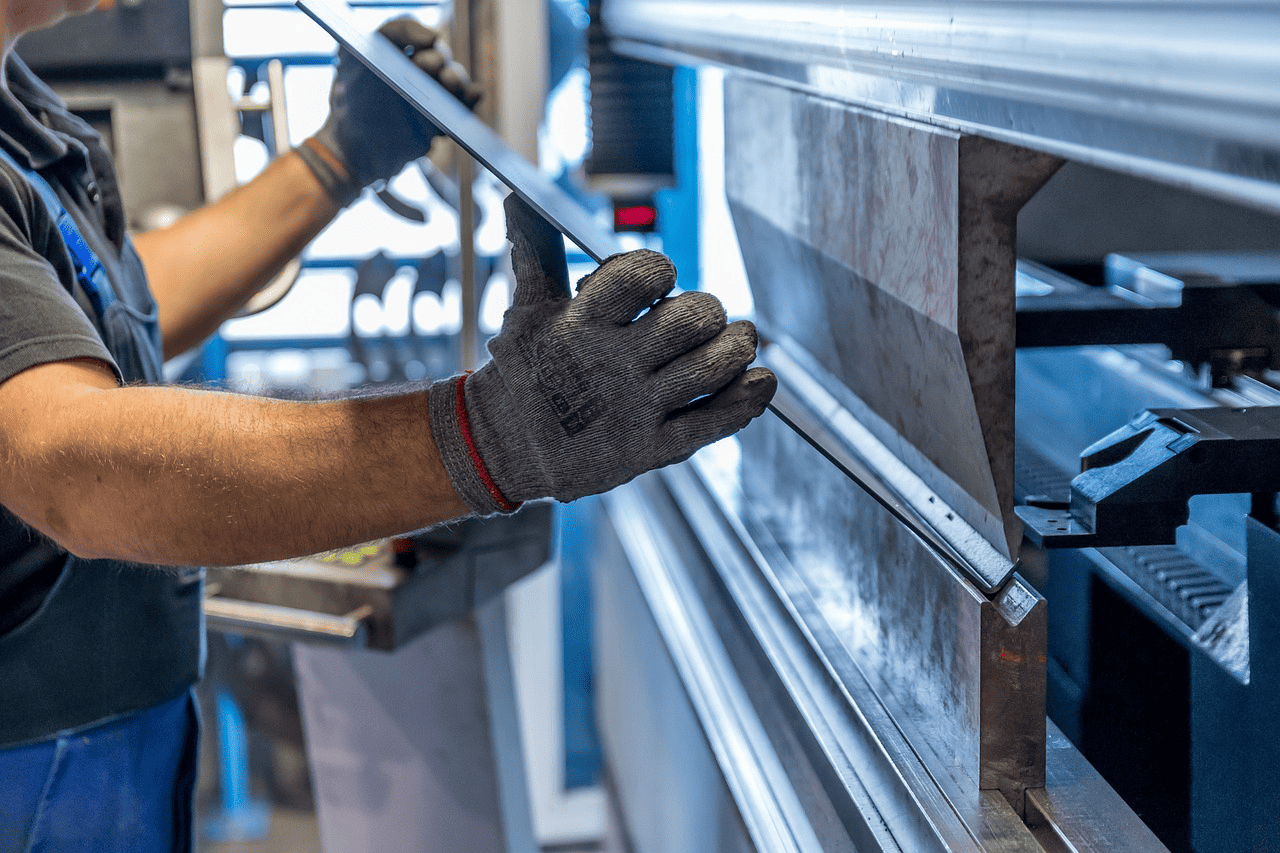
About AGMAH
- Founders: Arpit Aggarwal and Ishaan Mahashabde
- Founded in: 2021
- Employees: 3
- Money raised: Self-funded
- Ultimate goal: Becoming the go-to partner for any factory looking to implement industry 5.0 technologies.
The next industrial revolution is around the corner. Industry 5.0 is set to take manufacturing and production forward, with artificial intelligence (AI) stepping up to improve processes. AGMAH developed a toolbox that allows factory managers, engineers, and operators to collect data and set up operations to smoothen its introduction within production plants.
Located in TWICE’s Alpha building within the Eindhoven University of Technology campus, the company has recently launched its product after months of research – and tens of visits to factories. In this installment of the Start-up of the Day series AGMAH’s founders, Arpit Aggarwal and Ishaan Mahashabde, told IO more about their company.
What does AGMAH do?
Mahashbade: “We are an AI software company concentrating on industrial automation solutions to make factories smarter, reduce downtimes, and increase revenues. Through our platform, users can customize and deploy their preferred solutions.”
How did the idea come to be?
Mahashabde: “When COVID-19 hit, I returned to India to work for my family business, a pneumatic tools manufacturing company. Even though companies were allowed to produce at thirty or fifty percent of their capacity, it seemed like it wasn’t possible. At the same time, other factories around the world – being completely automated – managed to do so. I realized there was a huge gap.
Then, I spoke to my close friend and former university colleague Arpit about creating a simple factory automation solution. That’s how our journey began, and we worked to develop a solution that immediately impacts factories.”
How does your solution work?
Mahashabde: “The core of our system is the ‘Smart Supervisor,’ an AI-powered supervisory platform. Through it, users can design processes without the need for software coding skills and remotely control their machinery and robots. Then, there’s our proprietary hardware device, the ‘Smart Node’. It can be retrofitted into any machine without changing its existing programming, running the processes designed through the supervisory tool. These nodes also allow the establishment of a mesh network that connects all the machines. We also offer a digital twin tool, which aids in designing the processes and assures they are performed as planned.”
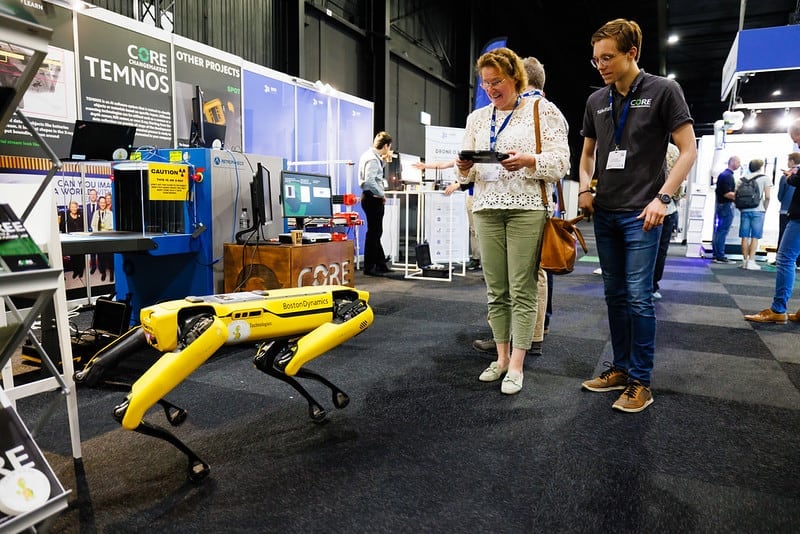
One of your goals is to make smart factories smarter. What’s the gap there?
Aggarwal: “The whole point of Industry 4.0 is making industry data-driven and capturing as much data as possible. When Industry 4.0 came into play, almost all factories started looking into robotics and tools to reduce their workforce and fully automate their plants. In many cases, companies have machinery from different vendors, which don’t talk to each other nor share data. The whole purpose of Industry 4.0 was to remove labor and improve production efficiency. In turn, what happened is that labor increased. Automation should’ve taken into account how a certain number of employees are indispensable to carry out processes.
That’s where we come in, trying to connect these dots and fostering human-centric automation. It allows factory engineers and managers to plan their staff’s working schedules considering what will happen on the production line – as it connects data from each machine – and people’s expertise.”
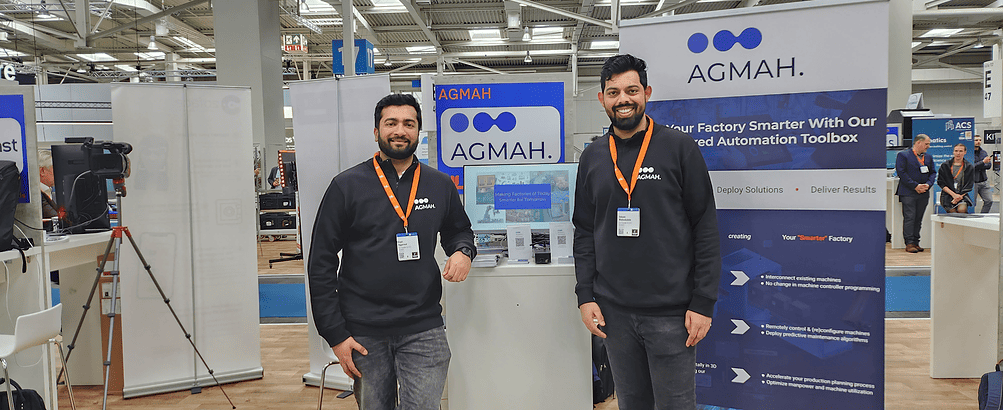
What industry sectors are you targeting?
Mahashabde: “Since we launched our ecosystem last April during the 2023 edition of the Hannover Messe – one of the main industry fairs – we ‘ve attracted the interest of fast-moving consumer goods (FMCG) and automotive companies. Besides them, the Eindhoven region’s food industry and circular manufacturing, too, have shown particular interest in our offerings.”
Aggarwal: “At the moment, we are working on two pilots. The first one is already ongoing in an automotive component manufacturer plant. The second one is in the pipeline and will be conducted at an FMCG production facility.”
How does the implementation of your system take place?
Aggarwal: “The first step is acquiring machine information from the factory engineers. Then, we look at their whole process, understanding where and how to set up our nodes to optimize their performance. After that, we install the nodes, testing them in-loop with the machines on the factory shop floor.
Once we’re satisfied with the setting, the system can work as a plug-and-play one, and it takes roughly a day to have the whole system up and running. Given that we are still in the early stages of our company, we are heavily involved in this part of the process. Ideally, we’d like to detach ourselves more and let the toolbox be mature enough to be set up by the factory engineers themselves.”
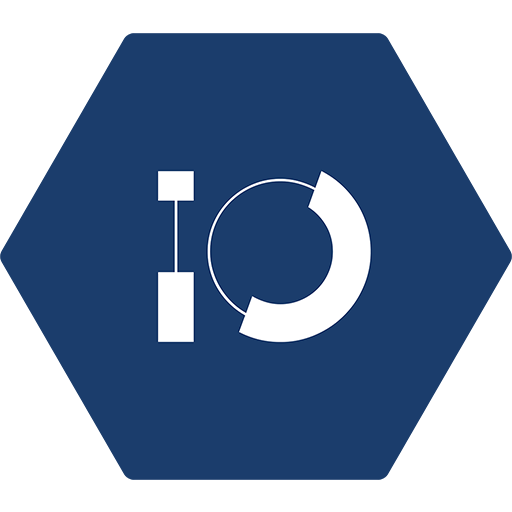
How do you showcase your technology?
Mahashabde: “We are launching a demo room – at AGMAH’s office location – in the second week of July. There, we want to showcase to factory engineers how our solution works. This way, they can see with their eyes what it’s capable of. A mini manufacturing and packaging
line will allow the user to interact with the ecosystem, seeing the added value it can bring to production lines.”
What sets you apart from other companies?
Aggarwal: “We try to bring engineering back to factory engineers. Our goal is not to let factory engineers act as supervisors but to give them tools to get their hands dirty, and control processes more. Furthermore, we offer a low-cost solution that can be taken into the current operating expenditures (OpEx) and not require additional capital expenditure (CapEx) budgets.”