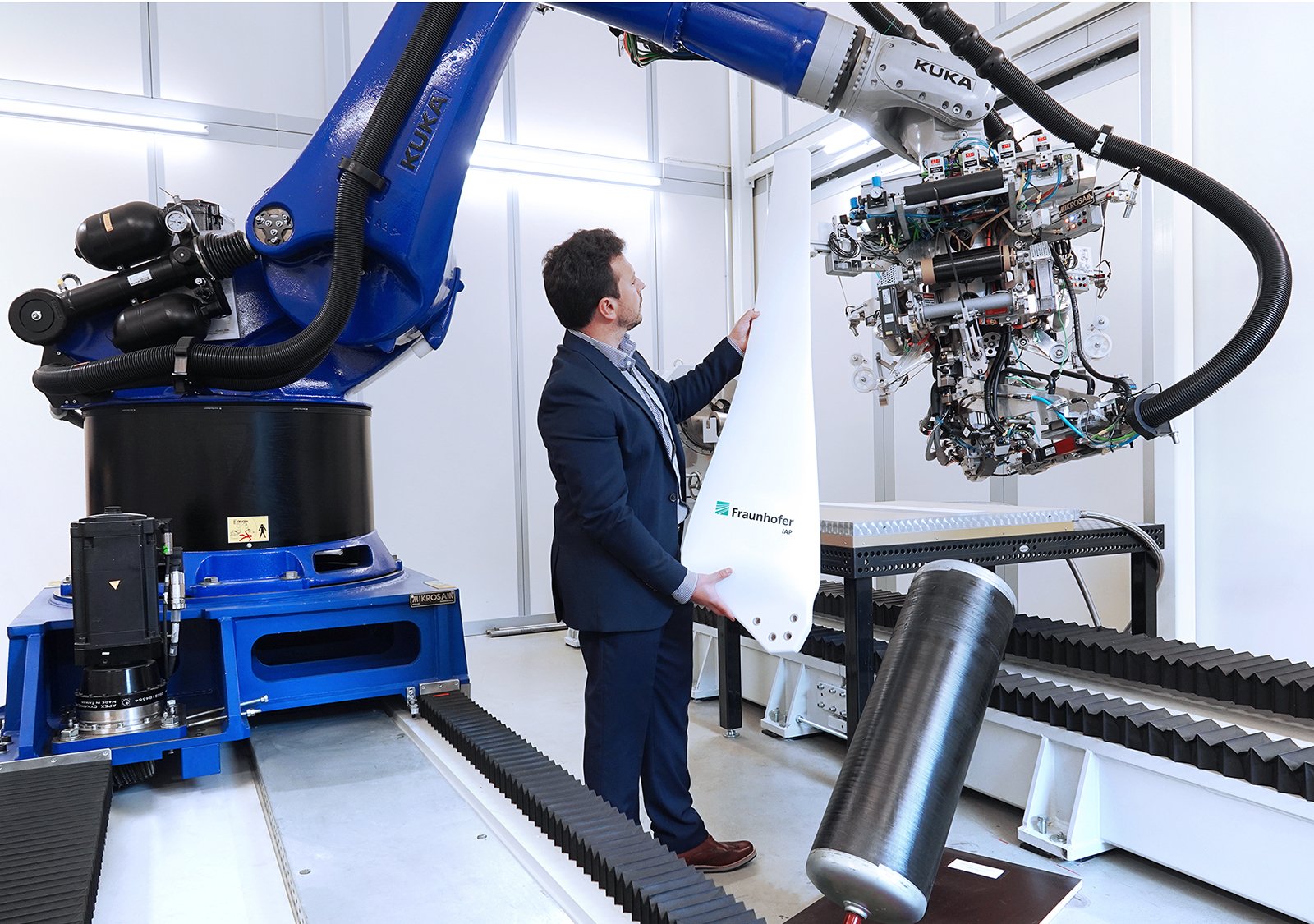
According to figures from the Federal Environment Agency, private households use around 25 percent of all the energy consumed in Germany. And almost half of this energy is still generated from fossil fuels such as oil and natural gas. Renewable energy sources continue to play a minor role โ despite ongoing climate change.
โHere, hydrogen obtained from renewable energy sources will be much more suitable as an energy carrier in the future,โ explains Prof. Holger Seidlitz, a lightweight construction specialist at BTU Cottbus-Senftenberg and head of the Polymer Materials and Composites PYCO research area at the Fraunhofer Institute for Applied Polymer Research IAP in Wildau, Germany. He and his team are currently developing a small, efficient wind turbine and a novel hydrogen tank made of fiber composites.
Your own hydrogen for home and car
โThe wind turbine will be designed to be so small that even private individuals can put one in their backyard,โ Seidlitz emphasizes. โThe hydrogen will then be produced on-site in a small electrolyzer and stored in a tank.โ This hydrogen can then be used to produce heat and electricity in the home by means of a fuel cell. In addition, anyone who owns a hydrogen car could refuel at home. Seidlitz believes the biggest advantage of the system is that it is small and at the same time very efficient.
For example, the wind turbineโs propeller turns and produces energy even when there is little wind. โHere in Lusatia, the wind blows much weaker than in northern Germany,โ says mechanical engineer Marcello Ambrosio, who is overseeing the project at Fraunhofer IAP. โWe have adapted the design of the rotor blades to this and reduced their mass by about 30 percent compared to conventional small wind turbines.โ It is made from fiber composites using an industrial 3D printer at Fraunhofer IAP that can print objects up to two by two meters.
Lightweight, agile rotors
Fiber composites consist of fiber strips that are placed in a mold. They are then hardened into a component with the help of resin or other plastics. At the Fraunhofer IAP, the assembly process is no longer done by hand but with a modern automated fiber placement system. It precisely places the reinforcing fibers in the mold. โUnlike assembling by hand, there is less overlap here so we can significantly reduce the dimensions,โ Ambrosio says.
A big plus of the rotor is that it not only rotates in low winds but can withstand high winds as well. This is because the rotor blades are elastic enough to bend and turn out of the wind during storms. โThis means that the turbine throttles back its rotation speed on its own without suffering any damage,โ says Holger Seidlitz. Complicated control technology is thus just as superfluous as complex mechanics. Initial tests of the rotors in the field are to take place in the coming months.
A tank with built-in safety sensors
Like the rotor, the hydrogen tank is made of lightweight carbon fiber composites and is therefore significantly lighter than conventional steel tanks. To ensure the necessary safety, the tanks are made of carbon fiber strips that are wound onto a cylindrical body. These are then infused with synthetic resin, which hardens them into a stable tank that can withstand hundreds of bars of pressure. This prevents hydrogen from escaping, which could otherwise form an explosive mixture when combined with atmospheric oxygen.
โCurrently, we are working with 3D printers that can process electrically conductive inks,โ explains Marcello Ambrosio. These would be integrated directly into the fiber composite, enabling the researchers to also incorporate small electronic components into the tank wall. This creates an early warning system, an important prerequisite for future safe use by end customers.
Cover photo: Novel low-wind rotors and hydrogen tanks with built-in safety sensors could make small wind turbines for private use possible in low-wind regions such as Lusatia, Germany. ยฉ Fraunhofer IAP
More articles on hydrogen can be found here.