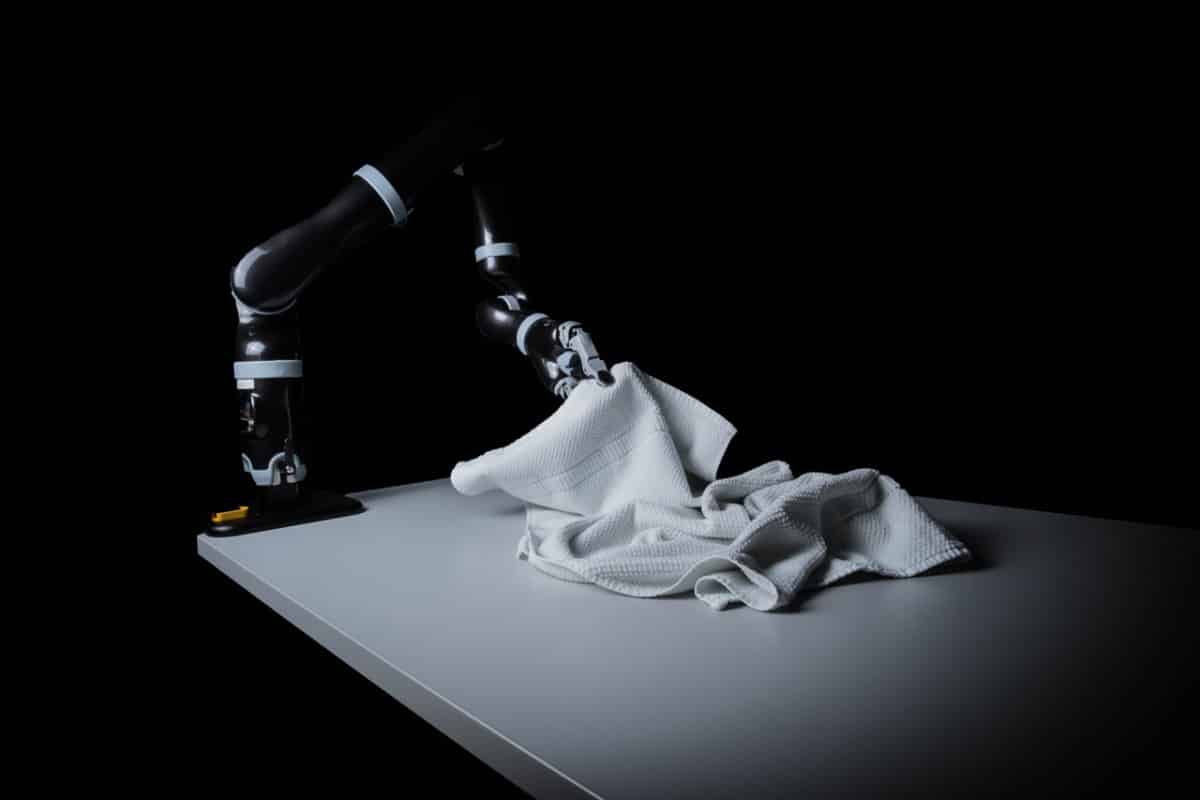
T-shirts can testify to having undergone long journeys. Prior to being offered for sale in Germany, they first migrate from the cotton plantations in the USA to the weaving and dyeing mills in India and are then sewn in Bangladesh. They finally land in the ports of Hamburg or Rotterdam after traveling as far as 40,000 km. Aside from the manufacturing process, the actual transport of these products releases huge amounts of greenhouse gases as well. Yet for economic reasons regional manufacture still seems not to be possible. This could change in the near future as the young start-up sewts ( the name is a combination of the English suit and to sew ) wants to bring textile production back to Germany. The production work will be carried out entirely by robots instead of being done by people. The three founders Alexander Bley, Tim Doerks and Till Rickert recently presented a prototype for the fully automated handling of textiles – as part of a large-scale industrial laundry – at the Tech Check (Bavarian Center for Digitization) in Munich.

We spoke to Alexander Bley about the founding of sewts and the company’s ambitions.
How did you come up with the idea to found the start-up?
The idea was a gradual process. Two of our founders, Tim and I, were working intensively in the field of fiber compounds during our studies. Our main focus was on the lightweight structure of carbon aircraft wings. It is important to know that technological textile materials such as carbon fabric are layered on top of each other for manufacture and then impregnated with resin. The aim of the study was to automate the processing of these inherently unstable materials. The challenge was then to predict how such soft materials would behave when applied.
Throughout the developmental phase, we asked ourselves which sectors would even benefit from such a solution. This is how we got into textile production. Especially since all three of us are convinced that the routes that the clothing industry is presently taking are anything but sustainable. Just like the manufacturing processes – when it comes to dyeing or sewing for such dirt cheap prices. Short production routes would not only be interesting when considering the reduction of emissions, but in the long term they may also help raise the level of education in countries like Bangladesh by eliminating low-skilled jobs. We have already witnessed similar changes within production during the 1950s in Germany.
Where do you see the specific areas for their application?
We see the primary area for application first and foremost in common sewing processes. For example, in clothing but also in car or aircraft seat covers. At the moment, however, we are focusing on industrial laundry technology. Because currently there is still a person standing at a machine sorting the textiles according to their category and then placing them in the automated ironing machines. Our development would make a cost-effective, fully automated industrial laundry possible.
What makes your product special compared to other products?
Actually there are already efforts to design a similar product. For example, a US start-up has specialized in sewing floor mats and pillows. But the Americans are working with a so-called Cartesian portal system – which means that their robots run on rails. Accordingly, they are only suitable for their specific area of application.
In comparison, our robot is flexible because it is able to differentiate between products. We first scanned and classified various textiles. This means that thanks to AI, our robot recognizes colors, surfaces, materials and the actual products. For instance, it is able to distinguish a napkin from a pillow. It also knows about material properties and bending stiffness. In addition, we have calculated contact points so as to determine how textiles are able to be handled without causing wrinkles. Thanks to all of this background information, our design is able to work with a much higher product variability.
What was the biggest hurdle you had to overcome initially?
I would say that the biggest hurdle was daring to take that first step into self-employment. We were all at the stage of being able to gain a doctorate. And up until just before it was all realized, we still didn’t know whether we would receive a grant.
Was there a moment when you wanted to give up?
No, fortunately not. But we also set ourselves a definite goal. Our private finances would have been enough for about six months – even without any generated revenue. If it hadn’t worked by that time, we would have given up. Fortunately, this wasn’t the case.
What was the greatest moment for you when it came to setting up your company, what made you particularly proud?
There were actually two really great moments. One was when we were sitting at the notary and signing the Certificate of Incorporation. We had been working on our robot for a year – but that was within the university environment. And suddenly we were entrepreneurs.
The other time was in mid-July. Here we went public for the first time with our prototype during the tech check held by the Zukunftsrates der Bayerischen Wirtschaft (Bavarian Business Council for the Future) – without fear of our idea being stolen. After all, we had previously applied for an international patent. The event was a confirmation to us of the innovative character of our design.
What can we look forward to in the next few years, in other words: What can we expect from you in the coming years?
At the moment we are focusing on the concept of a fully automated laundry. This means that we are working to ensure that our robots can recognize towels and bed sheets in the laundry mountain and place them on an ironing machine without creasing them. Our main concern here is to build up our competence in the field of fully automated textile handling. We first want to gain credibility before moving on to fully automated clothing production. Our goal is to automate the process chain of industrial laundry a full 100%. The first products will be available here in November 2020. Then our next step will be around 2023: We intend to launch production of the first fully-automated T-shirt in Munich within this time frame.
What drives you every morning?
Imagining looking back at your own life in 20 to 30 years time and being proud of having brought the world a little further where sustainability is concerned. In other words, having a positive impact makes it worth it.
What is your vision: Where do you see your company in 5 years time and what is your ultimate goal?
Ultimately, we envisage manufacturing regionally produced tailor-made garments within a brief time period – independent of any size norms such as S or L. This means that our vision is that the customer is, for example, able to scan an image of their body and transmit these along with their measurements via a mobile phone to our robot. The robot then produces an original garment.
“Our vision is the establishment of fully automated, made-to-measure textiles – so that the world will ultimately become more sustainable.”