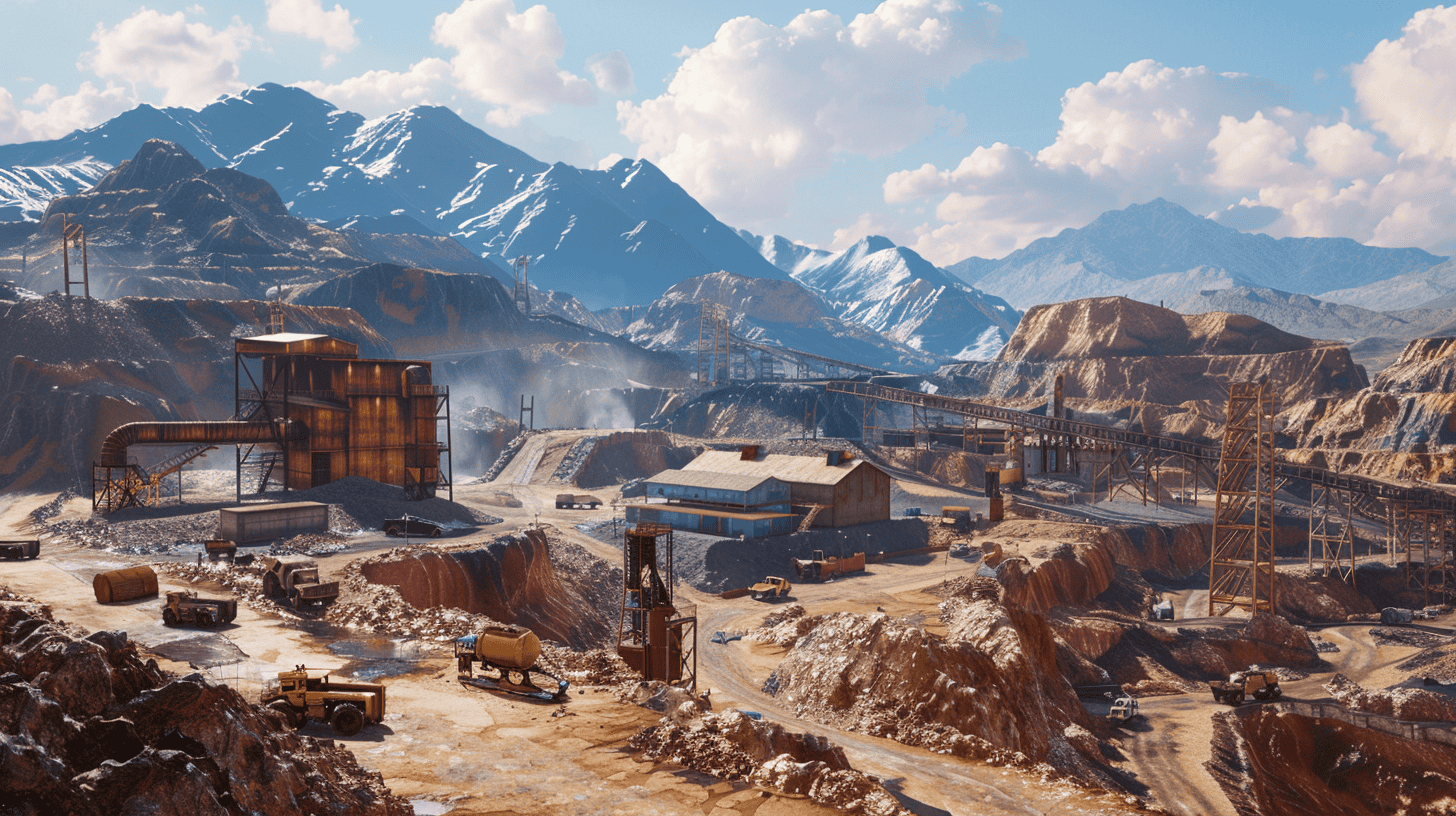
Copper, lithium, cobalt, or better: wind turbines, solar panels, batteries, computers, screens, and devices of all sorts. Tens of raw materials are behind every key technology fueling the green transition and a centerpiece of geopolitical tension. David Peck, a professor of critical materials and product design at the Delft Univesity of Technology (TU Delft), compares current times with the post-World War II situation. Then, the six European countries behind the European Coal and Steel Community understood that there was no future without metals and energy. “Nowadays, the situation is not that different; we can’t do without them,” he underlines.
Why this is important
Critical raw materials are one of the flywheels of the green transitions. However, Europe and the Netherlands depend on third countries to import most of them. The TU Delft is actively researching all aspects related to this topic, from recycling to market models.
TU Delft’s Materials Week is in full swing. With this initiative, the university showcases its efforts in one of the pivotal domains in the decades to come. Last year, the European Commission published a study on critical raw materials (CRMs) underlining their resign demand, updating the list of CRMs, and outlining the EU’s dependence on third countries for most of them.
Last March, the EU) adopted the Critical Raw Materials Act, setting new sourcing, recycling, and mining standards, aiming for a diversified, affordable, and sustainable supply by 2030. The regulation defined these materials as indispensable for a set of strategic sectors, including aerospace, net zero industry, and defense. One of the directive’s tenets established that 10% of the EU’s yearly consumption of minerals must be extracted in Europe.
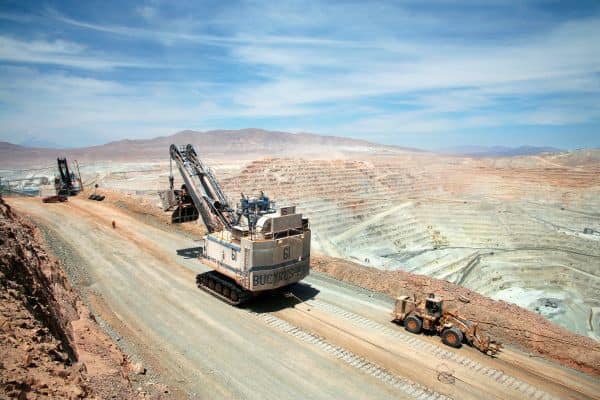
New ways of mining
Mining is the primary way to source materials, and the TU Delft is also studying less polluting ways to extract materials. Recovering materials from waste streams is one option. When mining for copper, only 1% is actually copper, as it bonds with other minerals. The remaining 99% is discarded. Mines also release wastewater into the environment that still contains precious metals, such as zinc, in the case of copper.
Lot van der Graaf, a researcher at the Resource Engineering department, looks at the use of microorganisms to recover minerals from mines’ waste streams. In a way, she is mining with bacteria. “As a microbiotechnologist, I find this bacteria fascinating. They live in extreme conditions, where there is almost no life at all, and they can be used to recover some of the minerals that are now lost,” she explains. Her colleague Tobias Schmiedel studies other potential mineral sources. Geothermal water, for example, contains lithium concentrations. Interestingly, part of his research also concerns the asphalt waste stream, where a mineral like platinum—coming out of cars’ exhausts—can be found. Platinum—also flagged as a CRM—is widely used in the electronics and automotive industries.
Recycling
Another target set by the Critical Raw Materials Act is to increase the amount of recycled materials. By 2030, 25% of the raw materials annually consumed in the EU must be recycled. At TU Delft’s hydrometallurgy lab— a technique that uses a water-based solution to extract metals—scientists experiment with chemical recycling of electronic components. By researching ways to separate materials and components efficiently, they pave the way to fully circular electronics.
Furthermore, the scientists are also looking into ways to recycle lithium-ion batteries. Starting from the so-called black mass– the resulting powder mix after shredding batteries— they are working to find the most efficient ways to get reusable nickel, cobalt, or lithium. “Step by step, we work to separate and recover all the minerals, starting with aluminum and copper and then retrieving manganese, nickel, cobalt, and even lithium. However, these processes are not optimal yet, and we still need to conduct further research,” explains Shoshan Abrahami, a professor at the mechanical engineering faculty.
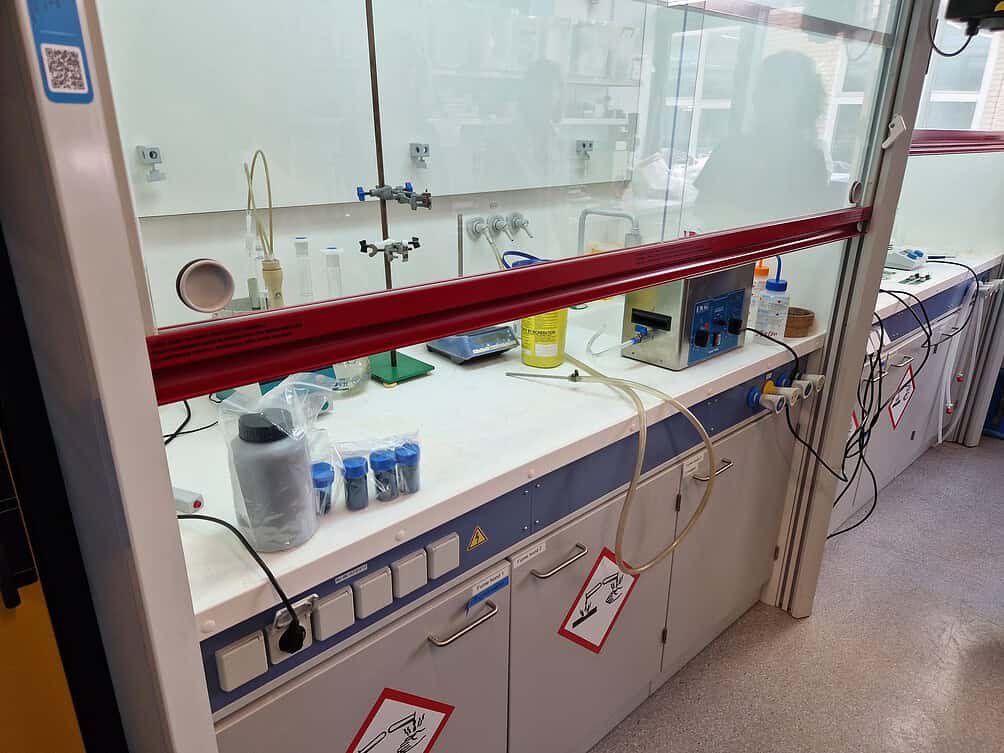
Tracking raw materials
Starting from 2027, the EU’s Digital Product Passport (DPP) will be launched. This initiative, set to start with metals, textiles, and batteries, aims to make data about the whole lifecycle of a given material transparent. Companies will have to comply and share data on a given product’s raw materials and origins, ultimately giving consumers higher transparency about the goods they buy. “Sharing all information about products and their origins is essential to foster recycling and reuse of such materials at the end of their life cycle,” said Jolien Ubacht, a professor at the faculty of Policy and Technology Management.
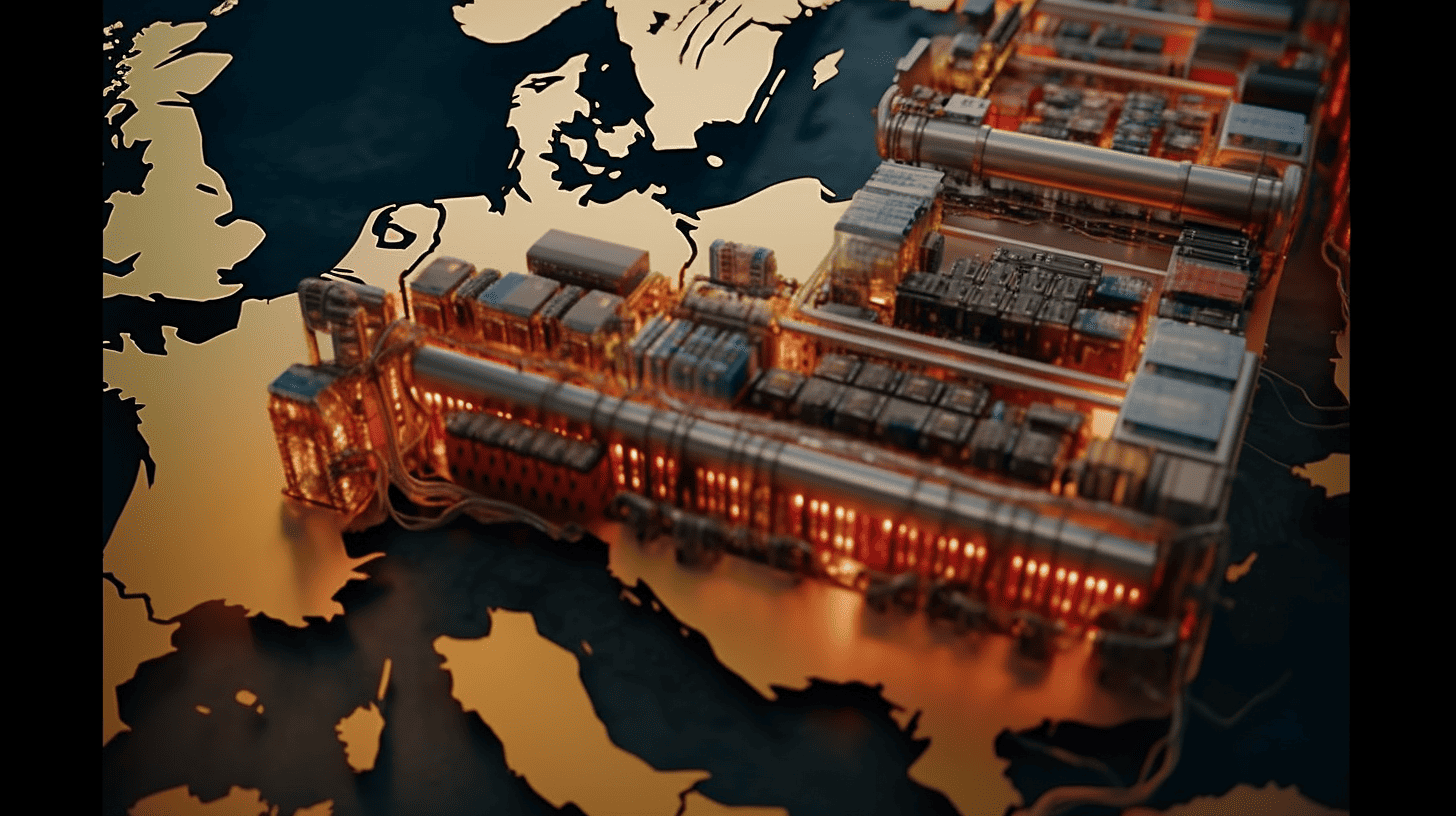
What’s next?
Looking at the future, Delft scientists are conducting simulations of the actual amount of raw materials needed in the coming decades. Willem Auping, from the faculty of Policy and Technology Management is working on different models to calculate how much CRMs will be needed in different scenarios. And such scenarios can vary significantly, depending on the technological and strategic choices, as well as the breakthoughs in one or the other sector.
Similarly, Benjamin Sprecher, professor at the faculty of industrial design engineering, has been studying — given the data shared by grid operator Tennet on how Dutch electricity will look in the coming years. He sees a lot of fluctuations in production chains. Mentioning the example of lithium-iron-phosphate battery production in China, he showed how production went down to 32% from 70% in the three years, and how it has picked up again by 30% in the following three ones. Therefore, it is hard for countries and companies to plan mining investments. “What makes the difference is state support, which, in China, is certainly present,” he said.
Despite all the concerns, Peck looks positively at the future. “We can’t look at the future without looking back. In the past we have had bad times. Did we through ingenuity, drive and working together collaboratively solve it? Yes we did. Can we do it again? Yes, we can.”