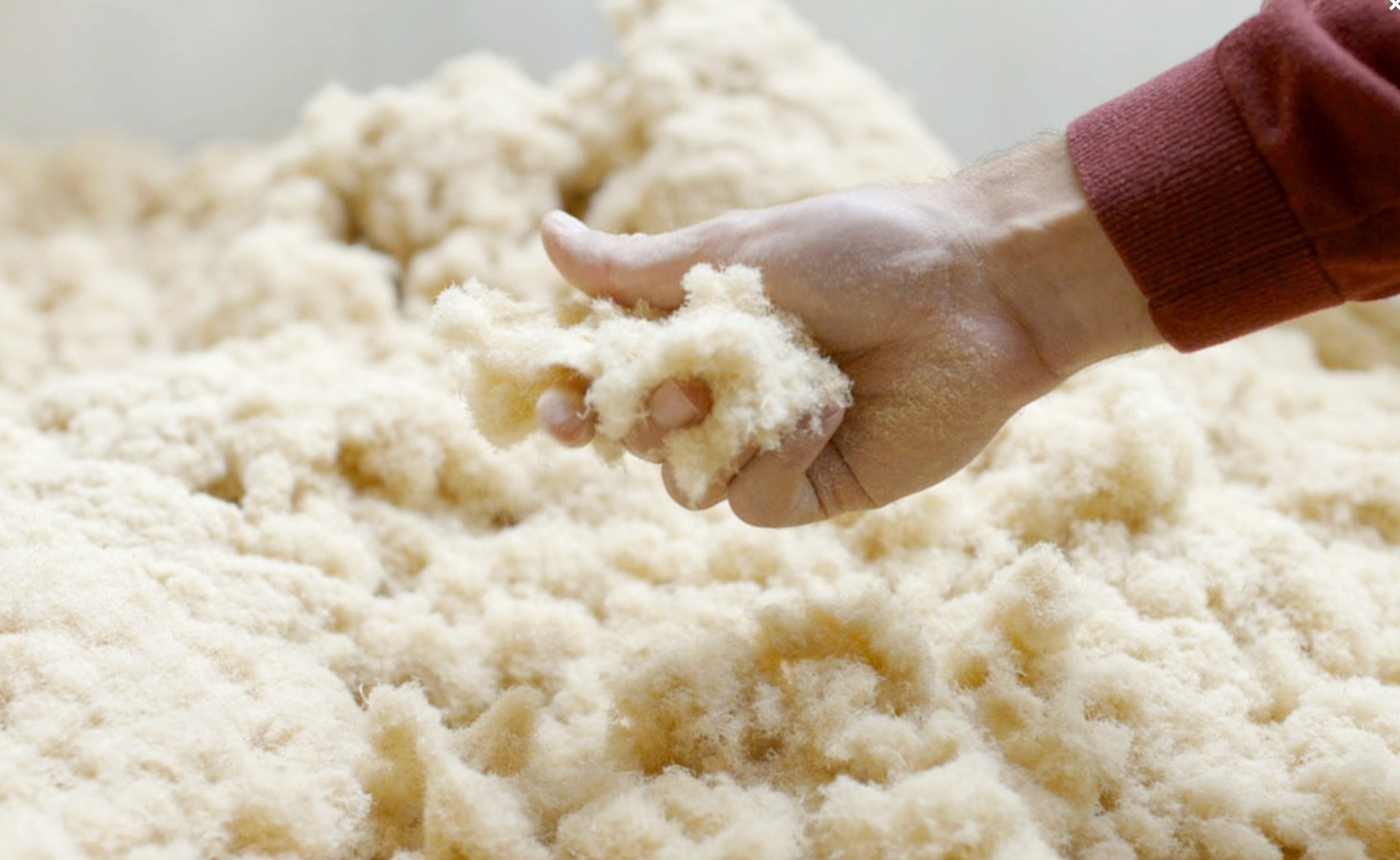
Stand-up paddling (SUP) is a sport close to nature. But plastic boards are anything but environmentally friendly. Usually, petroleum-based materials such as epoxy resin, polyester resin, polyurethane and expanded or extruded polystyrene are used in combination with fiberglass and carbon fiber to produce the boards.
In many parts of the world, these plastics are not recycled, let alone disposed of properly. Large quantities of this plastic end up in the sea and collect in huge ocean eddies. This prompted Christoph Pöhler, a scientist at the Fraunhofer WKI and an avid stand-up paddler, to think about a sustainable alternative.
Balsa wood from rotor blades
“In common boards, the polystyrene core, known as styrofoam, is reinforced with fiberglass and sealed with an epoxy resin. We, on the other hand, use bio-based lightweight material,” says the civil engineer. Pöhler and his colleagues use recycled balsa wood for the core. This has a very low density, so it is light but can still withstand mechanical stress.
Balsa wood grows primarily in Papua New Guinea and Ecuador and has been used in large quantities in wind turbines here for many years. Up to six cubic meters of it can be found in a rotor blade. Currently, many of the turbines are going off the grid. In 2020 alone, 6,000 of them were dismantled. A large proportion of them will be sent for thermal recycling, but it would make more sense to recover the material from the rotor blade and recycle it in line with the circular economy. “This was precisely our consideration. This valuable wood is too good to be incinerated,” says Pöhler.
Patented technology
But how is it possible to recover the balsa wood from the rotor blade? After all, it is firmly bonded to the outer shell, a fiberglass-plastic composite. First, the wood is separated from the composite material in an impact mill. The differences in density allow the mixed material structures to be split into their individual components using a so-called air classifier. The balsa wood fibers, now in the form of chips and fragments, are then finely ground.
“We need this very fine starting material to produce wood foam. The Fraunhofer WKI has a patented technology for this,” explains the researcher. In this process, the wood particles are glued together to form a kind of cake batter and processed into a lightweight yet firm wood foam that holds together by virtue of the wood’s own binding forces. The addition of glue is not necessary. The density and strength of the foam can be adjusted. “It is important that the density not be too high. Otherwise, the stand-up paddleboard would be too heavy to transport.”
Sandwich material
Since all sandwich material used in conventional boards is supposed to be completely replaced, the shell of the ecological board is also made of a 100 percent bio-based polymer. It is reinforced with flax fibers grown in Europe, which have very good mechanical properties. To pull the shell over the balsa wood core, Pöhler and his team use the hand lay-up and vacuum infusion processes. Feasibility studies are still underway to determine the optimal method.
An initial prototype of the ecological board should be available by the end of 2022. “In terms of environmental protection and resource conservation, we want to use natural fibers and bio-based polymers wherever technically possible. In many places, fiberglass-plastic composite is used even though a bio-based counterpart could do the same,” Pöhler says.
Initially, the researchers are focusing on SUP boards. However, the hybrid material is also suitable for all other boards, such as skateboards. The future range of applications is broad. For example, it could be used for thermal insulation in the façades of buildings. The technology can also be used in the construction of vehicles, ships and trains.
Photo: Christoph Pöhler with a chunk of a former wind turbine rotor blade in the Fraunhofer WKI’s wood workshop. © Fraunhofer WKI
Also interesting: Vitrimers will make plastics of the future sustainable