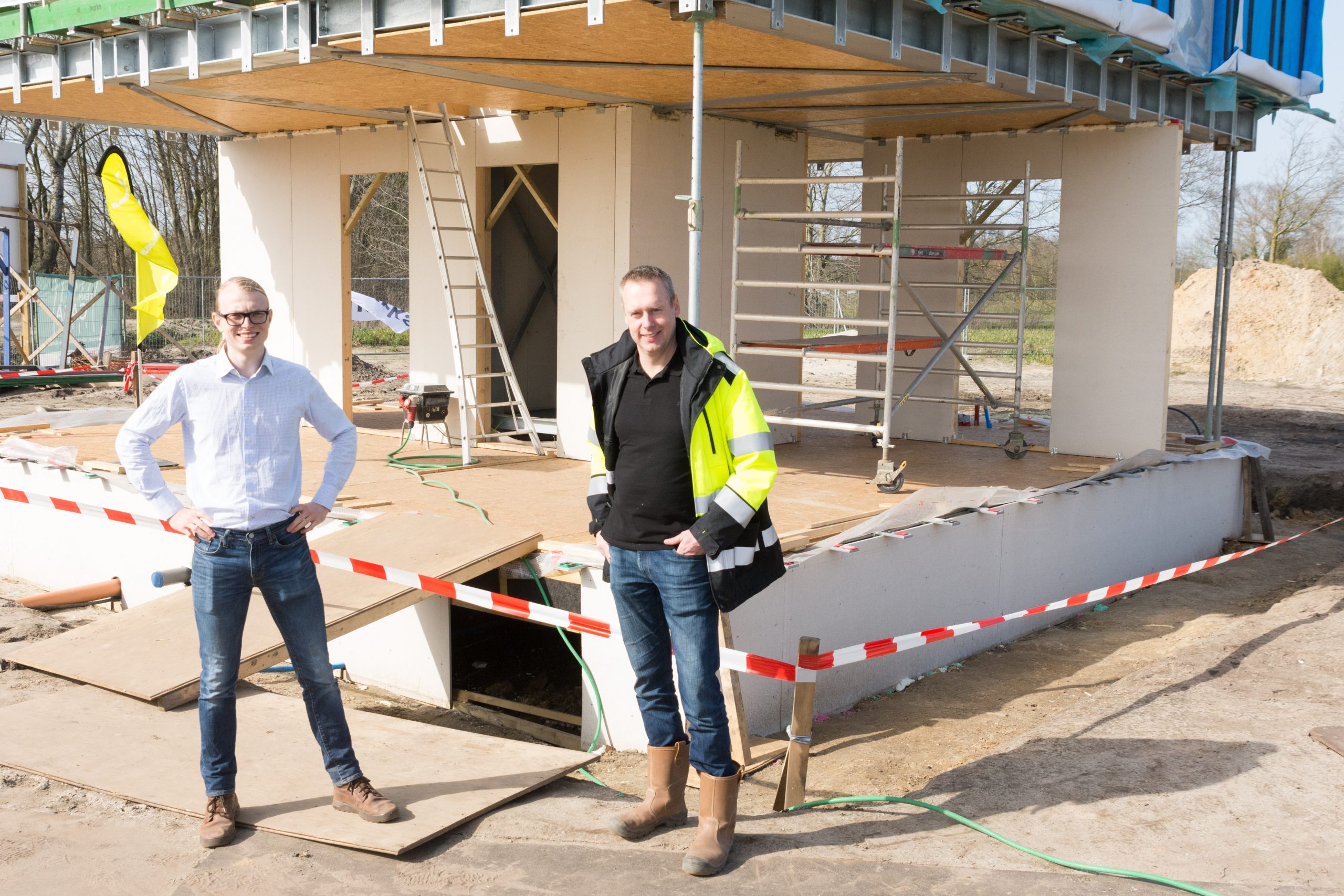
Five years ago, the plan was hatched to build a ‘Comfortable, Affordable, Sustainable Alternative‘ house. Students from the Eindhoven University of Technology (TU/e) started working on the plan as Team CASA. Gradually, a whole arsenal of companies from the Dutch Brainport region joined in to help integrate solar panels, a heat pump and seasonal storage tanks for heated water, among other things. The plans have almost become reality: Together with the Dutch housing corporation Woonbedrijf and the Hurks construction company, Team CASA is building three innovative social housing units in the Brainport Smart District in Helmond. Last week, construction reached its highest point and at the end of June, the first residents will be able to move into CASA 1.0.
Dream
For team leader Antoine Post, it feels quite bizarre to stand in front of his future home. “We have worked on this for so long. We spent so much time staring at the computer in order to design it. To see it now in real life is like a dream come true.”
The unique aspect of the three homes is how the energy systems are integrated, Post explains. “If you were to zero in on, let’s say, the roof with solar panels and underfloor heating piping, that’s nothing new. Except that we’ve integrated it with a seasonal storage system for heated water.”
When the students started out in 2016, they discovered that there are lots of companies developing innovative products for residential housing. “But what doesn’t seem to work well is connecting all the installations and systems together so that things work properly and efficiently. You can’t just sketch out exactly how everything lines up; you actually have to try it all out with one another. That takes time, but you do gain a lot in return.”
Insulated water tank
The solar panels generate electricity and heat. “You could store that heat underground, but then you’d have to turn on the heat pump in winter. That wouldn’t really make much difference.” That’s why Team CASA came up with a solution that uses a water tank. Electricity and hot water are supplied via the roof. That runs to the source side of the heat pump, where the water can reach up to about 75 degrees C. That water then goes to a well-insulated water tank located four meters under the house.
The tank was positioned underneath the house in just over a week, says Paul Claes project coordinator at Hurks. “The thing that was kept running here the longest was the water pump.” Brainport Smart District is in an area of arable land, with plenty of groundwater, Claes explains. “If you have to dig four meters deep, what with the groundwater level at about two meters, you first have to bring that groundwater level down to minus four.” That’s why the water pump was kept running for more than two weeks before any digging took place. Then came a hole where foils were put in place, followed by the framework. The foils were resealed after that and the earthworks laid over them. “And then you stick the hose in and fill it up with water.”
Energy-efficient
The combination also enables the heat pump to cool the floors in summer, says Post. “With the last two summers in mind, that’s no longer an excessive luxury.” And this system is very economical and energy-efficient, “because you don’t have to turn on the heat pump in winter.”
Read more about Team CASA here.
What is still clearly visible is, the ‘core’ of the house, the so-called service core. This houses everything needed for the technology of the roof to work with the seasonal storage system. “But also the ventilation system. and just about all the drains that are in there. It’s basically where everything happens.”
The beating heart
That core is not only “the heart” that keeps everything running, it also holds the house up. The facades and walls are not load-bearing ones; the floors are suspended from the core. That core is made of steel. Claes: “We thought that we would first make the steel structure in the zinc factory and then put it up in a day or two. On a diagram, everything looks perfectly even and sleek. But on the building site, it is all slightly crooked or even smaller. That’s why we decided to assemble the steel structure on the building site. The floor builders had to adapt to that.
The great thing about this project is that all the partners are open to it. People are really very proud of what they are making. It’s not what they usually do. You can see that in everyone, in the person who made the steel structure, but also among our carpenters.”
The three homes are built around the core. ” They must, above all, be pleasant to live in,” Post notes. So, no hindrance from the ventilation system or any other noise. The core is therefore properly insulated and can be closed off, “if you don’t have to be in there, you won’t be bothered by it,” Claes adds. Also, everything about the house is circular. It can be completely disassembled and rebuilt somewhere else.
List of suppliers
Claes notes that this project is quite different from other construction projects. “Team CASA immediately came up with a complete list of suppliers and subcontractors with whom they wanted to build the building. As a contractor, we don’t come across that very often. A customer often comes to us and asks: ‘Would you like to make this house or building for us?’ Then we make an offer and hit the market. But in this case, it was just the other way around.”
What also makes things different is that something new is always being tried out, Claes said. “After all, the construction world is set up pretty traditionally. We do try new things, but we often fall back on standard practices. Which is why we find something new quite exciting.”
Traditional division of roles
Construction company Hurks became involved in the project back in August 2017 because a student was eager to graduate with a degree focusing on innovation in construction, says Inge Schipper director of Hurks. It was through this student that Schipper came into contact with Post. Initially for some input of knowledge as well as sponsorship. Together with other entrepreneurs, Hurks was going to build CASA 1.0 under the leadership of Team CASA. However, it became clear during the entire development process that the traditional division of roles in the construction industry turned out to be an obstacle, Schipper recalls.
Which is why Hurks wanted to be more than just a partner. In consultation with Woonbedrijf and Brainport Smart District, the construction company decided to share in the responsibility for the risks involved. Hurks became the main contractor, “with due respect for the 25 partners who also sponsored part of the project.” A contract was drawn up between Woonbedrijf, Hurks and team CASA. In which Hurks and Woonbedrijf both bore part of the risks involved. “Because we feel that risk could not be taken on by Team CASA.”
Internet connection
The first residents can move into CASA 1.0 at the end of June. “That’s another special thing about this project. I’ve never worked so closely with a resident before,” says Claes. Post is not only the person who started the dream, worked on it, came up with the installation systems and brought parties together to make the dream a reality, he is also going to live in it, together with his girlfriend. “After July 3 is actually better, because my girlfriend has exams up until then. And it’s not yet certain that the Internet connection will be working by then,” Post jokes.
As a resident, Post will immediately experience what it is like to live in CASA 1.0. This is how he brings living and working closer together and actually gets to live in his dream home. “It’s actually the ultimate test of whether what we came up with actually works.”
Woonbedrijf rents out the studio on the second floor via Wooneasy, the system that links house hunters to housing. In this case, the matching is very specific. “We are looking for a resident who is motivated to live in such a sustainable home and who will share their experiences with us,” says Ingrid de Boer, director of Woonbedrijf, “By doing this, they will contribute to the sustainability of this region.” The studio offers a temporary contract for two years, so that a new resident also gets to gain and share experiences.
De Boer is expecting a lot of interest in the homes. That’s why Woonbedrijf keeps the top studio as a show room. That is temporary, “we will probably rent out that studio as well around the turn of the new year.”
Energy poverty
“It is also important to us to combine affordability with sustainability” says De Boer. “If you have plenty of money then that’s not all that difficult. Nowadays, you’re also talking about energy poverty, that people with a small budget should also be able to benefit from the latest techniques and the savings that come with that.” That’s why Woonbedrijf stays under €430 per month for the studios, so that people can still apply for a rent subsidy. The apartment has a rent of €620 per month.
“These homes are really a test case,” Post points out. “You want to make sure that the heating works before you start building 100 homes on this kind of system.” He certainly sees room for improvement in terms of making it more interesting for a housing cooperative. “The core is not being made pre-fab at this point; it’s made on the construction site and put together there.”
Gold mine
According to project coordinator Claes, this can also be done more efficiently: “If you can supply complete components in the near future, you will be so much faster in terms of construction speed without having to compromise on quality. Now you have to deal with wind and weather. If you condition it beforehand and assemble it right there on the work site, then you’re sitting on a gold mine.” Post: “And it would be great for social housing if you could make an installation system for six homes. We are going to develop that together with Hurks.”
CASA 1.0. was partly made possible by subsidies from the Metropolitan Region of Eindhoven, the Province of North Brabant and the Netherlands Enterprise Agency. As portfolio holder for Brainport Smart District, councillor Cathelijne Dortmans from the Municipality of Helmond is closely involved in the project. She emphasizes that everyone can learn from the knowledge and experiences that this housing will yield. “This house was created in this region using the existing ecosystem. But we are not going to keep it exclusive to this region. Everything we learn is accessible to the province, to the Netherlands and far beyond as well.”
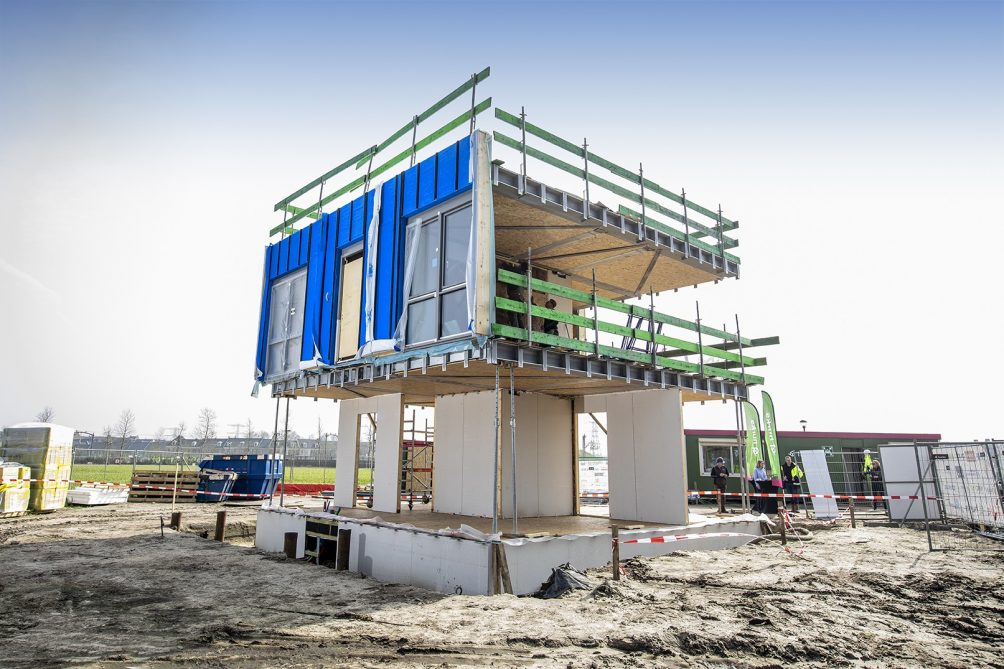