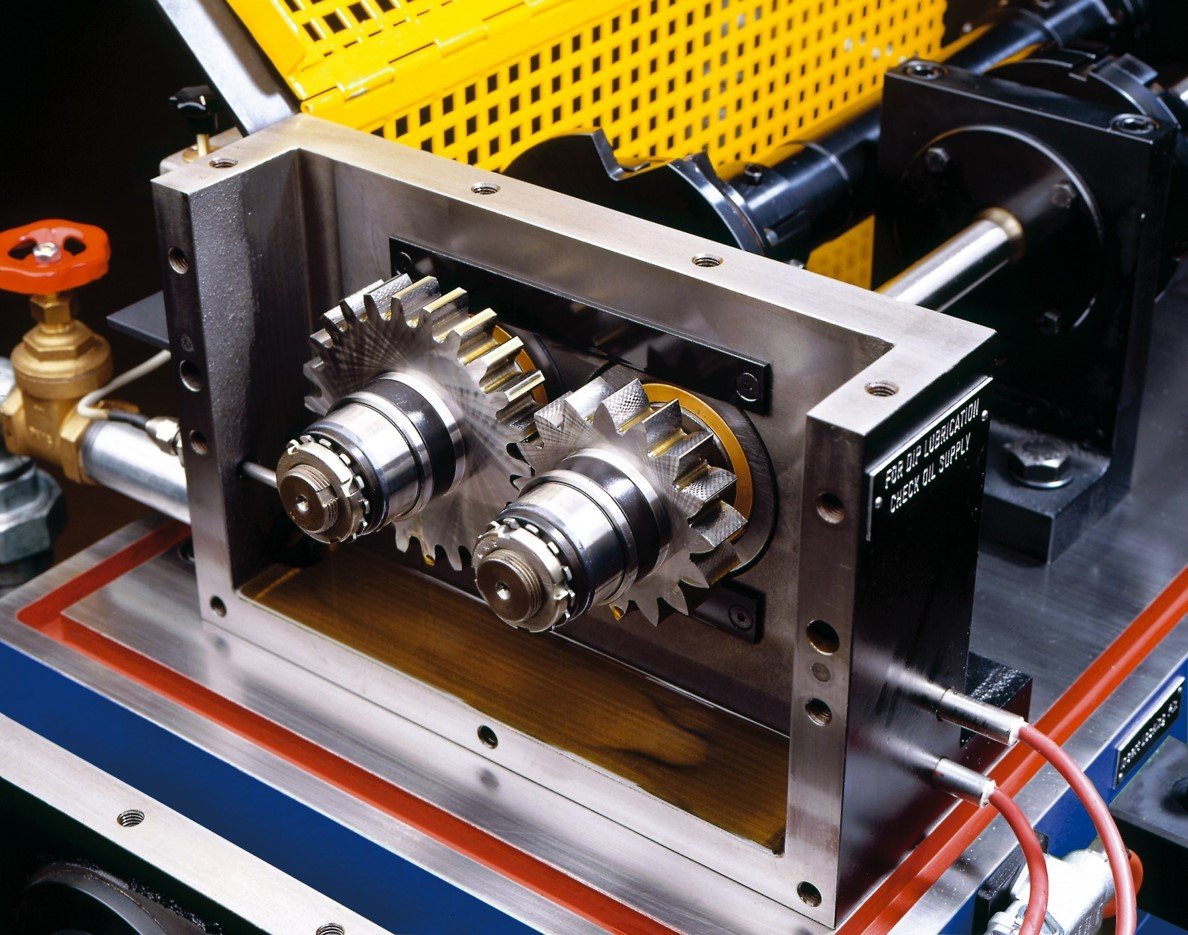
Conventional lubrication systems for high-performance transmissions are based on oil. This is problematic since no gearbox is one hundred percent leak-proof. The consequence is so-called “oil shrinkage” which leads to the gradual poisoning of water and soil. Plus, the common worldwide practice of disposing of used oil by burning causes CO2 emissions. “But people accept this because it is the state of the art,” explains Dominik Cofalka, managing director of the start-up Reintrieb in Vienna, Austria.
Environmentally-friendly lubrication system
Cofalka and his team have developed a lubrication system for high-performance transmissions that contributes to decarbonization. It no longer taps into valuable petroleum resources and reduces CO2 emissions – both in loading and disposal. The technology is based on naturally occurring water and is 100 percent sustainable, in line with the United Nations Sustainable Development Goals. The use of the lubrication system makes sense wherever the escape of harmful lubricating oil is undesirable, onshore and offshore, from shipping to power plant and barrage installations to supply pipes. In industry, applications can be found in the production of food, rubber and pharmaceuticals.
Also interesting: Inland shipping of the future will soon have a helmsman ashore
By the same token, the entry of water into lubrication systems of gearboxes is also problematic. Even with a 0.1 percent water content, the quality of lubricating oil suffers. Water in gear oil is the main reason for operational failures in ships, power plants and pumps in general.
Proof of concept
On a laboratory scale, Reintrieb’s water-based lubrication system for gearboxes works. This amazed even mechanical engineer Karsten Stahl from the Faculty of Mechanical Engineering at the Technical University of Munich, Germany, who carried out the proof of concept. After all, common sense tells you that water causes metal to rust and thus wear out quickly. Nevertheless, with Reintrieb’s lubrication system, he says, problems such as wear, tooth breakage, galling and surface fatigue are manageable even if there are still unanswered questions and a need for further research, Stahl said.
There are also other research teams working on oil-free lubrication systems for gearboxes. In Germany, the focus is on fluid-free lubrication systems that can withstand high loads. Cofalka calls it “thick water” and says that it must not contain additives:
With oil, you can tell it has leaked. It forms streaks on water and on land. Additives disappear into the environment. Nobody knows how to remove them again.
Dominik Cofalka, Managing Director, Reintrieb
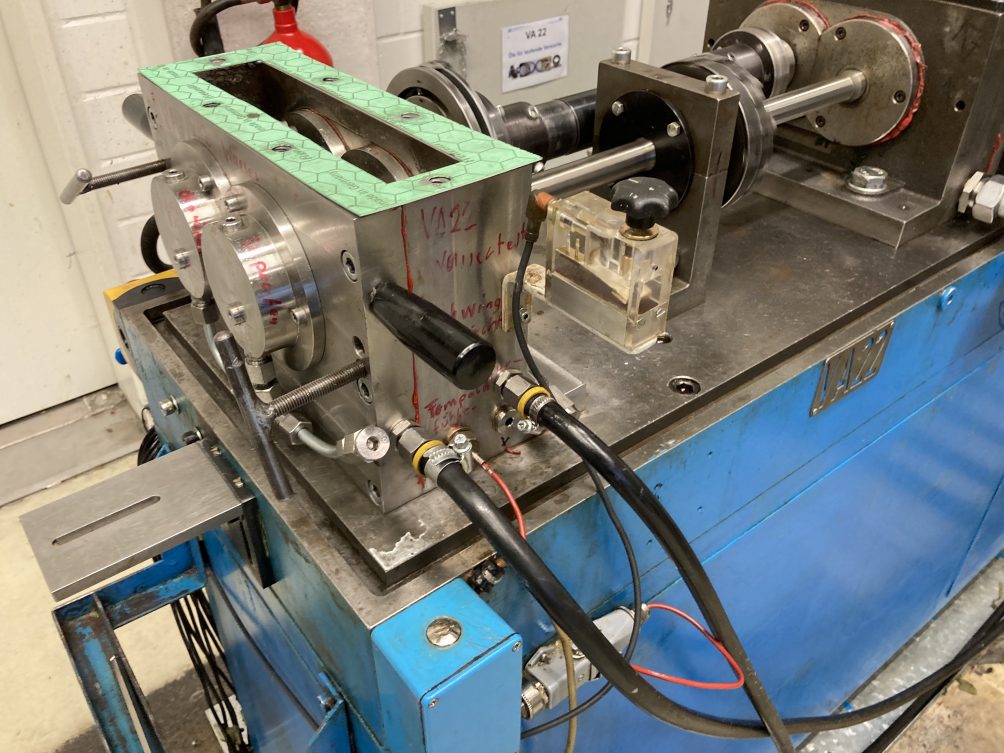
At Reintrieb, research has focused less on the lubricant than on the material for the gears. The challenge, he says, was to balance the three factors of hardness, elasticity and corrosion. With metals that are harder than steel and the lubricant water, they succeeded. The novel lubrication system has the same service life as conventional ones. And the price structure is potentially even more economical, he said.
Lubrication and cooling
This system also combines lubricating with cooling at the same time. “On a surface comparable to that of a fingernail, the surface of a gear flank in conventional gear use must withstand 36 times the weight of a VW Golf. The frictional heat generated in the process reaches 10 times the heating capacity of an iron. In oil lubrication, the oil acts as a protective film between the surfaces of the gears that meet. This prevents intense heating. If it gets too hot, however, the oil begins to evaporate. So water has a disadvantage over oil in lubrication and an advantage in cooling.”
“So water has a disadvantage over oil in lubrication and an advantage in cooling.”
Dominik Cofalka, Managing Director, Reintrieb
Aquaplaning effect
In lubrication, Reintrieb takes advantage of a type of aquaplaning effect. This sets in as the speed of the gear increases because a film of water then forms on the gear surfaces, causing a loss of adhesion. This means that the gears run smoothly while simultaneously cooling.
Three types of water were tested in the proof of concept: Fresh water, salt water and distilled water, as used in radiator systems. All types produced good results, but it became apparent that the water quality had a decisive influence on the function and service life of the gear units. Salt water would be particularly advantageous in shipping since it would not have to be carried. It could be taken directly from the sea. But Cofalka rules it out for the time being because it attacks some materials, and also because he assumes it will not become an open-circuit lubrication system.
Novel ship propulsion
In marine applications, the gear lubrication system can solve two problems at once: the intake of water into gear oil and vice versa: the leakage of gear oil into bodies of water. A modern cruise ship or freighter loses between six and ten liters of oil a day. Cofalka quotes from a U.S. Environmental Protection Agency study indicating that ten percent of the world’s oil contamination comes from gear oil. It will be about a year before the first water-lubricated gearbox can be used in shipping. Reintrieb is currently working on finalizing the prototype. Their cooperation partner is the experienced gear manufacturer Heinz Ehgartner from Leoben.
This is where another of the start-up’s innovations comes into play, one that has already attracted interest from the shipping industry: The partners are building a 20-kilowatt underwater gearbox (lower gearbox) of a rudder propeller. An initial application of this so-called side-by-side drive is scheduled to take place in cooperation with Hydromaster in Rotterdam, Netherlands.
Reduced draft
Rudder propellers make ships easy to navigate. Conventional models consist of a large propeller, but Reintrieb’s novel model consists of two small propellers side by side in a nozzle, resulting in a solution with a draft that is 25 percent smaller. This allows ships to sail even in shallow water, as is the case during periods of drought. The potential area of application is primarily in inland waterway transport; an area that the EU wants to promote to reduce transport-related greenhouse gas emissions. Climate change is exacerbating the problem of low-water phases.
Also interesting: Inland waterway shipping can make freight transport much more sustainable
The mechanism of rudder propellers can be compared to a household blender whose two blades rotate in relation to each other. “The propellers rotate at high speed and generate forward propulsion, but have a high power loss due to turbulence. The fine art is to create as little turbulence as possible. Through fine-tuning, we have managed to optimize the eddy current. In the process, we were able to improve efficiency. In addition, we also want to use Big Data flow calculations to reduce fuel consumption and the ensuing CO2 emissions,” explains Cofalka.
About Reintrieb:
Reintrieb was founded in Vienna in 2016 and pursues the research, development and commercialization of cleantech technologies. The founders are brothers Dominik and Vincent Cofalka and engineer Siegfried Lais. Vincent Cofalka works for the U.S. corporation Carnival Inc. as Fleet Captain and as Captain of the flagship AIDAnova, among other positions. Siegfried Lais worked for 50 years in marine propulsion engineering and related fields. Dominik Cofalka is also founder and managing director of a management consultancy focusing on capital market issues.