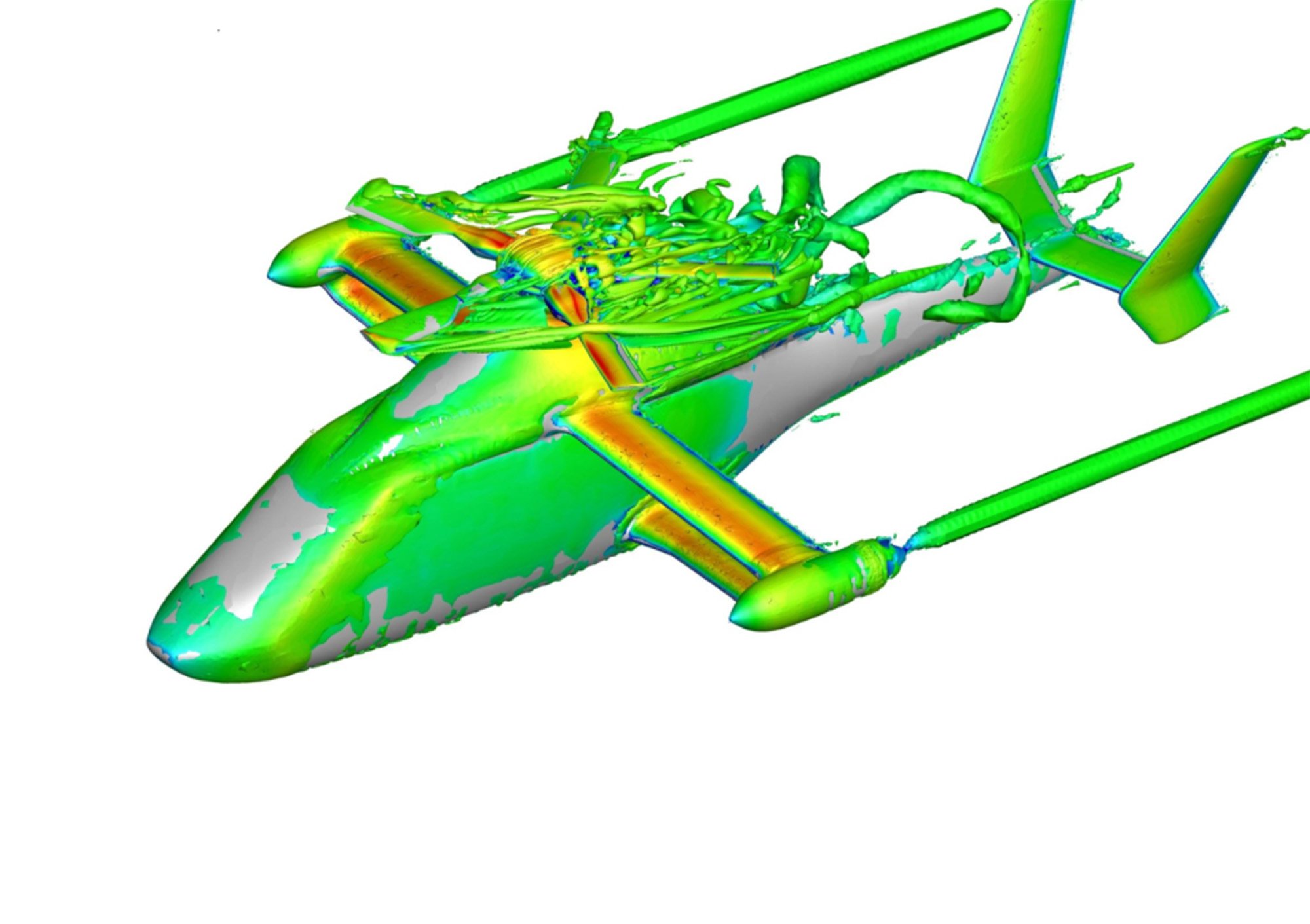
Vertical take-off and landing helicopters are indispensable in places that cannot be reached by road and where no runways are available for aircraft. This is the case in mountain rescue operations, on oil platforms, for medical care in remote areas or after accidents. In such instances, helicopters are usually used, but unlike airplanes, they not only consume more energy but are also able to reach only lower speeds in forward flight. This is because the rotor generates high air resistance in flight. However, the helicopter needs the rotor to take off vertically and maintain a stable position in the air.
With the Airbus demonstrator RACER (Rapid And Cost-Effective Rotorcraft), an international team of scientists now wants to develop an aircraft that can reach a speed of 400 kilometers per hour in forward flight and is at the same time quieter and more environmentally friendly than conventional helicopters. Thatโs why the RACER not only has a rotor, but also wings like an airplane. This allows it to generate lift in an aerodynamically efficient manner and reduces the load on the rotor.
Saving energy through optimal rotor shape
At a flight speed of 400 km/hour, the helicopterโs aerodynamics are essential. Thatโs why researchers at the Technical University of Munich (TUM) have joined forces with Airbus Helicopters (AH) in the FURADO (Full Fairing Rotor Head Aerodynamic Design Optimization) project to develop an aerodynamic fairing or covering for the rotor head. โThe components that cause the most drag in helicopters during cruise flight are the fuselage and the rotor head,โ says Patrick Pรถlzlbauer, a research associate at the Chair of Aerodynamics and Fluid Mechanics.
Geometries have already been developed for the fuselage that cause as little drag as possible. However, since the aerodynamics of the rotor are very complex, an aerodynamically optimized full fairing for the rotor head is a greater challenge. That is because the rotational motion of the rotor leads to a permanent change in the inflow conditions at the rotor blade. This gives rise to both so-called attached flow, which follows the contour of the object โ as is the case, for example, on a wing in cruise flight โ and so-called detached flow, which has a particularly high drag, the researchers explain.
โDetached flow occurs when, for example, the contour of the body is cut off with an edge, as in the case of a blunt vehicle tail on a car,โ says TUM professor Christian Breitsamter. โThen the flow detaches and there is turbulence. This leads, for example, to dirt particles landing on the tail.โ Such blunt edges also exist in the rotor head area at the interface with the rotor blades.
Novel aerodynamic rotor head fairing
The researchers perform simulations of such complex aerodynamic processes using advanced software and computational methods. However, they do not rely on technology alone. โThere are many setting variables in flow simulation, and these must be chosen correctly to get a reliable result. This requires both expertise and experience,โ says Breitsamter.
Patrick Pรถlzlbauer was able to design the shape of the rotor head in such a way that only small turbulences occur, as the flow remains attached there for as long as possible. He has also developed an โoptimization chain for the aerodynamic design of geometriesโ that can theoretically be applied to the development of fairings for other rotor models.
โThe plan is to manufacture the developed rotor head fairings and test them on the flight demonstrator,โ Pรถlzlbauer explains. These first flight tests of the RACER will show whether reality and results from the simulator match up.
Cover photo: Visualization of the turbulent structures in the vicinity of the rotor head. ยฉ TUM
Also of interest:
Variable rotational speed to make helicopter gearbox eco-efficient
Sensors guide aircraft through turbulence without vibration
Urban Air Mobility: City traffic in three dimensions