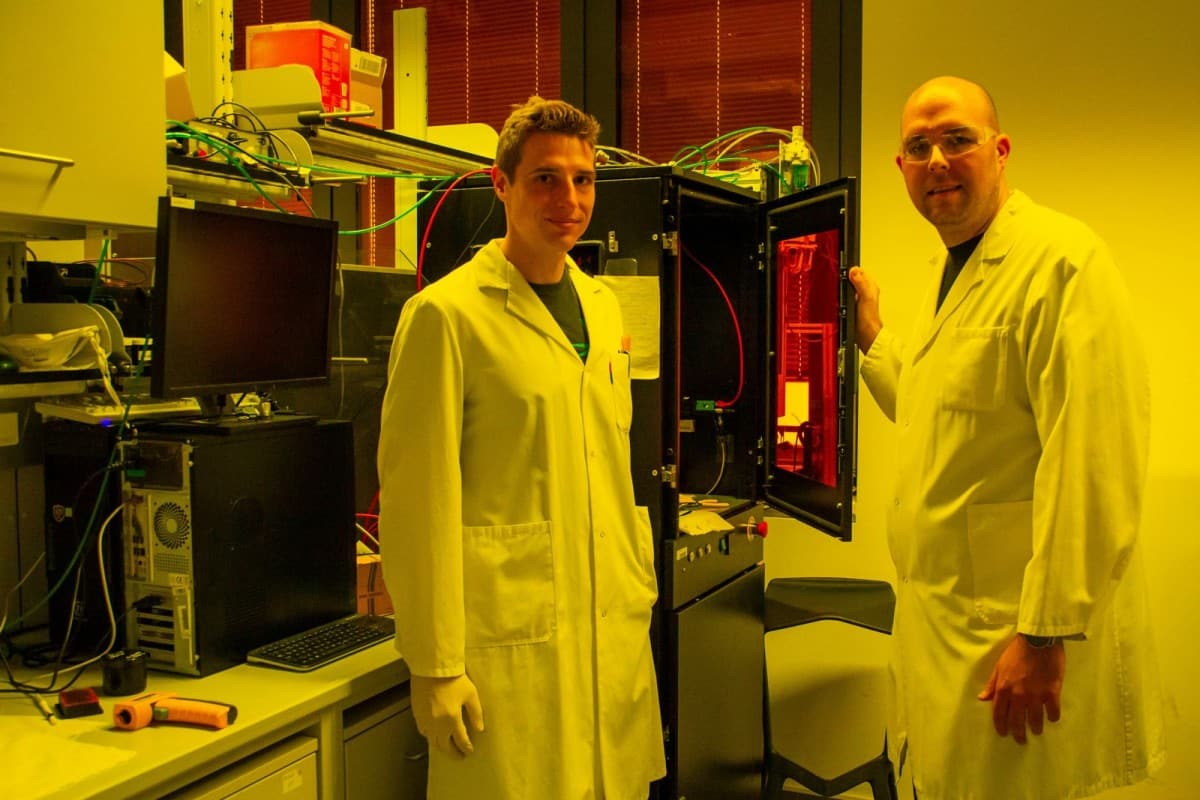
Stefan Baudis aims to enable the natural regeneration of damaged bone with a bone substitute from a 3D printer. This should be organically constructed and biodegradable and should therefore not be a foreign body.
Healthy bones are capable of remarkable regeneration. Certain cells are constantly busy dismantling and rebuilding these. This is why bone fractures are able to heal by themselves, explains Stefan Baudis Stefan Baudis from the Department of Macromolecular Chemistry at the Institute for Applied Synthetic Chemistry at TU Vienna. If the bone is seriously damaged through an accident or a tumour or an infection, there are often limits to how the bone can be repaired. Affected patients need a bone replacement in order to avoid amputation.
Individualized bone substitution
3D printing is an ideal instrument for bone replacement. Fused filament fabrication is a widely used procedure. Thermoplastics are melted, deposited into ultra-thin filaments and built up layer by layer into structures. Approaches for patient-specific implants already exist for the face, jaw and skull. Baudis knows that some of these are already being used in clinics. Yet they are still foreign bodies.
Completely degradable
Baudis is pursuing a radically different approach: a bone substitute which is biodegradable. He wants to provide the body with a suitable skeleton from the 3D printer, which can be colonised by the body’s own cells and converted into normal bone by these cells. With the establishment of a new Christian Doppler Research Laboratory (CDL), he can now move on from basic research to practical application. CDL is a funding initiative that encourages cooperation with business partners. The laboratory is called Advanced Polymers for Biomaterials and 3D Printing, and was opened on June 25.
Modern imaging computer procedures enable the precise measurement of a damaged piece of bone. The exact bone section required can be determined and produced within a few hours using 3D printing and subsequently attached to the bone, Baudis says.
Complex specifications
What sounds simple is a major challenge from the perspective of materials science. The artificially created bone sustitute must meet complex specifications:
- The cells that are responsible for the natural degradation and formation of bone are supplied by their own blood vessels that pass through the bone. To enable this process in 3D printing material also, it must have a porous structure. This is the only way that the cells are able to penetrate and discover a functional material transportation.
- The material must be solid, although not too brittle so that it does not immediately break.
- The material must be degradable within a reasonable period of time. If this has been replaced by the natural bone, no part of the structure should remain.
- Particles of calcium phosphate which have already been incorporated into the material, are then converted into natural bone material.
3D printing specifications
Last but not least, the material must be suitable for 3D printing. It must remain liquid at room temperature until it is irradiated with light at the appropriate wavelength. This triggers a chemical chain reaction that hardens the material at the irradiated points.
Baudis explains: “We already know a lot about the chemistry of the individual components that are needed for this. Now we are researching the right material compounds in order to meet all of these requirements.”
In addition to the material compound, 3D printing technology will also be further developed. The team can fall back on a lot of knowledge and experience gained at the TU Vienna. Several research groups are involved.
Photopolymer-based systems
The team concentrates on photopolymer-based systems within the material compound. Photopolymers are formed within a few seconds by exposing special light-sensitive resins. This means that the liquid compound becomes solid when exposed to light. 3D printing is made possible by the layer-by-layer exposure of these resins with stereolithography.
Material properties which are very similar to bone can be produced by combining various monomers, additives and fillers. The monomers are selected to produce biodegradable polymers. The porosity of the bone structure and the external form are carefully managed in CAD planning and adapted to the patient’s situation.
The Christian Doppler Laboratory
The funding initiative stemming from the Austrian mathematician and physicist of the same name, Christian Doppler Research Association, enables outstanding scientists to carry out basic practical research in cooperation with innovative businesses. The financing is provided by the participating companies and the public sector. In this case, the sponsor is the Federal Ministry for Digilization and Business Centers (BMDW). Business partners are KLS Martin, Lithoz and TCC.
Also interesting:
VIVATOP: How VR and 3D Models Make Surgery Easier
3D Printing of Implants: Kumovis wins Munich Business Plan Competition