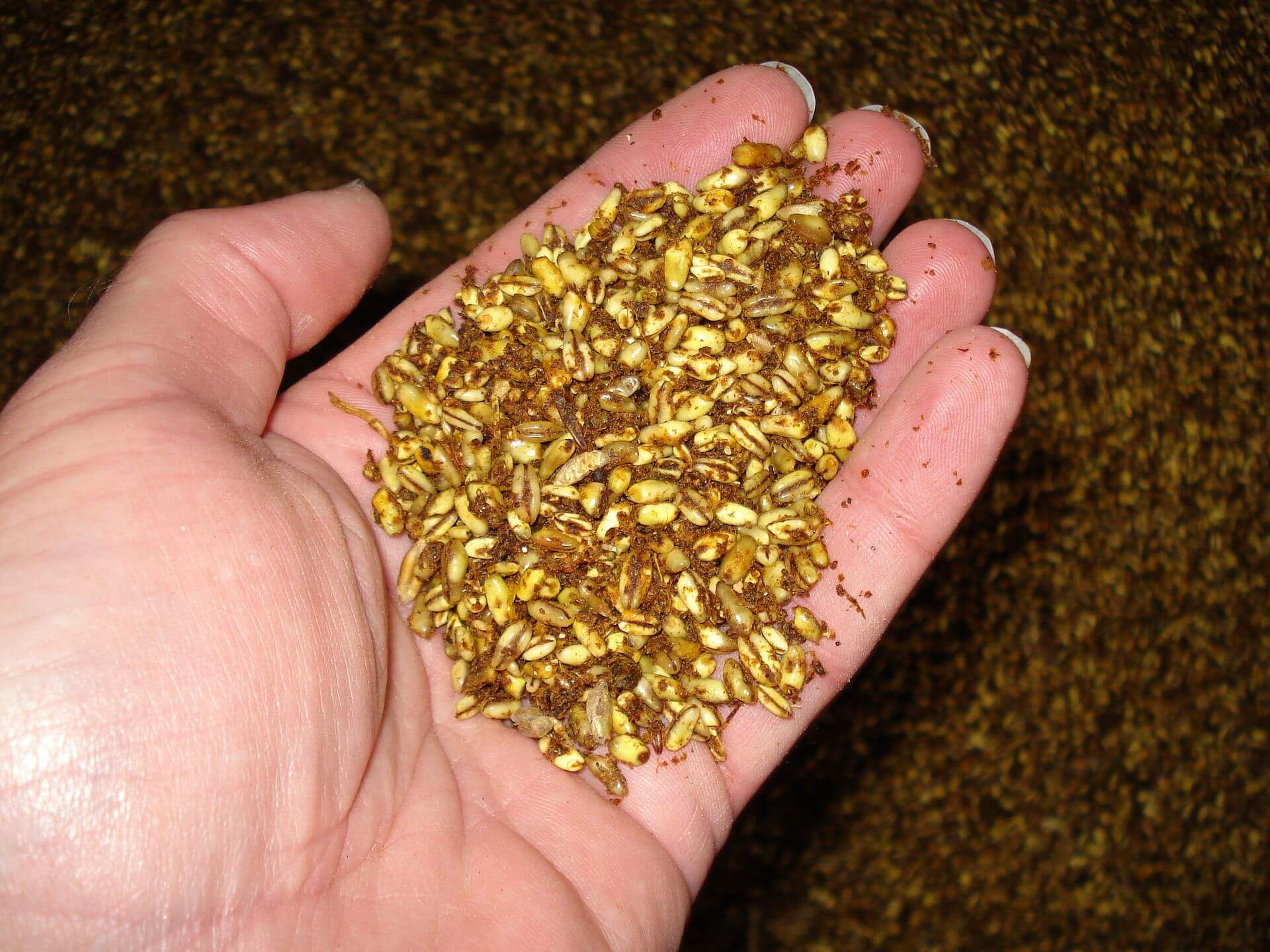
At the Technical University of Munich (TUM), Professor Arne Skerra has succeeded for the first time in using gaseous CO2 as a basic material for the production of a chemical mass product. This is methionine, an essential amino acid, which is mainly used in animal fattening. It is a basic building block of proteins, which is not only vital for many living beings but above all for humans. The problem: Humans cannot produce methionine themselves and have to take it up with food. In fattening animals, such as poultry or fish, methionine accelerates growth – similar to the way mineral fertilizer allows plants to grow faster. Currently, about one million tons of methionine are produced worldwide.
The newly developed process can represent a breakthrough since a 6-stage chemical process based on petrochemical starting materials was necessary for the previously common industrial production of methionine. Among other things, highly toxic prussic acid is required. This process also produces the technically unproblematic intermediate product methional – a decomposition product of methionine found in nature. This is crucial for the new process.
Evonik invited to tender
Preparations for the research work began when Evonik Industries invited university researchers to submit proposals for new methods for the safe production of methionine as part of a call for proposals in 2013. Evonik is one of the world’s largest manufacturers of the substance.
“Based on the idea that methionine in microorganisms is degraded from enzymes to methional by releasing CO2, we tried to reverse this process,” explains Professor Arne Skerra, Chair of Biological Chemistry at TUM. “Because every chemical reaction is reversible in principle, but often only with a high use of energy and pressure.” Skerra took part in the tender, the idea was awarded a prize by Evonik and supported as a project.
“Every chemical reaction is reversible in principle, but often only with a high use of energy and pressure.”
Together with postdoc Lukas Eisoldt, Skerra began to determine the basic conditions for the production process and to produce the necessary biocatalysts (enzymes). In initial trials, they tested the CO2 pressure required to produce methionine from methional in a biocatalytic process. It turned out that even at relatively low pressure – for example, that of a car tire: about two bar – the yield was unexpectedly high. Thanks to these successes, which took effect after just one year, Evonik extended its production. The team continues the research with the support of doctoral student Julia Martin.
More effective than photosynthes
After several years of work, it was finally possible to improve the reaction on a laboratory scale to a yield of 40 percent and to clarify the theoretical background of the biochemical processes. “Compared to complex photosynthesis, in which nature also integrates CO2 into biomolecules by biocatalytic means, our process is highly elegant and simple,” reports Arne Skerra. “Photosynthesis uses 14 enzymes and has a yield of only 20 percent, while our method requires only two enzymes.”
The basic pattern of this novel biocatalytic reaction can serve as a model for the industrial production of other valuable amino acids, as well as a precursor for drugs. In the meantime, the process has been patented and refined by protein engineering to such an extent that it is suitable for large-scale technical applications. This would be the first time that there has been a biotechnological production process that uses gaseous CO2 as an immediate chemical feedstock. All previous attempts to recycle the climate-damaging greenhouse gas have failed because of the extremely high amount of energy required.
Photo: Wikimedia Commons