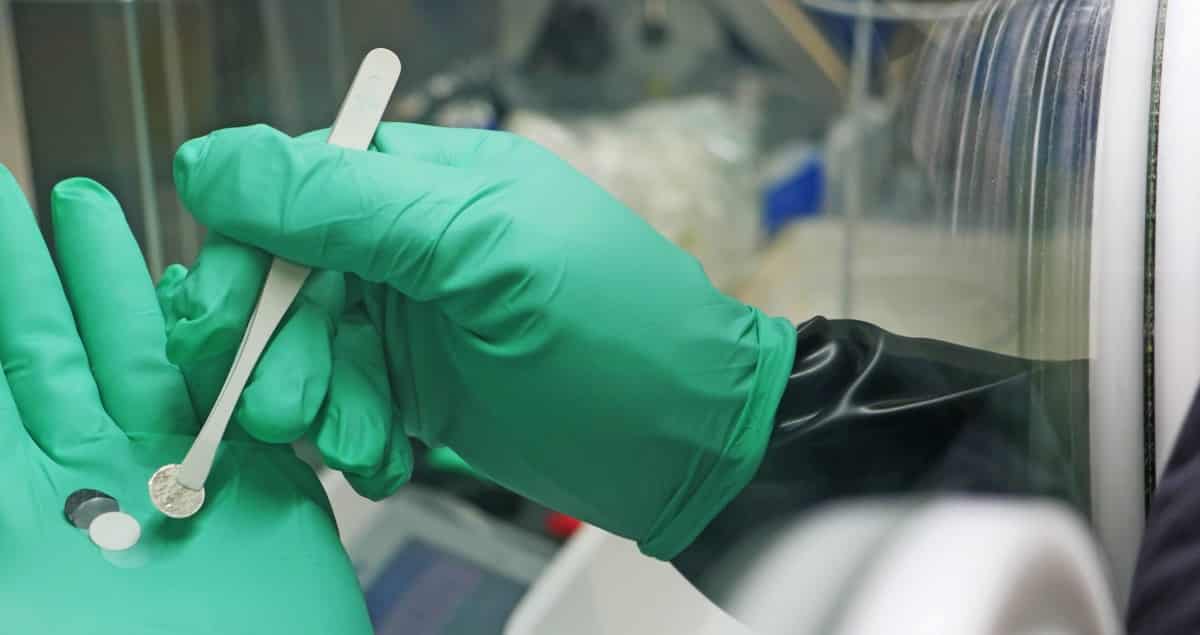
Scientists of the Research Centre Jülich and the Westphalian Wilhelms University Münster developed a new solid-state battery. Its speciality: It has an anode made of pure lithium. The alkali metal is regarded as the ideal electrode material because it achieves the highest energy densities. But since the metal is very reactive, it has not yet been used as an anode. The researchers, however, tricked this property by using two additional layers of a novel polymer. These layers protect the ceramic electrolyte of the battery and thus prevent the metal from being deposited in a destructive way. In laboratory tests, hundreds of charging cycles were possible without the cells significantly losing capacity.
Significant future expected
Solid batteries are regarded as an important development for the future. Their particular advantage is that solid-state batteries do not contain any liquids that could leak or catch fire. For this reason, they are significantly safer, more reliable and more durable than current lithium-ion batteries with liquid electrolyte. At the same time, solid-state batteries have the potential to store more energy in the same space with less weight. Accordingly, it is expected that this technology could help various areas to achieve a breakthrough. Possible application scenarios include electromobility, but niche applications in medical and space technology are also conceivable.
“The aim was to expand our concept for a solid-state battery in such a way that a stable operation with a lithium anode is possible, and we have achieved this,” says Dr. Hermann Tempel from the Jülich Institute for Energy and Climate Research (IEK-9), pleased with the current results. Lithium as an anode is considered the material of choice when it comes to achieving the highest possible energy densities. Because the lightest metal is also the most electronegative of all chemical elements.
The new solid-state battery has an energy density of 460 Wh/kg for both electrodes. In comparison with current lithium-ion batteries, this is a very good value. In addition, there are further advantages to the design. Solid-state batteries are significantly less temperature-sensitive than conventional lithium-ion batteries with liquid electrolyte. This means that they do not require any temperature management devices, such as those previously used in electric cars, which should save additional weight.
Polymer film as a protective layer

The use of an anode made of pure lithium was made possible by installing a polymer film between the anode and the electrolyte. Pure lithium tends to form uncontrolled excesses when charging. These so-called dendrites can short-circuit the cell or mechanically destroy it. In the anode of today’s lithium-ion batteries, lithium atoms are therefore stored in a storage medium, usually graphite. This increases the weight of the electrode and the entire battery many times over.
“The polymer functions like a protective layer that makes the use of a lithium anode possible in the first place,” explains Tempel. “It prevents the ceramic electrolyte from coming into direct contact with the metallic lithium at the anode. This prevents harmful processes such as dendrite formation and chemical changes in the ceramic electrolyte that impair the function of the battery.” Initial tests in the laboratory have already been successful. Over 500 charging and discharging cycles, while hardly any loss of performance could be detected.
“The special thing about the cell is that it functions despite the moderately conductive polymers; in some respects even better than without,” states Professor Hans-Dieter Wiemhöfer of the Helmholtz Institute Münster (HI MS), who developed the special polymer, which belongs to the class of polyphosphazenes. Wiemhöfer coordinates the BMBF joint project MEET-HiEnD II, from which the new battery emerged.
The polymer layer is applied as a liquid during production. It penetrates deeply into the porous ceramic electrolyte. This improves the contact between the solid electrolyte and the solid electrode – a common problem with solid-state batteries. This process does not require a stable and heavy housing to mechanically compress the various components and ensure a good connection. This also saves weight and helps to increase the energy density.
Double energy density but longer charging time
However, as an additional barrier between the individual components, the polymer layers also have a negative effect on the performance of the battery, especially on the current flow. Last year, Jülich scientists presented a well-functioning, fast-charging solid-state battery that can be charged and discharged within half an hour. Using lithium anode and hybrid electrolyte, they have now succeeded in doubling the theoretical energy density. However, the charging time has now been extended to two hours. This is still a good value for solid-state batteries.
The battery is still in an early development stage and is only ready for practice to a limited extent. For example, the cell must currently be kept at a minimum temperature of 50 degrees Celsius during operation so that the hybrid electrolyte remains permeable to charge carriers. “For low-price applications, the manufacturing process is still too costly. However, the functioning cell shows that the hybrid electrolyte makes it possible to circumvent typical problems at the interfaces of solid-state batteries,” explains Professor Rüdiger-A. Eichel, head of the institute at Forschungszentrum Jülich (IEK-9). The inherently safe battery with its high energy density may already be of interest for niche applications in which costs do not play such a major role. “But the approach also has great potential for cost-critical applications such as electric mobility.”
The research work was developed in the BMBF joint project MEET-HiEnD II, in which the Westfälische Wilhelms-Universität Münster, the Forschungszentrum Jülich and the RWTH Aachen collaborate. The original publication was published in issue 8/2019 in Journal of Materials Chemistry A.
Main image: The components of the lithium solid-state battery with hybrid electrolyte still in the laboratory stage ©Forschungszentrum Jülich / T.Schlößer