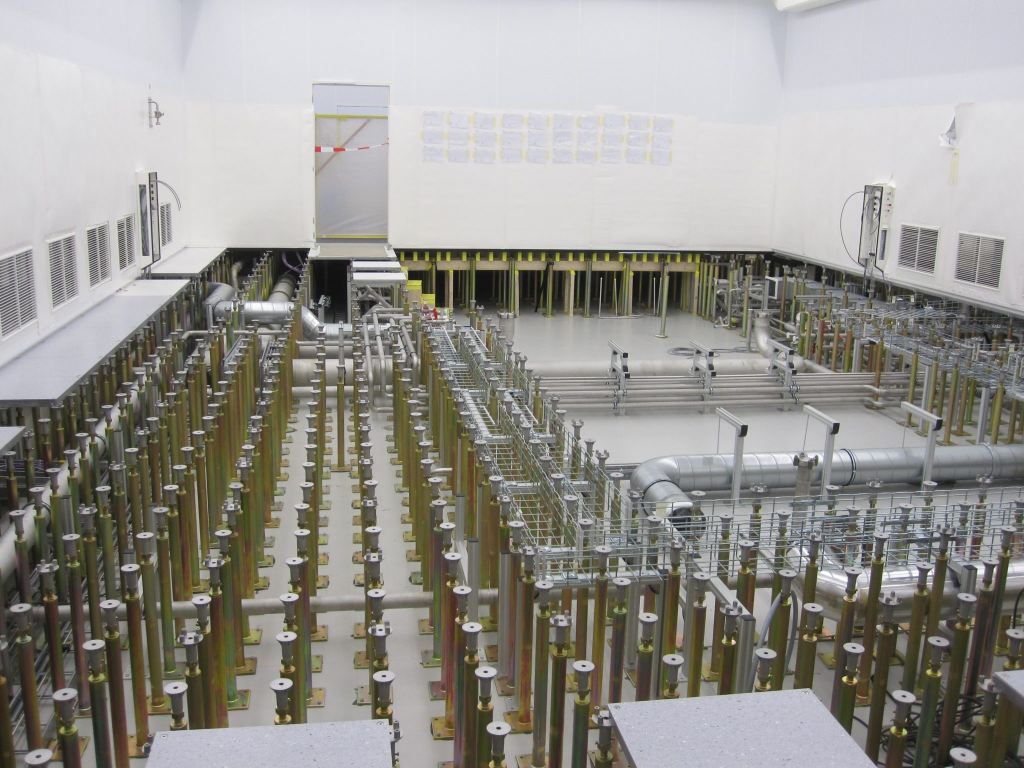
With 14,000 employees worldwide and an annual revenue of 6 billion Euros in 2014, the Veldhoven chip machine manufacturer, ASML, has grown so large that something special has happened there. But what exactly? You’d need a background in engineering as well as business to really understand it and, even then, part of the story will always remain hidden behind the walls of Tower 8 at De Run.
The tower is not actually where the “real” work took place. No, the heart of the organisation is where the research and the implementation come together, like the chambers and the atrium of the human heart. In ASML terms, where lab meets fab. In and above the cleanrooms, the lab and the factory are a whole. No outsiders are normally allowed in, and that’s not to be economical. It’s partly to ensure that the competition doesn’t become smarter than necessary, but also to keep the processes inside 100% dust-free.
And yet, on the odd occasion, the company accommodates a select group of visitors in this very spot. Not that all the secrets are revealed, on the contrary, every visible detail prompts more questions than answers for a visitor, but it does give the impression – literally – of the staggering developments to which ASML is now giving shape. e52 was able to go along and see how the latest chip machines are constructed, thread by thread, screw by screw, data part after data part, in this dust-free environment. They are the machines of the future because, even during construction, the developments continue to take place.
To enjoy a tour around the newest cleanroom, 5H, which officially opened in June, you have to conform to the company’s rules – and those of science. Cue seven journalists and their four guides in full bunnysuits. No cameras or notebooks. They’re the rules.
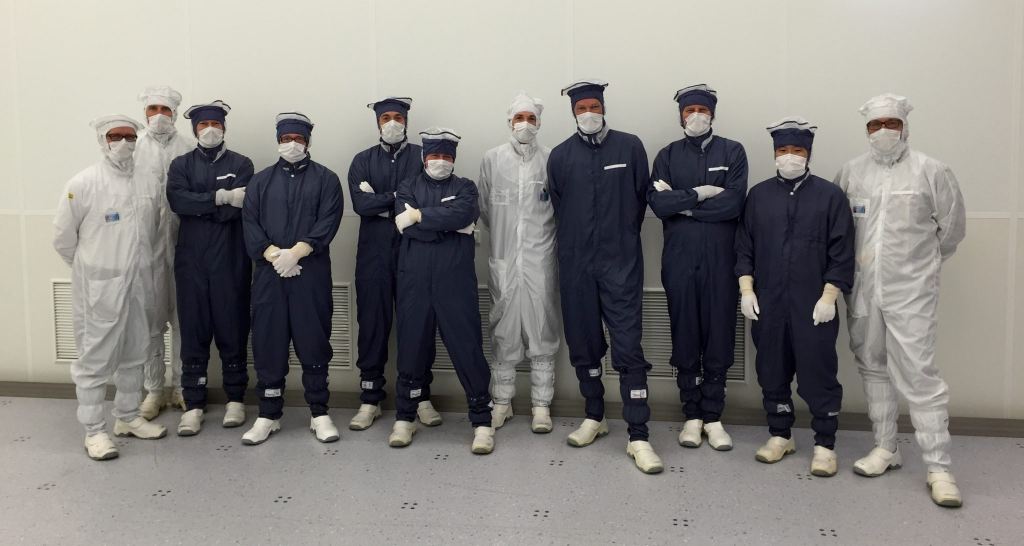
According to VP Facility Management Marc Peels, the most important idea behind lab-fab is that “our strategy brings lab and fab, research and production, as closely together as possible.” He explains that in almost 30 years, not only the size of the machines has increased (the PAS2500 from 1987 weighed 2500 kilos and could fit in a closet, the NXE from 2015 weighs almost 100,000 kilos and would just about fit on to a Boeing 747), but also the level of cleanliness has increased. Where it was once sufficient for employees to wear a hairnet and a dustcoat, they are no longer allowed in without a full body suit.
As well as the secrets kept from visitors, ASML requires unconditional mutual trust from its suppliers for the whole process of negotiation, definition and construction. Peels: “We came up with a formula: trust is knowledge x collaboration x flexibility divided by self-interest. Those who truly want to be trusted should be able to eliminate the self-interest. For this reason, we require our partners and suppliers to not only understand how it works, but to be collaborative and flexible as well.”
With the rate at which everything is changing, ASML can’t afford not to plan. “But the difference with us is that various planning stages run simultaneously instead of one after another. In this way, you can considerably reduce a traditional construction cycle that is usually about 5 to 7 years. What makes it even more complicated is that, together with our construction partners, we have to parallel plan and also remain open for future adjustments. There were 35 scope changes during the construction of our current factory as a result of innovations and technological advances alone.”
Before the machines could be put in place, ASML and its seven construction partners had to ensure that they could operate vibration-free in all circumstances, because even the slightest deviation would disrupt the chip manufacturing process. And so, 1500 piles, around 25 kilometres in total, were driven into the ground. Then came a steel network weighing in at three million kilos with 15,000 cubic metres of concrete and finished with a raised floor on top of about 20,000 piles.
Not only is the foundation solid, but the same can be said of the superstructure, where an Eiffel Tower of steel was incorporated, allowing the required offices to be built.
It might sound strange for a company that is living proof of Moore’s Law (every two years the number of transistors on one chip has doubled), but Peels says it’s important to ensure that what they have today can be achieved in the next twenty years. Step by step, ASML is working on the design. Walking through the newest cleanrooms we see the various machine assembly stages, from those no further than the rough structures of the basic machine, to the adjustments and fine-tuning. Each machine requires a few weeks to be built, but around a year and a half to be adjusted.
The huge processes (in terms of time and money) involved raise the question of why ASML would ever build the machines in their own factory first. They, after all, intended to be used by a client somewhere else on the globe. Peels: “There are two main reasons: we continue to incorporate developments during the construction of the machine. We want the client to benefit as much as possible and the final adjustments are so time-consuming that it would not only be inconvenient, but also extra-costly to do this on the client’s premises. In short, we can bring lab and fab together here on our own turf.”
The new factories are fully equipped to build the latest-generation chip machines: the third-generation NXE machine based on EUV lithography, ultraviolet light. The chips can then be ‘filled’ in even greater detail. Product Manager Rudy Peeters believes that there is a huge advantage to these machines: “They ensure that the lithography process can be completed in fewer steps, making it cheaper.”
But, according to Peeters, they are not yet fully developed. “Our goal for both this and next year is to increase the stability and availability of these machines, and so large and small improvements will be required. The good thing is that we do this together with the client. Whoever purchases this kind of machine, and the older generations too, for that matter, knows that they can get all the improvements installed.”
What applies to the machines also applies to the cleanroom in Veldhoven. Marc Peels: “At the end of construction, there’s a list of over 35 points for improvement. You might think, 35, that’s a lot, but when you consider that a new house has, on average, around 100 points for improvement, I think we have put in a great performance.”
All illustrations (c) ASML.