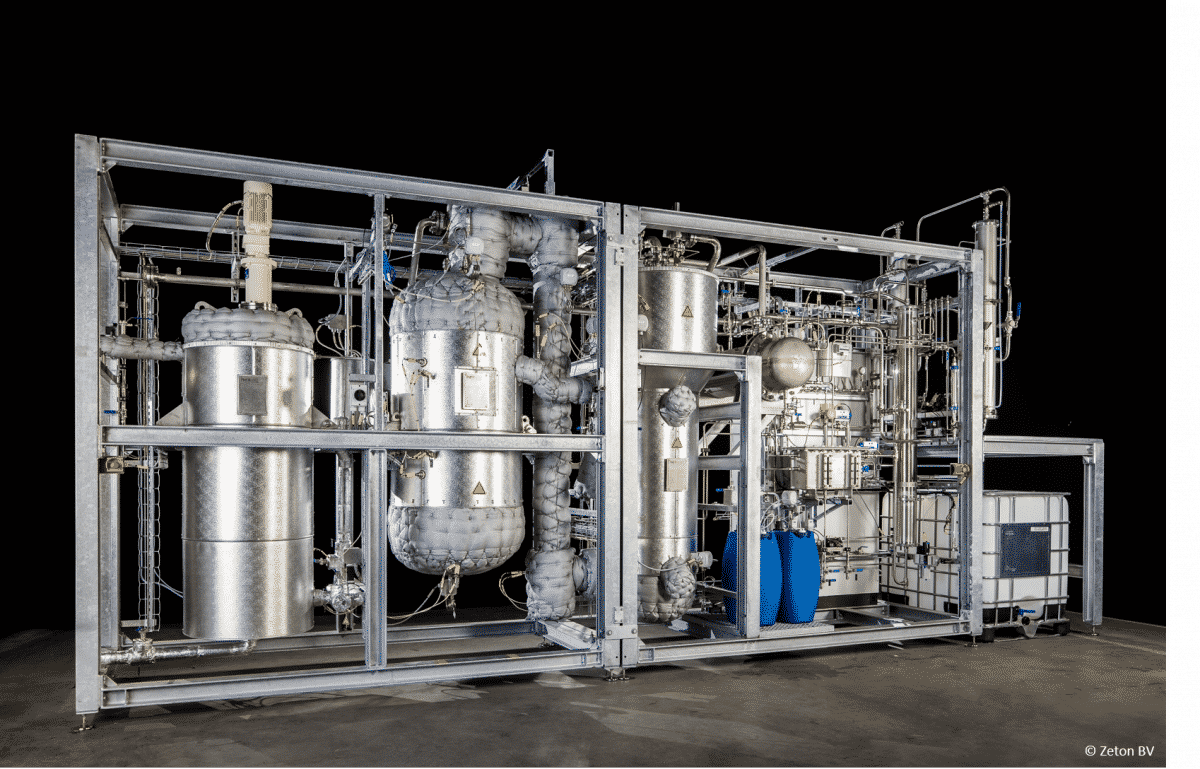
It is not just for the sake of our energy supply that we are still largely dependent on fossil fuels. The chemical industry almost exclusively uses fossil fuels as raw materials as well, for example in the production of plastics. That is why the Groningen start-up BioBTX wants to blast a new, green gust of fresh air through the chemical industry. The company is counting on artificial intelligence to be able do this.
A half-opened garage door conceals a tangle of aluminium colored vats, switches and pipes. Except for one technician, the BioBTX workshop is unmanned. It is tucked away somewhat, right at the back of the Energy Academy on the Zernike campus in Groningen. Little suggests that five people are working here on a machine which could turn the entire chemical industry upside down. “What we want to do here is to start a revolution,” says Chief Technology Officer Niels Schenk.
BioBTX has developed a pilot plant for extracting chemicals from biomass. The Groningen start-up does this by breaking down glycerine, a waste product released during the production of biodiesel, into small fundamental building blocks, namely benzene, toluene and xylene – better known as BTX. These in turn form the basis for all kinds of aromatics, which are used for many chemical applications. Examples are amino acids, sweeteners or antidepressants, but also polymers (from which wind turbines or cars are made) and aramids (extremely strong fibers that are used in bulletproof vests, for instance).
At the moment, we are extracting almost all of these chemicals from fossil fuels, resulting in massive pollution and CO2 emissions. By converting biomass into chemicals, BioBTX will be able to make a significant contribution towards making the chemical sector more sustainable.
Optimization with AI
But that’s not all. The company wants to accelerate that process using artificial intelligence. In a lab at the Faculty of Science & Engineering of the University of Groningen (RUG), researchers are using test tubes to simulate the operation of the larger BioBTX pilot plant. There they can experiment with different set-ups in order to determine the most efficient production process for BTX.
There are more than enough possibilities, because by combining different raw materials, catalysts and temperatures, you are easily able to perform 5 million different experiments. Add to this the fact that carrying out such an experiment takes half a day, and you will understand why such technology developments usually happen on the basis of a targeted selection of experiments.
Not so for BioBTX. Together with researchers from the Chemical Engineering department, the Groningen start-up approached the data science team of the CIT of the University of Groningen. Based on data from a small number of experiments carried out, data scientist Dimitrios Soudis developed an algorithm for predicting what would have been the outcome of the millions of experiments that were not carried out.
According to project leader Erik Heeres from the Faculty of Chemical Engineering, the contribution of data science ‘makes a huge difference’. “We have discovered interesting links between the type of catalyst or reactor temperature and the amount of BTX produced. That way we occasionally enter domains that I hadn’t thought of myself.”
By unleashing artificial intelligence on the data, you can simulate the real world and discover patterns in it that would otherwise slip by unnoticed. But it also offers additional advantages. “By using AI you are also able to make very accurate predictions,” says Niels Schenk. “Instead of drawing up an experimental plan, they are now coming up with their own suggestions based on their algorithm. Then they say, for example: if you have this raw material, it is best to work with this type of catalyst, or with a higher temperature. So you come up with information that you would otherwise have had to do millions of experiments for. In the long term, this gives an enormous amount of added value.”
Towards a circular economy

The application of AI ensures that uses glycerine in the BTX production process is considerably more efficient. But BioBTX doesn’t want to stop there. This summer, the company from Groningen wants to take a big step towards becoming a global pioneer in the transition towards a circular economy.
A circular economy consists of a cycle of raw materials. Instead of throwing away products when they are worn out or when we have a new product in mind, you can add value to them by reworking them into new products. So today’s smartphones will be tomorrow’s raw materials. From a disposable and a replaceable economy which leads to the depletion of raw materials and tons of unbreakable waste and CO2, towards an economy that follows the natural cycle of nature.
Translate this to the plastics sector and it becomes clear why BioBTX not only wants to process glycerine into new chemicals this summer, but also wants to recycle chemicals from waste plastics. This involves laminated or mixed plastics, which are now mostly burned, dumped in the sea or exported to third world countries.
By processing these plastics into chemicals, BioBTX wants to redefine the concept of ‘waste’, says Schenk. “In our view, waste plastics should become so valuable that they can no longer be simply thrown away.”
Once the pilot plant on the Zernike campus is operating properly, BioBTX will be able to start thinking about the next step: scaling up and commercializing their model. “Only then can we really change the world of plastic pollution and CO2 emissions associated with the production of plastics. Because that’s the goal that we all started with: to make the world a little better.”