made directly right in the operating theater thanks to the SLEDM. This is because: “an LED light is naturally less dangerous in an operation than a powerful laser source,” Haas explains.
The second focus is on sustainable mobility, such as bipolar parts for fuel cells or battery systems.